Обзор отличительных компонентов немоторной тележки
Немоторная тележка по своей основной структуре во многом унифицирована с моторной тележкой, поэтому ее компоненты, полностью совпадающие с аналогичными компонентами моторной тележки, здесь не перечисляются. К каждой из двух поперечных балок рамы тележки (рис. 3.116) болтами закреплены три клещевых механизма 2, которые воздействуют на три вентилируемых тормозных диска, напрессованных на среднюю часть оси немоторной колесной пары.
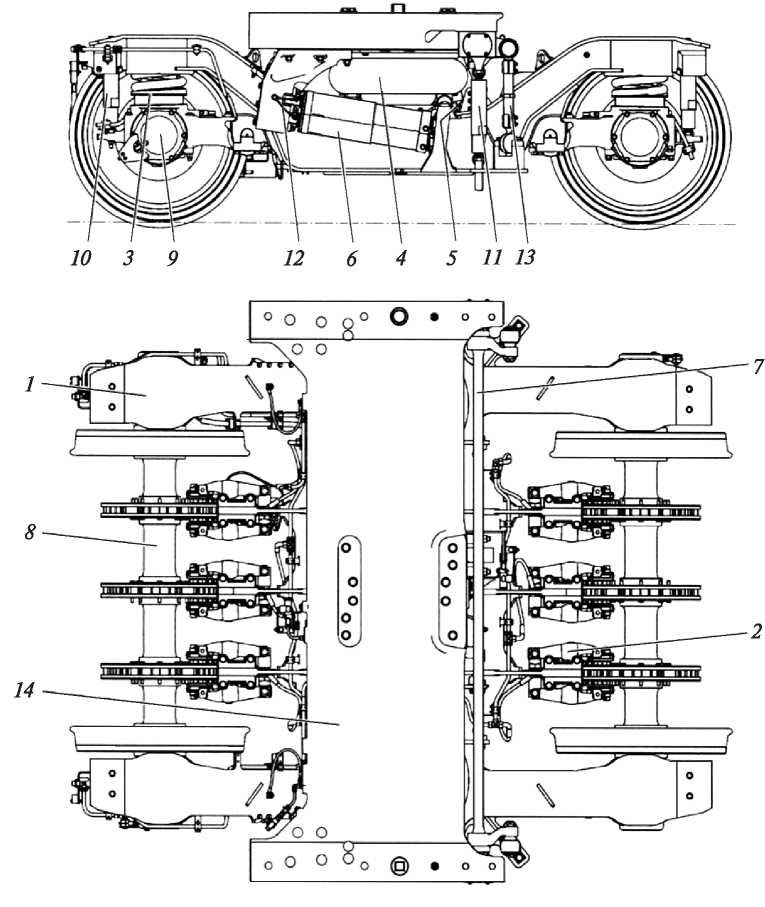
Рис. 3.116. Немоторная тележка с траверсой: 1 — рама тележки; 2 — клещевой механизм фрикционного тормоза; 3 — цилиндрическая пружина 1-й ступени рессорного подвешивания; 4 — пневморессора; 5 — демпфер успокоения поперечных колебаний кузова; 6 — демпфер виляния тележки; 7 — торсион поперечной устойчивости кузова; 8 — ось колесной пары; 9 — букса; 10 — демпфер гашения вертикальных колебаний рамы тележки (1-й ступени рессорного подвешивания); 11 — демпфер гашения вертикальных колебаний кузова (2-й ступени рессорного подвешивания); 12 — страховочный трос демпферов виляния; 13 — регулируемая тяга торсиона поперечной устойчивости кузова; 14 — траверса
Рама немоторной тележки (рис. 3.117) по своей конструкции максимально приближена к раме моторной тележки. Различия имеются только в конструкции поперечных балок. Из-за отсутствия тягового привода на поперечных балках рамы нет кронштейнов для подвески поддона с ТЭД и кронштейна для подсоединения С-образного упора подвески редуктора. Вместо них присутствуют три, а не два кронштейна 1 для крепления клещевых механизмов.
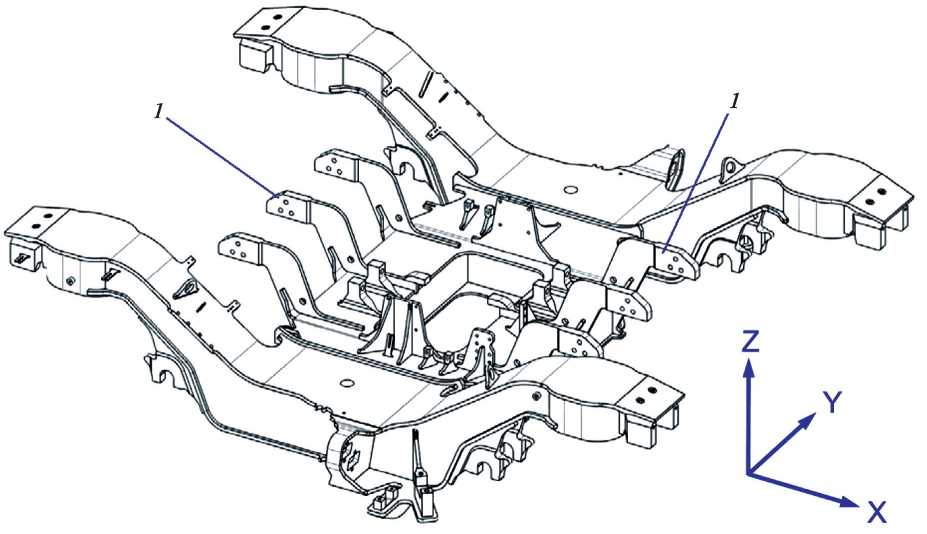
Рис. 3.117. Рама немоторной тележки: 1 — кронштейн крепления клещевых механизмов фрикционных тормозов
Аксонометрический разбор узлов немоторной тележки представлен на рис. 3.118.
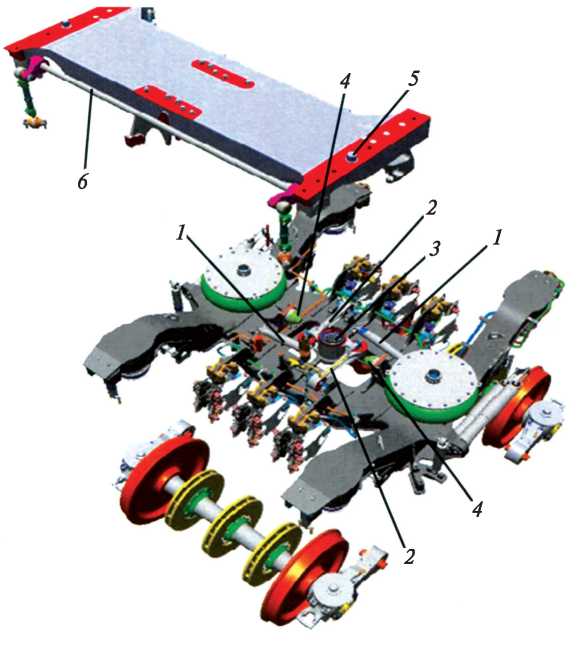
Рис. 3.118. Общий вид немоторной тележки: 1 — демпфер поперечного успокоения кузова; 2 — тяга передачи продольных усилий; 3 — лемнискатный механизм; 4 — упорный резиновый буфер; 5 — центрирующий штифт монтажа траверсы к раме кузова вагона; 6 — балка торсиона пружины качения (успокоение раскачивания вагона)
На рис. 3.119—3.122 изображены тормозные компоненты, смонтированные на немоторной тележке.
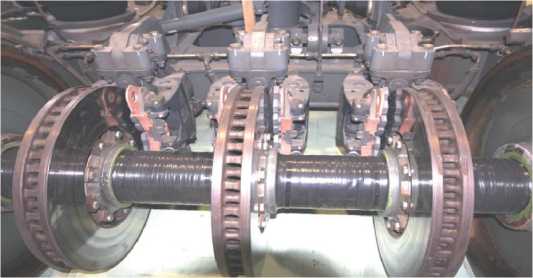
Рис. 3.119. Устройства тормозов в немоторной тележке
Узел крепления клещевых механизмов в немоторной тележке идентичен узлу моторной тележки.
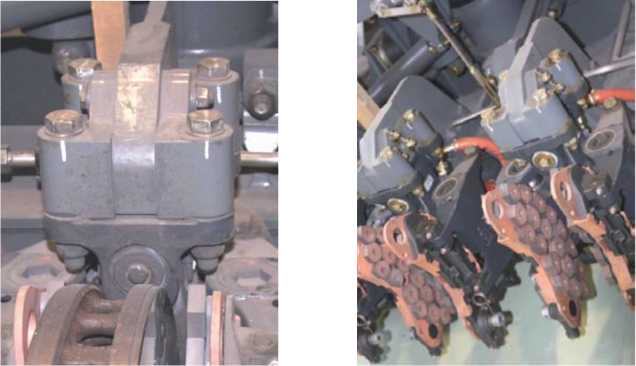
Рис. 3.120. Крепление клещей к раме немоторной тележки
Ось немоторной колесной пары, помимо зон основной напрессовки колесных центров 2 (см. рис. 3.121) и буксовых подшипников, имеет еще три зоны напрессовки суппортов тормозных дисков 4. Как и у моторной колесной пары, на немоторной колесной паре замена изношенного тормозного диска 4 требует распрессовки элементов колесной пары. Для обеспечения возможности напрессовки на ось суппортов тормозных дисков и колесных центров диаметры подступичных частей оси разные. Наибольший диаметр подступичной части оси — на месте напрессовки суппорта центрального тормозного диска.
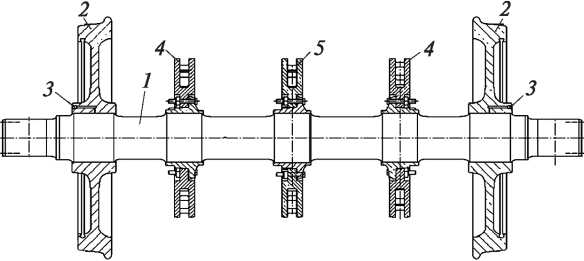
Рис. 3.121. Чертеж немоторной колесной пары: 1 — ось; 2 — колесный центр; 3 — технологическое отверстие для гидравлической распрессовки; 4 — вентилируемый тормозной диск; 5 — лопасти автоматической вентиляции тормозного диска
На рис. 3.122 представлены компоненты немоторной колесной пары.
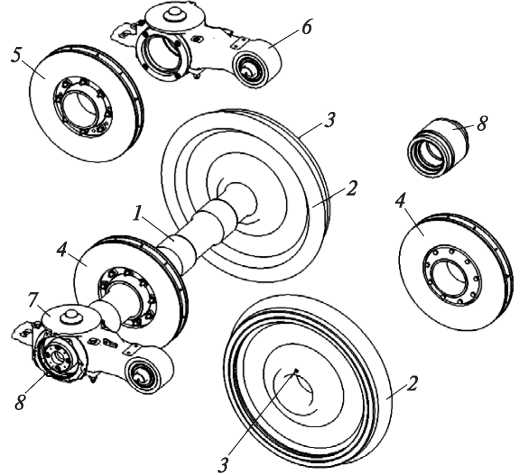
Рис. 3.122. Компоненты немоторной колесной пары: 1 — ось немоторной колесной пары; 2 — цельнокатаное колесо; 3 — резьбовая заглушка; 4 — тормозной диск (внешний); 5 — тормозной диск (центральный); 6 — корпус буксы колесной пары, правый; 7 — корпус буксы колесной пары, левый; 8 — букса колесной пары
Осевые тормозные диски (рис. 3.123) имеют кольцеобразный литой корпус с поперечно расположенными охлаждающими перегородками. Диски изготовлены из специальной литой стали или специального литого чугуна с шаровидным графитом. Для максимальной скорости 350 км/ч диски выполнены с шириной фрикционного кольца (поверхности трения) В > 135 мм.
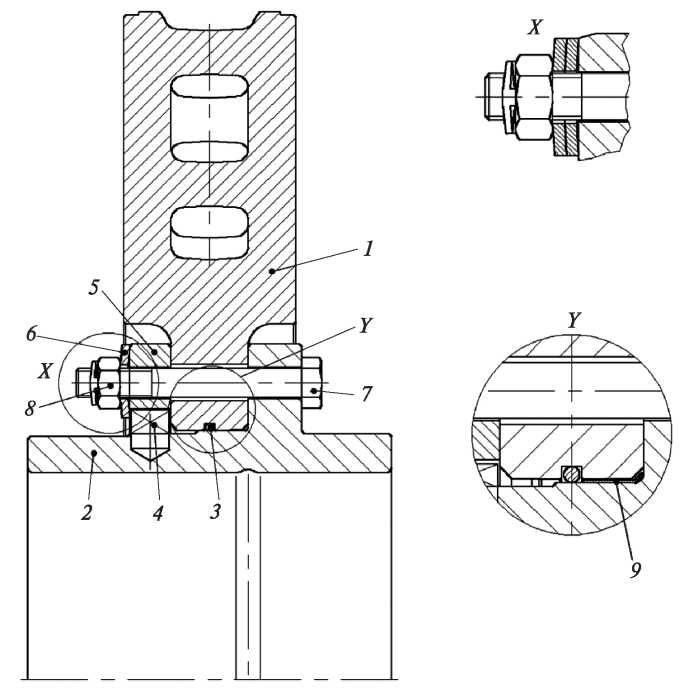
Рис. 3.123. Осевой тормозной диск на оси немоторной колесной пары с плоской посадкой (с предохраненным от проворота зажимным кольцом): 1 — фрикционный диск; 2 — ступица; 3 — центрирующее кольцо (алюминий); 4 — болт для стопорения вращения диска на ступице 2; 5 — зажимное кольцо; 6 — зажимные шайбы (или втулка в зависимости от исполнения); 7 — винт с шестигранной головкой; 8 — стопорная гайка; 9 — промежуточное кольцо
Фрикционный диск 1 в цельном исполнении крепится фланцем при помощи кольцеобразно расположенных резьбовых соединений по центру к ступице 2 посредством зажимного кольца 5. Ступица 2 посажена с натягом на ось колесной пары. Для недопущения возможности проворота осевого тормозного диска вокруг ступицы между зажимным кольцом 5 и ступицей 2 закладываются болты для стопорения вращения диска на ступице 4, которые своей верхней частью плотно покрываются специальными выступами зажимного кольца 5. Толщина фрикционного диска и размер охлаждающих перегородок рассчитаны таким образом, что при торможении не возникает перегрев. При конструировании фрикционного диска одновременно был учтен аспект минимального общего веса.
При проверке степени износа фрикционного диска необходимо ориентироваться на следующие основные параметры (рис. 3.124—3.126):
G — предельное значение износа, G = B — 2T — 2 • 0,5 мм;
H — вогнутый износ (выкружка);
T — глубина износа.
На тормозных дисках в сочетании с такими органическими накладками, как KRS, UIC:
- выкружка H = 2,0 мм макс.;
- косой износ S = 2,0 мм макс.;
- выемки глубиной 1,0 мм макс.
На тормозных дисках в сочетании со стандартными агломерационными накладками или с агломерационными накладками ISOBAR:
- выкружка H = 1,0 мм макс.;
- косой износ S = 1,0 мм макс.;
- выемки глубиной 1,0 мм макс.
Фрикционный диск проверяется на отсутствие трещин по следующим данным.
Волосные трещины. Во время эксплуатации тормозных дисков, подвергающихся воздействиям высоких температур, на фрикционных дисках появляется тонкая сетка трещин небольшой глубины, так называемых волосных трещин. Такие трещины не оказывают негативного влияния на эксплуатацию и допустимы по всей поверхности фрикционного диска.
Глубокие трещины. Глубокие трещины — это трещины, которые не проходят от внутреннего до внешнего диаметра шлифованного кольца (поверхности трения), но уходят вглубь шлифованного кольца. На шлифованных кольцах дисков может быть несколько таких трещин, если при этом длина трещины b < 50 мм, а расстояние между двумя трещинами составляет по меньшей мере 10 мм. Глубокие трещины длиной 50 мм < b < 70 мм допустимы лишь условно. Эксплуатация разрешается до следующей контрольной проверки. Глубокие трещины длиной b > 70 мм не допускаются. Фрикционные диски с подобными трещинами следует незамедлительно заменить.
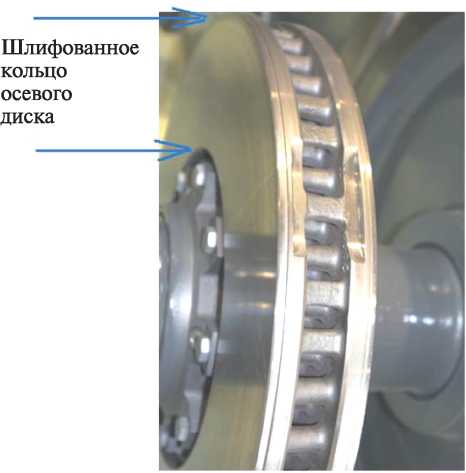
Рис. 3.124. Изображение тормозного диска на оси немоторной колесной пары
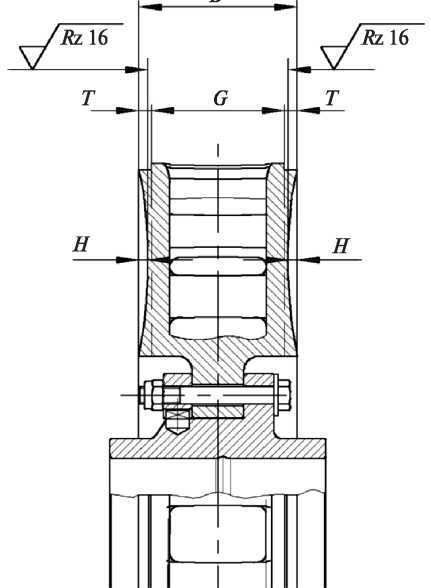
Рис. 3.126. Вогнутый износ тормозного диска немоторной колесной пары
Поверхностные трещины. Поверхностные трещины — это открытые трещины, которые не уходят вглубь шлифованного кольца. На поверхности трения может быть несколько поверхностных трещин, если длина трещины a < 100 мм (трещина не задевает ни внутренний, ни внешний диаметр), длина трещины b < 100 мм (трещина задевает внутренний или внешний диаметр), a > 100 мм, если расстояние между внешним и внутренним диаметром составляет по меньшей мере 10 мм и расстояние между двумя трещинами больше 50 мм. Поверхностные трещины, расположенные на шлифованных кольцах друг против друга, не могут быть длиннее 70 мм.
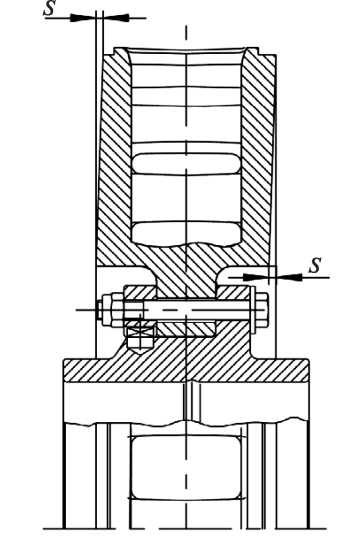
Рис. 3.125. Косой износ тормозного диска немоторной колесной пары
Такие поверхностные трещины допустимы лишь однократно. Глубокие трещины недопустимы на соединительных фланцах составных фрикционных дисков, на соединительных накладках. Сквозные трещины недопустимы на обоих шлифованных кольцах фрикционного диска от внутреннего до внешнего диаметра и до канала для охлаждения. Также недопустимы сквозные трещины на соединительных фланцах составных фрикционных дисков.
Первоначальный опыт эксплуатации колесных пар с профилем «AG Siemens»
Первоначальные испытания высокоскоростных электропоездов «Сапсан» на железных дорогах РФ привели к образованию выщербин на поверхностях катания колесных пар в зимнее время. Это произошло вследствие того, что профиль колесных пар не совпадает с принятым в сети ОАО «РЖД» , а именно является более коническим. В итоге это стало причиной концентрации напряжений в узкой зоне, расположенной ближе к гребню колесной пары, и разрушению контактного слоя (рис. 3.127).
В первоначальном варианте профиля в условиях скоростей выше 200 км/ч и при температурах окружающего воздуха ниже 20 °С наблюдались подобные выбоины на поверхностях катания колесных пар.
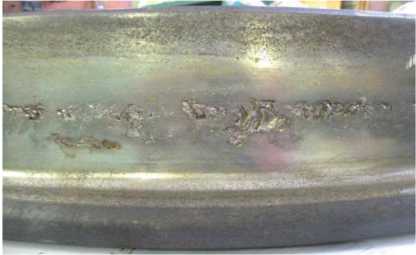
Рис. 3.127. Выбоины на поверхности круга катания колесных пар ЭВС «Сапсан»
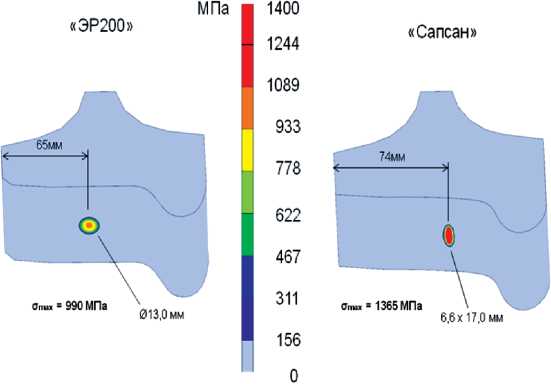
Рис. 3.128. Сравнение профиля ЭР200 ОАО «РЖД» с первоначальным профилем колес ЭВС «Сапсан»
Из рис. 3.128 видно, что на первоначальном профиле имеется сосредоточение контактных напряжений 1365 МПа против 990 МПа на профиле ЭР200.
Повреждения поверхности катания колес ЭВС «Сапсан» были вызваны повышенными контактными напряжениями по отношению к пределу контактной выносливости материала колеса. После переточки профилей колес на профиль ЭР200 описываемое явление прекратилось, поскольку контактная нагрузка с профилем ЭР200 способствует более распределенному по ширине круга катания пятну касания и, как следствие, недопущению напряжений, превышающих предел текучести.