Конструкция тележки высокоскоростного поезда «Сапсан» (международное обозначение — SF-520) выполнена на основе требований стандарта плавности и обеспечения комфортности поездки. Тележки электропоезда «Сапсан» разработаны и изготовлены на заводе в городе Грац (Австрия), являющемся крупнейшим в Европе производителем многих видов тележек для подвижного состава различных типов. На рис. 3.1 изображены тележки SF-500 электропоезда ICE 3 немецких железных дорог, на базе которого был создан электропоезд «Velaro RUS» «Сапсан».
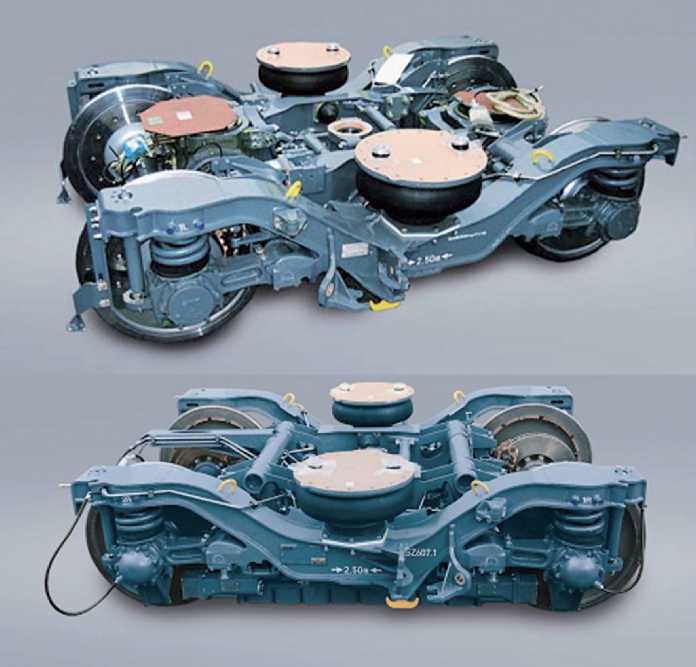
Рис. 3.1. Моторная и немоторная тележки SF-500 электропоезда ICE 3
Моторная тележка и ее характеристики
Основные технические характеристики тележки SF-520: Максимальная эксплуатационная скорость ......................... 300 км/ч База............................................................ 2600 мм Ширина колеи (российская широкая колея)......................... 1520 мм Диаметр колеса (нового / изношенного) .......................... 920 / 840 мм Минимальный радиус кривой в составе / отдельном вагоне.......... 250/150 м Максимальная нагрузка от колесной пары на рельсы................ 19 т Масса тележки со шкворнем и поперечной балкой................... около 11,193 т Высота опоры кузова вагона...................................... 1109 мм Вторичное устройство передачи продольного усилия................ шкворень тележки Подвешивание тягового двигателя................................. опорно-рамное с поперечным подрессориванием Привод ......................................................... второго класса с поперечным подрессориванием тягового двигателя Тормоз.......................................................... механический (пневматический), стояночный, рекуперативно-реостатный Расположение тормозных дисков .................................. на колесном центре (моторная тележка) на оси (немоторная тележка) Расположение суппорта тормозного механизма...................... на тележке
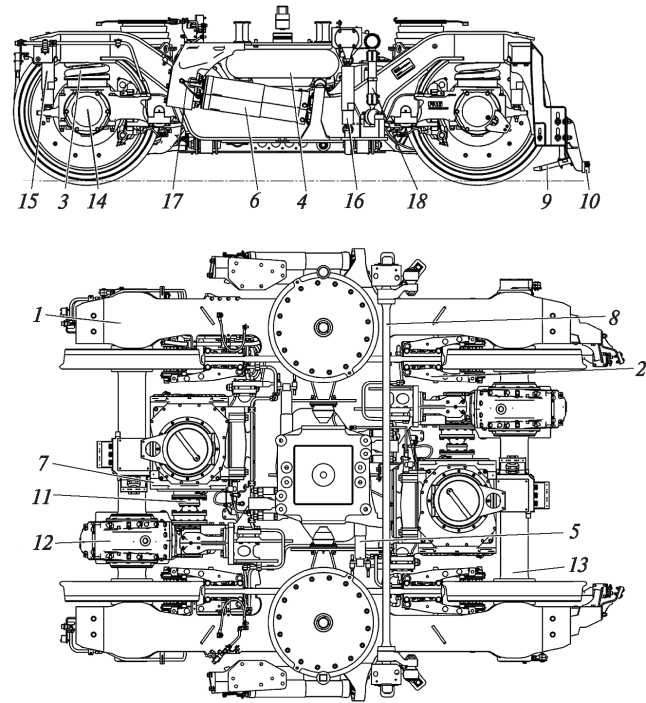
Рис. 3.2. Моторная тележка SF-520 ЭВС «Сапсан» (показана без траверсы): 1 — рама тележки; 2 — клещевой механизм фрикционного тормоза; 3 — цилиндрическая пружина 1-й ступени рессорного подвешивания; 4 — пневморессора; 5 — демпфер успокоения поперечных колебаний кузова; 6 — демпфер виляния тележки; 7 — ТЭД; 8 — торсион поперечной устойчивости кузова; 9 — форсунка песочницы первой колесной пары; 10 — путеочиститель первой колесной пары; 11 — зубчатая муфта; 12 — корпус тягового редуктора; 13 — ось колесной пары; 14 — букса; 15 — демпфер гашения вертикальных колебаний рамы тележки (1-й ступени рессорного подвешивания); 16 — демпфер гашения вертикальных колебаний кузова (2-й ступени рессорного подвешивания); 17 — страховочный трос демпферов виляния; 18 — регулируемая тяга торсиона поперечной устойчивости кузова
Конструктивно моторные и немоторные тележки ЭВС «Сапсан» (SF-520) являются максимально унифицированными узлами. Различия между ними обусловливаются только наличием компонентов тягового привода и его расположением в моторной тележке. Далее рассмотрена конструкция моторной тележки и ее компонентов (рис. 3.2, 3.3), затем будет дан обзор отличий конструкции немоторной тележки.

Рис. 3.3. Моторная тележка SF-520 ЭВС «Сапсан» (показана с траверсой): 1 — ось моторной колесной пары; 2 — цилиндрическая пружина рессорного подвешивания 1-й ступени; 3 — шарнирное соединение рычага буксы колесной пары; 4 — устройство передачи продольного усилия (шкворень траверсы тележки); 5 — ограничитель максимальных амплитуд поперечных смещений кузова относительно тележки; 6 — клещевой механизм фрикционного тормоза; 7 — статор тягового двигателя; 8 — патрубок системы принудительной вентиляции ТЭД; 9 — балка торсиона поперечной устойчивости кузова; 10 — система пневматического подрессоривания (2-я ступень рессорного подвешивания); 11 — устройство управления пневморессорами моторной тележки; 12 — резиновый упорный буфер рамы тележки; 13 — демпфер виляния тележки; 14 — рама моторной тележки; 15 — поперечная балка — траверса; 16 — металлическая трубка пневматических соединений; 17 — датчик угловой скорости вращения колесной пары; 18 — датчик поперечного ускорения рамы тележки; 19 — гаситель колебаний (вертикальный демпфер) 2-й ступени рессорного подвешивания; 20 — шильда (табличка); 21 — форсунка песочницы; 22 — центрирующий посадочный штифт траверсы на раму кузова; 23 — гаситель поперечных колебаний кузова — поперечный демпфер 2-й ступени рессорного подвешивания; 24 — гаситель колебаний 1-й ступени; 25 — тяговый поводок рессорного подвешивания 2-й ступени; 26 — корпус лемнискатного механизма — седло шкворня траверсы, имеющее две степени свободы относительно рамы тележки; 27 — соединительная коробка силовых проводов статора ТЭД
Траверса (надрессорная балка) — это поперечная пустотелая металлическая балка, конструктивно относящаяся к тележке, которая со стороны тележки опирается на нее через две пневморессоры и шкворневое устройство, а со стороны кузова прикреплена к его раме болтовыми соединениями (см. рис. 3.21). Пневморессоры являются 2-й ступенью рессорного подвешивания, причем воздушные каналы питания пневморессор расположены непосредственно внутри траверсы. Шкворневое устройство является осью поворота рамы тележки относительно кузова и служит для передачи продольных и поперечных усилий от рамы тележки к раме кузова. Демонтаж тележки выполняется вместе с траверсой. Шкворневое устройство траверсы закреплено на ней жестким болтовым соединением, нижняя часть шкворня траверсы посажена в корпус лемнискатного механизма, который дает возможность шкворню проворачиваться в нем вокруг вертикальной оси. Сам корпус лемнискатного механизма шарнирно связан с рамой тележки системой тяговых поводков и поперечных демпферов 2-й ступени рессорного подвешивания.
Кинематические схемы моторной тележки
Кинематическая схема помогает более четко представить работу элементов тележки: схему передачи усилий, схему взаимодействия элементов во всех плоскостях и т.д. Все элементы кинематической схемы лишь приближенно соответствуют своим истинным геометрическим (чертежным) размерам.
Ниже представлены три кинематические схемы моторной тележки ЭВС «Сапсан» (рис. 3.4—3.6). Кинематические схемы немоторных тележек в части рессорного подвешивания 1-й и 2-й ступеней и соединения тележек с рамой кузова ничем не отличаются от кинематических схем моторных тележек. Различие состоит в том, что в немоторных тележках передача тормозного усилия на каждую ось колесной пары осуществляется не двумя, а тремя клещевыми механизмами, закрепленными вдоль поперечной балки рамы тележки и передающими тормозное усилие через три тормозных диска, закрепленных на средней части оси каждой немоторной колесной пары.
Рассмотрим рис. 3.4 — кинематическую схему моторной тележки (рессорное подвешивание 1-й и 2-й ступеней).
Моторная тележка ЭВС «Сапсан» включает следующие основные компоненты: две колесные пары 2, сварная рама тележки 3 и траверса тележки 10. Эти основные компоненты тележки связывает между собой двухступенчатое рессорное подвешивание. Буксы колесных пар 4 жестко закреплены болтовым соединением в разъемных буксовых рычагах-балансирах 5, которые одной стороной шарнирно связаны с рамой тележки резинометаллическими сайлент-блоками 6, а с другой стороны соединяются с ней цилиндрической пружиной 7 и демпфером 8. Элементы 4, 5, 6, 7 и 8 образуют 1-ю ступень рессорного подвешивания. Вертикальную нагрузку воспринимает цилиндрическая пружина 7, горизонтальную, продольную и поперечную нагрузки — мощный сайлент-блок 6.
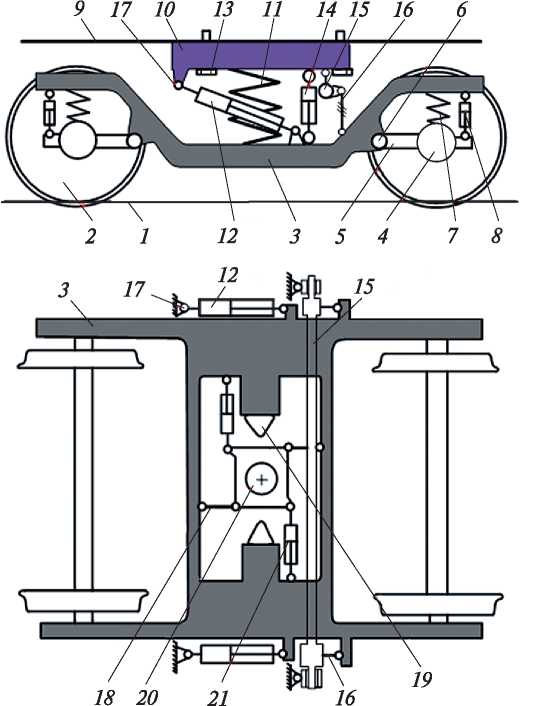
Рис. 3.4. Кинематическая схема моторной тележки (рессорное подвешивание 1-й и 2-й ступеней) (вид сбоку и сверху): 1 — уровень головок рельсов; 2 — колесная пара; 3 — сварная рама тележки; 4 — букса колесной пары; 5 — разъемный (разрезной) буксовый рычаг (балансир) 1-й ступени рессорного подвешивания; 6 — сайлент-блок буксового рычага 1-й ступени рессорного подвешивания; 7 — цилиндрическая пружина 1-й ступени рессорного подвешивания; 8 — демпфер гашения вертикальных колебаний 1-й ступени рессорного подвешивания; 9 — уровень боковой продольной балки кузова; 10 — траверса тележки; 11 — пневморессора 2-й ступени рессорного подвешивания (на схеме условно изображена в виде пружины); 12 — демпфер виляния тележки; 13 — болт крепления траверсы к раме кузова; 14 — демпфер гашения вертикальных колебаний кузова 2-й ступени рессорного подвешивания; 15 — балка торсиона поперечной устойчивости кузова; 16 — регулируемая тяга балки торсиона поперечной устойчивости кузова; 17 — шарнирное крепление демпфера виляния к траверсе тележки; 18 — тяга передачи продольных усилий; 19 — ограничительно-упорный резиновый буфер; 20 — шкворень траверсы, вставленный в центральный рычаг лемнискатного механизма; 21 — демпфер гашения поперечных колебаний кузова
2-ю ступень рессорного подвешивания образуют две пневморессоры 11 с системой поводков и демпферов 18, 21. Пневморессоры 11 связывают траверсу тележки 10 с рамой 3, опираются своими центрами на средние части продольных балок рамы тележки 3 напротив колесных центров и воспринимают на себя вертикальную нагрузку. Траверса тележки как единая металлическая конструкция закреплена болтами 13 к балкам рамы кузова вагона 9, но является компонентом тележки. При повороте тележки относительно траверсы, центром которой является вертикальная ось шкворня траверсы тележки, вставленного в лемнискатный механизм 20, пневморессоры деформируются. Центральный рычаг лемнискатного механизма 20 представляет собой стальную втулку, имеющую свободу в вертикальной и в поперечной к оси пути плоскости относительно рамы тележки, связанную с ней двумя тяговыми поводками 18 и двумя поперечными демпферами 21. Лемнискатный механизм является седлом шкворня траверсы, позволяющим шкворню вращаться в нем при повороте рамы тележки. В вертикальной плоскости шкворень закреплен в лемнискатном механизме резьбовым соединением. Продольные горизонтальные усилия от рамы тележки к шкворню траверсы передают две металлические тяги 18, шарнирно соединенные с лемнискатным механизмом 20 и с рамой тележки 3. Поперечные усилия между рамой тележки и траверсой воспринимают на себя несколько компонентов: это сами пневморессоры 11, демпферы гашения поперечных колебаний кузова 21 и ограничительно-упорные резиновые буфера 19. Центрирование положения траверсы относительно рамы тележки осуществляется пневморессорами, а успокоение в поперечном направлении — демпферами 21. Из рис. 3.4 видно, что демпферы 21 развернуты относительно друг друга на 180°. Это позволяет им гасить своим ходом отбоя поперечные колебания в левую и в правую стороны. При сильных возмущениях кузова относительно рамы тележки в поперечном направлении пневморессоры 11 и демпферы 21 могут не справиться с ними, и тогда упорная поверхность шкворня 20 упирается в резиновый буфер 19, который также является ограничителем поперечного перемещения траверсы 10. Сам лемнискатный механизм представляет собой корпус, через который проходит вертикальный стержень — шкворень траверсы, и может на нем свободно поворачиваться вокруг вертикальной оси. Шкворень траверсы десятью болтами зафиксирован на траверсе, а в лемнискатном механизме уплотнен резиновой втулкой. Вертикальный демпфер 14 гасит вертикальные колебания кузова — траверсы 10 относительно рамы тележки 3. Вертикальные демпферы 14 находятся с обеих сторон тележки симметрично относительно ее центра. Для успокоения поперечных раскачиваний кузова (качки кузова относительно его продольной оси по типу «крен влево — крен вправо») установлен торсион — балка круглого профиля для поперечной устойчивости кузова 15. Торсион представляет собой ровную крепкую круглую балку, выполненную из специальной стали и имеющую высокий момент сопротивления на скручивание. Торцы торсиона закреплены на резиновых шарнирах к траверсе 10, рядом с обеих сторон торсиона на него жестко напрессованы кулачки, к которым шарнирно закреплены регулировочные тяги 16. С противоположной стороны эти тяги 16 шарнирно закреплены к раме тележки 3. Таким образом, торсион не препятствует синхронному вертикальному перемещению кузова — траверсы 10 относительно рамы тележки 3, но, как только эти вертикальные колебания становятся несинхронными, торсион 15 с тягами 16 сразу начинает их гасить и принудительно выравнивает положение кузова — траверсы 10 относительно рамы тележки 3.
В отличие от классических боковых скользунов пневморессора 11 может воспринимать поворотные перемещения рамы тележки 3 относительно кузова — траверсы 10, но не способна их успокаивать. Это может привести к тому, что тележка относительно кузова будет вилять. Виляние тележки может оказать весьма негативное влияние на комфортность поездки. Особенно опасен режим, когда частота виляния тележки совпадет с естественной частотой виляния кузова и сможет образоваться резонанс, что недопустимо. Для гашения виляния тележки между траверсой 10 и рамой тележки 3 установлены демпферы виляния тележки 12 (по паре с каждой стороны). На рис. 3.4 (вид сверху) продемонстрировано, что левые и правые демпферы виляния 12 установлены в одну и ту же сторону. Таким образом, виляние рамы тележки 3 вправо гасит левая пара демпферов своим ходом отбоя, а виляние рамы тележки влево — правая пара демпферов 12. Демпферы 12 стоят парами для резервирования в случае выхода из строя одного из них.
Рассмотрим рис. 3.5 — кинематическую схему моторной тележки (подвешивание тяговых двигателей — ТЭД).
Для снижения неподрессоренной массы рамы тележки в поперечном направлении, а также для снижения уровня шумопередачи от тягового привода на раму тележки выполнено специальное подвешивание тяговых двигателей 9. Такой способ подвески тяговых двигателей нельзя назвать опорно-рамным, поскольку тяговые двигатели жестко закреплены в поддоне, подрессоренном в поперечном направлении к раме тележки. Оба тяговых двигателя 9 тележки жестко закреплены четырьмя болтами 12 к единому изделию — поддону тяговых двигателей 8. Сам поддон 8 закреплен на четырех цапфах рамы тележки 3 четырьмя листовыми рессорами 7. Это позволяет поддону 8 с тяговыми двигателями 9 перемещаться поперек оси пути. Для дополнительного успокоения этих поперечных перемещений поддона 8 установлены два взаиморазвернутых демпфера 10. Демпферы 10 шарнирно крепятся к поддону и к раме тележки. Поддон 8 является самой низкой частью тележки и имеет два штифта 11, предохраняющих его от падения в случае разрушения поперечных листовых рессор 7.
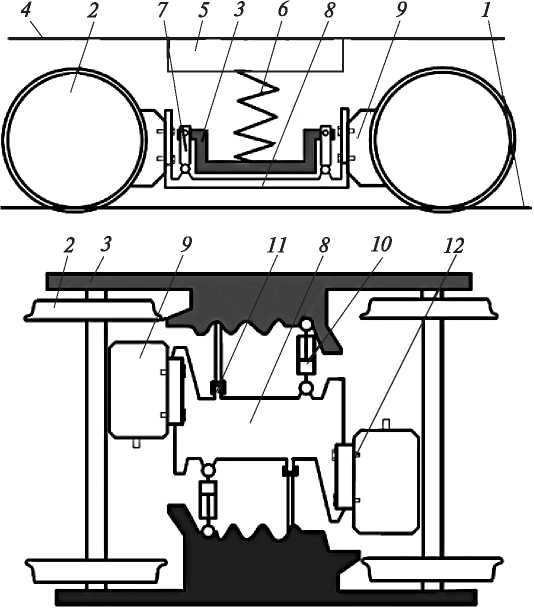
Рис. 3.5. Кинематическая схема моторной тележки (подвешивание ТЭД): 1 — уровень головок рельсов; 2 — колесная пара; 3 — сварная рама тележки; 4 — уровень боковой продольной балки кузова; 5 — траверса тележки; 6 — пневморессора 2-й ступени рессорного подвешивания; 7 — листовая рессора поперечных колебаний поддона тяговых двигателей; 8 — поддон тяговых двигателей; 9 — тяговый двигатель; 10 — демпфер гашения поперечных колебаний тягового двигателя; 11 — предохранительный болт подвески поддона тяговых двигателей; 12 — болт крепления статора тягового двигателя к поддону
Рассмотрим рис. 3.6 — кинематическую схему моторной тележки (передача сил тяги и торможения), позволяющую описать процесс передачи сил тяги и торможения при рекуперативно-реостатном торможении.
На вал ротора 12 тягового двигателя 4 и на вал малой шестерни 7 напрессован фланец. Оба фланца соединены зубчатой муфтой 14. В отличие от упругой резино-кордовой муфты зубчатая муфта передает момент вращения с очень малым угловым зазором (свободным ходом), но имеет возможность свободного перемещения осей валов ротора и малой шестерни друг относительно друга во всех плоскостях и в поперечном к оси пути направлении. Амплитуда описанных выше перемещений строго ограничена параметрами зубчатой муфты 14. Малая шестерня 7 закреплена в подшипниках 15 в нижней половине корпуса редуктора 5. Большое зубчатое колесо 6 жестко напрессовано на ось колесной пары 1 и находится в постоянном зацеплении с малой шестерней 7 косозубой передачей. Верхняя половина корпуса редуктора 5 соединена с нижней сочленяющими болтами, но усилий практически не несет. С одной стороны корпус редуктора опирается на ось колесной пары 1 через подшипниковый опорный узел корпуса редуктора 13, а с другой стороны закреплен упруго через два резиновых амортизатора подвески редуктора 8 к С-образному кронштейну 9 рамы тележки. С-образный кронштейн 9 закреплен болтами 10 к поперечной балке рамы тележки 2.
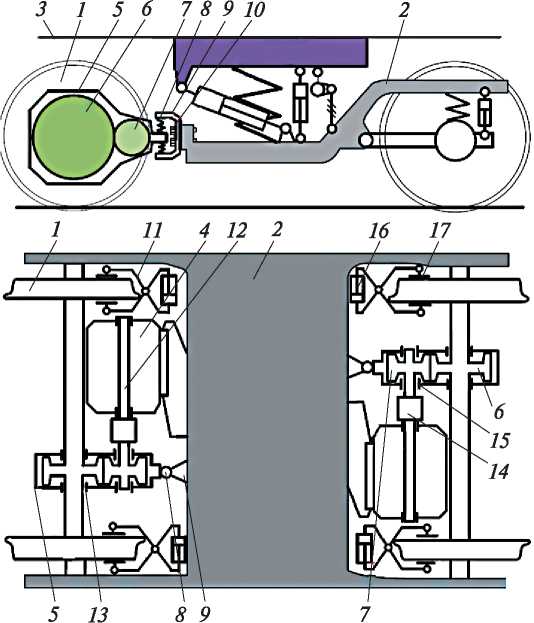
Рис. 3.6. Кинематическая схема моторной тележки (передача сил тяги и торможения): 1 — колесная пара; 2 — сварная рама тележки; 3 — уровень боковой продольной балки кузова; 4 — ТЭД; 5 — корпус тягового редуктора; 6 — большое зубчатое колесо (далее БЗК); 7 — малая шестерня (далее МШ); 8 — резиновый амортизатор упругой подвески корпуса тягового редуктора; 9 — С-образный кронштейн подвески корпуса тягового редуктора; 10 — болт крепления С-образного кронштейна подвески редуктора к раме; 11 — клещевой механизм механических тормозов; 12 — вал ротора ТЭД; 13 — опорный узел корпуса редуктора; 14 — зубчатая муфта; 15 — подшипник малой шестерни; 16 — тормозной цилиндр клещевого механизма; 17 — тормозные колодки (композиционные накладки) клещевого механизма механических тормозов
Силы фрикционного (механического) торможения активируются клещевыми механизмами механических тормозов 11. Сами клещевые механизмы 11 закреплены болтами к поперечной балке рамы тележки и посредством прижатия тормозных колодок — композиционных накладок 17 к тормозным дискам, закрепленным на колесных центрах, создают тормозное усилие на колесную пару. Детали клещевого механизма 11 приводятся в действие тормозными цилиндрами 16, входящими в состав клещевого механизма.
Обзор компонентов моторной тележки
Рама моторной тележки
Рама тележки (рис. 3.7) является несущим устройством ходовой части и ее монтажных деталей. От рамы тележки передаются статические и динамические нагрузки от кузова вагона на колесные пары. Таким же образом принимаются усилия, возникающие в режиме тяги (приводящие и тормозные усилия). Рама тележки выполнена в форме буквы «Н» и состоит из двух сваренных продольных балок 1 коробчатого профиля, которые соединены друг с другом двумя поперечными балками коробчатого профиля 2. На продольной балке располагаются кронштейны для монтажа вертикального рессорного подвешивания 1-й ступени, вертикального рессорного подвешивания 2-й ступени, поворотного демпфера, пружины качения, шарнирного соединения колесной пары и петли для подъема рамы краном. На продольной балке моторной тележки дополнительно располагаются кронштейны дисковых тормозов. Центральное соединение 2 служит опорой для всех кронштейнов продольных рычагов подвески, поперечного рессорного подвешивания, а также кронштейнов узла привода на моторной тележке и кронштейнов тормозов на моторной и немоторной тележках.
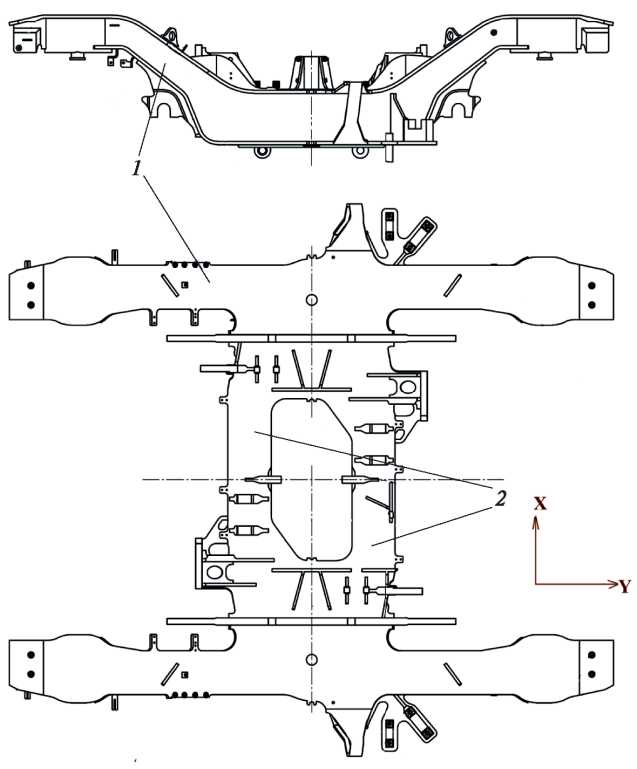
Рис. 3.7. Рама моторной тележки: 1 — продольные балки; 2 — центральное соединение (поперечные балки)
Геометрические данные рамы моторной тележки Длина рамы тележки..................................................................... 3360 мм Ширина рамы тележки.................................................................... 3069 мм Высота рамы тележки.................................................................... 815 мм Вес рамы тележки....................................................................... 2250 кг Расстояние между колесными парами в направлении оси Х.................................. 2600 мм Расстояние между пружинами первой ступени подвешивания в направлении оси Y............. 2100 мм Расстояние между упругими элементами второй ступени подвешивания в направлении оси Y... 2000 мм
На рис. 3.8 изображена рама моторной тележки с обзором монтажных точек.
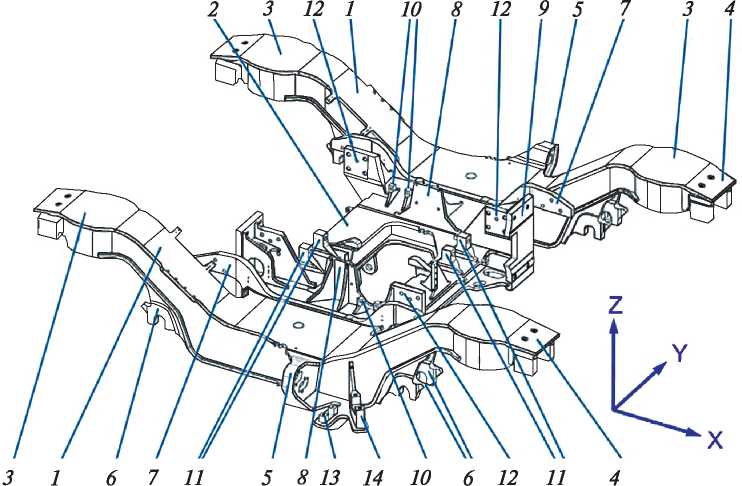
Рис. 3.8. Рама моторной тележки с обзором монтажных точек: 1 — боковая балка рамы тележки; 2 — поперечная балка рамы тележки; 3 — опорные гнезда цилиндрических пружин 1-й ступени рессорного подвешивания; 4 — приливы рамы для подсоединения вертикальных гасителей 1-й ступени рессорного подвешивания, кронштейнов песочниц и рельсоочистителей; 5 — приливы рамы для подсоединения демпферов виляния тележки; 6 — приливы рамы для прикрепления шарнирного соединения колесной пары; 7 — кронштейны для закрепления к раме клещевых механизмов тормозов; 8 — кронштейны резиновых буферов ограничения поперечных смещений кузова; 9 — кронштейны для присоединения С-образных упоров подвески тягового редуктора; 10 — точки подсоединения к раме гасителей поперечных колебаний кузова; 11 — точки подсоединения к раме тяговых поводков; 12 — кронштейны крепления к раме листовых рессор подвески поддона с ТЭД; 13 — точки подсоединения к раме вертикальных гасителей 2-й ступени рессорного подвешивания; 14 — точки подсоединения к раме регулируемых тяг торсиона поперечной устойчивости кузова
Рессорное подвешивание 1-й ступени
1-я ступень рессорного подвешивания (рис. 3.9) классически устраивается между колесной парой и рамой тележки. Она обеспечивает амортизацию рамы тележки относительно колесной пары с одновременной передачей усилий во всех плоскостях. Колесные центры колесных пар являются цельнокатаными и амортизацию нагрузок не осуществляют.
Гнездо в продольной балке рамы тележки 9 через вкладыш 10 опирается на цилиндрические пружины 1 и 2. Пружины опираются на резинометаллический амортизатор 5, лежащий на тарели разъемного буксового балансира 8. Резинометаллический амортизатор 5 первым воспринимает ударные вертикальные нагрузки от буксы колесной пары и обеспечивает электрическую изоляцию буксы от рамы тележки. Все защитное и рабочее заземление на системе постоянного тока выполнено только через четыре заземляющих устройства (ЗУ) на корпусах букс вагонов DR Т 02 и DR Т 09. Листовая рессора 4 несет чисто защитную функцию. В случае внезапного сильного вертикального возмущения на подвешивание со стороны буксы шпинтон 7 упрется в малый внутренний резинометаллический амортизатор 6, опирающийся на листовую рессору 4. В состоянии полной загрузки вагона между шпинтоном 7 и амортизатором 6 имеется зазор в 28 мм, аварийный прогиб листовой рессоры 4 может составлять 7 мм, так как она упрется в центральный выступ тарели буксового балансира. Если и этого в случае экстремального динамического удара будет недостаточно, то еще 22 мм сжатия подвески может обеспечить деформация малого амортизатора 6. Дальнейшее сжатие подвешивания может привести к его повреждению и поломке вертикального демпфера. Вертикальный демпфер 3 обеспечивает успокоение вертикальных колебаний во время хода отбоя — хода рамы тележки вверх относительно буксы. Верхнее крепление к раме тележки и нижнее крепление к рычагу буксового балансира 14 вертикального демпфера выполнено шарнирными сайлент-блоками 12. Внутри сайлент-блоков 12 находится резиновая втулка, через которую пропущен стержень, закрепляющийся болтами 11 к раме тележки и к буксовому балансиру 14.
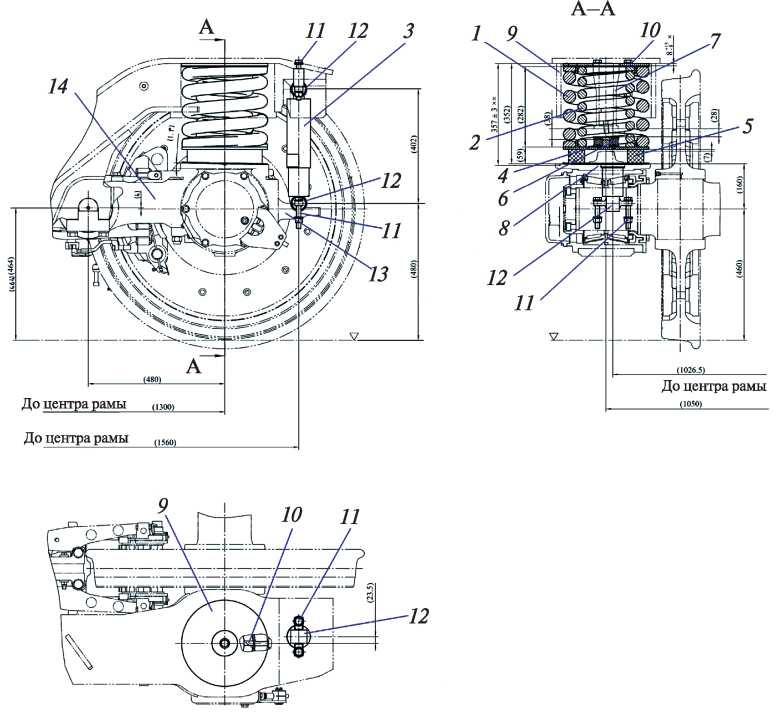
Рис. 3.9. 1-я ступень рессорного подвешивания: 1 — большая наружная цилиндрическая пружина 1-й ступени подвешивания; 2 — малая внутренняя цилиндрическая пружина 1-й ступени подвешивания; 3 — гаситель колебаний 1-й ступени (вертикальный демпфер); 4 — листовая рессора (упругая чаша); 5 — резинометаллический амортизатор; 6 — малый упорный резинометаллический амортизатор; 7 — шпинтон; 8 — тарель разъемного буксового балансира; 9 — гнездо рамы тележки цилиндрической пружины 1-й ступени подвески; 10 — вкладыш для рессорного подвешивания 1-й ступени; 11 — болт крепления вертикального демпфера; 12 — шарнирное соединение (сайлент-блок) вертикального демпфера; 13 — кронштейн разъемного буксового балансира для подсоединения вертикального демпфера; 14 — буксовый балансир
Все усилия в горизонтальной плоскости от буксы колесной пары к раме тележки (тягово-тормозные и поперечные) воспринимает шарнирное соединение буксового балансира 6 к раме тележки в виде сайлент-блока (рис. 3.10). Сайлент-блок вставлен в цилиндрическое отверстие буксового рычага, торцевые части металлического валика сай-лент-блока буксового поводка фиксируются к раме тележки крепежным суппортом 3 посредством болтовых соединений крепежными болтами 7 с моментом затяжки 220 Н-м. Конструкция металлического валика сайлент-блока обеспечивает поддержание зазора 7 мм между буксовым балансиром и рамой тележки. Предохранительная планка 4 служит для недопущения падения буксового балансира 6 вместе с сайлент-блоком 5 при изломе или откручивании крепежных болтов 7.
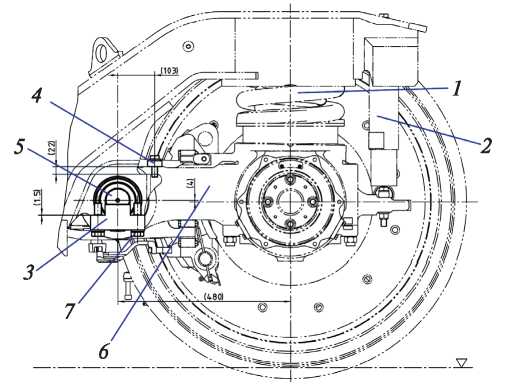
Рис. 3.10. Связь сайлент-блока, буксового балансира и рамы тележки: 1 — большая наружная цилиндрическая пружина 1-й ступени подвешивания; 2 — вертикальный демпфер; 3 — крепежный суппорт валика сайлент-блока; 4 — предохранительная планка (аварийный улавливатель); 5 — валик сайлент-блока буксового рычага; 6 — буксовый балансир; 7 — крепежный болт с шестигранной головкой
На рис. 3.11 изображен монтаж сопряженного оборудования на ходовой части.
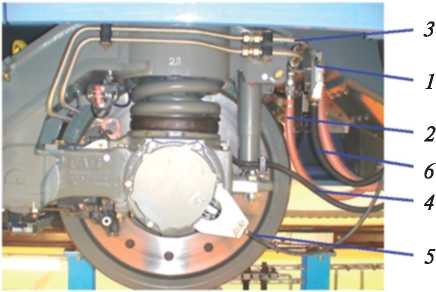
Рис. 3.11. Колесная пара с 1-й ступенью рессорного подвешивания и сопряженное оборудование: 1 — датчик поперечного ускорения тележки; 2 — армированный пневмошланг; 3 — металлические трубки подводки сжатого воздуха к пневмоцилиндрам клещевых механизмов тормозов; 4 — кабель к термодатчикам контроля нагрева букс; 5 — кабель к датчику угловой скорости вращения колесной пары; 6 — кабель к датчику поперечного ускорения
На рис. 3.12 и 3.13 изображен буксовой балансир в сборке и поэлементно соответственно.
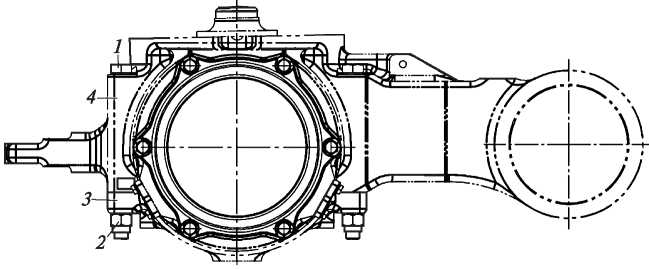
Рис. 3.12. Разъемный буксовый балансир: 1 — стяжной болт зажима корпуса буксы; 2 — гайка стяжного болта зажима; 3 — нижняя половинка зажима корпуса буксы; 4 — верхняя половинка зажима корпуса буксы (тело самого буксового рычага)
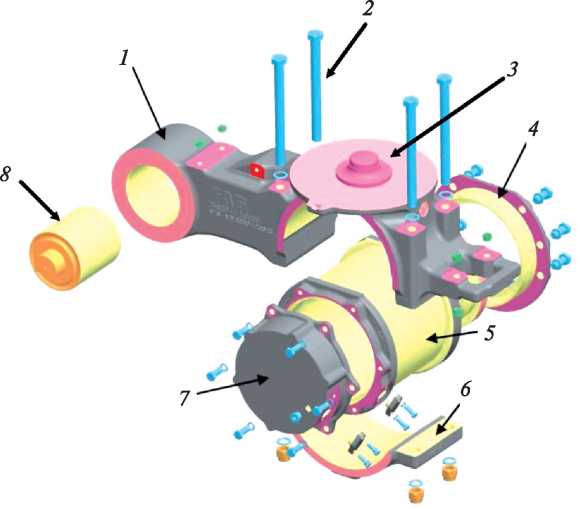
Рис. 3.13. Элементы узла разъемного балансира: 1 — рычаг буксового балансира; 2 — стяжные болты; 3 — тарель цилиндрической пружины 1-й ступени рессорного подвешивания; 4 — задняя крышка буксы; 5 — блок TAROL; 6 — съемная нижняя часть буксового балансира; 7 — передняя крышка буксы; 8 — сайлент-блок
Разъемный буксовый балансир является корпусом буксы, одетым вокруг подшипника (блок TAROL).
Демонтаж моторной колесной пары заключается в откручивании шарнирного соединения сайлент-блока — отворачивании болтов (позиция 7 на рис. 3.10) буксового балансира от рамы тележки, отсоединении вертикального демпфера первой ступени подвешивания — отворачивании болтов (позиция 11 на рис. 3.9), расстыковке зубчатой муфты тягового привода, откручивании резьбовых соединений С-образного упора подвески редуктора и отключения всех электрических соединений к колесной паре. Далее колесная пара с редуктором и с буксовыми балансирами может опускаться вниз и эвакуироваться.
Демонтировать моторную колесную пару можно и другим способом: без разборки 1-й ступени рессорного подвешивания. Необходимо открутить и демонтировать вертикальный демпфер 1-й ступени, установить вместо него специальную резьбовую стяжку 1-й ступени рессорного подвешивания, разобрать буксовый балансир путем отворачивания его стяжных болтов (позиции 1, 2 на рис. 3.12), болтов задней крышки буксы от буксового балансира (рис. 3.9), далее выполнить процедуры, указанные в первом способе, и после этого моторная колесная пара высвобождается вниз с тяговым редуктором, с корпусом буксового подшипника (блок TAROL), но уже без разъемных буксовых балансиров.
Резьбовая стяжка 1-й ступени рессорного подвешивания является специальным технологическим вспомогательным элементом, необходимым для процесса монтажа и демонтажа колесной пары с тележки описанным способом. Стяжка устанавливается на место вертикального демпфера (рис. 3.14) и удерживает сжатое положение основных цилиндрических рессор при отсутствии колесной пары в тележке.
На рис. 3.15 изображен принцип действия аварийного улавливателя буксового балансира, заключающийся в зацеплении пластины на болтовом креплении и выступа на раме тележки.
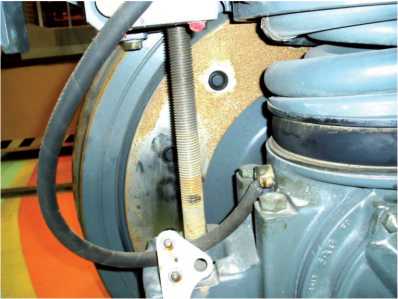
Рис. 3.14. Резьбовая стяжка рессорного подвешивания 1-й ступени
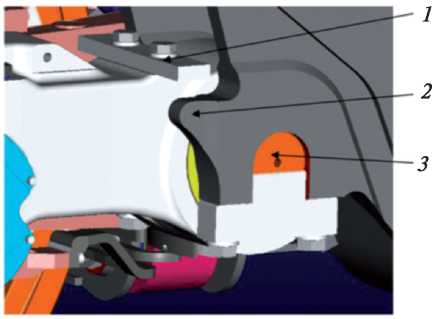
Рис. 3.15. Аварийный улавливатель буксового балансира: 1 — пластина аварийного улавливателя; 2 — выступ аварийного улавливателя; 3 — букса направляющей системы подвески колесной пары
Рессорное подвешивание 1-й ступени немоторной тележки выполнено идентично.
На рис. 3.16 показана тележка с собранным рессорным подвешиванием 1-й ступени, но без колесной пары. На рисунке видно, что вместо резьбовой стяжки стоит вертикальный демпфер. Буксовый балансир максимально опущен вниз, что не соответствует его положению под нагрузкой. Наличие специальной резьбовой стяжки дает возможность фиксировать 1-ю ступень в положении нагрузки при выкатке колесной пары, что необходимо при ее оперативной замене под составом на специализированной позиции ремонтного цеха.
Демонтаж колесной пары (рис. 3.17) происходит следующим образом: тележка вывешивается специальным домкратом, который передвигается продольно под составом, затем между колесной парой и тележкой расстыковываются все необходимые соединения, выдвижной рельс 1 перемещается во внешнюю часть колеи в продольном направлении, и специальный домкрат выводит в сторону демонтируемую колесную пару.
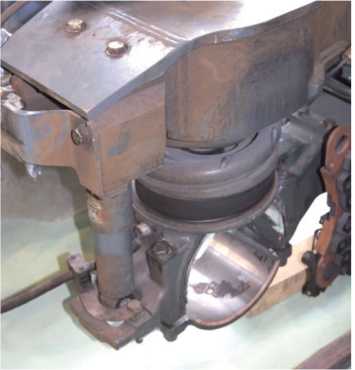
Рис. 3.16. Вид рессорного подвешивания 1-й ступени с внутренней стороны тележки (колесная пара демонтирована)
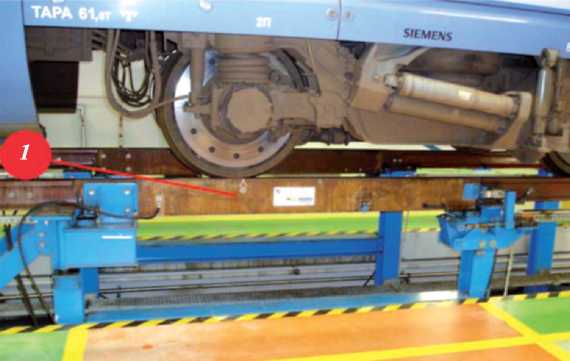
Рис. 3.17. Специализированная позиция демонтажа колесных пар под поездом: 1 — выдвижной рельс
Датчик поперечного ускорения тележки (рис. 3.18, 3.19) относится к устройствам безопасности и предназначен для передачи системам управления поезда информации о наличии вибрации рамы тележки в поперечном к оси пути направлении выше критического уровня. Подробное описание устройства и алгоритма работы датчиков ускорения и температурных датчиков букс приведены в гл. «Системы безопасности».
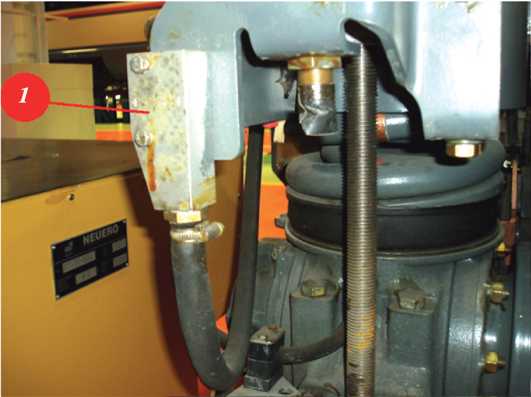
Рис. 3.18. Внешний вид датчика поперечного ускорения: 1 — корпус датчика поперечного ускорения.
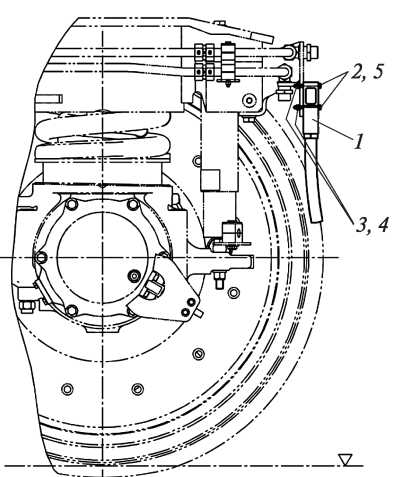
Рис. 3.19. Монтажная позиция датчика поперечного ускорения тележки: 1 — датчик поперечного ускорения; 2 — винт шестигранный; 3 — гайка шестигранная; 4 — предохранительная шайба; 5 — шайба.
Рессорное подвешивание 2-й ступени
На рис. 3.20 изображено смонтированное на тележке оборудование 2-й ступени рессорного подвешивания.
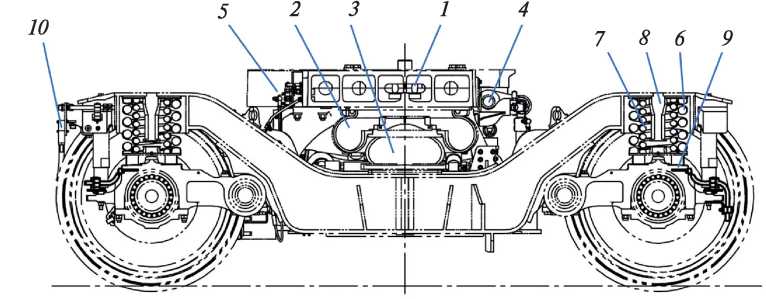
Рис. 3.20. Тележка в разрезе вдоль центра боковой балки рамы: 1 — траверса с внутренними полостями подачи сжатого воздуха к основным пневморессорам; 2 — основная пневморессора; 3 — аварийная монолитная резиновая рессора; 4 — балка торсиона поперечной устойчивости; 5 — устройство выравнивания уровня полов вагонов; 6 — основная наружная цилиндрическая пружина (относится к 1-й ступени); 7 — дополнительная внутренняя малая цилиндрическая пружина (относится к 1-й ступени); 8 — шпинтон (относится к 1-й ступени); 9 — буксовый балансир (относится к 1-й ступени); 10 — устройство контроля тележки (датчик поперечного ускорения)
2-ю ступень рессорного подвешивания устраивают между кузовом и рамой тележки. Основу рессорного подвешивания 2-й ступени составляют пневморессоры, осуществляющие функцию амортизации при передаче основной вертикальной нагрузки от кузова вагона на раму тележки. При этом они могут испытывать некоторую деформацию на скручивание при прохождении поездом кривых участков пути.
Верхняя поперечная балка тележки — траверса — закреплена болтовыми соединениями к раме кузова, является центральным соединительным элементом между тележкой и кузовом вагона и служит дополнительным единым резервуаром для двух пневморессор системы пневматического подрессоривания (рис. 3.21).
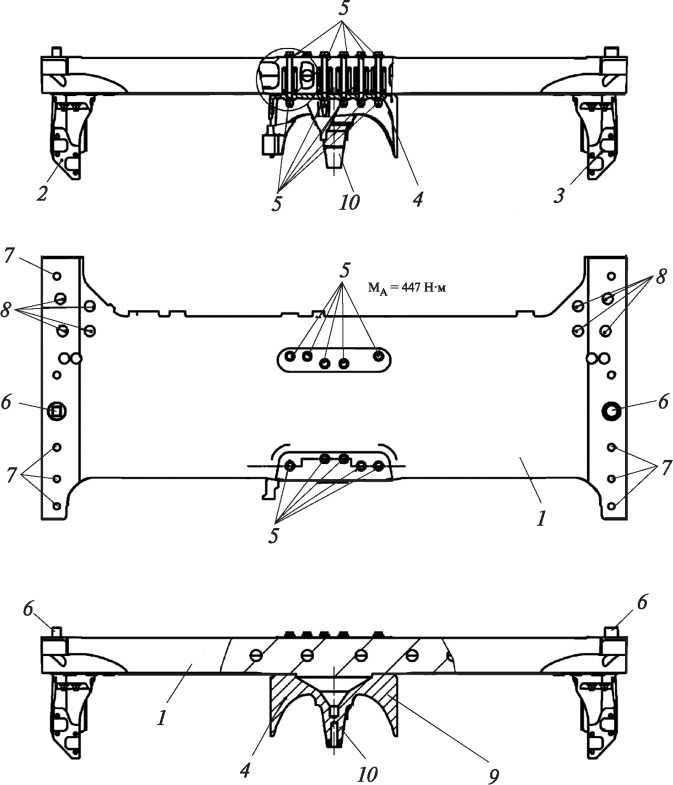
Рис. 3.21. Траверса: 1 — траверса; 2, 3 — кронштейны поворотных демпферов (демпферов виляния тележки); 4 — шкворень; 5 — крепежные болтовые соединения шкворня к траверсе с моментом затяжки 447 Н-м; 6 — посадочный штифт; 7 — отверстия под болтовые соединения траверсы к раме кузова вагона (10 шт.); 8 — болтовые соединения траверсы с кронштейном поворотного демпфера; 9 — упорная планка шкворня; 10 — посадочная коническая втулка шкворня в лемнискатный механизм
Кроме того, траверса предназначена для передачи тягового и тормозного усилия на кузов вагона. Она строго центрируется посадочными отверстиями рамы кузова вагона на посадочные штифты 6 и крепится к раме кузова десятью болтами. Один посадочный штифт выполнен цилиндрической формы, другой — квадратной. К самой траверсе подсоединены болтовыми соединениями кронштейны поворотных демпферов 2, 3, шкворень 4, устройство выравнивания полов, вертикальные демпферы 2-й ступени, опора балки торсиона. В траверсе дополнительно имеется соединительная резьба для подключения устройств подачи сжатого воздуха, например клапана устройства управления пневморессорами, спускного клапана. Траверса содержит две точки подключения защитного заземления между ней и кузовом вагона, а также между ней и рамой тележки. Внутренние ограничители поворота тележки действуют между шкворнем и рамой тележки. Внешние ограничители поворота тележки действуют между упорными планками 9 шкворня траверсы и специальными резиновыми буферами рамы тележки. Также в поперечную балку интегрирован кронштейн опор балки торсиона с самим торсионом (показан далее).
На рис. 3.22 изображена тележка, демонтированная с состава поезда. Наглядно продемонстрировано подсоединение к траверсе кронштейнов поворотных демпферов 1 (по шесть болтов каждый), подсоединение вертикального демпфера 2-й ступени подвешивания 2, подсоединение опоры торсиона 3, регулировочные тяги торсиона 6, видны 10 болтов крепления шкворня 4, два посадочных цилиндрических штифта 5 и 10 отверстий под болты крепления траверсы к раме кузова вагона. В таком положении траверса обязательно должна быть предохранена от опрокидывания на бок, что обычно достигается посредством деревянных распорок необходимой длины.
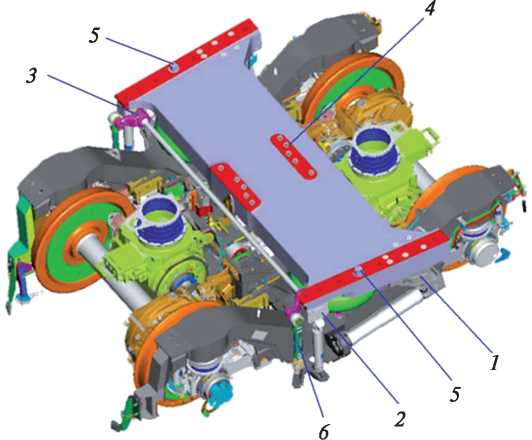
Рис. 3.22. Вид сверху моторной тележки с траверсой: 1 — кронштейн траверсы для монтажа поворотных демпферов; 2 — кронштейн вертикального демпфера второй ступени гашения колебаний; 3 — узел крепления торсиона; 4 — крепежные болты шкворня; 5 — посадочные штифты; 6 — регулировочные тяги торсиона
На рис. 3.23 изображена посадочная поверхность кузова вагона на траверсу.
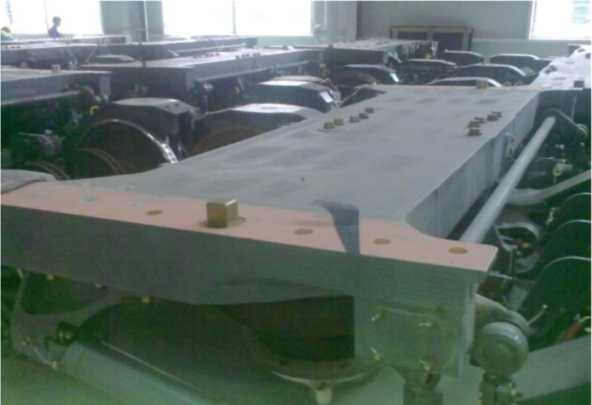
Рис. 3.23. Траверса
На рис. 3.24 не изображена траверса, а также поворотные и вертикальные демпферы 2-й ступени, торсиона. В корпус шкворня вставлены все 10 болтов его крепления к траверсе. Траверса является компонентом тележки и демонтируется с поезда вместе с ней.
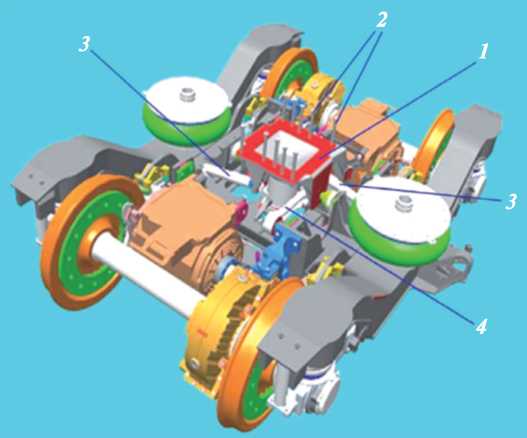
Рис. 3.24. Общий вид моторной тележки без траверсы (вид сверху): 1 — литой корпус шкворня; 2 — болты крепления корпуса шкворня к траверсе; 3 — успокоитель поперечных колебаний кузова вагона; 4 — тяговый поводок
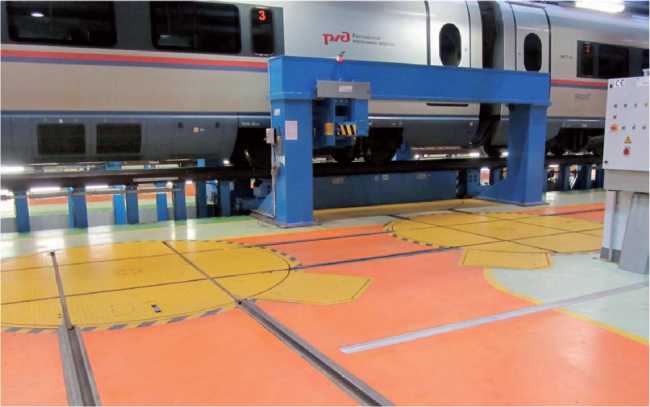
Рис. 3.25. Специализированная позиция смены тележек
На специализированной позиции смены тележек (рис. 3.25), оборудованной системой поворотных опускающихся рельсов и вертикальных домкратов, замена тележки производится следующим образом:
- указанный вагон устанавливается дефектной тележкой на специальную позицию с домкратом и площадкой поворотными и опускающимися рельсами;
- отворачиваются все 10 болтов, крепящие траверсу к боковым балкам рамы кузова вагона;
- расстыковываются все электрические и пневматические соединения тележки с кузовом;
- кузов вагона поддомкрачивается;
- дефектная тележка опускается вниз до уровня технологических рельсов, поворачивается на 90° и далее эвакуируется в боковом направлении;
- на втором поворотном кругу она вновь поворачивается на 90° и далее эвакуируется с поэтапными поворотами (см. рис. 3.25) в подкрановое поле мостового крана зоны ремонта тележек;
- аналогичным способом в обратном порядке подводится новая тележка;
- траверса новой тележки закрепляется болтами к раме кузова;
- убираются домкраты кузова;
- пристыковываются все электрические и пневматические соединения тележки к вагону.
Система пневматического подрессоривания расположена между рамой тележки и поперечной балкой в качестве подвешивания 2-й ступени. Пневморессоры (рис. 3.26) передают вертикальные и частично (в весьма малом соотношении) боковые усилия. При этом пневморессоры одновременно не препятствуют всем относительным смещениям между тележкой и кузовом вагона. При повороте рамы тележки относительно кузова (относительно траверсы) пневморессоры терпят некоторую деформацию. При выходе из строя пневморессоры или системы подачи сжатого воздуха кузов вагона опускается на аварийные рессоры. Между аварийной рессорой и рамой тележки проложены изготовленные из пластмассы вставки 3 и полимерные регулировочные шайбы 4, с помощью которых устанавливается точный уровень кузова вагона. Подача сжатого воздуха в пневморессору из траверсы осуществляется посредством штуцера подключения воздуха на диафрагменной пластине. Уплотнение стыковочного узла «траверса—пневморессора» осуществляется посредством шайбы (диафрагменной пластины) 8 с уплотнительным элементом на штуцере подключения воздуха. Болтовое соединение 6 служит для фиксации диафрагменной пластины на траверсе. Болтовое соединение 11 со стороны рамы тележки предназначено для фиксации основания полимерных регулировочных шайб 4 пневморессоры на раме тележки.
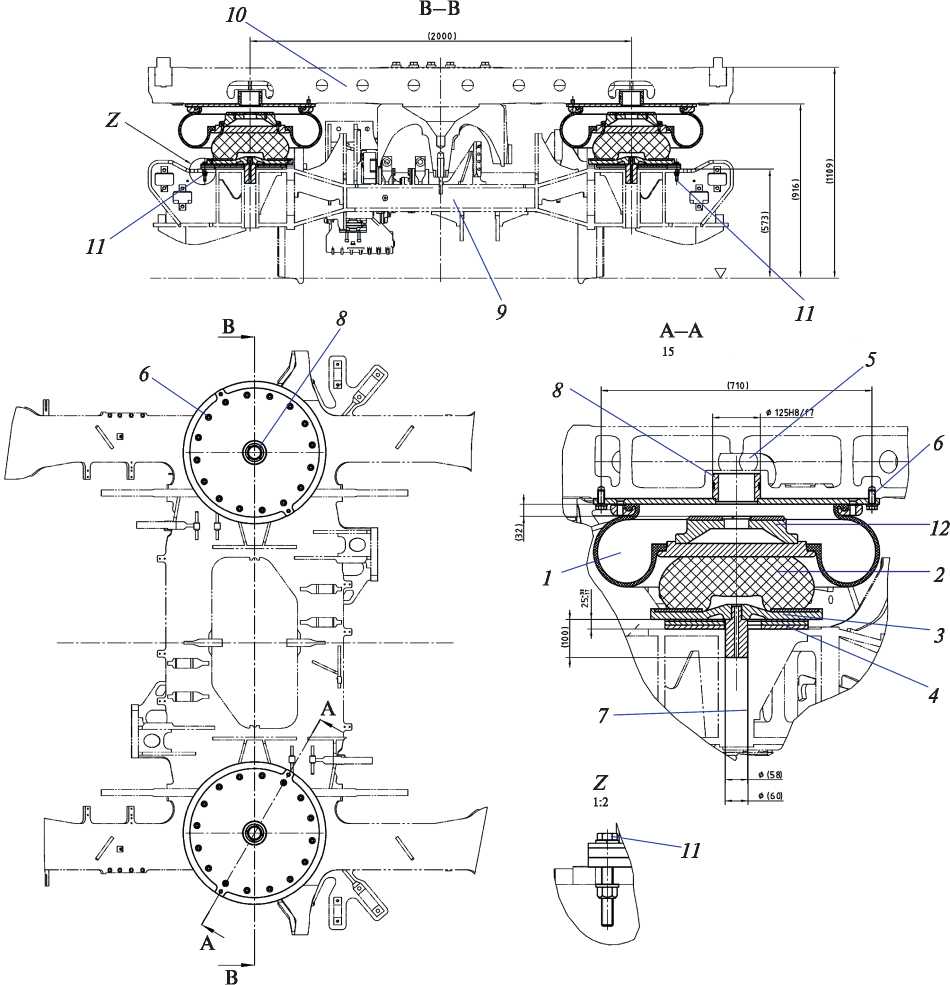
Рис. 3.26. Пневморессоры: 1 — основная рабочая пневморессора; 2 — аварийная (монолитная) рессора; 3 — основная вставка пневморессоры; 4 — полимерная регулировочная шайба; 5 — каналы сжатого воздуха внутри траверсы; 6 — болты крепления верхней стыковочной шайбы пневморессоры к траверсе; 7 — вертикальный посадочный канал в раме тележки; 8 — верхняя стыковочная шайба (диафрагменная пластина) пневморессоры с траверсой с уплотнителем; 9 — рама тележки; 10 — траверса; 11 — болтовое соединение со стороны рамы тележки; 12 — промежуточная шайба
Аварийная рессора 2 представляет собой резиновую монолитную структуру, на которую может опираться траверса тележки через промежуточную шайбу 12 в случае выхода из строя рабочей пневморессоры 1. Комфортность поездки в данном вагоне при этом несколько ухудшается. На рис. 3.27 показан узел крепления наружной оболочки основной пневморессоры к стыковочной шайбе траверсы. При сборке этого узла должны соблюдаться условия герметичности. На рис. 3.28, 3.29 изображен узел пневморессоры и аварийной рессоры в сборе.
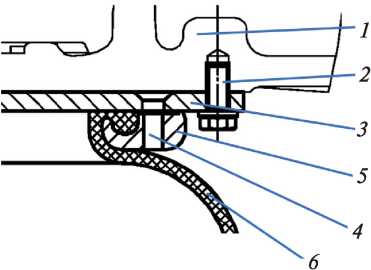
Рис. 3.27. Узел крепления наружной оболочки основной пневморессоры: 1 — траверса; 2 — болт крепления верхней стыковочной шайбы к траверсе; 3 — верхняя стыковочная шайба; 4 — винт крепления верхнего бортового кольца к верхней стыковочной шайбе; 5 — верхнее бортовое кольцо; 6 — наружная оболочка основной пневморессоры.
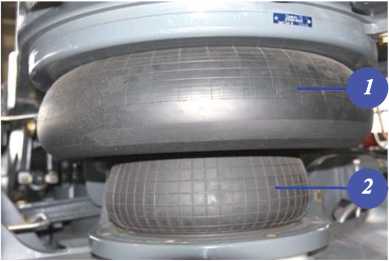
Рис. 3.28. Основная пневморессора (1) и аварийная рессора (2)
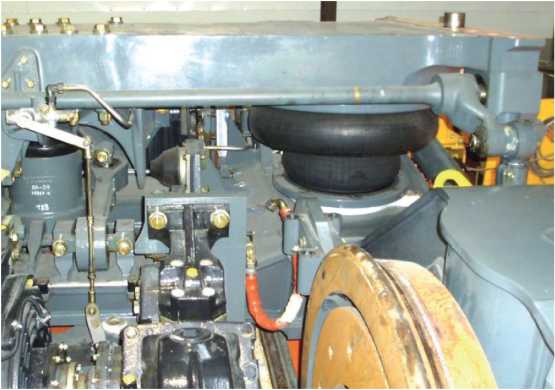
Рис. 3.29. Основная пневморессора и аварийная рессора с рамой тележки и с траверсой
На рис. 3.30 представлено устройство управления пневморессорами.
Поступление сжатого воздуха в основную пневморессору производится через траверсу. На рис. 3.26 (позиция 5) был виден разрез канала воздуха внутри траверсы тележки и его соединение с верхним патрубком — воздуховодом рабочей пневморессоры. Пневморессора получает сжатый воздух из питательной магистрали «НВ» через разобщительные краны L02 посредством специального редукционного клапана, открывающего доступ воздуха к системе пневморессоры только когда давление в питательной магистрали превысит 6,7 атм. Траверса тележки имеет два специальных клапана автоматической регулировки давления в пневморессорах, что необходимо для поддержания постоянной высоты кузова. Клапаны находятся с обеих сторон траверсы. Один клапан 3 (см. рис. 3.30) производит основную регулировку давления в обоих пневморессорах одновременно, второй клапан, аналогичный клапану 3, но располагающийсяс наружной стороны тележки, обеспечивает быстрый сброс давления при резком движении кузова вагона — траверсы 2 вверх. Задача устройств — вне зависимости от загрузки вагонов поддерживать одинаковый уровень высоты рам кузовов. Это называется механизмом выравнивания уровня полов.
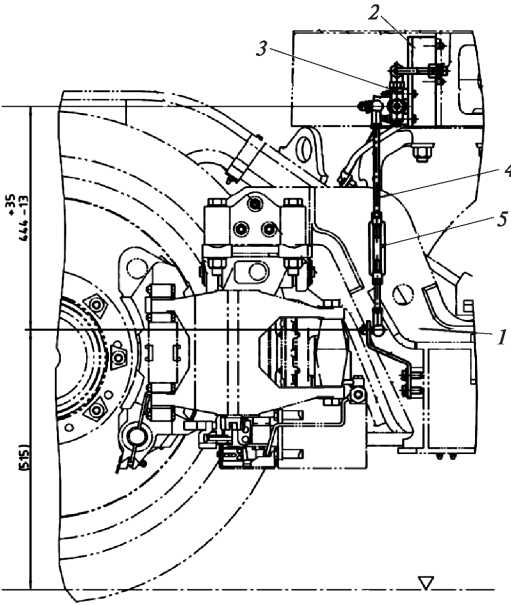
Рис. 3.30. Устройство управления пневморессорами (устройство выравнивания уровня пола вагона): 1 — рама тележки; 2 — траверса; 3 — клапан управления давлением воздуха в пневморессорах; 4 — рычаг клапана; 5 — регулировочная муфта рычага.
Клапан имеет специальный регулирующий рычаг 4 (рис. 3.31), установленный между траверсой и рамой тележки (аналогично авторежиму). При уменьшении расстояния между траверсой тележки и рамой тележки клапан увеличивает давление воздуха в пневморессорах тележки и наоборот. Длина рычагов клапана 4 может точно подгоняться под необходимую при регулировке благодаря наличию регулировочной муфты 5. Также траверса имеет дополнительные краны выпуска воздуха из пневморессор (подробнее все указанные пневмоустройства описаны в гл. «Пневмооборудование»). Практика эксплуатации устройств выравнивания полов в зимних условиях показала их уязвимость в условиях обильного налипания снега внутри тележки. Налипший снег существенно осложняет работу указанных устройств. В особо суровых условиях обильные массы налипшего снега могут производить шунтирование пневморессор между рамой тележки и траверсой, что существенно сказывается на комфортности поездки. Для обеспечения надежной работы клапана в зимних условиях конструктивно устанавливается защита, изображенная на рис. 3.32.
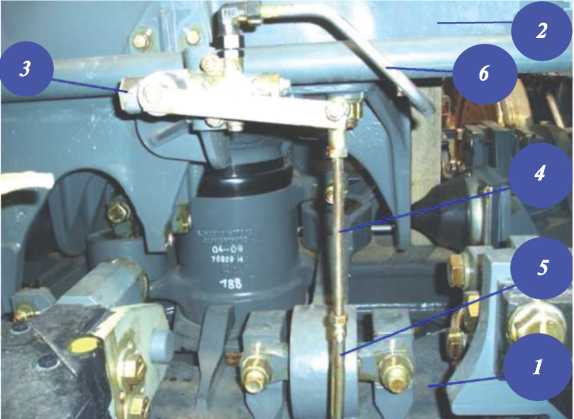
Рис. 3.31. Вид клапана системы выравнивания полов: 1 — рама тележки; 2 — траверса; 3 — сбрасывающий клапан пневморессор; 4 — рычаг клапана; 5 — регулировочная муфта рычага; 6 — трубка подвода сжатого воздуха к клапану
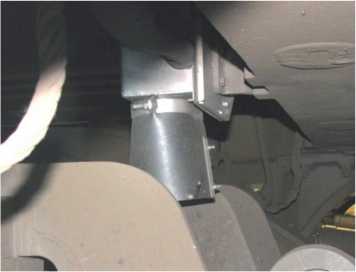
Рис. 3.32. Защита регулировочного клапана при его работе в зимних условиях
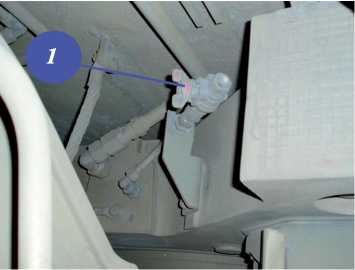
Рис. 3.33. Кран L16 (1) выпуска воздуха из пневмоканалов траверсы (из обеих пневморессор тележки)
Кран L16 находится под полом вагона рядом с траверсой и предназначен для непосредственного аварийного выпуска воздуха из обеих пневморессор тележки (рис. 3.33). Этот кран открывается только после перекрытия крана L02.
Успокоение вертикальных колебаний во 2-й ступени
На рис. 3.34 изображена схема размещения демпферов 2-й ступени рессорного подвешивания.
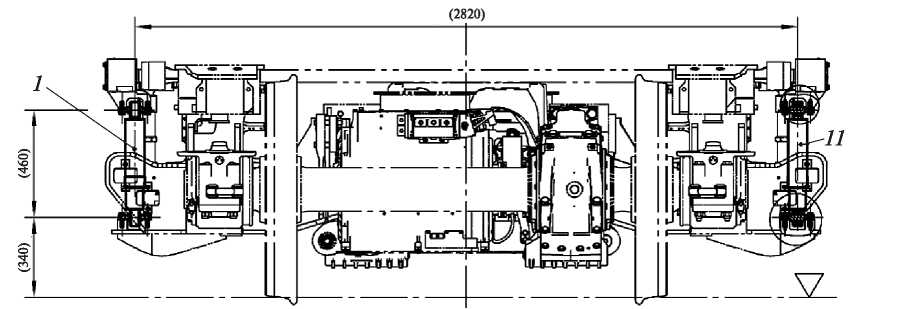
Рис. 3.34. Вертикальные демпферы 2-й ступени рессорного подвешивания (показаны цифрой 1)
На каждой тележке с обеих сторон установлено по два вертикальных демпфера. Демпферы успокаивают вертикальные колебания кузова (траверсы) относительно рамы тележки. Присоединение демпферов 1 (рис. 3.35) к раме тележки снизу и к траверсе сверху конструктивно выполнено одинаково. В монтажное кольцо демпфера впрессована резиновая втулка 3, через которую пропущен крепежный стержень 4, с обеих сторон закрепленный болтовыми соединениями 2 к соответствующим кронштейнам рамы тележки и траверсы. Такая конструкция обеспечивает и надежное крепление вертикального демпфера и возможность в определенных диапазонах не оказывать на шток вертикального демпфера изламывающих усилий при поперечных и поворотных перемещениях траверсы относительно рамы тележки.
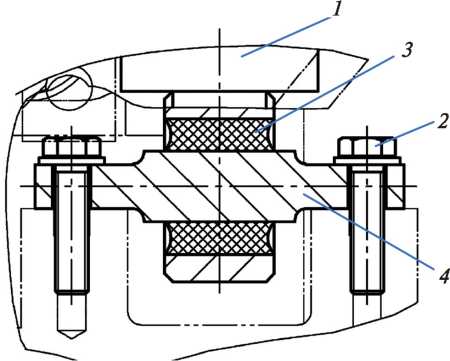
Рис. 3.35. Крепление демпфера вертикальных колебаний кузова: 1 — вертикальный демпфер 2-й ступени рессорного подвешивания; 2 — болтовое крепление вертикального демпфера; 3 — резиновая втулка; 4 — крепежный стержень вертикального демпфера
На рис. 3.36 наглядно проиллюстрирована 2-я ступень рессорного подвешивания, смонтированная на раме тележки.
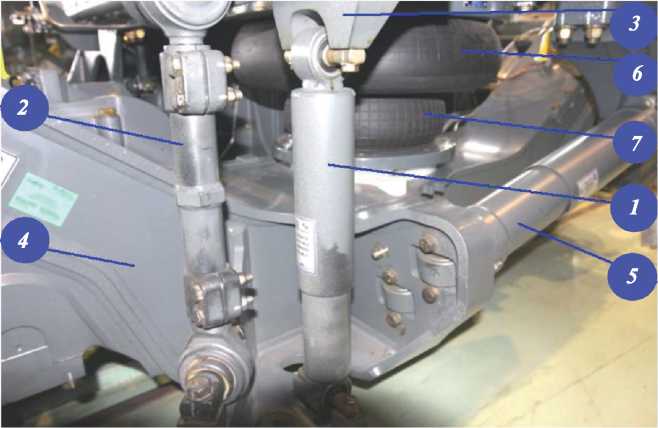
Рис. 3.36. Компоненты рессорного подвешивания 2-й ступени: 1 – вертикальный демпфер 2-й ступени рессорного подвешивания; 2 — регулируемая тяга торсиона; 3 — кронштейн вертикального демпфера на траверсе; 4 — рама тележки; 5 — поворотный демпфер; 6 – основная пневморессора; 7 – аварийная пневморессора
Успокоение боковой качки кузова во 2-й ступени
Тележка оборудована пассивной системой стабилизации наклона кузова, задачей которой является уменьшение наклона кузова в сторону, а также успокоение колебательных процессов наклона кузова при воздействии внешних возмущений: движение в кривой, по стрелочным переводам, сильный боковой ветер.
Принцип работы этого устройства абсолютно идентичен принципу работы стабилизатора поперечной устойчивости автомобиля, который уменьшает наклон кузова в сторону при движении в повороте, что положительно сказывается на безопасности виража и комфортности поездки.
Торсион является упругой балкой, работающей на скручивание. Балка торсиона выполнена из соответствующей стали, что позволяет ей иметь большой момент сопротивления на скручивание. Торсион снижает наклон кузова вагона во внешнюю сторону кривой. Таким образом, торсион гарантирует соблюдение габаритов приближения и служит для увеличения плавности хода. Также применение торсиона необходимо, если 2-я ступень рессорного подвешивания выполнена на пневмоподвеске. Пневморессоры являются сообщающимися друг с другом, через внутренние каналы траверсы сосудами и не могут самостоятельно предотвращать крен кузова в одну из сторон. В отличие от пневморессор цилиндрические пружины могут бороться с креном кузова, так как при сжатии той пружины, в сторону которой происходит наклон кузова, в ней возникает реактивное вертикальное усилие больше аналогичного усилия противоположной пружины. Это и способствует уменьшению крена вагона.
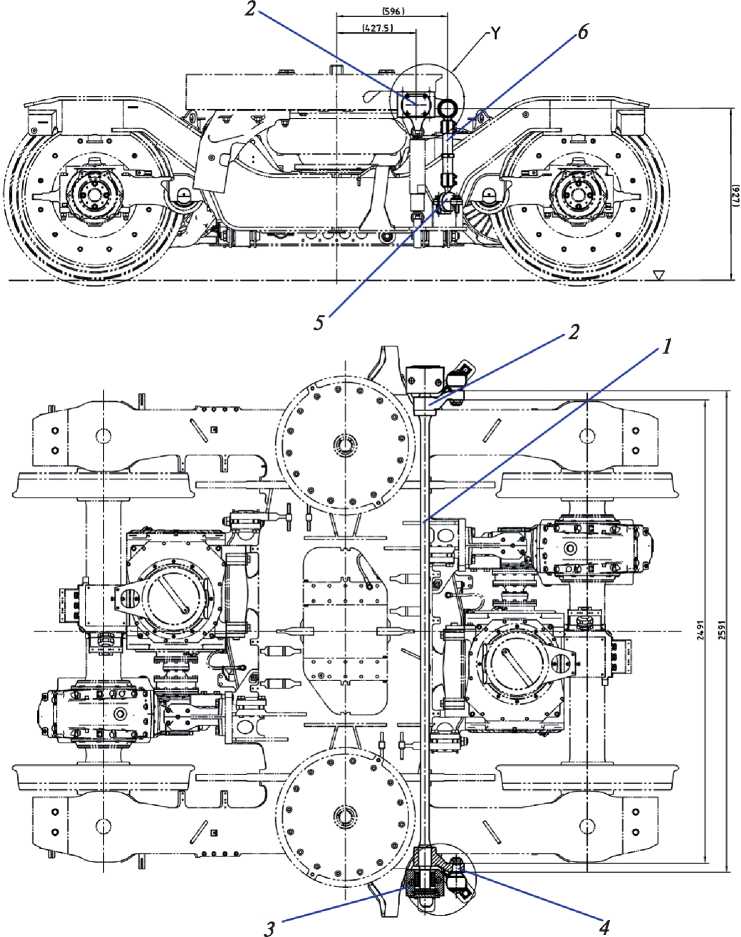
Рис. 3.37. Торсион: 1 — балка торсиона; 2 — поворотный рычаг балки торсиона; 3 — шарнир вращения балки торсиона в траверсе; 4 — пальцевое крепление регулируемой тяги в рычаге; 5 — шарнирное соединение регулируемой тяги к раме тележки; 6 — регулируемая тяга торсиона
Торсион 1 устанавливается на шарнире вращения балки торсиона в траверсе 3 (рис. 3.37). Шарниры вращения балки торсиона крепятся на траверсе посредством болтового соединения (позиции 6, 7 на рис. 3.38). Осевой зазор торсиона ограничивается и может настраиваться регулировочной шайбой 3 и соответствующими вкладышами для системы качения 4. Шарниры вращения балки торсиона плотно закрываются крышкой кронштейна опоры пружины качения 2 и уплотнительным кольцом 5. Соединение торсиона с рамой тележки осуществляется посредством устанавливаемой в длину регулируемой тяги торсиона. К обеим сторонам тележки на торсион в горячем состоянии насажены два рычага 1. Концы рычагов соединены с тягой торсиона подвижным шаровым пальцевым шарниром (позиция 4 на рис. 3.37). Другой конец регулируемой тяги торсиона укреплен на раме тележки посредством болтового соединения (позиции 6, 7 на рис. 3.38). Благодаря такому расположению движение поперечного качания корпуса вагона (крен вагона в сторону) на кривых участках пути передается по продольной оси в торсион тележки, жесткость на скручивание которого снижает наклон кузова.
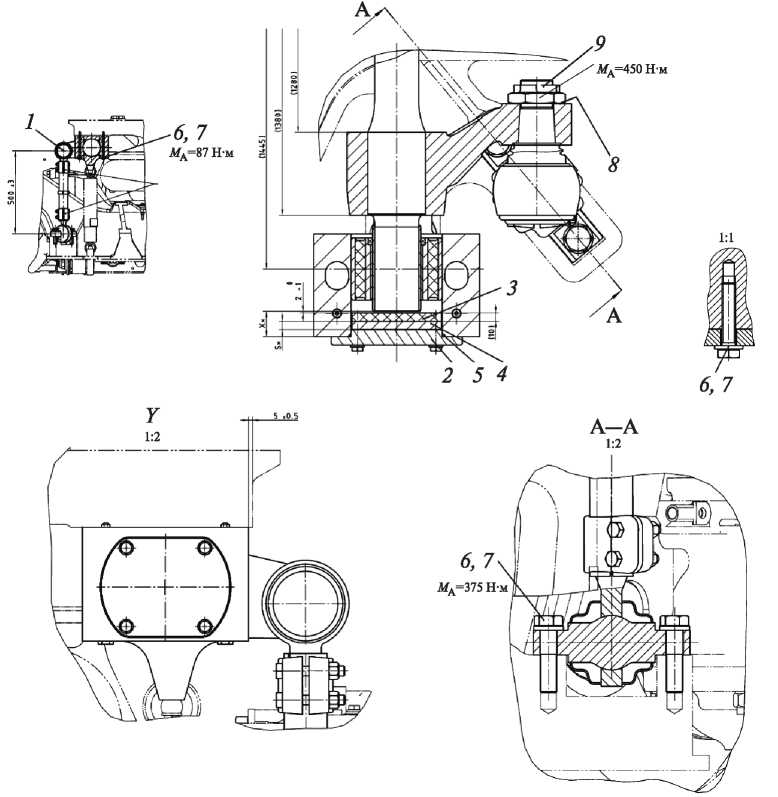
Рис. 3.38. Крепеж элементов торсиона: 1 — поворотный рычаг балки торсиона; 2 — крышка кронштейна опоры качения; 3 — регулировочная шайба; 4 — вкладыш для системы качения; 5 — уплотнительное кольцо круглого сечения; 6 — предохранительная шайба; 7 — винт с шестигранной головкой; 8 — шайба; 9 — корончатая гайка пальцевого шарнира крепления разъемной тяги к поворотному рычагу торсиона
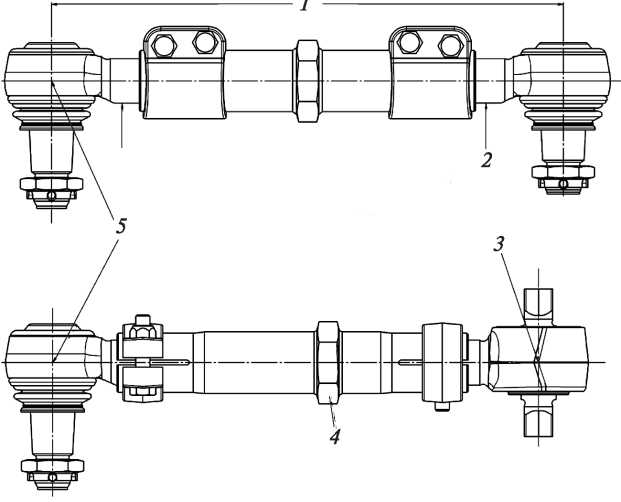
Рис. 3.39. Регулируемая тяга торсиона: 1 — регулируемая длина; 2 — левая резьба; 3 — шарнир с предварительно напряженным упругим элементом; 4 — приваренная шестигранная гайка; 5 — шариковый подшипник; 6 — правая резьба
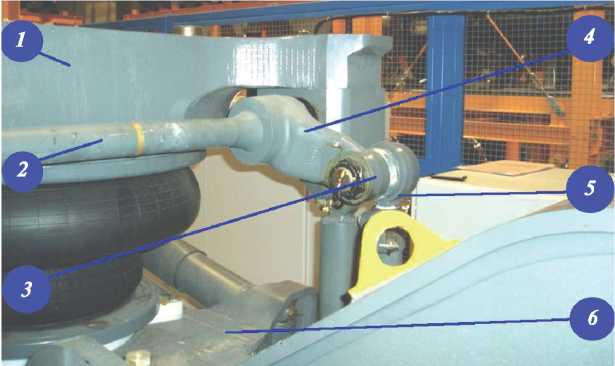
Рис. 3.40. Балка и поворотный рычаг торсиона: 1 — траверса; 2 — балка торсиона; 3 — пальцевый шарнир рычага торсиона; 4 — рычаг торсиона; 5 — регулируемая тяга торсиона; 6 — рама тележки
В тележке применен вариант, когда регулируемая тяга торсиона расположена снизу (рис. 3.39). Тяга торсиона выполнена регулируемой с целью точной настройки балки торсиона, соблюдения изначального нулевого угла наклона кузова на абсолютно ровном пути при равномерно распределенной нагрузке в кузове. Если на стоящей на пути тележке регулируемая тяга торсиона свободно немного проворачивается в своих шарнирах, то это означает, что торсион не напряжен, участок пути и нагрузка вагона — ровные, балка торсиона в данное время свободна.
На рис. 3.40 изображен узел шарнирного соединения балки и рычага торсиона.
Передача тягового усилия во 2-й ступени
Передача тягового усилия в рессорном подвешивании 2-й ступени (рис. 3.41) осуществляется двумя тяговыми поводками 1 от рамы тележки к центральному рычагу лемни-скатного механизма, в который вставлен шкворень траверсы, прикрученный болтовыми соединениями к траверсе, которая в свою очередь жестко прикручена к кузову вагона.
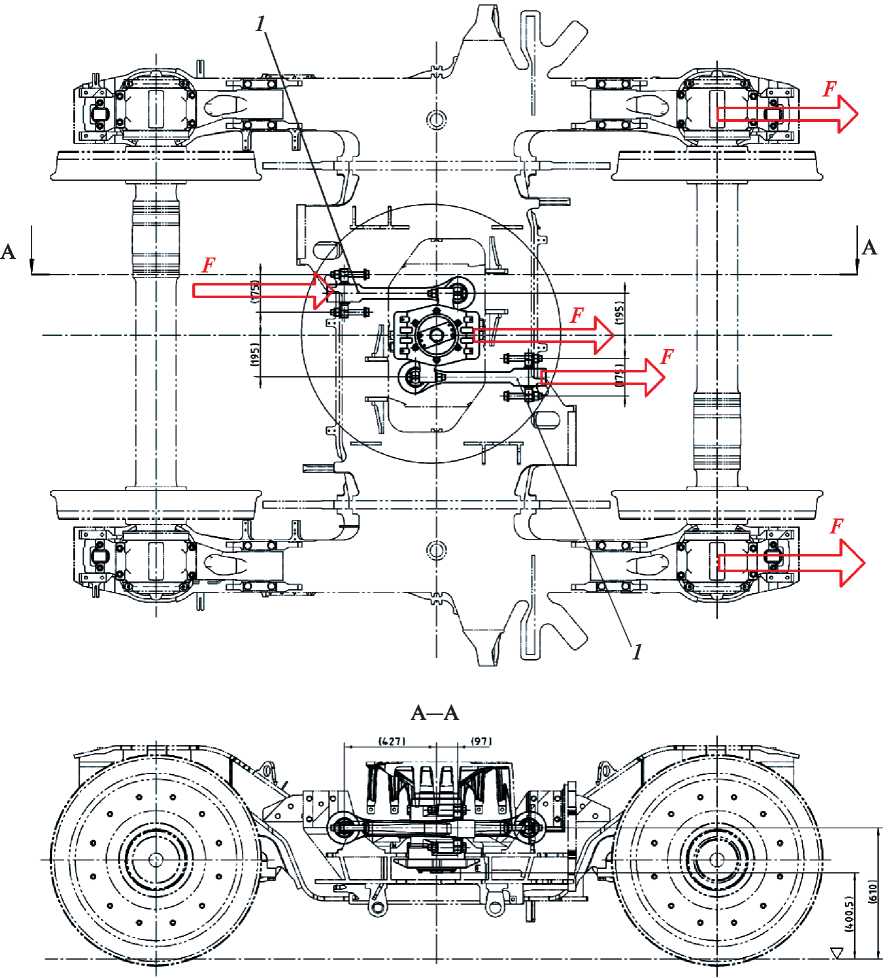
Рис. 3.41. Передача тягового усилия в рессорном подвешивании 2-й ступени: 1 – тяговый поводок (направляющая тяга); F – тяговое усилие
Устройство передачи продольного усилия передает рабочее усилие от рамы к шкворню тележки, установленному на поперечной балке, давая возможность осуществлять поворотные и продольные движения, а также подрессоривание кузова вагона относительно тележки. При подъеме кузова вагона тележка также приподнимается посредством вторичного ограничителя вертикального перемещения, который состоит из двух кронштейнов, приваренных к центральному соединителю рамы тележки, и двух опорных поверхностей на корпусе центрального рычага лемнискатного механизма.
Тяговые и тормозные усилия во 2-й ступени подвески, т.е. от рамы тележки на траверсу (кузов), передаются через два симметрично расположенных тяговых поводка (позиция 1 на рис. 3.41). Поводки крепятся и к раме тележки и к центральному рычагу лемнискатного механизма 1 (рис. 3.42) шарнирно-болтовыми соединениями (8, 10, 11).
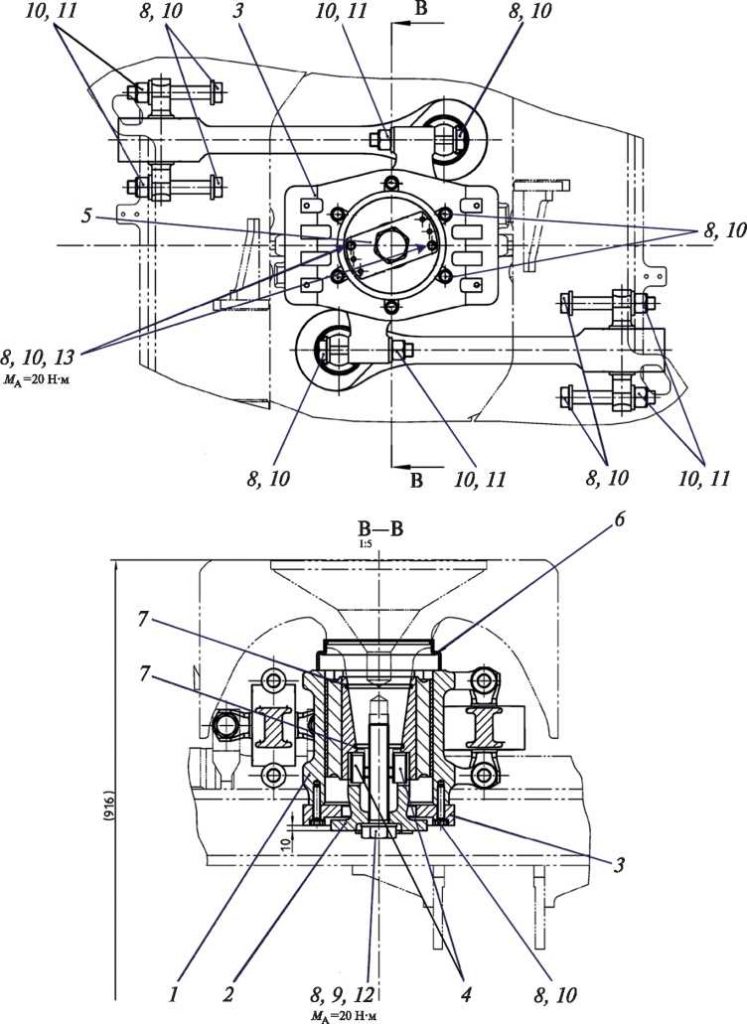
Рис. 3.42. Узел лемнискатного механизма: 1 — центральный рычаг лемнискатного механизма; 2 — втулка для устройства передачи продольного усилия; 3 — упорная плита устройства передачи продольного усилия; 4 — призматическая шпонка для устройства передачи продольного усилия; 5 — предохранитель устройства передачи продольного усилия; 6 — манжета; 7 — уплотнительное кольцо круглого сечения; 8—12 — винт с шестигранной головкой; 13 — шайба
Болтовое соединение крепления тягового поводка осуществляется болтами M24x160 (8) с моментом затяжки 436 Н/м. Поводки (позиция 1 на рис. 3.41) не позволяют центральному рычагу лемнискатного механизма смещаться в плоскости вдоль оси пути, тем самым фиксируя раму тележки строго под центром траверсы в продольном к оси пути направлении. Однако и в поперечном, и в вертикальном направлениях корпус лемнискатного механизма имеет возможность перемещаться. Именно из-за этого тяговые поводки выполнены с разворотом отверстий на 90° под резиновые втулки 2 (рис. 3.43). В противном случае поперечные смещения лемнискатного механизма оказывали бы негативные изламывающие усилия на шарнирно-болтовые крепления тяговых поводков к лемнискатному механизму. Кроме того, шарнирно-болтовые соединения тяговых поводков к центральному рычагу лемнискатного механизма выполнены с перехлестом, что необходимо для исключения реактивных усилий разворота центрального рычага лемнискатного механизма при поперечном смещении траверсы.
Центральный рычаг лемнискатного механизма 1 (рис. 3.44) включает подшипник шкворня тележки 2, который с помощью резьбового соединения (позиции 8, 9 на рис. 3.42) и втулки для устройства передачи продольного усилия (позиция 2 на рис. 3.42) запрессовывается на конус шкворня тележки. Болт шкворня — M36x190 с моментом затяжки 1100 Н-м.
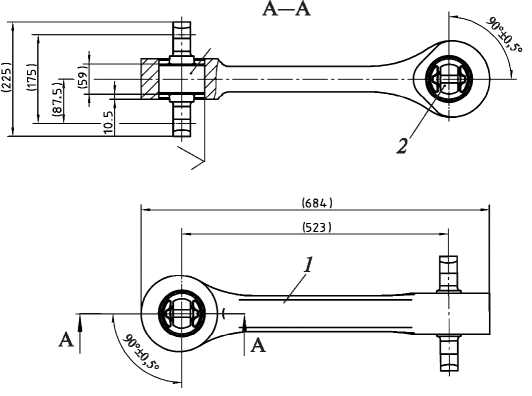
Рис. 3.43. Тяговый поводок (направляющая тяга) (1) и втулка (2)
Упорная плита 3 (см. рис. 3.42) служит в качестве вторичного ограничителя вертикального перемещения и закрепляется с помощью резьбового соединения (8, 10) на центральном рычаге лемнискатного механизма 1. Две призматических шпонки для устройства передачи продольного усилия 4 предотвращают проворачивание подшипника шкворня тележки на конусе шкворня тележки. Предохранитель устройства передачи продольного усилия 5 закрепляется с помощью резьбового соединения (8, 10) и стопорного элемента 13. Манжета 6 уплотняет шарнирную систему со стороны траверсы. Между втулкой 2 и упорной плитой 3 имеется зазор, который обеспечивает поворотное перемещение шкворня в центральном рычаге лемнискатного механизма, но при подъеме кузова этот зазор выбирается, поскольку винт 8 является устройством ограничителя вертикального перемещения во 2-й ступени рессорного подвешивания.
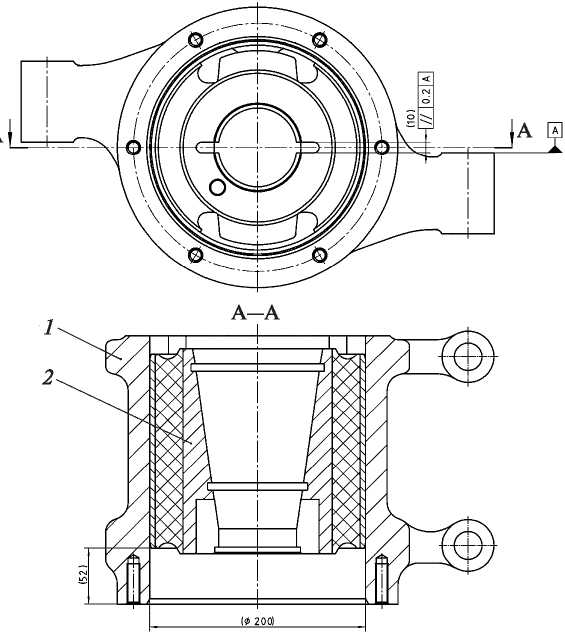
Рис. 3.44. Центральный рычаг лемнискатного механизма (корпус лемнискатного механизма) (1) и подшипник шкворня тележки (2)
Обе направляющих тяги 1 (см. рис. 3.43), монтируемых между центральным рычагом лемнискатного механизма и рамой тележки, образуют лемнискатное шарнирное соединение. В отверстия, расположенные на обоих концах соединения, впрессовываются буксы штанги или резинометаллические втулки 2 тягового поводка.
На рис. 3.45 изображен лемнискатный механизм, смонтированный на раме тележки.
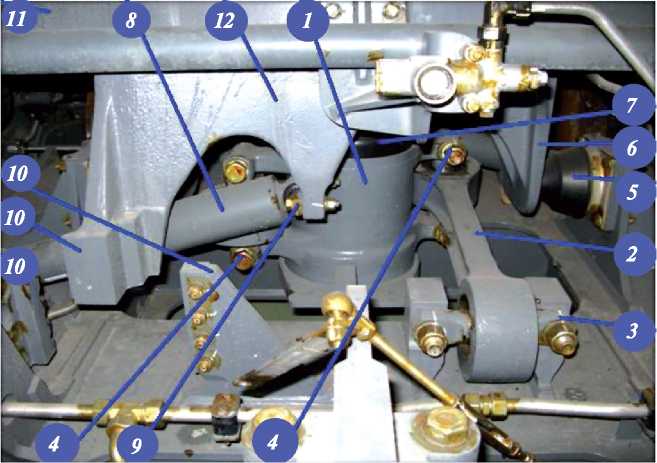
Рис. 3.45. Лемнискатный механизм тележки: 1 — центральный рычаг лемнискатного механизма; 2 — тяговый поводок; 3 — шарнирно-болтовое соединение тягового поводка к раме тележки; 4 — шарнирно-болтовое соединение тягового поводка к центральному рычагу лемнискатного механизма; 5 — упорный резиновый буфер; 6 — упорная планка шкворня; 7 — уплотнительная резиновая манжета шкворня; 8 — поперечный демпфер; 9 — шарнирно-болтовое соединение поперечного демпфера к траверсе; 10 — металлический упор ограничения предельного поперечного смещения траверсы относительно рамы тележки; 11 — траверса; 12 — шкворень
Демпфирование поперечных перемещений кузова во 2-й ступени
Как уже было сказано выше, пневморессоры могут свободно передавать, но не могут ограничивать поворотные и поперечные перемещения траверсы относительно рамы тележки. В отличие от ЭВС «Аллегро», где и в части регулирования поперечного положения кузова относительно рамы тележки также применена активная пневматическая система, управляемая компьютером, на ЭВС «Сапсан» использована пассивная система регулировки и ограничения поперечных перемещений траверсы (кузова).
Система ограничения поперечных перемещений траверсы (рис. 3.46—3.48) условно имеет три зоны: успокоение поперечных колебаний, ограничение поперечных колебаний, ограничение предельно допустимых поперечных колебаний.
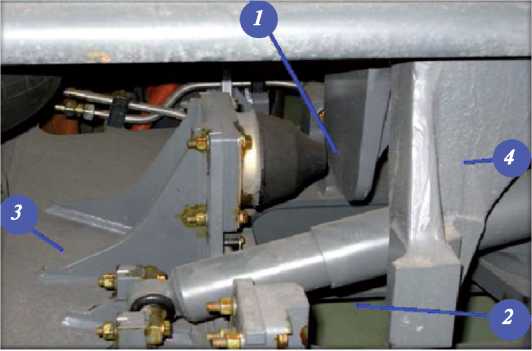
Рис. 3.46. Рабочее и предельное ограничение поперечных перемещений кузова: 1 — зона рабочего ограничения поперечных перемещений кузова; 2 — зона предельного ограничения поперечных перемещений кузова; 3 — рама тележки; 4 — шкворень траверсы
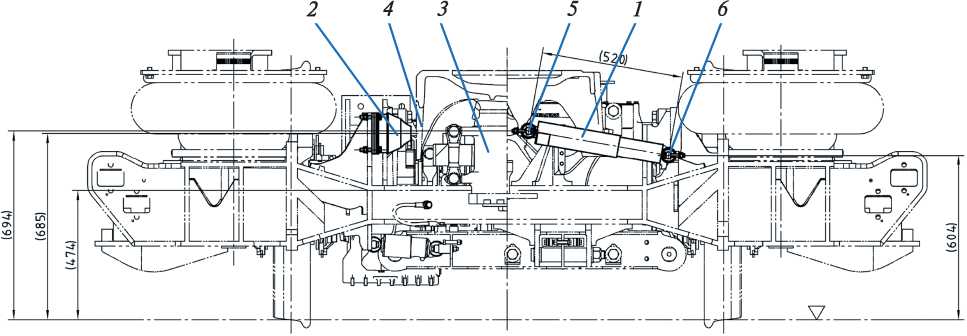
Рис. 3.47. Монтаж поперечного демпфера (вид спереди): 1 — поперечный демпфер; 2 — упорный резиновый буфер; 3 — центральный рычаг лемнискатного механизма; 4 — упорная планка шкворня траверсы; 5 — шарнирно-болтовое крепление поперечного демпфера к шкворню траверсы; 6 — шарнирно-болтовое крепление поперечного демпфера к раме тележки
При движении по прямому участку пути кузов вагона подрессоривается преимущественно благодаря горизонтальной жесткости системы пневматического подрессорива-ния в поперечном направлении поезда. При движении в кривой возникающие центробежные силы переносятся благодаря буферу, прилегающему к упорной поверхности шкворня тележки.
Два симметрично расположенных поперечных демпфера 1 (см. рис. 3.48) успокаивают поперечные перемещения траверсы относительно рамы тележки. Два симметрично расположенных упорных резиновых буфера 2, взаимодействуя с упорными планками 3 шкворня траверсы, выполняют ограничения поперечных перемещений. Зазор между каждой упорной планкой 3 и упорным буфером 2 равен 20 мм. Дальнейшее (более 20 мм в сторону) поперечное смещение траверсы с жестко привинченным к нему шкворнем будет активно гаситься упругим сжатием буфера 2. В случае особо сильного поперечного перемещения, с которым упорный резиновый буфер 2 может уже не справиться, произойдет выбирание зазора в металлическом упоре ограничения предельного поперечного смещения траверсы относительно рамы тележки. Это приведет к жесткому упору металлического элемента шкворня на раму тележки. Шарнирно-болтовые соединения тяговых поводков с рамой тележки 3 (см. рис. 3.45) будут терпеть при этом некоторую изламывающую деформацию, однако конструктивно эти элементы не предназначены для гашения поперечных перемещений траверсы.
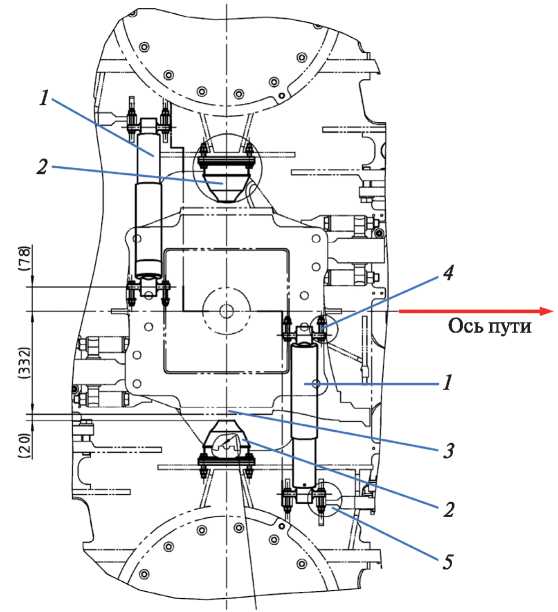
Рис. 3.48. Устройства ограничения поперечных перемещений кузова (вид сверху): 1 — поперечный демпфер; 2 — упорный резиновый буфер; 3 — упорная планка шкворня траверсы; 4 — шарнирно-болтовое крепление поперечного демпфера к шкворню траверсы; 5 — шарнирно-болтовое крепление поперечного демпфера к раме тележки
На рис. 3.49 и 3.50 изображены ограничители поперечных перемещений кузова (вид снизу) и упорный резиновый буфер соответственно.
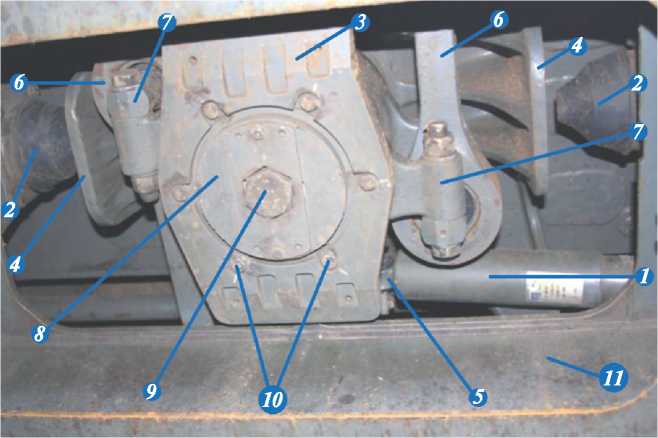
Рис. 3.49. Ограничители поперечных перемещений кузова (вид снизу): 1 — поперечный демпфер; 2 — упорный резиновый буфер; 3 — центральный рычаг лемнискатного механизма; 4 — упорная планка шкворня траверсы; 5 — шарнирно-болтовое крепление поперечного демпфера к раме тележки; 6 — тяговый поводок; 7 — шарнирно-болтовое соединение тягового поводка с центральным рычагом лемнискатного механизма; 8 — упорная плита устройства передачи продольного усилия лемнискатного механизма; 9 — нижний (основной) болт шкворня (момент затяжки 1100 Н-м); 10 — болты крепления втулки для устройства передачи продольного усилия к центральному рычагу лемниската; 11 — рама тележки
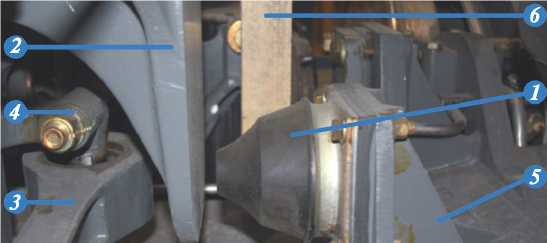
Рис. 3.50. Упорный резиновый буфер: 1 — упорный резиновый буфер; 2 — упорная планка шкворня траверсы; 3 — тяговый поводок; 4 — шарнирно-болтовое соединение тягового поводка с центральным рычагом лемнискатного механизма; 5 — рама тележки; 6 — технологическая распорка (доска), устанавливаемая для недопущения опрокидывания траверсы (случай, когда тележка с траверсой выкачена из-под вагона)
Ограничение поворотных перемещений тележки во 2-й ступени
Демпфер виляния тележки (рис. 3.51, 3.52) иногда называют поворотным демпфером.
Поворотный демпфер расположен между траверсой и рамой тележки и служит для демпфирования виляния тележки по отношению к кузову вагона в горизонтальной плоскости. Так как поворотные демпферы выполняет функции, относящиеся к безопасности, они выполнены с резервированием, т.е. на каждой стороне тележки они расположены в количестве двух штук. Как описывалось выше, рама тележки вращается вокруг шкворня траверсы. Центральный рычаг лемнискатного механизма имеет возможность поворачиваться вокруг шкворня. Момент сопротивления на вращение в указанном устройстве несопоставимо мал по сравнению с аналогичным моментом при классической опоре на боковые скользуны. Кроме того, сами пневморессоры также не имеют достаточного сопротивления в горизонтальной плоскости. Наиболее опасен режим резонансного вращательного раскачивания рамы тележки вокруг оси шкворня траверсы при движении по пути, имеющему неровности в плане (виляние пути). Описанное явление успешно успокаивается системой поворотных демпферов.
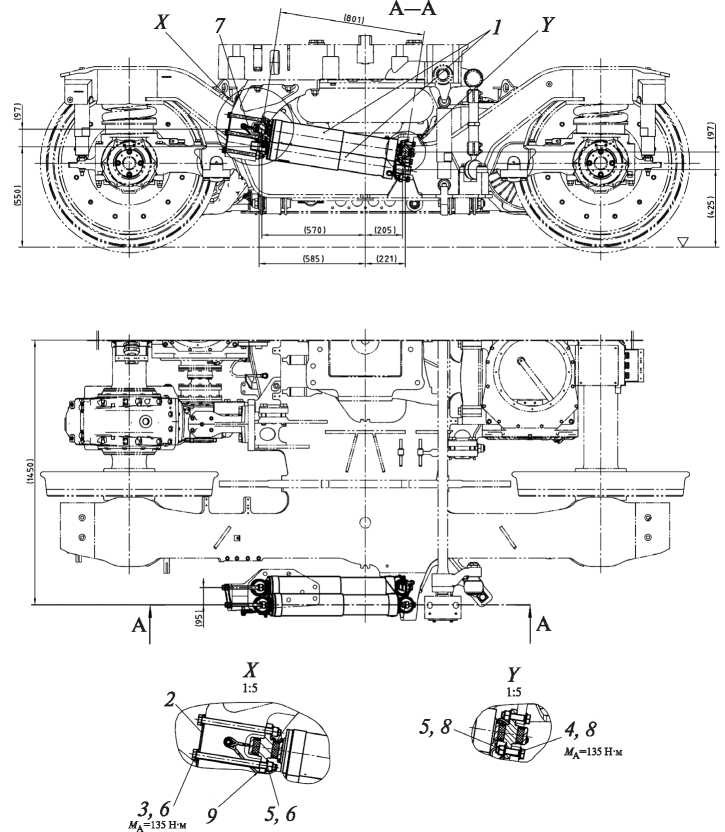
Рис. 3.51. Демпферы виляния тележки: 1 — поворотный демпфер; 2 — вкладыш для поворотного демпфера; 3, 4 — винт с шестигранной головкой (М16х70, момент затяжки 135 Н-м); 5 — шестигранная гайка; 6 — стопорная шайба; 7 — предохранитель поворотного демпфера от падения (страховочный тросик); 8 — шайба; 9 — крепежный стержень демпфера виляния
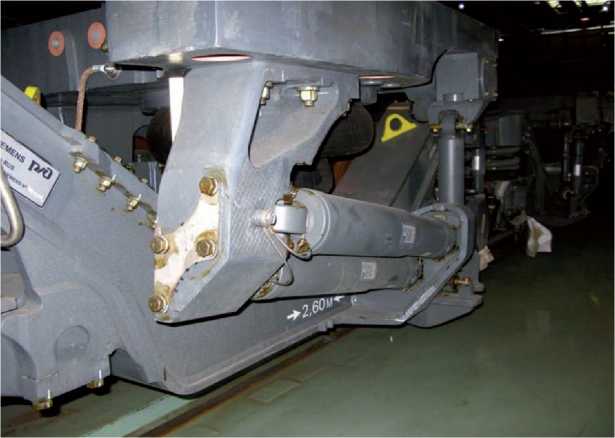
Рис. 3.52. Вид демпферов виляния (поворотных демпферов) тележки с одной стороны тележки
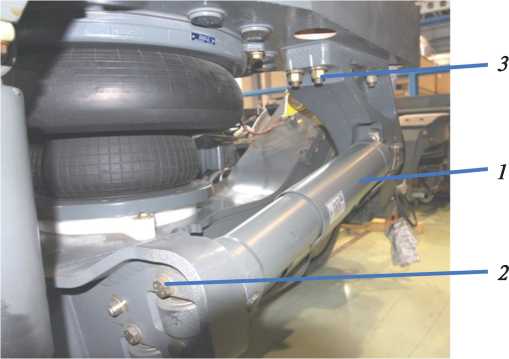
Рис. 3.53. Вид демпферов виляния тележки с другой стороны: 1 — поворотный демпфер; 2 — винт с шестигранной головкой (М16х70, момент затяжки 135 Н-м); 3 — болты крепления кронштейна поворотного демпфера к траверсе
Крепление поворотного демпфера к кронштейнам рамы тележки и траверсы винтами 2 (рис. 3.53) аналогично по конструкции шарнирно-болтовым креплениям других демпферов. На рис. 3.54 представлено размещение элементов рессорного подвешивания первой и второй ступеней.
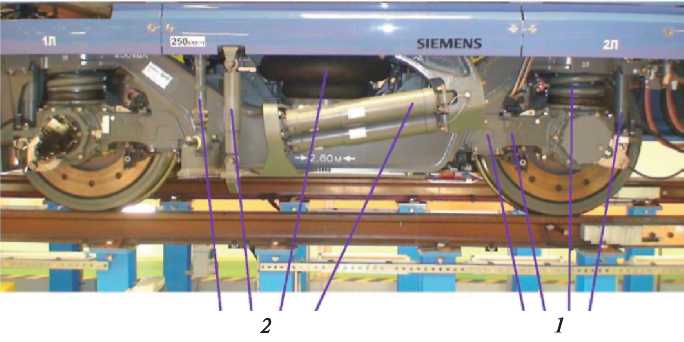
Рис. 3.54. Тележка с элементами рессорного подвешивания 1-й (1 ) и 2-й ступеней (2 ) (вид сбоку)