Механическое оборудование
Сцепные устройства
Автоматическая сцепка
Перед проведением работ автоматическую сцепку перевести в ремонтное состояние, перекрыть разобщительный кран, при необходимости произвести очистку сцепки. Очистку незначительных загрязнений произвести кистью с последующей протиркой влажной ветошью. Сильные загрязнения удалить нанесением очистителя WEICON S, с предварительным закрытием электрических узлов для предотвращения попадания капель очистителя. Не допускается использовать очистители на базе концентрированных щелочей, фосфорной и соляной кислот, а также с содержанием бензола.
Произвести очистку электрической сцепки (после эксплуатации электропоезда в режиме сдвоенного состава).
Очистить сухой безворсовой ветошью или кистью для очистки:
- корпус;
- заслонку (внутри и снаружи);
- контактодержатель и контакты.
Профильное уплотнение очистить ветошью увлажненной водой и протереть насухо.
Произвести визуальную проверку. Не допускаются механические повреждения сцепки и тарельчатой муфты, которая соединяет головку сцепки с соединительной штангой.
Произвести проверку легкости хода замка сцепки. Порядок проверки:
- тягу защелки оттянуть назад и удерживать;
- несколько раз повернуть замок сцепки возвратно-поступательным движением за ручку расцепляющего троса.
Замок сцепки должен отводиться назад до упора, без застреваний. Для устранения застревания замка сцепки нанести разбрызгиваемую пластичную смазку ISOFLEX TOPAS NCA 52 и снова проверить легкость хода. Если застревание замка не устраняется нанесением смазки, то замок демонтировать и проверить на износ.
Произвести смазку главного пальца запрессовкой пластичной смазки ISOFLEX TOPAS NCA 52, с предварительным снятием защитного колпачка смазочного ниппеля.
Провести проверку состояния и крепления муфтового соединения. При недостаточном количестве смазки в полостях произвести пополнение смазкой ISOFLEX TOPAS NCA 52. Ослабшее резьбовое соединение заменить новым.
Беззазорное сцепное устройство БСУ-ТМ122
Перед проведением работ, при необходимости, произвести очистку сцепки. Очистку незначительных загрязнений производить кистью с последующей протиркой влажной ветошью. Сильные загрязнения удалить уайт-спиритом или очистителем WEICON S. Не допускается использовать очистители на базе концентрированных щелочей, фосфорной и соляной кислот, а также с содержанием бензола.
Произвести визуальную проверку на отсутствие видимых повреждений (трещин, деформации и т.д.) на узлах и деталях сцепки, болтовых соединений крепления наконечников шунтирующих кабелей, целостности пружин опор и целостности пластиковых планок опор. По контрольным меткам проверить состояние крепежа сцепки к раме вагона, узлов и деталей на самой сцепке. Неисправные детали заменить.
Произвести проверку крэш-элемента ТМ121.03.00.000- 02.
Произвести проверку контрольного размера крэш-элемента (367+1 ) мм -4 и сравнение его с изначальным значением, записанным на боковой поверхности трубы крэш-элемента (рисунок 7.1.1).
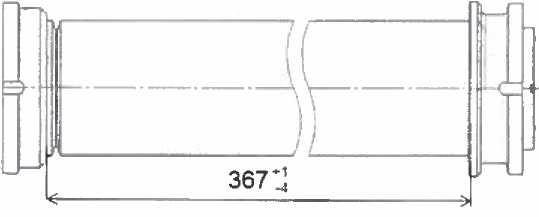
Рисунок 7.1.1 – Чертеж крэш-элемента ТМ121.03.00.000-02
При отклонении контрольного размера (367+1(-4)) мм в любую сторону более, чем на 1 мм (менее 362 мм или более 369 мм) произвести раскатку вагонов и частичную разборку сцепки и проверить крэш-элемент на отсутствие следующих дефектов:
- а) отсутствие деформации и трещин в сварном шве между гайкой и трубой крэш-элемента;
- б) отсутствие сдвига фильеры крэш-элемента;
- в) отсутствие кручения фильеры.
Порядок выполнения работ указан в приложении М.
При выявлении данных дефектов крэш-элемент подлежит замене.
Каждый раз при инцидентах, связанных с соударением поезда с препятствиями или с проведением маневровых работ, вызвавших соударение сцепок, производить проверку срабатывания крэш-модуля между 1 и 2 вагонами (или между 5 и 4 вагонами) по описанной выше методике. В случае изменения величины длины крэш-модуля произвести его замену на новый согласно приложению М.
Вспомогательная сцепка (адаптер)
Порядок обслуживания вспомогательной сцепки:
- перед проведением работ произвести сухую очистку от загрязнений с последующей протиркой влажной тряпкой. Сильные загрязнения удалить очистителем WEICON S;
- проверить сцепку на наличие целостности деталей и отсутствие механических повреждений (изгибов, изломов, трещин) сцепки и тарельчатой муфты, соединяющей головку сцепки с соединительной штангой. Повреждения не допускаются. Неисправные детали заменить новыми;
- проверить торсионные пружины на наличие изломов и других механических повреждений. Изломы и механические повреждения не допускаются;
- проверить запирающие механизмы на легкость хода. Заедания не допускаются;
- восстановить (при необходимости) лакокрасочное и антикоррозионное покрытие торцевых поверхностей, воронки и конуса; – нанести специальную пластичную смазку ISOFLEX TOPAS NCA 52;
- проверить шланги подключения сжатого воздуха тормозной и питательной магистралей на наличие пористости и не герметичности.
Неисправные шланги или со сроком службы более 6 лет заменить.
В процессе эксплуатации вспомогательной сцепки провести:
- демонтаж сцепки с подвижного состава;
- внешний осмотр на отсутствие механических повреждений, трещин;
- проверку длины сцепной головки шаблоном № 873р (рисунок 7.1.2). Между шаблоном 2 и сцепной головки 1 обязательно должен быть зазор 3. В исправной сцепной головке шаблон не войдет в пространство между указанными поверхностями. Операцию выполняют в зоне не выше и не ниже 80 мм от продольной оси сцепной головки.
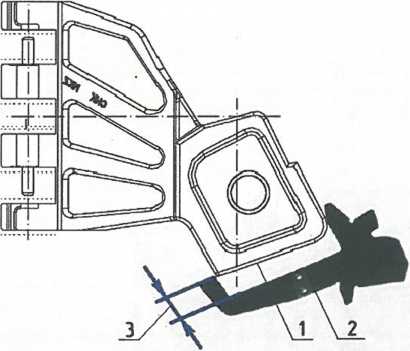
Рисунок 7.1.2 – Проверка шаблоном длины сцепной головки вспомогательной сцепки: 1 – сцепная головка; 2 – шаблон для проверки параметров автосцепного устройства №873р; 3 – зазор
Путеочиститель
Проверить состояние путеочистителя и его крепление. Трещины в путеочистителе и ослабление крепления не допускается. Выполнить замер высоты нижней кромки путеочистителя над головками рельсов – высота должна быть в пределах от 200 до 210 мм.
Проверить крепление и замерить высоту приемных катушек КП-РС над уровнем головок рельсов – высота низшей точки корпуса приемной катушки должна находится в пределах от 205 до 240 мм. При этом:
- уровень нижней плоскости приемных катушек должен быть выше нижней кромки путеочистителя – на 5 мм;
- середина катушки должна располагаться над осью рельса на прямом участке пути;
- разница высот катушек слева и справа должна быть не более 5 мм».
Тележка
Произвести визуальную проверку состояния рамы тележки. Наличие деформации, трещин не допускается.
Проверить наличие и состояние предохранительных устройств.
Провести осмотр состояния цилиндрических пружин. Не допускаются деформации, наличие трещин, соединение витков.
Произвести осмотр состояния многослойных пружин. Не допускается наличие трещин, отслаивание и вспучивание резины.
Устройства передачи продольного усилия
Произвести визуальный контроль крепления устройства передачи продольного усилия, шкворня и ограничителя вертикального перемещения на наличие ослабленных креплений или отсутствующих деталей и повреждений (деформации, поломки, трещины и т.д.). По мере необходимости провести частичную очистку.
Произвести визуальный контроль упоров передачи продольного усилия на наличие вздутий, разломов, трещин в резине, отслаивания резины от металла. Проверить резьбовые соединения на прочность посадки. Неисправные или поврежденные детали заменить.
Провести визуальный контроль установки поперечного буфера и установки поперечного демпфера на предмет непрочно закрепленных или отсутствующих деталей, а также на предмет повреждений (деформаций, разломов, трещин). Наличие подтеков масла демпфера не допускается. По мере необходимости провести частичную очистку.
Провести визуальный контроль опоры пружины качения на предмет обнаружения ослабленных креплений или отсутствующих деталей, а также на наличие повреждений (деформации, поломки, трещины).
При необходимости более тщательного осмотра демонтировать компоненты для обеспечения доступа к проверяемому узлу, детали.
Провести проверку на прочность крепления к кузову. Дефектные детали заменить.
Провести визуальный контроль пружины качения (торсиона, тяг торсиона, кронштейнов) на наличие повреждений (деформации, поломок, трещин, ослабления посадок). По мере необходимости провести частичную очистку.
Произвести визуальный контроль системы рессорного подвешивания 2-й ступени. Не допускаются:
- ослабшие болтовые соединения;
- механические повреждения;
- повреждения рессор, наличие трещин, следов трения, образование пузырей, явления старения и т.д.;
- повреждения дополнительных рессор, наличие трещин, выкрашиваний, отслаиваний и т.д.;
- наличие подтеков масла у демпферов.
При необходимости произвести частичную очистку.
Провести визуальный осмотр центральной втулки. Не допускаются трещины, деформация. При повреждении соединения резиновой и металлической частей втулку заменить.
Колесная пара
Осмотреть устройства защиты оси от вылета щебня на комплектность, отсутствие повреждений и надежность крепления. Деформации с открытием оси, наличие коррозии, ослабление креплений не допускаются.
Провести контроль поверхностей катания и ободьев цельнокатаных колес на отсутствие повреждений (коррозия, трещины, изломы, места выкрашивания, выбоины).
Предельные эксплуатационные параметры колесных пар указаны в приложении Е «Руководства по эксплуатации 32303.0.00.000.000 РЭ9».
Осмотреть корпуса букс колесных пар на отсутствие повреждений (коррозии, деформации, изломов, изменения цвета на основании перегрева подшипников, выдавливания смазки).
Провести визуальный контроль направляющей системы подвески колесной пары на отсутствие видимых признаков трещин, вздутий, утери резинометаллического соединения и т.д.
Произвести контроль состояния тормозных фрикционных дисков. Порядок контроля и предельные эксплуатационные параметры указаны в приложении Е «Руководства по эксплуатации 32303.0.00.000.000 РЭ9».
Неисправные или поврежденные детали заменить.
При обнаружении смещения контрольной риски проверить проворачивание крепежного комплекта с помощью динамометрического ключа с выставленным моментом 5,0 Н-м, момент прикладывается к гайке без удержания болта. Контролю подвергнуть все крепежные комплекты данного диска. При выявлении проворачивания:
- демонтировать провернувшийся крепежный комплект;
- установить новый крепежный комплект со старой гайкой и добавить одну тарельчатую пружину со стороны головки болта;
- затянуть крепежный комплект моментом затяжки (50 – 75) Н-м, проверить на проворачивание крепежного комплекта моментом 5,0 Н-м, если проворачивание не устранилось, добавить еще одну тарельчатую пружину со стороны гайки;
- при устранении проворачивания, заменить старую гайку на новую, затянуть крепежный комплект моментом затяжки (50 – 75) Н-м, проверить на проворачивание моментом 5,0 Н-м.
Устранить проворачивания крепежного комплекта при наличии выработки на венце и ступице.
При появлении выработки на венце и ступице в месте контакта с деталью Кольцо (черт. 744.000.003), заменить Втулку (черт. 744.000.002) размером 80Ы2 на размер 76b12, добавить второе Кольцо в крепежный комплект и проверить его проворачивание по п. 7.1.4.5.1.
Осевой редуктор ASZF 410:
Произвести осмотр картера редуктора на наличие трещин, вмятин. Трещины и вмятины не допускаются. Визуально проверить надежность крепления болтов картера редуктора.
Произвести проверку уровня масла по масломерному стеклу. Электропоезд должен находиться на горизонтальном пути. Проверку произвести не менее, чем через 30 минут отстоя, для того чтобы масло стекло в маслосборник. Уровень масла должен находиться между верхней и нижней кромкой паза (красный цвет), вместо паза может быть нанесен красный круг в центре масломерного стекла, размеры которого соответствуют ширине паза. При нахождении уровня масла на нижней кромке паза (круга) и ниже произвести добавление масла (рисунок 7.1.3).
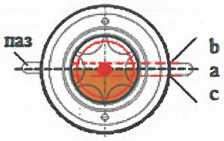
Рисунок 7.1.3 – Контроль уровня масла в редукторе: a – нормальный уровень; b – максимальный уровень; с – минимальный уровень
Очистить окружающие поверхности резьбовой пробки маслозаливного отверстия. Вывинтить резьбовую пробку с уплотнительным кольцом. Залить свежее масло с применением заправочного фильтра (тонкость фильтрации 25 мкм). Уровень масла должен находиться между верхней и нижней кромкой паза (круга) масломерного стекла. Завинтить резьбовую пробку с новым уплотнительным кольцом и затянуть с моментом затяжки 100 Н-м.
Муфта зубчатая ZBG 238
Произвести визуальный контроль крепления болтов и гаек.
Соединительные болты и соединительные гайки проверить на надежность фиксации по цветной маркировке (рисунок 7.1.4) и отсутствии коррозии. Ослабшие (линии маркировки смещены относительно друг друга) или сильно поврежденные коррозией болты, гайки заменить.
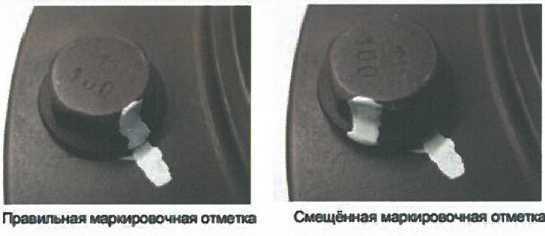
Рисунок 7.1.4- Контроль маркировки головки болта
Произвести визуальную проверку муфтовых частей на наличие трещин, следов коррозии, повреждений поверхностей прилегания муфтовых частей к уплотнительным кольцам. Устранить легкие следы коррозии и повреждения внешнего слоя покрытия муфтовых частей. Произвести замену поврежденных или сильно подверженных коррозии частей муфты.
При необходимости произвести очистку и удаление обледенения (в зимний период) распыленной струей жидкости чистящего средства. При этом давление не должно превышать 1,5 бар, расстояние между форсункой и муфтой должно составлять не менее 0,4 м, температура жидкости не должна превышать плюс 80°C. Для устранения обледенения использовать пропиленгликоль или смесь воды с пропиленгликолем. Не допускается использовать для очистки предметы с острыми кромками, проволочные щетки, наждачную бумагу и т.п. Во избежание повреждений муфты, в особенности резиновых элементов, не допускается использование агрессивных чистящих и противообледенительных средств (бензин, бензол, толуол, масла), нитроразбавителей, растворителей на основе углеводорода, трихлорэтилена, тетрахлорметана.
Произвести проверку на герметичность. Не допускается выдавливание смазки через уплотнительные кольца и уплотнительные поверхности между крышками и поводковыми кольцами, ступичной частью и поводковым кольцом. При сильном выступании смазки муфту демонтировать для устранения неисправностей.
Клещевые механизмы (Knorr-Bremse)
Провести визуальный осмотр тормозных клещевых механизмов. Проверить отсутствие повреждений, ослаблений, недостающих или незадействованных крепежных элементов.
Произвести визуальный контроль толщины тормозной накладки. При необходимости выполняется замер с помощью штангенциркуля. Толщина тормозной накладки должна быть более 5 мм с учетом достаточного ресурса по износу до следующего технического обслуживания. При недопустимом износе, наличии трещин тормозные накладки заменить.
Произвести осмотр держателей тормозных накладок на отсутствие ослабленных или недостающих крепежных элементов.
При помощи калибра проверить зазор между колодками и диском. На моторных вагонах суммарный зазор должен быть в пределах от 2,4 до 5,6 мм, на промежуточных – в пределах от 2,2 до 4,2 мм.
Произвести проверку состояния тормозных шлангов, при наличии повреждений (удары, потертые места, сгибы, трещины) шланги заменить.
Кабельные соединения на тележках
Произвести визуальный контроль кабельных соединений на наличие отсоединившихся или отсутствующих деталей. Наличие повреждений (деформаций, потертостей, перегибов, изломов, трещин) не допускается. По состоянию цветовой маркировки провести контроль болтовых соединений на прочность посадки. Не допускается ослабление креплений.
Гидравлические демпферы
Гидравлические демпферы, элементы крепления и кронштейны тележек осмотреть для выявления внешних признаков неисправностей. Утечки рабочей жидкости не допускаются, при обнаружении следов утечки с каплеобразованием демпфер заменить исправным и направить в ремонт. Проверить наличие и состояние предохранительных тросовых петель. Неисправные тросовые петли должны быть заменены.
Ослабленные болтовые крепления цапф к кронштейнам тележки подтянуть динамометрическим ключом с установкой новых стопорных (пружинных или фигурных) шайб. Проверить состояние резиновых втулок проушин. При внешних признаках повреждения резиновых втулок (трещин, расслоения, наличии зазоров между втулкой, проушиной или цапфой, смещения резиновой втулки более 2 мм относительно проушины головки) демпфер снять с вагона и направить в ремонт.
Осмотреть сварочные швы крепления металлического защитного кожуха к головке демпфера. При повреждении сварочного шва демпфер направить в ремонтное отделение для исправления выявленного дефекта и стендового контроля работоспособности.
Кузов
Произвести визуальную проверку отсутствия механических повреждений, повреждений лакокрасочного покрытия кузова.
Произвести визуальный контроль состояния внутрикузовного оборудования.
Произвести проверку работоспособности освещения вагонов.
Произвести визуальную проверку состояния окон.
Произвести контроль внешнего вида и работоспособности мусорного контейнера, состояния багажных полок, шкафов для приспособлений и инвентаря, перегородок, поручней. Неисправности не допускаются.
Произвести контроль состояния пассажирских кресел на предмет возможности их дальнейшего использования или их замены (например, при сильном загрязнении, повреждении).
Уход за кожаными креслами:
- еженедельно произвести протирку кресел от пыли мягкой тканью;
- ежемесячно, пылесосом, используя разные насадки, чтобы добраться в труднодоступные места, удалить пыль, крошки или другие остатки пищи;
- один раз в (2 – 3) месяца с применением кондиционера для кожи произвести протирку кожи кресел – операция сохранит мягкость кожи, и не даст образоваться трещинам. Применять pH нейтральный кондиционер на водной основе, который не содержит продуктов нефтяной дистилляции, силикона или воска;
- пятна кофе, чая, грязь удалить обычным мыльным раствором. Мягкими круговыми движениями (не втирающими) пятно очистить с кожаной обивки тампоном, смоченным в растворе мыла. Затем влажное пятно подсушить сухой тканью;
- масляные пятна и пятна от бытового жира удалить бензином;
- пятна от моторного и машинного масла – перхлорэтиленом;
- пятна от чернил и шариковых ручек – смесью спирта с магнезией или с уксусной кислотой;
- жевательную резинку на обивке кожаной удалить при помощи льда, в пластиковом пакете, который прикладывается к налипшей жевательной резинке. После того, как жвачка застыла, она соскребается любым тупым предметом;
- след от шариковой ручки удалить при помощи обычного скотча. Липкая лента наклеивается на штрих от ручки, затем плотно прижимается, после чего аккуратно снимается;
- след от фломастера удалить при помощи ваты, смоченной в спирте, либо специальными средствами для чистки кожи.
Обслуживание пассажирских кресел
Очистка обивки
Химическую чистку и дезинфекционную обработку пассажирских кресел следует выполнять методами и средствами, разрешенными к применению органами и учреждениями госсанэпидслужбы в установленном порядке.
Рекомендуются следующие группы дезинфицирующих средств с моющим эффектом, испытания которыми проводились на обивочных материалах:
- средство «Дезэффект – Свежесть» по ТУ 9392-007-18465550-2008;
- средство «Экор» по ТУ 9392-027-38965786-2006;
- средство «Сурфаниос плюс», Франция;
- средство «Тримицин-лайт» по ТУ 9392-003-74451497-2008;
- средство «Трилокс» по ТУ 9392-003-52582566-2005.
Уход за окрашенными частями и пластиком
Окрашенные порошковой краской поверхности можно очищать с использованием средств, указанных выше, а также использовать моющие средства со значением pH от 5 до 9 и растворитель уайт-спирит. Не допускается использовать чистящие средства с абразивом, с выраженными кислотными и щелочными свойствами, растворители 646, Р4, Р12 и их аналоги. При использовании чистящих средств соблюдать рекомендации производителя.
Описание работ по демонтажу частей кресел для ремонта или замены приведено в приложении Е настоящего Руководства.
Обслуживание оборудования кухни
Обслуживание оборудования Модуля 1
У охлаждаемого места для тележки и агрегата произвести:
- очистку конденсатора и холодильного агрегата;
- очистку испарителя и бачков испарителя;
- контроль участка слива талой воды в холодильнике на герметичность.
Обслуживание оборудования Модуля 2
Произвести контроль заполнения, при необходимости пополнение дозаторов для жидкого мыла и для ручных полотенец.
Обслуживание оборудования Модуля 3
7.2.7.3.1 При обслуживании микроволновой печи произвести:
- очистку фильтра воздухозаборника;
- контроль защиты от брызг;
- контроль керамической пластины.
При обслуживании холодильника произвести:
- очистку испарителя и бачков испарителя;
- контроль участка слива талой воды в холодильнике на герметичность.
Обслуживание Модуля глубокой заморозки
При обслуживании Модуля глубокой заморозки произвести:
- очистку конденсатора и холодильного агрегата;
- очистку испарителя и бачков испарителя;
- контроль участка слива талой воды в холодильнике на герметичность.
Обслуживание кухонного шкафа для запасов
При обслуживании кухонного шкафа для запасов произвести:
- очистку конденсатора на холодильном агрегате;
- очистку испарителя и бачков испарителя;
- контроль участка слива талой воды в холодильнике на герметичность.
Кабина управления
Провести визуальный осмотр деталей обшивки кабины, шкафов, кресел.
Порядок выполнения работ по техническому обслуживанию деталей обшивки интерьера и экстерьера кабины указан в приложении К настоящего Руководства.
При необходимости произвести очистку стен и потолка от грязи и пыли, с возможным применением моющих средств. Запрещается очистка с применением органических растворителей.
Произвести визуальный контроль и проверку исправности лобового стекла.
Проверить исправность стеклоочистителя/стеклоомывателя, заменить щетки стеклоочистителя (при необходимости), заправить емкость стеклоочистителя (летом – жидкостью для обмыва стекол или водой, зимой -незамерзающей жидкостью).
Провести проверку работы прожектора, буферных фонарей.
При выходе из строя более 3 светодиодов на обеих платах «дальнего света» прожектор подлежит замене.
При необходимости произвести регулировку прожектора (рисунок 7.3.1). Регулировку выполнить с помощью экрана.
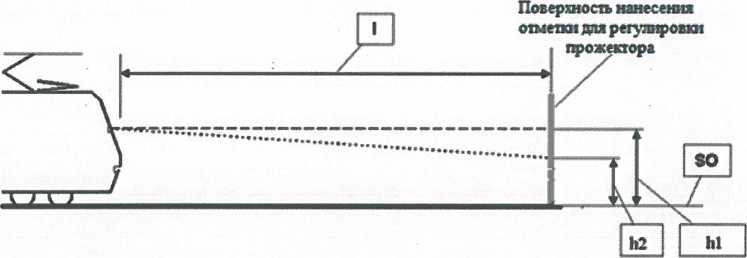
Рисунок 7.3.1 – Схема регулировки прожектора: I – измеренное расстояние; SO – уровень головки рельса; h1 – высота прожектора над уровнем головки рельса; h2 – высота второй отметки над уровнем головки рельса
Таблица 7.3.1 – Места нанесения отметок
Измеренное расстояние | 1 м | 1,5 м | 2 м | 3 м | 4 м | 5 м |
Наклон h1 – h2 | 3,5 см | 5,3 см | 7,0 см | 10,5 см | 14,0 см | 17,5 см |
В зависимости от измеренного расстояния на экран нанести следующие отметки (таблица 7.3.1):
- высота прожектора относительно оси рельсового пути и уровня головки рельса (h1);
- под этой отметкой нанести другую отметку для настройки на самую яркую точку светового пятна фары (h2);
- для облегчения регулировки рекомендуется нанести вокруг этой точки несколько концентрических кругов на расстоянии (100 – 200) мм.
Место регулировки затемнить. Затем прожектор установить на максимальный уровень освещения («дальний свет»). Установить самую яркую точку на нижние отметки (при h2) (вертикальная настройка). Направить центр прямо на соответствующую нижнюю отметку (горизонтальная настройка).
Горизонтальная и вертикальная настройки осуществляются до тех пор, пока обе настройки не будут выполнены правильно. Регулировку выполнить с помощью четырех гаек М8 на обратной стороне прожектора.
Пульт машиниста
Провести визуальный контроль, проверку и очистку пульта машиниста, проверить рабочее положение кранов под пультом управления.
Провести визуальный контроль контроллера «тяга/тормоз», клапана экстренного торможения на отсутствие повреждений.
Произвести визуальный контроль и проверку исправности дисплеев терминала управления и диагностики (УиД).
Проверить сроки поверок манометров на пульте управления и вольтметра аккумуляторной батареи на панели шкафа +115 (+215).
Приборы заменить, если срок поверки истекает или истечет до захода электропоезда на очередное плановое обслуживание или ревизию. Межповерочные интервалы указаны в приложении Г настоящего Руководства.
Боковые окна
Произвести визуальный осмотр состояния стеклопакета, при необходимости заменить.
Произвести очистку наружных и внутренних поверхностей стеклопакета моющими средствами с нейтральным PH (Surf -АСЕ -CRISTAL).
Произвести визуальный осмотр состояния резиновых уплотнителей, при необходимости заменить.
Контактирующие поверхности уплотнителей створки и окна смазать силиконовой смазкой «Si-М» ТУ 2257-001-54736950-2001 или ПМС – 300 ГОСТ 13032-77.
Проверить работоспособность, при необходимости заменить, створки, оконные ручки, петли, шторки.
Наружные тамбурные двери
Провести визуальный осмотр состояния створки и рамки двери.
Проверить работоспособность замка, защелки и петель, фиксатора открытого положения двери. При необходимости произвести регулировку.
Проверить состояние резиновых уплотняющих контуров.
В зимний период (с 15 октября по 15 апреля) нанести тонким слоем нейтральную силиконовую смазку «Si-М» или ПМС-300 на поверхность соприкосновения резиновых уплотняющих профилей с рамкой, на замки дверей.
Выдвижная подножка
Подножки выдвижные электропоезда ДБПС 004.01.12.000
Открыть нижние кожуха, провести визуальный осмотр механизма привода, при необходимости выполнить очистку деталей механизма привода.
Произвести проверку работоспособности подножки путем проведения двух циклов открытия / закрытия кнопками локального открытия и кнопками пульта машиниста. Подножка должна выдвигаться и задвигаться плавно, без рывков, перекосов и заеданий. Проверить плавность торможения и время открывания и закрывания подножки, которое должно быть (4 – 6) с после выдержки в открытом состоянии от 10 до 15 с. При необходимости произвести регулировку. Проверить срабатывание системы распознавания помех – при помехе открыванию подножка должна вернуться в положение «Закрыто», после чего должна повторно пытаться перейти в рабочее положение (функция противозащемления), при помехе закрыванию подножка должна сработать в обратном порядке.
Произвести визуальный осмотр надежности крепления мотор-редуктора, кардана по контрольным меткам. Осмотреть визуально надежность крепления звездочек, валов, состояние цепей. Произвести визуальный осмотр состояния линейных подшипников, при необходимости выполнить замену подшипника.
Подножка выдвижная автоматическая электропоезда ФКГП 605.20.00.000
Перед проведением технического обслуживания составные части и узлы подножки должны быть очищены от грязи и пыли. Сухую очистку осуществлять, применяя волосяную или капроновую щетку и ветошь. В холодное время года (температура окружающей среды ниже 5 °C), при необходимости, допускается производить сухую очистку ступеней лестничного марша подножки от загрязнений, снега и льда жесткой синтетической щеткой и/или пластиковым скребком.
ВНИМАНИЕ!
МЕХАНИЧЕСКАЯ ОЧИСТКА ПОДНОЖЕК С ИСПОЛЬЗОВАНИЕМ МЕТАЛЛИЧЕСКИХ ПРИСПОСОБЛЕНИЙ (СКРЕБКОВ, ЩЕТОК И Т.П.), А ТАКЖЕ МОЮЩИХ СРЕДСТВ НА АБРАЗИВНОЙ ОСНОВЕ ЗАПРЕЩАЕТСЯ.
Необходимо удалять мусор, накопившийся в зоне движения направляющих и тяг каретки, на тягах и коромыслах поворотной ступени, очищать ступени и накладки противоскольжения на краях ступеней.
При необходимости – использовать моющие средства в соответствии с рекомендациями ГОСТ Р 54612-2011 с последующей протиркой ветошью, смоченной водой, и далее – сухой ветошью насухо.
Произвести проверку работоспособности подножки, устранение неисправностей и / или регулировку (при необходимости).
Провести проверку открытия/закрытия подножки в ручном режиме:
- для открытия подножки вставить четырехгранный ключ в замочную скважину и повернуть против часовой стрелки на 90°. Вынуть четырехгранный ключ. Выдвинуть подножку вручную, потянув за верхние три ступени лестничного марша на себя до фиксации в открытом положении;
- для закрытия подножки вставить четырехгранный ключ в замочную скважину и повернуть по часовой стрелке на 90°. Вынуть четырехгранный ключ. Задвинуть подножку вручную, толкая ее за верхние три ступени лестничного марша под вагон до фиксации в закрытом положении.
С помощью секундомера провести проверку открытия/закрытия подножки в автоматическом режиме:
- после подачи сигнала на открытие, подножка должна перейти в положение «открыта» (разложена) за время от 2 до 4 с;
- после подачи сигнала на закрытие, подножка должна перейти в положение «закрыта» (сложена) за время от 3 до 5 с.
С помощью рулетки и динамометра универсального образцового электронного провести проверку (в автоматическом режиме работы) работоспособности подножки при наличии помехи.Ес
ли при открытии подножки ступени лестничного марша сталкиваются с препятствием:
- расположенном на расстоянии до 50 мм, то система обнаружения препятствий игнорируется;
- расположенном на расстоянии от 50 до 100 мм, то после воздействия подножкой на препятствие в течение 1 с, блок управления дверями (далее -БУД) должен подать команду на остановку длительностью до 0,5 с, затем на складывание подножки. После складывания подножки БУД должен выдерживать паузу в 1 с и дать повторную команду на выдвижение подножки. После трех попыток выдвижения, БУД должен подать команду на складывание и передать в систему управления сигнал о неисправности подножки;
- расположенном на расстоянии более 100 мм, после воздействия подножкой на препятствие в течение 1 с БУД должен подать команду на остановку длительностью до 0,5 с, затем на складывание подножки в пределах от 70 до 100 мм. После выдержки паузы в течение 1 с БУД должен подать повторную команду на выдвижение подножки, при этом максимальное значение силы, действующей на препятствие должно быть не более 300 Н.
После трех попыток выдвижения подножки, БУД должен подать команду на складывание и передать в систему управления сигнал о неисправности подножки.
Если при закрытии подножки ступени лестничного марша сталкиваются с препятствием:
- расположенном на расстоянии до 50 мм, то система обнаружения препятствий игнорируется;
- расположенном на расстоянии от 50 до 100 мм, то после воздействия подножкой на препятствие в течение 1 с БУД должен подать команду на остановку длительностью 0,5 с, затем на выдвижение подножки. После выдвижения подножки и выдержки времени в течение 1 с БУД должен подать повторную команду на складывание. После трех попыток складывания подножки, БУД должен подать команду на остановку подножки и передать в систему управления сигнал о неисправности подножки;
- расположенном на расстоянии более 100 мм, то после воздействия подножкой на препятствие в течение 1 с БУД должен подать команду на остановку длительностью до 0,5 с, затем на выдвижение подножки в пределах от 70 до 100 мм. После выдержки паузы в течение 1 с БУД должен подать повторную команду на складывание подножки. После трех попыток складывания подножки БУД должен подать команду на остановку подножки и передать в систему управления сигнал о неисправности подножки.
Привод подножки
Произвести внешний визуальный осмотр состояния и функциональную проверку работы привода, при которой не допускается наличие постороннего шума (стук, звон, хруст и т.п.). Устанавливаются и устраняются причины образования шума.
Салонная дверь
Двери межвагонного перехода
Произвести визуальный контроль состояния стекол, уплотняющих элементов салонных дверей, дверей межвагонных переходов. При необходимости заменить. Произвести очистку от грязи направляющих дверей.
7.6.2 Произвести проверку работоспособности блокирующего устройства дверей межвагонных переходов, при необходимости его регулировку и смазку силиконовой смазкой «Si-М» ТУ 2257-001-54736950-2001 или ПМС-300 ГОСТ 13032-77.
Произвести проверку работоспособности привода дверей межвагонных переходов, при сильном износе или поломке – заменить. При необходимости произвести регулировку положения крайних роликов каретки, пружинного возвратного цилиндра, натяжения ремня.
При наружной температуре воздуха менее 5 °C смазать контактирующие поверхности уплотнителей створок дверей межвагонных переходов силиконовой смазкой «Si-М» ТУ 2257-001-54736950-2001 или ПМС-300 ГОСТ 13032-77.
Межвагонный переход
Произвести визуальный контроль состояния волнового сильфона, площадок, кабелей заземления. При выявлении неисправностей произвести восстановительный ремонт (приложение В).
Полуавтоматический подъемник для инвалидов
Произвести внешний визуальный осмотр подъемника INV-300-CW (при наличии) на отсутствие механических повреждений, подтеков масла гидравлической системы.
Выполнить проверку работы подъемника, при необходимости, электрические функции для управления подъемником должны активироваться только тогда, когда поезд не двигается и прислонно-раздвижные двери открыты. При проверке работы подъемника необходимо открыть четырехгранный замок. После этого платформу вручную выдвинуть из исходного положения до параллельного положения с боковой стенкой поезда и фиксации.
При проверке осуществлять управление подъемником с помощью мобильного блока ручного управления. Во время использования подъемника должны включаться акустические и визуальные сигналы, которые оповещают о работе подъемника.
Санитарный комплекс
Произвести осмотр и обслуживание санитарного комплекса:
- произвести проверку состояния направляющих дверей, полотна двери кабины комплекса на равномерное движение и отсутствие загрязнений. Загрязнения на направляющих и полотне двери удалить очистителем на водной основе RST-5 («Mulder-Hardenberg GmbH»);
- при отрицательных температурах окружающей среды проверить работоспособность системы обогрева трубопроводов;
- проверить корректность работы электрооборудования, включая освещение комплекса, нагреватель электрический, датчик (комплект датчиков) температуры воздуха,. комплект обогрева трубопроводов, блок вентиляции с решеткой и вентилятором, преобразователь, панель управления;
- проверить электромонтаж комплекса, включая индикаторы занятости, кабель для вентилятора, кабель для светильников, кабель для кнопки аварийного вызова, кабель для подключения обогрева трубопроводов, шунты заземления;
- выполнить проверку целостности трубных соединений и отсутствия течи в муфтовых и резьбовых соединениях санитарного комплекса (визуально);
- выполнить опорожнение накопительного бака и тщательно промыть бак накопительный;
- очистить фильтр-грязеуловитель водяной магистрали;
- выполнить заправку водой бака водяного санитарного комплекса, проверить отсутствие течи из накопительного бака и водяного бака комплекса (визуально);
- произвести визуальный осмотр стойки с баками. При этом проверить наличие контровки и штепсельных разъемов и проверить состояние узлов крепления стойки с баками к вагону;
- проверить затяжку крышек лючков;
- проверить уровень заполнения накопительного бака по дисплею контроля уровней в шкафу управления санитарным комплексом.
- произвести проверку работоспособности освещения и динамика;
- визуально проверить туалетное сантехническое оборудование, размещаемое в туалетном помещении, включая туалетную вакуумную систему замкнутого типа со смывом водой, чашу и столешницу умывальника (мойки), дозатор жидкого мыла, держатель туалетной бумаги, крючок для одежды, зеркало рядом с умывальником, зеркало над умывальником, контейнер для мусора, крышку контейнера для мусора, комплект поручней, кран для мытья рук;
- произвести уборку туалетного помещения с использованием дезинфицирующих растворов, указанных в приложении И настоящей части руководства по эксплуатации;
- произвести заправку бумагодержателя, полотенцедержателя и наполнение картриджа дозатора мыла;
- устранить замечания по работе санитарного комплекса, выявленные в эксплуатации;
Произвести проверку функционирования санитарного комплекса (рекомендуется проводить ежемесячно).
Включить электропитание санитарного комплекса:
- подать на источник питания санитарного комплекса напряжение 110 В от электросети вагона включив в шкафу управления автомат защиты «Источник питания 110/24 В»;
- подать на электронагреватели системы обогрева трубопроводов и электронагреватель обогрева магистрали к умывальнику санитарного комплекса через термостат напряжение 220 В от электросети вагона, включив в шкафу управления автомат защиты.
Заправить водяной бак, для чего:
- убедиться, что запорные краны до унитаза и умывальника открыты;
- запорный кран слива закрыт;
- подключить водяной шланг к заправочной трубе под вагоном;
- включить подачу воды;
- контролировать заполнение водяного бака по дисплею контроля уровней (рисунок 7.9.1), при полном наполнении бака водяного возможен перелив излишков воды через переливной трубопровод под вагон;
- после заполнения бака водой отключить ее подачу и закрыть запорный кран под вагоном.
Для включения дисплея контроля уровней необходимо кратковременно прикоснуться к круглому сенсору (рисунок 7.9.1).
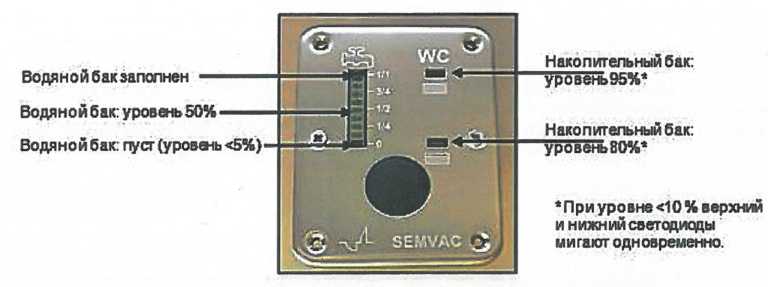
Рисунок 7.9.1 – Внешний вид дисплея контроля уровней
Зарядить пневмосистему вагона, открыть кран подачи сжатого воздуха к санитарному комплексу под вагоном, убедиться, что запорные краны до унитаза открыты.
Убедиться в «моргании» зеленого светодиода на блоке управления и индикации туалетным модулем. Произвести несколько контрольных смывов унитаза, последовательно нажимая на кнопку «Смыв», каждый раз дожидаясь окончания предыдущего цикла смыва. Убедиться в поступлении воды в унитаз. Убедиться в отсутствии протечек из подводящего трубопровода и трубопроводов внутри унитаза.
Произвести несколько смывов крана умывальника и убедиться в поступлении воды в чашу мойки, через несколько секунд после каждого поднесения рук к датчику подача воды должна самопроизвольно прекратиться. Убедиться в отсутствии протечек в патрубках слива мойки.
При проверке убедиться в отсутствии сообщений о неисправностях санитарного комплекса. Проверить визуально наличие и исправность работы оборудования санитарного комплекса.
Подвагонное оборудование
Производится визуальный контроль состояния и крепления контейнеров с оборудованием к кузову вагона. Ослабление креплений не допускается.
Произвести визуальный контроль кабельных соединений на наличие отсоединившихся или отсутствующих деталей. Наличие повреждений (деформаций, потертостей, перегибов, изломов, трещин) не допускается.
Токоприемник
Провести очистку токоприемника и крыши возле него от загрязнений. Выполнить протирку деталей токоприемника ветошью, смоченной нефрасом (нефтяном растворителе).
Произвести визуальную проверку состояния узлов и деталей токоприемника на отсутствие трещин в изоляторах, трубах и литых деталях шарниров, изгибов полозов и рам, прожогов от воздействия электрической дуги, коррозионных повреждений, нарушений лакокрасочного покрытия.
Произвести проверку надежности крепления всех деталей. Детали (тяги, рамы и др.), имеющие трещины заменить. При ослаблении крепления деталей или утере деталей крепления (шплинтов, болтов и гаек) восстановить их крепление и шплинтовку.
Произвести проверку крепления гаек и болтов динамометрическим ключом моментом в соответствии с ОСТ 37.001.050-73:
- основания к опорным изоляторам (М20) – 500 Н м;
- шунтовых соединений (М12) – 100 Н м.
Произвести проверку состояние шунтов. Шунты, имеющие обрывы свыше 10% жил – заменить, менее 10% – забандажировать поврежденное место медной проволокой. При замене шунтов разборные контактные поверхности (места крепления) очистить от старой смазки и нанести новую смазку ЭПС 98 (ЭПС 98 ВТ).
Произвести замер износа рога полоза. При диаметре трубы рога, измеренном в плоскости, перпендикулярной оси рога, в месте с наибольшим износом (определяется визуально) менее 16,5 мм – заменить полоз по износу рога.
Произвести контроль состояния вставок по наличию трещин, степени износа, наличию пропила, сколов, прожогов и прилегания к каркасу полоза и неравномерности износа крайних рядов. При наличии трещин на вставке полоз заменить.
Замену угольных вставок по износу произвести в случае остаточной высоты:
- для отечественных вставок – менее 10 мм от подошвы вставки или если от элементов каркаса, крепящих вставку, до поверхности трения менее 1 мм летом, менее 2 мм зимой, менее 3 мм при гололеде. Зазор между торцами вставок должен быть не более 1 мм;
- для импортных вставок – от подошвы угольной части вставки до поверхности трения менее 2 мм летом и зимой, 3 мм при гололеде. Зазор между торцами вставок и элементом рога должен быть не более 1 мм.
При наличии пропила или прожога (визуальный контроль), запилить пропил (прожег) под углом не более 20 ° к горизонтали. Измерить скол (при наличии). При величине скола более 30 % ширины вставки – вставку (полоз) заменить. Замер произвести в наиболее изношенном месте. Плавная волнистая поверхность трения вставок не является браковочным признаком.
Произвести проверку качества крепления вставок. Надавливанием пальцами на грани каждой вставки убедиться в отсутствии качания. При наличии ослабления затянуть крепление вставки.
При значительной неравномерности износа вставок крайних рядов развернуть полоз на 180 °.
Произвести проверку состояния тросов подъемного механизма на обрыв жил и наличие смазки. Трос, имеющий обрыв более 5 жил, заменить. При отсутствии смазки произвести нанесение смазки ЦИАТИМ-201.
Визуально проконтролировать состояние резинового корпуса пневморессоры на отсутствие трещин, вздутий (разрывов корда) и потертостей в зоне работы тросов. При наличии вышеуказанных дефектов, корпус пневморессоры заменить.
Проконтролировать визуально состояние резиновых буферов на отсутствие трещин, срезов и деформации. При наличии дефектов буфера заменить.
Произвести визуальный контроль лакокрасочного покрытия на деталях токоприемника, при нарушении произвести восстановление покрытия:
- область с нарушением лакокрасочного покрытия разогреть до температуры (100 ±20) °C промышленным феном;
- кистью нанести на разогретую область краску порошковую RAL 3020 красную гладкую, РЕ-глянец;
- область с нанесенным порошком разогреть промышленным феном на наименьшей скорости обдува до равномерного растекания порошка.
Произвести проверку величины нажатия полоза на контактный провод и время подъема/опускания токоприемника. При необходимости отрегулировать.
Величина контактного нажатия полоза должна быть:
- в летний период времени: активное – 90 Н, пассивное 105 Н;
- в зимний период времени: активное – 100 Н, пассивное 125 Н.
При проверке величины нажатия подъем токоприемника ограничивается упором на высоте (1000 ±50) мм относительно поверхности вставок полностью опущенного токоприемника. В пневморессору подается сжатый воздух давлением 0,5 МПа. К штанге в сборе прикрепляется динамометр таким образом, чтобы его вес не влиял на показания. Установка активного контактного нажатия производится в районе упора с помощью регулировочного клапана, поворотом регулировочной головки клапана по часовой или против часовой стрелки. После регулировки нажатия регулировочная головка фиксируется контргайкой, расположенной под регулировочной головкой.
Время подъема и опускания должно быть:
- от 6 до 10 с – время подъема;
- от 4 до 6 с – время опускания.
При проверке времени подъема/опускания подъем токоприемника ограничивается на максимальной рабочей высоте полоза 2100 мм от сложенного положения. В пневморессору подается сжатый воздух давлением 0,5 МПа. С началом подъема токоприемника одновременно включается секундомер и выключается при касании полоза ограничителя высоты подъема. Регулировка времени подъема выполняется поворотом регулировочной головки клапана. При подаче команды на опускание с началом опускания одновременно включается секундомер и выключается при достижении сложенного положения. Операции по проверке времени подъема/опускания токоприемника повторяются дважды.
При образовании гололеда выполнить нанесение антигололедной смазки на предварительно протертые сухие подвижные рамы и тяги, металлические части механизма подъема, боковые (вертикальные) поверхности полозов.
Смазку перед нанесением тщательно перемешать и нанести мягкой кистью равномерным слоем толщиной (1-2) мм. Расход смазки на один токоприемник примерно (200 – 300) г.
О типе нанесенной смазки, дате, времени и пункте нанесения смазки должна быть произведена запись в журнал формы ТУ-152 и формуляр токоприемника. По окончании периода образования гололеда смазку удалить, детали токоприемника протереть «насухо».
Произвести визуальную проверку состояния, качества посадки и крепления электрических соединительных разъемов пневмораспределителя ПР3 и пневмореле P1, Р2 заземленного пневматического модуля. При наличии ослабления затянуть крепление разъема.
Ограничитель перенапряжений
Внешним осмотром проверить отсутствие повреждений в фарфоровых покрышках, состояние цементных швов.
Если на поверхности фарфоровой покрышки имеется отложение солей или цементной пыли, произвести очистку поверхности салфеткой, смоченной в уайт-спирите (бензине), с последующим протиранием сухой салфеткой.
При обнаружении трещин фарфоровой поверхности или других неисправностей, которые могут вызвать нарушение герметичности, при наличии сколов или повреждений изоляционной поверхности более 20 % ограничитель заменить.
Мелкие трещины не являются причиной для браковки ограничителя, в этом случае они покрываются влагостойким покрытием.
7.13 Выключатель автоматический быстродействующий серии ВАБ-УЭТМ®-55-1600/30
Произвести визуальный контроль надежности запирания замков крышки корпуса.
Проверить выключатель на работоспособность, произвести пятикратный цикл включения/отключения. Заедания не допускаются.
Тяговый электродвигатель 1ТВ2216 — 0GC0
Произвести визуальный контроль болтовых соединений крепления остова с рамой тележки.
fodn. Дата
Со стороны редуктора осмотреть состояние фильтрующих холстов водухозаборных решеток для охлаждения тягового двигателя. При необходимости произвести их демонтаж, очистку или замену и монтаж, (смотри п.п.10.9.5); После демонтажа, при необходимости, произвести очистку отверстий воздухозаборной решетки.
Произвести проверку герметичности клеммных крышек и состояния герметика. При наличии неплотностей выполнить демонтаж крышки, проверить визуально отсутствие влаги в клеммной коробке, установить крышку с нанесением герметика.
Установка охлаждения «Bosch Rexroth AG»
Произвести визуальный контроль на отсутствие загрязнения, очистку решетки для защиты от пыльцы. Наличие загрязнений решетки для защиты от пыльцы не допускаются. Очистку выполнить при помощи пылесоса.
Выполнить проверку герметичности трубопроводов, положение шаровых кранов, проверку уровня охлаждающей жидкости расширительного бака по индикатору уровня, проверить работу насосов охлаждающей жидкости на отсутствие посторонних шумов.
Система кондиционирования воздуха ЗАО «АТК»
Кондиционер кабины машиниста (ККМ)
Произвести замену материала воздушного фильтра, допускается в период с 1 декабря по 1 апреля замену материала фильтра проводить 1 раз в два месяца или по сигналу о критической забивке материала, который передается в систему управления электропоездом.
Замену фильтроматериала производить следующим образом:
- выключить и обесточить ККМ;
- выкрутить болты и снять люк обслуживания ККМ;
- освободить доступ к окну для замены фильтрующего элемента;
- произвести замену фильтроматериалов;
- установить люк обслуживания обратно и закрутить болты.
ВНИМАНИЕ! ЗАПРЕЩАЕТСЯ УСТАНАВЛИВАТЬ ВЛАЖНЫЙ ЭЛЕМЕНТ ФИЛЬТРУЮЩИЙ. ЗАПРЕЩАЕТСЯ ЭКСПЛУАТАЦИЯ ККМ БЕЗ ФИЛЬТРУЮЩЕГО ЭЛЕМЕНТА.
Система обеспечения параметров микроклимата пассажирских салонов (СОМ)
Произвести замену материала воздушного фильтра.
Допускается в период с 1 декабря по 1 апреля замену фильтроматериала проводить 1 раз в два месяца или по сигналу о критической забивке материала, который передается в систему управления электропоездом.
Замену фильтроматериала производить следующим образом:
- выключить и обесточить СОМ;
- выкрутить болты и снять люк обслуживания СОМ;
- освободить доступ к окну для замены фильтрующего элемента;
- произвести замену фильтроматериалов;
- установить люк обслуживания обратно и закрутить болты.
Установка обеззараживания воздуха (УОВ)
Произвести контроль режимов работы УОВ по сигналам в системе управления установки кондиционирования воздуха (УКВ) электропоезда. Сигналы режимов работы УОВ приведены в таблице 7.16.1.
Таблица 7.16.1 – Сигналы режимов работы УОВ
№ п/п | Сигналы в системе управления УКВ | Причины |
1 | Штатная работа | |
Подается сигнал «РАБОТА»
Через (26±3) с при включении УФ ламп подаются сигналы «Контроль 1», «Контроль 2», «Контроль 3» и «Контроль 4» |
Подача напряжения питания на УОВ | |
Подаются сигналы «Контроль 1», «Контроль 2», «Контроль 3 и «Контроль 4» | Работа УОВ при включенных УФ лампах | |
2 | Неисправность УФ лампы и/или ЭПРА | |
Не подается сигнал | Выход из строя: | |
«Контроль 1»
«Контроль 2» «Контроль 3» «Контроль 4» «Контроль 1» «Контроль 2» «Контроль 3» «Контроль 4» |
УФ лампы 1
УФ лампы 2 УФ лампы 3 УФ лампы 4 ЭПРА 1 ЭПРА 2 ЭПРА 3 ЭПРА 4 |
|
3 | Перегрев УОВ | |
Не подаются сигналы «Контроль 1», «Контроль 2», «Контроль 3 и «Контроль 4». Подается сигнал «Перегрев». | Температура УОВ более 60 °C |
При подаче сигнала «Перегрев» в систему управления УКВ необходимо:
- снять напряжение питания с УОВ путем отключения автомата Q16 в шкафу системы управления УКВ;
- выяснить и устранить причину срабатывания датчика перегрева УОВ;
- после устранения причины подать напряжение питания на УОВ путем включения автомата Q16 в шкафу системы управления УКВ.
При неисправности заменить электронные пускорегулирующие аппараты ЭПРА Л~380-1×270-3302-168 и УФ лампы АНЦ 270/133-П3.
Замену УФ лампы производить в чистых хлопчатобумажных перчатках. Отметку о замене УФ лампы и ЭПРА внести в паспорт на установку климатическую пассажирского салона.
В случае боя бактерицидных амальгамных ламп извлечь остатки лампы из установки, используя перчатки для защиты от порезов, и поместить их в металлический контейнер для последующей утилизации.
Проверить визуально работу системы кондиционирования, проверить показания датчиков температуры для контроля внутри салона, датчиков для приточного и смешанного воздуха. Проверить наличие связи с системой управления поезда на мониторе в кабине и отсутствие диагностических ошибок.
Рециркуляционный обогреватель
Проверить работу обогревателей при включении с пульта машиниста.
Тормозной резистор
Проверить внешнее состояние резистора, состояние эластичных опор, отсутствие люфта в эластичных опорах, крепление внешних болтовых соединений, крепление шин заземления. При ослаблении произвести крепление болтов M10 с моментом затяжки 22 Н м.
Проверить наличие зазора между витками резистивного элемента – при зазоре менее 5 мм произвести рихтовку ленты.
Токоотводящее устройство
Произвести контроль состояния и надежность крепления. Ослабление креплений, механические повреждения корпуса не допускаются.
Безопасный локомотивный объединенный комплекс БЛОК
7.19.1 Произвести внешний осмотр блоков комплекса и проверить:
- наличие на них пломб, в соответствии с требованиями «Руководства по эксплуатации 36905-000-00 РЭ»;
- сроки действия периодических регламентных работ, указанных на этикетках блоков в соответствии с таблицей 7.19.1. Блоки, у которых эти сроки могут истечь до следующего технического обслуживания на КП или ПТО, следует заменить;
- выполнить проверки комплекса БЛОК на КП (ПТО) в соответствии с таблицей 7.19.2 (тип оборудования, используемого при проверках, должен соответствовать указанному в «Руководстве по эксплуатации 36905-000-00 РЭ»).
По окончании работы опломбировать блоки комплекса БЛОК, согласно «Руководства по эксплуатации 36905-000-00 РЭ».
Таблица 7.19.1 – Периодические регламентные работы (ПРР)
п/п | Наименование устройства, блока | Периодичность ПРР | Вид ТО |
1 | СШ | 15 лет | R4 |
2 | Монитор 5, БИЛ-УМВ, БИЛ-ПМВ, БИЛ-ИП, БР-У, БС-СН/БЛОК, МВ, МСС | 15 лет | R4 |
3 | Рукоятки бдительности РБ, РБС, РБП | 15 лет | R4 |
4 | АЛС-ТКС | 15 лет | R4 |
5 | КП-РС | 2,5 года | I4 |
6 | ДПС-У | 2,5 года | I4 |
7 | БС-ДПС | 15 лет | R4 |
8 | ЭПК-153А | 6 мес. | I2 |
9 | КОН | 6 мес. | I2 |
10 | Кабельный монтаж | 15 лет | R4 |
И | ПЭКМ, ЭПВ | 5 лет | I6 |
12 | ПРИС | 15 лет | R4 |
13 | ТСКБМ-К | 2 года | I4 |
14 | ТСКБМ-ПCAN | 5 лет | I6 |
15 | Антенна локомотивная | 10 лет | R2 |
Таблица 7.19.2 – Перечень проверок комплекса БЛОК на КП (ПТО)
Наименование проверок | |
1 | Проверка напряжения питания ИП-ЛЭ |
2 | Проверка сопротивления изоляции |
3 | Проверка и ввод эксплуатационных характеристик |
4 | Проверка и изменение постоянных параметров канала САУТ |
5 | Диагностика ячеек и блоков комплекса БЛОК |
6 | Проверка функции принудительной остановки (при наличии ЭПВ) |
7 | Проверка функции принудительной остановки при отсутствии движения электропоезда |
8 | Проверка работы устройств цифрового радиоканала |
9 | Проверка приемных катушек |
10 | Проверка исправности датчиков угла поворота универсальных ДПС-У |
11 | Проверка исправности рукояток РБ, РБС, РБП |
12 | Проверка исправности ключа ЭПК |
13 | Проверка исправности цепи контроля включения тяги |
14 | Проверка функции запрета несанкционированного движения (скатывания) |
15 | Проверка срабатывания блока КОН |
16 | Проверка соответствия ЭК и базы данных САУТ |
17 | Проверка приема сигналов канала АЛСН |
18 | Проверка приема сигналов канала АЛС-ЕН |
19 | Проверка работы функции контроля бодрствования машиниста |
20 | Проверка функции служебного торможения |
21 | Проверка исправности комплектов БЛОК |
22 | Проверка индикации давления в магистралях локомотива (МВПС) |
23 | Проверка приема спутниковых сигналов |
24 | Проверка функционирования ячейки Шлюз CAN (Шлюз-CAN-MVB2) |
25 | Проверка формирования речевых сообщений |
26 | Проверка приема сигналов от путевых генераторов |
27 | Проверка переключения режимов движения |
28 | Проверка проведения комплексом БЛОК сравнения фактической скорости с допустимой, с применением мер к торможению в случае превышении фактической над допустимой |
29 | Проверка автоматического перехода блоков комплекса БЛОК в активное (пассивное) состояние при изменении признака активности кабины |
30 | Проверка работы с устройством АЛСО с подвижными блок-участками. |
31 | Порядок проведение предрейсовой диагностики |
Примечания:
- Нa МВПС, оборудованных двумя комплектами БЛОК, во второй кабине провести работы по техническому обслуживанию в полном объеме.
- При наличии замечаний по работе БЛОК в журналах форм ТУ-152 и ТУ-133 должны быть дополнительно проверены исправность и сопротивление изоляции электрических цепей БЛОК, напряжение и амплитуда пульсаций источников электропитания БЛОК, значения введенных в блок СШ эксплуатационных характеристик, формирование сигналов для САУТ, ТСКБМ. Амплитуда пульсаций проверяется осциллографом.
Пневматическое и тормозное оборудование
Произвести проверку внешнего состояния контейнеров с оборудованием, крепление к кузову вагона и крепление щитов, наличие неповрежденного заземления к подвижному составу.
При открытых щитах визуально проверить состояние всех компонентов внутри контейнеров на наличие заметных повреждений в видимой зоне, ослабленных, недостающих или незадействованных крепежных элементов, утечек сжатого воздуха.
Проверить прочность посадки электрических соединительных штекеров и отсутствие признаков проникновения влаги.
Произвести визуальный осмотр крана машиниста 345, проверить крепления электрических и пневматических соединений и проверить показатели крана машиниста:
- давление сжатого воздуха в тормозной магистрали (ТМ) в положении II «Поездное» крана машиниста (зарядное давление) должно быть (0,50 ±0,01) МПа ((5,2 ±0,1) кгс/см2);
- автоматическое поддержание установившегося зарядного давления (0,50 ±0,01) МПа в ТМ при создании искусственной утечки должно быть не более ±0,015 МПа;
- снижение в течении 180 с установившегося давления в ТМ в положении IV «Перекрыта с питанием» после ступени торможения на величину не более ± 0,01 МПа;
- время снижения давления в ТМ при служебном торможении (положение V) от 0,49 до 0,39 МПа должно быть в пределах от 4 до 5 с;
- время снижения давления в ТМ при экстренном торможении (положение VI) от 0,49 до 0,15 МПа должно быть не более 3 с;
- время снижения давления в ТМ при снятии напряжения с ЭПВН2 с 0,49 до 0,15 МПа должно быть не более 3 с;
работоспособность функции включения и отключения блокировки тормозов в штатном режиме подачей напряжения на ЭПВН1; - герметичность мест соединения узлов и деталей – пропуск воздуха не допускается;
- работоспособность функции диагностики блокировки тормозов и крана трехходового КрРШ2 в ручном режиме управления переводом ручки крана из положения «Д» в положение «Р»;
- замыкание микропереключателей контроллера в положении «Экстренное торможение».
Произвести визуальный осмотр блоков тормозного оборудования (БТО) 420, 420-01,420-02.
Произвести визуальный осмотр блоков пневматического оборудования (БПО) 419 дистанционного управления давлениями сжатого воздуха, подходящего к тифону и свистку.
Произвести визуальный осмотр блоков пневматического оборудования (БПО) 422 дистанционного управления давлениями сжатого воздуха, подходящими к:
- форсунке песочницы передней тележки моторного вагона электропоезда;
- форсунке песочницы задней тележки моторного вагона электропоезда;
- системе осушки песка, находящегося в бункере;
- сидениям машиниста и помощника машиниста, стеклоочистителям.
Система пескоподачи
Проверить уровень наполнения песком песочных баков, в случае необходимости произвести их пополнение.
Визуальным осмотром проверить отсутствие повреждений, ослабленных, недостающих крепежных элементов, утечек сжатого воздуха, самопроизвольного выхода песка. Проверить качество посадки штекерных разъемов питания нагревательных элементов.
Произвести проверку и при необходимости регулировку положения наконечников подсыпных рукавов, которые должны быть направлены в зону контакта колеса с рельсом и располагаться от головки рельса по высоте на расстоянии «Т» (37 – 45) мм, от оси колеса на расстоянии «С» (315 – 325) мм, как показано на рисунке 7.20.1. При необходимости, регулировку произвести смещением кронштейнов «У» и «Ф» в пазах (рисунок 7.20.2).
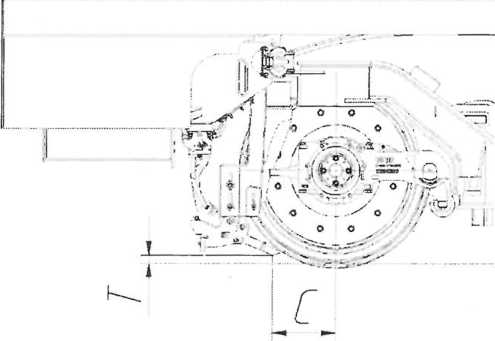
Рисунок 7.20.1 – Расположение наконечника подсыпного рукава
После проведения регулировки положения наконечников подсыпных рукавов произвести затяжку резьбовых соединений кронштейнов «У» и «Ф» (рисунок 7.20.2) с необходимым усилием (М8 – 17,8 Н-м, М12 – 72 Н-м, М16- 174 Н-м).
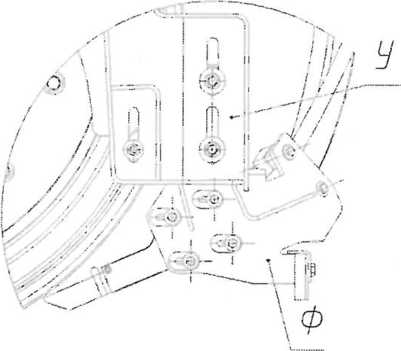
Рисунок 7.20.2 – Регулировка положения наконечника подсыпного рукава
Произвести проверки исправности подачи песка из обеих кабин управления под колесные пары на вагонах 1 и 5, с учетом нормы расхода песка:
- смонтировать устройство для улавливания песка (мешок и т.п.) на наконечниках подсыпных рукавов;
- включить электропитание систем отопления труб для подачи песка (должен наблюдаться заметный нагрев систем отопления труб для подачи песка);
- произвести подачу песка из кабины машиниста (подача песка, в зависимости от направления движения, должна производиться перед моторной тележкой, на наконечниках подсыпных рукавов должен быть заметен выход теплого воздуха);
- снять устройства для улавливания песка;
- произвести взвешивание устройств для улавливания песка;
- пересыпать песок из устройств для улавливания в песочные баки;
- после заполнения песочного бака закрыть крышку предварительно очистив край наполнительного штуцера от остатков песка и пыли.
ВНИМАНИЕ: НОРМА РАСХОДА ПЕСКА ПОД ОДНО КОЛЕСО ДОЛЖНА СОСТАВЛЯТЬ В ПРЕДЕЛАХ ОТ 0,3 ДО 0,5 КГ/МИН, ПРИ ЭТОМ КОЛИЧЕСВО ПЕСКА В УСТРОЙСТВАХ УЛАВЛИВАНИЯ ДОЛЖНО БЫТЬ ОДИНАКОВЫМ!
Произвести визуальный осмотр блоков пневматического оборудования (БПО) 425 отключения при помощи разобщительных кранов агрегатов компрессорных, питательной магистрали (ПМ) а также сообщения тормозной магистрали (ТМ) и ПМ через обратный клапан при следовании электропоезда «Холодным резервом».
Произвести визуальный осмотр индикатора тормозного 421 (ИТ) контроля текущего состояния фрикционного рабочего тормоза и стояночного тормоза пружинного типа на подвижном составе во время стоянки.
ИТ приводится в действие при помощи пневматического сигнала от фрикционного рабочего тормоза и стояночного тормоза пружинного типа.
Определение состояния тормоза осуществляется при помощи цветовых сигналов в двух окнах индикации на передней стороне устройства.
Произвести осмотр регуляторов положения кузова 003ММ, 003ММ-01, 003ММ-02, 003ММ-03 (РПК) автоматического поддержания заданного уровня высоты кузова от головки рельса независимо от величины нагрузки на пневморессору.
Произвести осмотр и проверку оборудования по замечаниям машинистов, указанным в журнале технического состояния электропоезда. Порядок устранения возможных отказов и повреждений тормозного оборудования указан в соответствующих руководствах по эксплуатации.
Произвести визуальный осмотр состояния шлангопроводов на отсутствие видимых повреждений (трещин, пористости, утечек сжатого воздуха). Выявленные недостатки устранить.
Произвести осмотр состояния трубопроводов на отсутствие видимых повреждений (коррозии, ослабленных, недостающих или незадействованных крепежных элементов, утечек сжатого воздуха). Выявленные недостатки устранить.
Произвести полное полуавтоматическое опробование тормозов.
Опробование тормозов выполняется в полуавтоматическом режиме, т.е. в режиме при котором требуется только частичное участие персонала (локомотивной бригады), при этом на монитор системы верхнего уровня (СВУ) должны отображаться соответствующие «подсказки», процент выполнения проверки тормозов и действие, которое выполняется в данный момент времени (рисунок 7.20.3).
Алгоритм опробования при полном полуавтоматическом режиме указан в разделе Б.4.1 приложения Б настоящего Руководства.
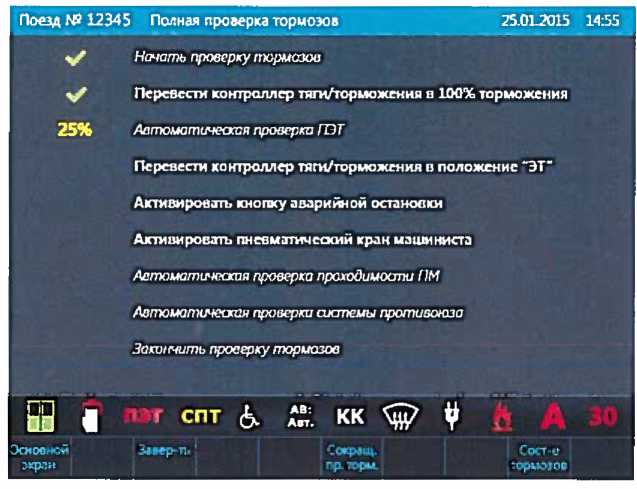
Рисунок 7.20.3 – Экран «Полная проверка тормозов»
Агрегат компрессорный винтовой АКБ 0,81/1 (АКБ):
- визуально проверить состояние панели управления и щита электрооборудования (находятся в шкафу электрооборудования), наличие трещин на приборах не допускается;
- проверить уровень масла в компактном модуле – при уровне масла ниже минимума долить масло, для чего медленно открутить пробку маслоналивной горловины, залить масло до максимального уровня, после чего закрутить пробку. Произвести пуск АКБ, дать ему проработать около 3 мин для удаления воздушных пробок, проверить уровень масла, при необходимости долить до максимального уровня;
- проверить состояние воздушного фильтра по индикатору засоренности, при необходимости заменить воздушный фильтр. Вынуть фильтрующий элемент из корпуса, очистить посадочное место фильтра от пыли и грязи, установить новый фильтрующий элемент, либо старый после чистки. Старый фильтрующий элемент подлежит чистке не более одного раза.
Чистка фильтрующего элемента проводится двумя способами:
- выбить пыль встряхиванием, не прилагая больших усилий, чтобы не повредить фильтрующий элемент;
- продуть изнутри фильтрующий элемент сухим сжатым воздухом давлением 0,5 МПа, направляя струю воздуха под углом к фильтрующей поверхности.
При замене фильтра не допускать попадания пыли и грязи внутрь впускного клапана компрессора;
- произвести визуальный осмотр внутренних узлов АКВ;
- визуально проверить состояние рукавов и пневмотрубок, не допускается подтеков масла и травления воздуха в местах соединений рукавов и пневмотрубок. В случае не герметичности рукавов высокого давления они подлежат замене;
- визуально проверить состояние электромагнитных клапанов управления и регенерации осушителями.
Агрегат компрессорный поршневой безмасляный АКПБ 0,07/0,7 Произвести очистку (протереть ветошью) от пыли, грязи, масла и других загрязнений наружные и внутренние поверхности АКПБ, включая наружные и легкодоступные внутренние части двигателя, а также наружные части компрессорной головки.
Система видеонаблюдения и оповещения пассажиров
Произвести очистку от грязи и пыли наружные поверхности элементов: видеокамера заднего вида, видеокамера «мертвой» зоны, видеокамера «черный ящик», громкоговоритель кабины управления, монитор видео информирования, микрофон, пульт управления, боковое, лобовое и салонное светодиодные табло, модуль салонного переговорного устройства, усилитель УТ-100.
Выполнить контроль изображения на предмет искажения, помех и т.д. с монитора видео информирования, пульта управления, бокового, лобового и салонного светодиодных табло.
Провести проверку работы и настройку видеокамер: заднего вида, «мертвая» зона, «черный ящик» и салона вагона.
Провести проверку работоспособности громкоговорителей (салона, кабины управления, портала и туалета) и усилителя УТ-100.
Проверить резервное питание от аккумуляторной батареи контроллера управления питанием сервера.
При необходимости выполнить обновление версии программного обеспечения сервера.
Произвести визуальную проверку внешнего состояния и надежности подключения кабелей и кабельных разъемов сервера, пульта управления, модуля салонного переговорного устройства, усилителя УТ-100, коммутаторов сети Ethernet SW16, SW24, и повторителя резервного канала.
Микропроцессорная система управления и диагностики (МПСУиД)
Произвести внешний осмотр состояния блоков и изделий системы и проверить:
- сохранность гарантийных пломб на корпусе, правильность маркировки и четкость нанесения обозначений в соответствии с требованиями конструкторской документации на блоки. Блоки с нарушениями опломбирования снять и подвергнуть проверке;
- надежность крепления блоков и изделий, и их составных частей;
- отсутствие механических повреждений, загрязнений и сколов краски;
- надежность крепления и подсоединения кабелей к блокам, состояния фиксирующих скоб разъемов;
- состояние контактов (клемм, зажимов) и надежность соединения проводов МПСУиД;
- состояние соединителей и надежность их сочленения. При обнаружении на штырях соединителя следов загрязнения, штыри протираются тампоном смоченным спиртом до полного снятия загрязнения;
- отсутствие обрывов или повреждений соединительных кабелей;
- отсутствие следов коррозии, отсоединившихся или слабо закрепленных элементов;
- соблюдение сроков действия поверки блоков, указанных в таблице 7.22.1. Порядок проведения поверки конкретных типов блоков описан в соответствующих методиках поверки. Блоки, не прошедшие поверку, подлежат замене.
При выявлении трещин (сколы) корпуса, нарушений в уплотнении корпуса с разъемами, контакты которых имеют не удаляемые следы нагара или электрокоррозии, произвести демонтаж и замену блока.
Таблица 7.22.1 – Периодическая поверка блоков МПСУиД
Наименование блока | Периодичность поверки | Вид технического обслуживания |
БС-СИ2 | 12 лет | I4 (при пробеге 2,4 млн км) |
ПНКВ-3 | 4 года | I6 |
БС-ДД-1 | 5 лет | I3 (при пробеге 1 млн км) |
Произвести считывание данных регистратора параметров РПМ.
Произвести обработку данных РПМ в автоматическом режиме. Выявленные замечания устранить.
При включенном выключателе управления проверить по монитору срабатывание органов управления, подключенных к блоку связи с пультом БСП. Проверку выполнить при отключенных поочередно первом и втором каналах питания.
Выполнить проверку работоспособности блоков МПСУиД в соответствии с руководствами по эксплуатации на конкретный блок. Перечень блоков МПСУиД, подлежащих проверке работоспособности представлен в таблице 7.22.2.
Таблица 7.22.2 – Перечень блоков МПСУиД, подлежащих проверке
Наименование блока | Периодичность проверки | Вид технического обслуживания |
БС-ДЦ-1 | После замены блока | – |
БВС-2 | После замены блока | – |
БКТБ | 18 месяцев или после замены блока | I2 |
БПЛ RS485-CAN | После замены блока | – |
БПЛ RS485-Ethemet | После замены блока | – |
БПЛ RS485-RS485 | После замены блока | – |
БСП-2 | После замены блока | – |
БС-РС | После замены блока | – |
БС-СИ2 | После замены блока | – |
БУК | После замены блока | – |
ИП-ЛЭ | 5 лет или после замены | I3 (при пробеге 1 млн км) |
ДН-4 | 1 месяц или после замены | VI |
ПНКВ-3 | После замены | – |
Монитор 6 | 5 лет или после замены монитора | I3 (при пробеге 1 млн км) |
ЦБУ | После замены блока | – |
Блоки, вышедшие из строя в процессе эксплуатации или не прошедшие периодическую проверку, заменить с последующей проверкой работоспособности.
Выполнить с периодичностью один раз в 5 лет замену клавиатуры монитора 6 с последующей проверкой работоспособности:
- отсутствие пиктограммы «наличие сим-карты» (определяет фактическое наличие сим-карты в системе «БРУС-М»);
- отсутствие пломб на шкафе приборов безопасности.
Выполнить проверку работы МПСУиД в режиме резервирования с поочередным отключением каналов питания.
Входная двухстворчатая дверь прислонно-сдвижная («КМТ»)
Перед производством технического обслуживания двери должны быть обесточены.
Произвести визуальную проверку на отсутствие механических повреждений.
Привод
Произвести функциональную и визуальную проверку. Проверить наличие всех деталей, проверить отсутствие шумов при работе электромеханического привода.
При необходимости произвести подтягивание болтовых соединений с соответствующим моментом затяжки и заменой защитного покрытия болтов. После окончания всех монтажных и регулировочных работ крепление болтовых соединений выполнить с моментами затяжки, указанными в таблице 7.23.1. Болты M16x1,5 поворотной колонки затягиваются с моментом 55 Нм. Все болты, винты и гайки маркируются сургучом (красным) и обрабатываются клеем Loctite 243 или аналогичным веществом.
Таблица 7.23.1 – Моменты затяжки болтовых креплений
Поз. | Конструктивный элемент | Болты/гайки | Крутящий момент, Н-м |
1 | Привод/портал | М12×40 | 93,1 |
2 | Привод/дверная створка | М8×25 | 40,1 |
3 | Поворотная колонка/портал | М8 | 27,3 |
4 | Угол раствора дверной створки | М5×16 | 4,2 |
5 | Выключатель «Дверь заблокирована» | М5×16 | 5,5 |
Произвести визуальную проверку зубчатого ремня на параллельность и износ (истирание, трещины, недостающие зубья). При необходимости зубчатый ремень очистить (ветошью) или заменить.
При недостаточном натяжении зубчатого ремня провести инструментальную проверку и регулировку при помощи измерительного прибора Krikit 1:
- измерить натяжение зубчатого ремня при открытой двери внизу зубчатого ремня. Точка измерения находится посередине между зажимом и поворотным роликом. Установочный размер (25 – 30) делений шкалы прибора. Если предельные значения натяжения зубчатого ремня превышены или занижены, выполнить регулировку и повторить измерение натяжения зубчатого ремня;
- измерить разницу натяжения сверху и снизу при закрытой двери. Если одно из измеряемых значений находится за пределами допустимых значений, произвести регулировку и замерить разницу натяжения сверху и снизу при закрытой двери.
Процесс измерения натяжения зубчатого ремня всегда выполнять на внешней, гладкой стороне.
Произвести визуальный осмотр направляющей шины в сборе и направляющего ролика в сборе на наличие видимых повреждений; состояние и крепление деталей. Во избежание повреждений металла, лака и других компонентов проверить отсутствие выступающих кромок и точек пересечения. Визуальным осмотром произвести проверку состояния защитного покрытия болтов. Поврежденное покрытие обработать клеем Loctite 243 или аналогичным веществом.
Произвести визуальный осмотр линейной направляющей с шариковой кареткой (продольный сдвиг). При ручной проверке работы раздвижных дверей определить отсутствие шумов и легкость хода дверей, отсутствие свободного хода линейной направляющей относительно двери. На линейную направляющую с шариковой кареткой нанести смазку Klüber ISOFLEX TOPAS NB 152.
На опору для направляющих роликов (поперечное перемещение) произвести нанесение смазки Interflon Fin Lube TF.
Визуальным осмотром произвести проверку состояния и крепления фиксирующего пальца и нанести смазку Klüber ISOFLEX TOPAS NB 152.
Произвести функциональную и визуальную проверку энергетической цепи и соединительных элементов привода – осмотреть состояние крепления соединительных элементов на кронштейнах, соединение энергетической цепи с соединительными элементами, отсутствие повреждений на энергетической цепи и соединительных элементах энергетической цепи.
При функциональной проверке работы дверей энергетическая цепь должна двигаться свободно.
Электрические разъемные и резьбовые соединения
Произвести проверку на прочность посадки электрических разъемных и резьбовых соединений на клеммных коробках и датчиках, распределителе дверных полотен.
Створки двери
Произвести визуальную проверку створок двери на наличие видимых повреждений; состояние и крепление деталей, движение створок от руки. Во избежание повреждений металла, лака и других компонентов проверить отсутствие выступающих кромок. Произвести проверку состояния болтовых соединений.
Произвести функциональную проверку поворотной колонки в сборе, при которой проверить правильность высоты расположения поворотной колонки. Если поворотные рукава верхней и нижней направляющей ролика остаются свободными на протяжении всего хода (ролики на нижнем поворотном рукаве полностью введены в направляющую шину), то высота расположения поворотной колонки в норме. При необходимости выполнить регулировку высоты поворотной колонки.
Аварийная рукоятка
Произвести визуальную проверку состояния аварийных рукояток на наличие повреждений, крепления корпусов. При функциональной проверке проверить взаимодействие аварийной рукоятки и троса Боудена.
Тросы Боудена внутреннего и наружного устройств разблокировки регулируются таким образом, чтобы включался контрольный переключатель (на поворотном рычаге) и затем устройство блокировки переводилось в положение «за мертвой точкой». Дверные створки должны легко открываться вручную. Регулировку троса Боудена выполнять при помощи соответствующего регулировочного болта на поворотном рычаге.
Розетка и штепсель высоковольтной цепи напряжения 3 кВ
При обесточенном электропоезде произвести осмотр корпусов холостого приемника межпоездных высоковольтных соединений на отсутствие механических повреждений. Специальным ключом открыть поворотную крышку. Произвести осмотр штепселя и розетки на отсутствие влаги (снега, льда) и загрязнений. Выполнить проверку контактов (штепселей и розеток) межпоездных высоковольтных соединений на отсутствие подгаров, механических повреждений, исправность фиксирующих устройств, отсутствие повреждений кабелей и защитных чехлов. При наличии повреждений демонтировать розетку (штепсель) межпоездных высоковольтных соединений и произвести ремонт или замену.
Выполнить замер сопротивления изоляции цепи межпоездных высоковольтных соединений мегаомметром напряжением 2500 В. Сопротивление изоляции должно быть не менее 10 МОм.
После проведения технического обслуживания провести проверку работоспособности системы питания 3 кВ от внешнего источника питания. Порядок выполнения проверки указан в приложении Л Руководства по эксплуатации 32303.0.00.000.000 РЭ7.
Двери салона электропоезда наружные ДБПС 004.01.00.000
Произвести наружный визуальный осмотр каждой двери на предмет отсутствия видимых перекосов дверного полотна, целостности обшивки, стеклопакета и уплотнителей.
Произвести визуальную проверку надежности крепления привода к проему, консолей и полотен дверей к приводу (наличие и целостность контрольных маркировок).
Проверить работоспособность дверей, производством трех циклов открытия и закрытия дверей в централизованном и индивидуальном режимах убедиться в отсутствии посторонних звуков, дверные полотна должны плавно, без заеданий движения створок открываться и закрываться.
Провести проверку работы мотор – редуктора по наличию и целостности контрольных маркировок, при выявлении неисправности произвести замену.
Проверить работоспособность линейных подшипников, убедиться в отсутствии посторонних звуков, загрязнений, проверить наличие смазки.
Проверить работоспособность механизма фиксации (наличие и целостность контрольных маркировок, наличие смазки на оси вращения кронштейна с роликом, отсутствие заеданий при фиксации).
Произвести визуальную проверку расположения эксцентриков полотна (наличие контакта поверхности эксцентрика с гранью паза).
Произвести визуальную проверку параллельности полотен дверей, убедиться в отсутствии перекоса.
При помощи специального четырехгранного ключа проверить наличие фиксации механического замка в крайних положениях, убедиться в наличии красной индикации при закрытии, зеленой при открытии замка.
Проверить наличие винтов крепления и надежность фиксации направляющей полотна.
Произвести визуальную проверку зацепа полотна (наличие и целостность контрольных маркировок).
Проверить защиту от съема дверного полотна на консоли (наличие противосъемника).
Произвести визуальную проверку верхней тяги консоли (наличие и целостность контрольной маркировки на консоли).
Проверить фиксацию разъемов и наличие этикеток БУД.