Выполнить работы в объеме технического обслуживания 14 и дополнительно:
Механическое оборудование
Беззазорное сцепное устройство БСУ-ТМ122:
- проверить визуально отсутствие сплошного зазора между торцами головок межвагонных сцепок в сцепленном состоянии;
- проверить визуально состояние пружин опор сцепок и измерить толщину пластиковых скользунов опор (при толщине менее 14 мм скользуны подлежат замене);
- проверить наличие графитовой смазки в пространстве между корпусами поглощающего аппарата. Старую смазку удалить салфеткой, нанести новую смазку кистью слоем толщиной примерно 0,5 мм.
Муфта зубчатая ZBG 238
Произвести проверку монтажного положения. Условием надлежащего функционирования муфты является исправное состояние системы скользящих ступиц со стороны редуктора.
При проверке монтажного положения муфты на тележке произвести измерение смещения муфты в вертикальном, горизонтальном и осевом направлении. При необходимости восстановить монтажное положение муфты.
Монтажное положение муфты необходимо внести в протокол.
ВНИМАНИЕ: ПЕРЕД ВВОДОМ В ЭКСПЛУАТАЦИЮ НЕОБХОДИМО УБЕДИТЬСЯ, ЧТО МУФТА УСТАНОВЛЕНА И ВЫРОВНЕНА ПРАВИЛЬНО!НЕОБХОДИМО СОБЛЮДАТЬ МОНТАЖНОЕ ПОЛОЖЕНИЕ МУФТЫ. ОТЛИЧАЮЩЕЕСЯ МОНТАЖНОЕ ПОЛОЖЕНИЕ МОЖЕТ ПРИВЕСТИ К ВЫХОДУ МУФТЫ ИЗ СТРОЯ!
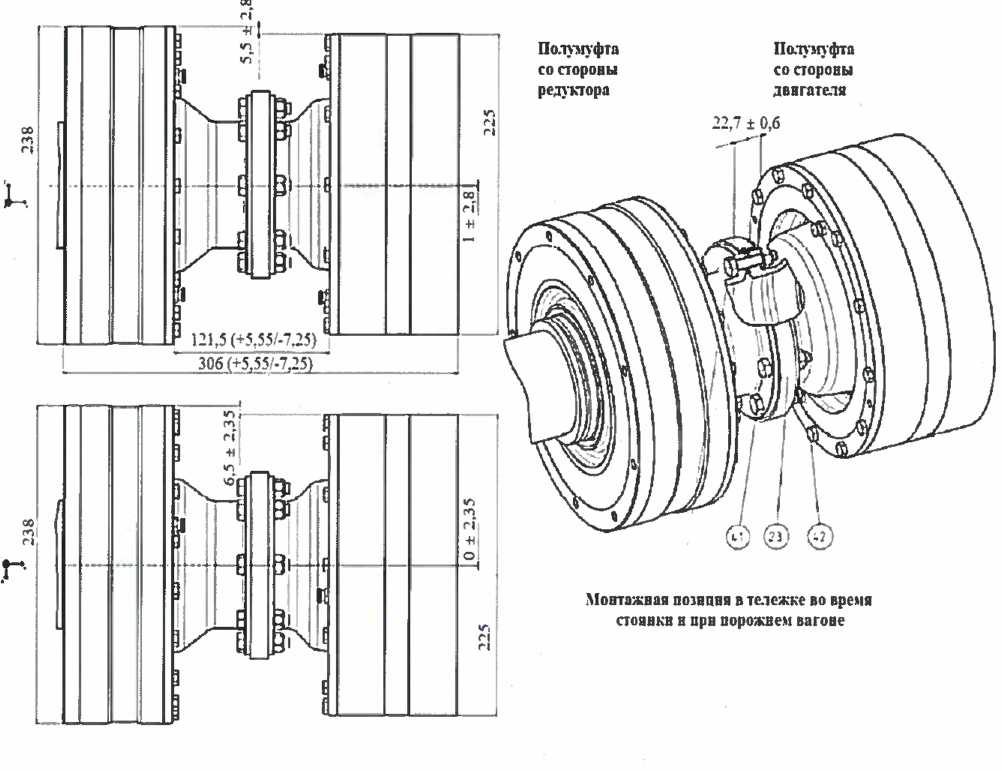
Рисунок 12.1.2 – Положение муфты
Монтажная позиция в тележке во время стоянки в при порожнем вагоне
Из-за осадки рессор 1-ой ступени подвешивания изменяется настройка муфты. Произвести контроль осадки и выполнить соответствующую регулировку для ее компенсации.
ВНИМАНИЕ: ПОСЛЕ УСТАНОВКИ НОВЫХ РЕССОР 1-ОЙ СТУПЕНИ ПОДВЕШИВАНИЯ, А ТАКЖЕ ПЕРЕД ВВОДОМ В ЭКСПЛУАТАЦИЮ ЗАМЕНЕННЫХ ТЕЛЕЖЕК ПОВТОРНО ПРОВЕРИТЬ МОНТАЖНОЕ ПОЛОЖЕНИЕ МУФТЫ И ОСАДКУ РЕССОР 1-ОЙ СТУПЕНИ ПОДВЕШИВАНИЯ ЧЕРЕЗ 24 ЧАСА ПОСЛЕ ВВОДА В ЭКСПЛУАТАЦИЮ!
Произвести добавление смазки POLYLUB GLY 791 в полумуфту со стороны двигателя и редуктора.
Смазку добавить шприцем через смазочный ниппель.
В полумуфту со стороны двигателя добавить 30 (+10) г смазки, в полумуфту со стороны редуктора – 20 (+10) г смазки. Демонтаж муфты не требуется.
Клещевые механизмы (Knorr-Bremse)
Для определения интервалов проведения капитального ремонта, провести выборочный капитальный ремонт, проверить отдельные клещевые механизмы на исправность работы, внешнее состояние, а также на отсутствие износа.
Произвести демонтаж любого клещевого механизма.
Вывести блок клещевого механизма из эксплуатации. Открыть заслонку контейнера тормозного оборудования и открыть доступ к соответствующим шаровым кранам. Перекрыть подачу сжатого воздуха к клещевым механизмам и удалить воздух из всех подключенных пневматических магистралей и резервуаров. На клещевые механизмы больше не должен воздействовать сжатый воздух. Закрыть соответствующие шаровые краны.
Произвести аварийное отпускание пружинного аккумулятора клещевого механизма:
- откинуть вверх пружинную скобу трубчатого шплинта и вынуть соответствующий шплинт;
- вытянуть устройство дистанционного управления тросовой тяги и удерживать в течение, как минимум, одной секунды (ход задействования около 20 мм);
- отвести устройство дистанционного управления назад и зафиксировать соединителем;
- тормозные накладки соответствующего клещевого механизма должны отойти от фрикционных дисков.
Повернуть возвратный шестигранник гаечным ключом SW 24 по часовой стрелке, пока регулятор не будет свинчен до упора.
Извлечь тормозные накладки. Открыть фиксирующую задвижку с помощью стержневого инструмента (отвертки или круглого прутка). Для открытия пруток насадить на продольное отверстие фиксирующей задвижки. Накладки выпадут.
Отсоединить пневматические магистрали от патрубка цилиндра служебного тормоза и патрубка тормоза с пружинным аккумулятором.
Демонтировать устройство дистанционного управления с запасного устройства отпуска:
- закрыть шаровой кран;
- если тормозной диск горячий, то он должен остыть;
- зафиксировать трос аварийного отпуска клещевого механизма.
Удалить крепежные винты из кронштейна и вынуть клещевой механизм из тележки.
Закрыть патрубки сжатого воздуха блока клещевого механизма крышками.
Закрыть патрубки сжатого воздуха пневматических магистралей крышками.
Произвести монтаж нового или отремонтированного клещевого механизма:
Перед монтажом установить максимально возможный раствор клещевых механизмов. Для этого повернуть возвратный шестигранник гаечным ключом SW 24 по часовой стрелке настолько, чтобы свинтить регулятор до упора.
При необходимости тормозные накладки снять.
Контактную поверхность кронштейна смазать смазкой STABURAGS NBU 30 РТМ. Контактная поверхность тележки должна быть обезжирена и не окрашена.
Блок клещевого механизма поднять в поворотную тележку и монтировать с использованием крепежных элементов. При подъеме и установке использовать подъемные механизмы, грузоподъемность которых рассчитана на вес устройства. Крепится блок клещевого механизма на тележке с помощью 4 винтов М20 с моментом затяжки 450 Н м. С целью сохранения силы начальной затяжки у болтов с эффективной длиной растяжения менее 100 мм рекомендуется использовать на каждом болте по две одинаково уложенные зажимные шайбы. При монтаже устройства его необходимо удерживать вильчатым ключом.
Монтировать и подсоединить тросовую тягу устройства дистанционного управления для запасного устройства отпуска.
Вставить тормозные накладки в направляющую держателя накладки типа «ласточкин хвост» и зафиксировать, закрыв фиксирующую задвижку.
Снять крышки с патрубков подключения сжатого воздуха блока клещевого механизма и пневматических магистралей со стороны подвижного состава. Тщательно очистить патрубки.
Установить присоединительные патрубки в патрубок цилиндра служебного тормоза и в патрубок цилиндра тормоза с пружинным аккумулятором клещевого механизма. Нанести на резьбу штуцеров пневматических магистралей подвижного состава тонкий слой средства STABURAGS NBU 30 РТМ. Ввинтить пневматические магистрали в присоединительные патрубки.
Проверить исправность работы, наличие установленного зазора между накладкой и диском, герметичность после монтажа.
Санитарный комплекс
Произвести работы в объеме технического обслуживания 14 и произвести замену узла смыва (не реже, чем через каждые 4 года).
Токоприемник
Произвести проверку функционирования токоприемника с пульта машиниста:
Убедиться визуально в том, что токоприемник находится в сложенном положении.
Ограничить подъем полоза токоприемника на максимальной рабочей высоте (2100 мм от сложенного положения).
На пульте управления переключатель «Токоприемник» установить в положение «Поднят».
Включить секундомер одновременно с началом подъема токоприемника и выключить при касании полоза токоприемника ограничителя (определяется визуально). Время подъема токоприемника от 6 до 10 с.
В случае увеличения времени подъема токоприемника более 10 с или уменьшения времени подъема менее 6 с отрегулировать время подъема, поворачивая регулировочную головку клапана против или по часовой стрелке.
На пульте управления переключатель «Токоприемник» установить в положение «Опущен».
Включить секундомер одновременно с началом опускания токоприемника и выключить при возвращении токоприемника в сложенное положение (определяется визуально). Время опускания от 4 до 6 с.
Операции с 12.4.1.3 по 12.4.1.7 повторить дважды.
Проверить величину наименьшего активного и наибольшего пассивного нажатия и, при необходимости, отрегулировать.
Подъем токоприемника ограничить упором на высоте (1000±50) мм относительно поверхности вставок полностью опущенного токоприемника. В пневморессору подать номинальное давление (0,5 МПа). Токоприемник должен подняться до упора. К штанге в сборе прикрепить динамометр так, чтобы его вес не влиял на показания. Установить активное контактное нажатие в районе упора 90 Н с помощью регулировочного клапана, поворачивая регулировочную головку клапана против или по часовой стрелке. После регулировки нажатия регулировочную головку зафиксировать контргайкой, расположенной под регулировочной головкой.
Операции повторить с другим токоприемником.
Быстродействующий выключатель ВАБ-55
Произвести демонтаж с полюса выключателя дугогасительной камеры, не вынимая полюс из контейнера (рисунок 12.5.1):
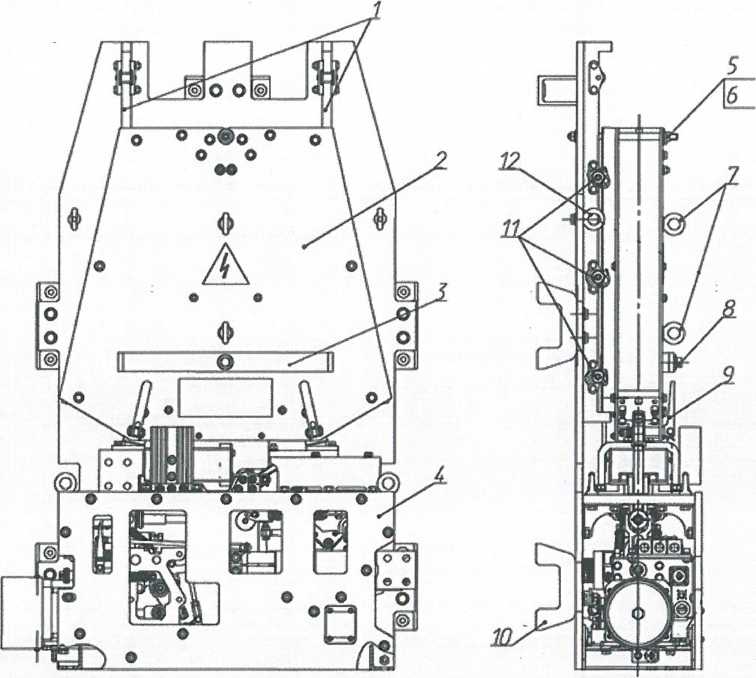
Рисунок 12.5.1 – Демонтаж дугогасительной камеры: 1 – направляющая; 2 – камера; 3 – брус; 4 – привод; 5 – шпилька; 6 – гайка; 7, 12 – рым-гайка; 8 – болт; 9 – рычаг; 10 – колодка; 11 – ролик
Снять экран (7) (рисунок 12.5.2), открутив винты (8), откинуть рычаг (9) (рисунок 12.5.1), открутить болт (8), снять прижимной брус (3), ослабить гайку (5) и откинуть шпильку (6).
Выдвинуть дугогасительную камеру (2) по направляющим (1), снять камеру, используя рым-гайки 7.
Удалить наплывы расплавленного металла с главных контактов выключателя, зачистить поверхности контактов напильником с мелкой насечкой. Площадь прилегания контактов должна быть не менее 30 %.
ВНИМАНИЕ! ЗАПРЕЩАЕТСЯ ЗАЧИСТКА КОНТАКТОВ НАЖДАЧНОЙ БУМАГОЙ.
При выгорании контактной накладки до величины менее 2 мм наконечники подвижного и неподвижного контактов заменить. При остаточной толщине накладок до 4 мм допускается дальнейшая эксплуатация.
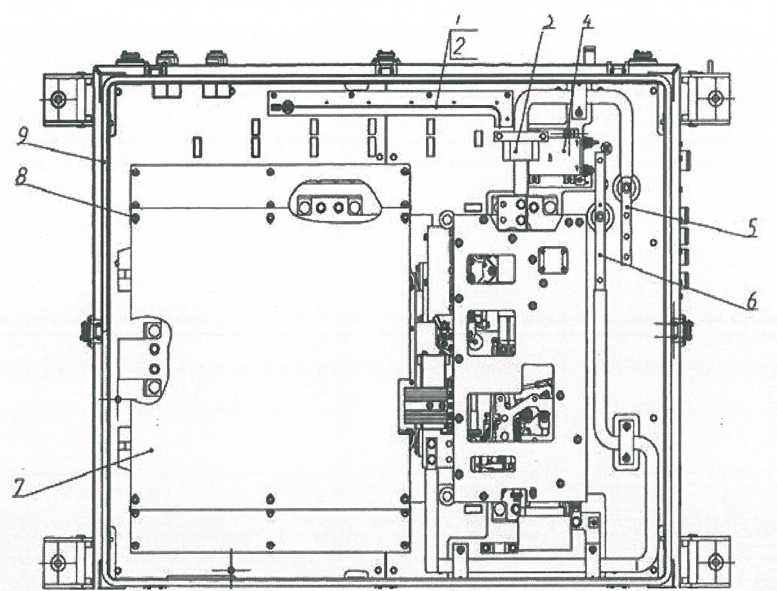
Рисунок 12.5.2 – Устройство выключателя (крышка снята): 1 – извещатель линейный тепловой пожарный; 2 – терминатор; 3 – датчик тока; 4 – датчик напряжения; 5, 6 – шины; 7 – экран; 8 – болт; 9 – уплотнение
Замену наконечников произвести без разборки выключателя:
Замена наконечника (3) неподвижного контакта (рисунок 12.5.3):
- открутить винты (6), гайку (5), болт (7), снять рог (2) и наконечник (3);
- собрать неподвижный контакт в обратной последовательности.
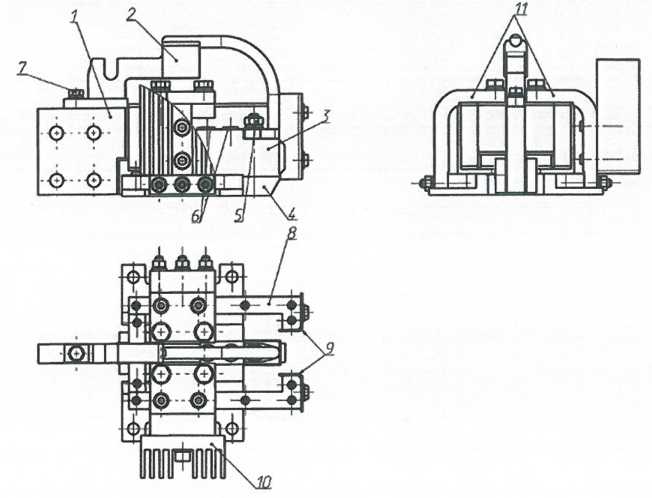
Рисунок 12.5.3 – Неподвижный контакт: 1, 11 – шины; 2 – рог; 3 – наконечник контактный; 4 – основание; 5 – гайка; 6 – винт; 7 – болт; 8 – магнитопровод; 9 – экран; 10 – радиатор
Замена контактного наконечника (1) подвижного контакта (рисунок 12.5.4):
- снять блок воздушного дутья (1), открутив гайки (18) (рисунок 12.5.5);
- открутить гайки (20), вынуть шпильки (21), снять скобы (2) (рисунок 12.5.4), снять наконечник (1);
- собрать подвижный контакт в обратной последовательности.
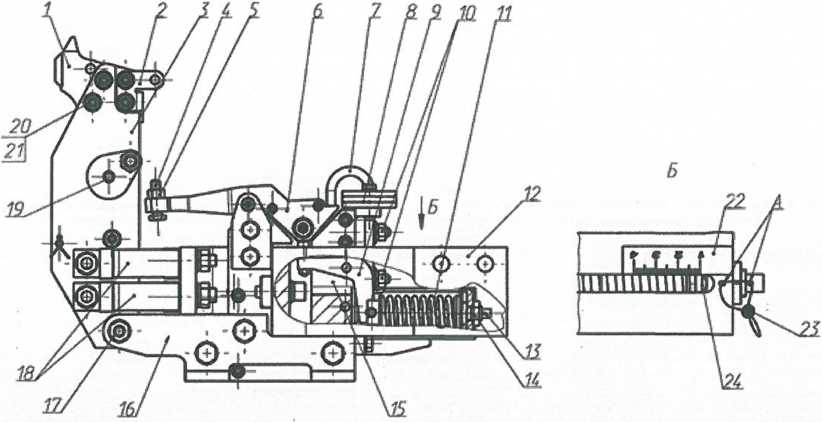
Рисунок 12.5.4 – Подвижный контакт: 1 – наконечник контактный; 2, 7 – скоба; 3 – контакт подвижный; 4 – болт; 5, 10, 14, 20 – гайка; 6 – якорь; 8 – кольцо; 9 – рычаг; 11 – пружина; 12 – шина; 13 – винт; 15 – магнитопровод; 16 – основание; 17 – ось; 18 – гибкие связи; 19 – ролик; 21 – шпилька; 22 – шкала; 23 – пломба; 24 – указатель
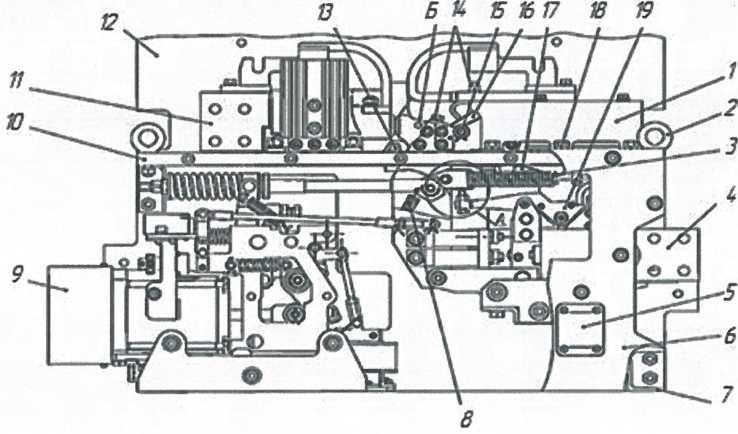
Рисунок 12.5.5 – Демонтаж блока воздушного дутья
Произвести очистку внутренних поверхностей перегородок (13, 14) дугогасительной камеры (рисунок 12.5.6) в зоне контактов от копоти и налета меди, после чего камеру продуть сухим сжатым воздухом.
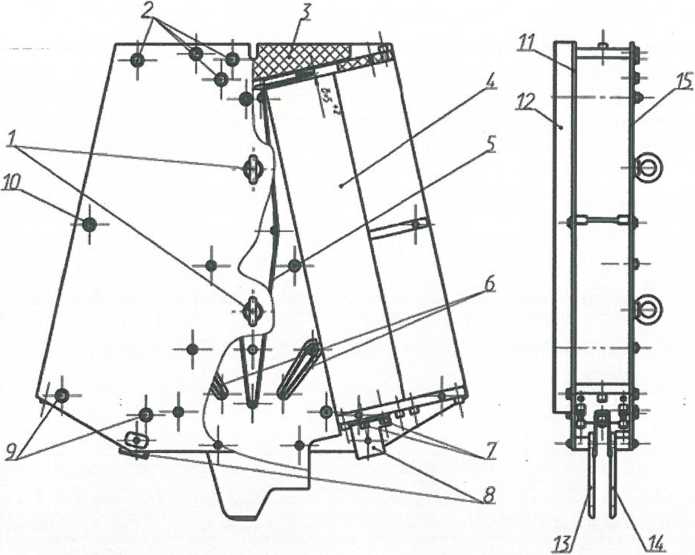
Рисунок 12.5.6 – Дугогасительная камера: 1 – рым-гайки; 2, 9, 10 – болты; 3, 12 – брус; 4 – блок дугогашения; 5, 6 – рога; 7 – винт; 8 – ламель; 11, 15 – щит; 13, 14 – перегородка
Произвести проверку блока воздушного дутья:
Снять блок воздушного дутья (1) (рисунок 12.5.5) и гибкую связь (15) (рисунок 12.5.7).
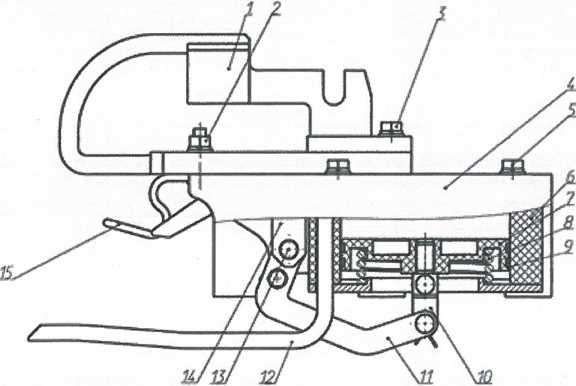
Рисунок 12.5.7 – Блок воздушного дутья: 1 – рог; 2, 3, 5 – болт; 4 – корпус; 6 – цилиндр; 7 – поршень; 8 – пружина; 9 – уплотнение; 10 – серьга; 11 – рычаг; 12 – трубка; 13 – ось; 14 – стойка; 15 – гибкая связь
Проверить легкость перемещения поршня (7). Сжать до упора пружину (8), повернуть рычаг (11) и резко отпустить.
При возвращении поршня назад заеданий не допускается.
Произвести смазку всех доступных осей вращения маслом МВП. Смазку нанести с помощью масленки по (1 – 2) капли в места контакта осей с поворотными узлами и деталями.
Сборку выключателя произвести в обратной последовательности.
Крышевое электрооборудование
Заземляющий разъединитель постоянного тока RM 0300.1000-585
На каждом втором техническом обслуживании 15 заземляющий разъединитель снять для проведения ревизии или заменить новым, или отремонтированным.
При установке разъединителя проверить монтажную опорную поверхность на крыше вагона, она должна быть ровная (неровности не более 0,6 мм) и чистая. Перед монтажом убедиться в наличии вклеенного уплотнительного кольца, расположенного на нижней кромке опорной плиты. Смазать 8 крепежных болтов М10 качества А4 универсальной смазкой Shell Alvania Grease. Момент затяжки 32 Н м. После затяжки на болты нанести маркировку. Контакты заземления закрепить болтами M12 с моментом затяжки 53 Н-м. После затяжки на болты нанести маркировку.
Подсоединить контактный вывод от контактного ножа к месту заземления с помощью медного провода повышенной гибкости. На местах контакта для этого предусмотрены сквозные отверстия для болтов M12. Момент затяжки 53 Н м. После затяжки на болты нанести маркировку.
Проверить рычаг управления на предмет свободного хода.
Установить штекер фирмы «Harting», у штекера имеется код для того, чтобы исключить неправильный монтаж. Штекерную часть фиксировать обеими крепежными болтами в гнезде. Штекер и гнездо должны быть чистыми и свободными от инородных тел.
Контактный нож должен полностью и без большого сопротивления входить в контактную петлю. Должна обеспечиваться возможность блокировки положения «рабочее» синим ключом «А», возможность блокировки положения «заземлено» красным ключом «В». В положении «рабочее» рычаг управления должен быть заблокирован. Оба конечных положения должны правильно квитироваться.
Разъединитель 25 кВ
Провести полную очистку разъединителя, неисправные детали заменить.
Главный выключатель М4А10ЕВВВ02
Проверить показания счетчика циклов, если он показывает более 200 000, заменить комплект конденсаторов.
Измерить величину хода главных контактов.
Переключатель RS
Выполнить работы в объеме технического обслуживания (инспекции I1). Проверить функционирование всех частей:
- плавное передвижение подвижного ножа, его приводную систему;
- для электрического привода – проверить изменения скорости и шума во время вхождения или выхода из контакта, для пневматического привода – при опорожненной пневматической сети вручную передвинуть подвижный нож в/из контакта. Заедания не допускаются;
- проверить переключение пневматического клапана.
Быстродействующий выключатель UR26-64T
Выполнить работы в объеме технического обслуживания инспекции 13.
Пневматическое и тормозное оборудование
Кран машиниста 345 с дистанционным управлением
Произвести демонтаж всего навесного оборудования крана машиниста 345 (рисунок 12.7.1.1), продуть сжатым воздухом пневматические каналы кронштейн-плиты (1), все сетчатые фильтры.
При наличии повреждений сетчатые фильтры заменить.
Произвести замену всех резиновых уплотнительных изделий, вулканизированных клапанов в соответствии с таблицей 12.7.1.1, но не реже одного раза каждые 4 года.
Назначенный срок службы резиновых уплотнительных изделий составляет четыре года, не считая 12 месяцев от даты изготовления, указанной на резиновом уплотнительном изделии или паспорте на партию изделий.
Установка резиновых уплотнительных изделий, имеющих надрывы и трещины, а также с истекшим назначенным сроком службы недопустима.
Провести проверку всех пружин в соответствии с таблицей 12.7.1.2. Пружины необходимо заменить при:
- наличии отклонений от контрольных значений параметров;
- наличии любых внешних повреждений (изломов, трещин и т.д.).
Трущиеся и уплотняемые поверхности деталей и узлов «металл-металл», «металл-резина», резьбовые разборные соединения при ремонте и сборке необходимо смазать смазкой ЖТ-79Л ТУ 0254-002-01055954.
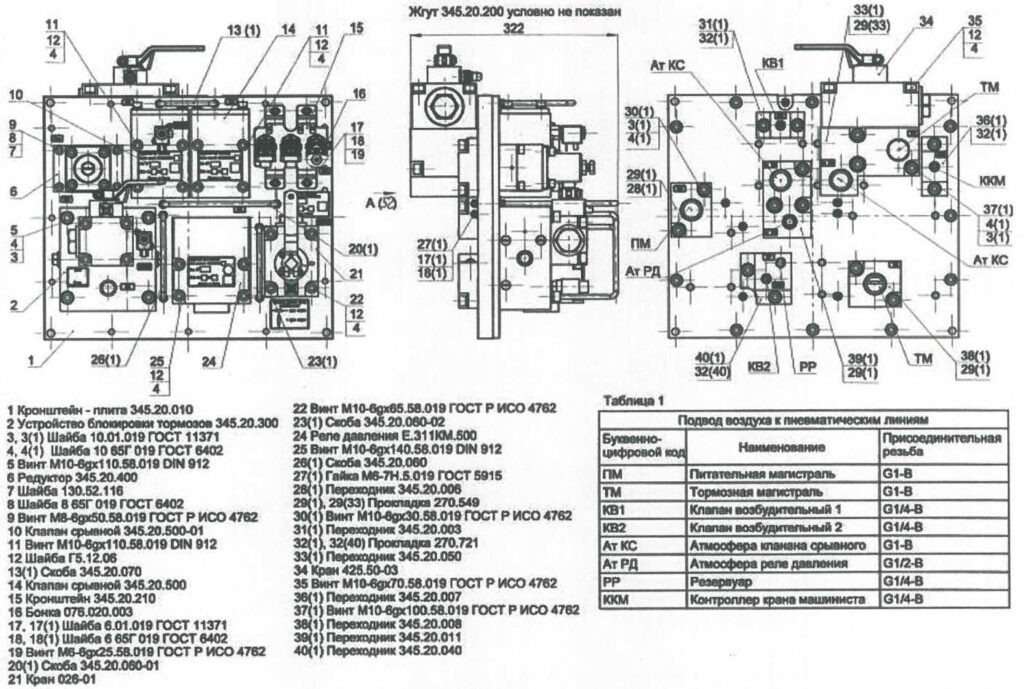
Рисунок 12.7.1.1 – Блок исполнительный 345.20
Таблица 12.7.1.1 – Замена уплотнительных резиновых изделий и вулканизированных клапанов крана машиниста 345
местоположение | наименование | обозначение | кол-во на изделие | примечание | |
рисунок | позиция | ||||
Модуль пневматический 345.10.100 | |||||
12.7.3 | 27 | Манжета воздухораспределителя | 305.156 | 3 | |
28 | Кольцо ГОСТ 9833 | 028-032-25-2-3 | 2 | ||
29 | Уплотнение | 270.711 | 6 | ||
31 | Кольцо ГОСТ 9833 | 032-036-25-2-3 | 1 | ||
37 | Клапан | 025М.030 | 2 | Неразборное соединение | |
41 | Кольцо ГОСТ 9833 | 024-028-25-2-3 | 1 | ||
42 | Манжета крана машиниста | 222.11 | 1 | ||
48 | Кольцо ГОСТ 9833 | 014-018-25-2-3 | 2 | ||
Блок исполнительный 345.20 | |||||
12.7.1 | 29 | Прокладка | 270.549 | 6 | |
32 | Прокладка | 270.721 | 3 | ||
Устройство блокировки тормозов 345.20.300 | |||||
12.7.4 | 2 | Прокладка | 270.549 | 4 | |
13 | Прокладка | 404.007 | 2 | ||
16 | Манжета | 270.769 | 2 | ||
18 | Кольцо ГОСТ 9833 | 014-018-25-2-3 | 2 | ||
19 | Кольцо ГОСТ 9833 | 024-028-25-2-3 | 2 | ||
21 | Кольцо ГОСТ 9833 | 030-034-25-2-3 | 2 | ||
25 | Манжета | 270.313 | 2 | ||
27 | Кольцо ГОСТ 9833 | 010-014-25-2-3 | 2 | ||
30 | Кольцо ГОСТ 9833 | 025-029-25-2-3 | 2 | ||
31 | Прокладка | 305.155 | 2 | ||
Редуктор 345.20.400 | |||||
12.7.5 | 12 | Диафрагма | 498.072 | 1 | |
17 | Прокладка | 348.216 | 2 | ||
20 | Кольцо ГОСТ 9833 | 028-033-30-2-3 | 1 | ||
Клапан срывной 345.20.500 | |||||
12.7.6 | 6 | Прокладка | 270.549 | 2 | |
8 | Поршень-гнездо (резина группы 3 (7-7130) ТУ 2539-054-05766882) | 345.20.530 (вулканизированный поршень-гнездо) | 1 | Неразборное соединение | |
10 | Манжета воздухораспределителя | 270.317 | 1 | ||
11 | Прокладка | 348.216 | 1 | ||
12 | Кольцо ГОСТ 9833 | 055-060-30-2-3 | 1 | ||
Клапан срывной 345.20.500-01 | |||||
12.7.7 | 8 | Прокладка | 270.549 | 2 | |
10 | Поршень-гнездо (резина группы 3(7-7130) ТУ 2539-054-05766882) | 345.20.530-01 (вулканизированный поршень-гнездо) | 1 | Неразборное соединение | |
12 | Манжета воздухораспределителя | 270.317 | 1 | ||
13 | Кольцо ГОСТ 9833 | 055-060-30-2-3 | 1 | ||
Резервуар 345.30 | |||||
12.7.8 | 6 | Кольцо ГОСТ 9833 | 018-023-30-2-3 | 1 | |
Реле давления Е.311КМ.500 | |||||
12.7.9 | 7 | Кольцо ГОСТ 9833 | 006-010-25-2-3 | 1 | |
8 | Прокладка | 270.721 | 1 | ||
10 | Кольцо ГОСТ 9833 | 021-025-25-2-3 | 1 | ||
11 | Кольцо ГОСТ 9833 | 106-112-36-2-3 | 1 | ||
14, 27 | Манжета крана машиниста | 222.11 | 2 | ||
17 | Кольцо ГОСТ 9833 | 018-023-30-2-3 | 1 | ||
19 | Манжета | 292М.202 | 1 | ||
22 | Клапан (резина группы 3 ТУ 2539-054-05766882) | 076М.080.040-1 (вулканизированный клапан) | 1 | Неразборное соединение | |
23 | Кольцо ГОСТ 9833 | 026-030-25-2-3 | 1 | ||
28 | Прокладка | 305.155 | 1 | ||
30 | Прокладка | 348.216 | 1 |
Таблица 12.7.1.2 – Контрольные значения параметров пружин крана машиниста 345
местоположение | обозначение | контрольные значения параметров * | |
рисунок | позиция | ||
Модуль пневматический 345.10.100 | |||
12.7.3 | 40 | 337.370 | P1 = 3±0,3 кгс; H1 = 14 мм Р2 = 5,2 ± 0,5 кгс; Н2 = 10 мм |
54 | 150.203-1 | F1 = 34 ± 3,4 Н (3,48 ± 0,18 кгс); L1 = 14,5 мм F2 = 51 ± 5,1 Н (5,24 ± 0,524 кгс); L2 = 13 мм |
|
Устройство блокировки тормозов 345.20.300 | |||
12.7.4 | 29 | 270.774-1 | F1 = 51 ± 5,1 Н (5,24 ± 0,524 кгс); L1 = 18 мм F2 = 59 ± 5,9 Н (6,045 ± 0,604 кгс); L2 = 16 мм |
Редуктор р 345.20.400 | |||
12.7.5 | 9 | 75М.05.124-1 | F1 = 589,06 ± 58,51 Н (59,7 ± 5,97 кгс); L1 = 45 мм F2 = 664,1 ± 66,3 Н (67,7 ± 6,77 кгс); L2 = 43 мм |
19 | 260.123 | P1 = 1,76 ± 0,18 кгс; H1 = 22 мм P2 = 3,96 ± 0,4 кгс; Н2 = 17 мм | |
Клапан срывной 345.20.500, 345.20.500-01 | |||
12.7.6, 12.7.7 | 9,11 | 130.10.092-1 | F1 = 42 ± 4,2 Н (4,27 ± 0,42 кгс); L1 = 35 мм F2 = 80 ± 8,0 Н (8,2 ± 0,82 кгс); L2 = 25 мм |
Реле давления Е.311КМ.500 | |||
12.7.9 | 24 | 404.033-1 | P1 = 8,08 ± 0,8 кгс; H1 = 14 мм Р2 = 12,12 ± 1,21 кгс; Н2 = 10 мм |
Примечание – * проверка контрольных параметров пружин выполняется при помощи машины для испытания пружин и штангенциркуля.
Контроллер 345.10
Демонтировать контроллер из пульта машиниста, предварительно отсоединив электрические соединения. Ремонт допускается производить без демонтажа кронштейна (поз. 4, рисунок 12.7.1.2). Для этого необходимо отвернуть шесть винтов (поз. 2, рисунок 12.7.1.2) и извлечь контроллер из пульта.
Разобрать контроллер 345.10.
Освободить модуль пневматический (3) от навесных и декоративных элементов:
- рукой отвернуть колпачок (9), снять втулку (10);
- отвернуть четыре винта (12), снять фальш-панель (11);
- отвернуть четыре винта (5) с шайбами (6 и 7), снять блок микровыключателей (1).
Разобрать модуль пневматический (рисунок 12.7.1.3):
- извлечь из корпуса (3) шесть уплотнений (29);
- отвернуть дроссель (49), извлечь уплотнительное кольцо (48);
- прочистить (прокалибровать), при необходимости, дроссель(49);
- отвернуть винт (7) с шайбами (8 и 9), снять кулачок (10);
- отвернуть две заглушки (53), извлечь пружины (54);
- отвернуть гайку (33) с шайбами (34 и 35), демонтировать барабан (13) в сборе с ручкой (14) и табличкой (12);
- отвернуть четыре винта (1) с одной стороны контроллера, снять крышку (2), затем с другой стороны контроллера отвернуть еще четыре винта (1) и снять крышку (32);
- извлечь втулку (19), снять с нее уплотнительное кольцо (31(19)) и извлечь манжету воздухораспределителя (27(22));
- извлечь ось (25) вместе с втулкой (21);
- отвернуть винт (1), снять эксцентрик (38) и втулку (21);
- снять с втулки (21) уплотнительные кольца (28(21) и 31(21)) и извлечь две манжеты воздухораспределителя (27(21));
- отвернуть винт (4) с шайбами (5 и 6), снять эксцентрик (45);
- отвернуть 16 винтов (четыре по четыре) (4) с шайбами (5 и 6), извлечь крышку (43), втулку (44), крышку (46), две крышки (36), четыре пружины (40), четыре клапана (37);
- снять с крышки (43) уплотнительное кольцо (41(43));
- снять с втулки (44) уплотнительное кольцо (41(44)), извлечь манжету крана машиниста (42(44));
- снять с крышки (46) уплотнительное кольцо (41(46)), извлечь уплотнительное кольцо (48(46));
- снять с двух крышек (36) уплотнительные кольца (41(36)), извлечь манжеты крана машиниста (42(36));
- провести замену резиновых уплотнительных изделий в соответствии с таблицей 12.7.1.1;
- осмотреть, проверить и заменить, при необходимости, пружины в соответствии с таблицей 12.7.1.2;
- собрать контроллер в порядке, обратном разборке. В процессе сборки трущиеся и уплотняемые поверхности деталей и узлов «металл-металл», «металл-резина», резьбовые разборные соединения смазать смазкой ЖТ-79Л ТУ 0254-002-01055954;
- уплотнения (29) рекомендуется устанавливать на клей 88-СА ТУ 38.105.1760.

Рисунок 12.7.1.2 – Контроллер 345.10
Блок микровыключателей (поз. 1, рисунок 12.7.1.2) является неремонтопригодным в условиях моторвагонных (локомотивных) депо и заменяется узлом в сборе.
Разобрать блок исполнительный 345.20 (рисунок 12.7.1.1):
- вывернуть винты (5), снять шайбы (3 и 4) и демонтировать устройство блокировки тормозов 345.20.300 (2);
- вывернуть винты (9), снять шайбы (7 и 8) и демонтировать редуктор 345.20.400 (6);
- вывернуть винты (11), снять шайбы (4 и 12) и демонтировать клапан срывной 345.20.500 (14) и клапан 345.20.500-01 (10);
- вывернуть винты (22), снять шайбы (4 и 12) и демонтировать кран 026-01 (21);
- вывернуть винты (25), снять шайбы (4 и 12) и демонтировать реле давления Е.311КМ.500 (24);
- вывернуть винты (35), снять шайбы (4 и 12) и демонтировать кран 425.50-03 (34);
- вывернуть винты (30(1)), снять шайбы (3(1) и 4(1)), демонтировать переходник (28(1)), извлечь прокладку (29(1));
- вывернуть винты (30(1)), снять шайбы (3(1) и 4(1)), демонтировать переходник (31(1)), извлечь прокладку (32(1));
- вывернуть винты (37(1)), снять шайбы (3(1) и 4(1)), демонтировать переходник (33(1)), извлечь прокладку (29(33);
- вывернуть винты (30(1)), снять шайбы (3(1) и 4(1)), демонтировать переходник (36(1)), извлечь прокладку (29(1));
- вывернуть винты (30(1)), снять шайбы (3(1) и 4(1)), демонтировать переходник (38(1)), извлечь прокладку (29(1));
- вывернуть винты (30(1)), снять шайбы (3(1) и 4(1)), демонтировать переходник (39(1)), извлечь прокладку (29(1));
- вывернуть винты (30(1)), снять шайбы (3(1) и 4(1)), демонтировать переходник (40(1)), извлечь прокладку (32(40)).
Проверить состояние резиновых уплотнительных изделий в соответствии с таблицей 12.7.1.1.
Произвести очистку сетчатых фильтров, при наличии повреждений сетчатые фильтры заменить.
Собрать блок исполнительный 345.20 в порядке, обратном разборке. В процессе сборки трущиеся и уплотняемые поверхности деталей и узлов «металл-металл», «металл-резина», резьбовые разборные соединения смазать смазкой ЖТ-79Л ТУ 0254-002-01055954.
Разобрать устройство блокировки тормозов 345.20.300 (рисунок 12.7.1.4):
- вывернуть винты (6), снять шайбы (4, 5), демонтировать кран 043-1 (9);
- открутить винт (10) и демонтировать распределитель (7);
- вывернуть датчик давления (3);
- вывернуть заглушку (28), извлечь прокладку (31), кольцо (30), пружину (29), клапан (11);
- вывернуть направляющую (15(11)), извлечь шайбу (14(11)), прокладку (13(H));
- вывернуть заглушку (22), извлечь кольцо (21), поршень (23), манжету (25(23)), втулку (17), манжету (16(17)), кольца (18(17)) и (9(17)).
Открутить заглушку (26(1)), извлечь кольцо (27(1)).
Проверить состояние резиновых уплотнительных изделий в соответствии с таблицей 12.7.1.1, проверить пружины в соответствии с таблицей 12.7.1.2.
Собрать устройство блокировки тормозов 345.20.300 в порядке, обратном разборке. В процессе сборки трущиеся и уплотняемые поверхности деталей и узлов «металл-металл», «металл-резина», резьбовые разборные соединения смазать смазкой ЖТ-79Л ТУ 0254-002-01055954.
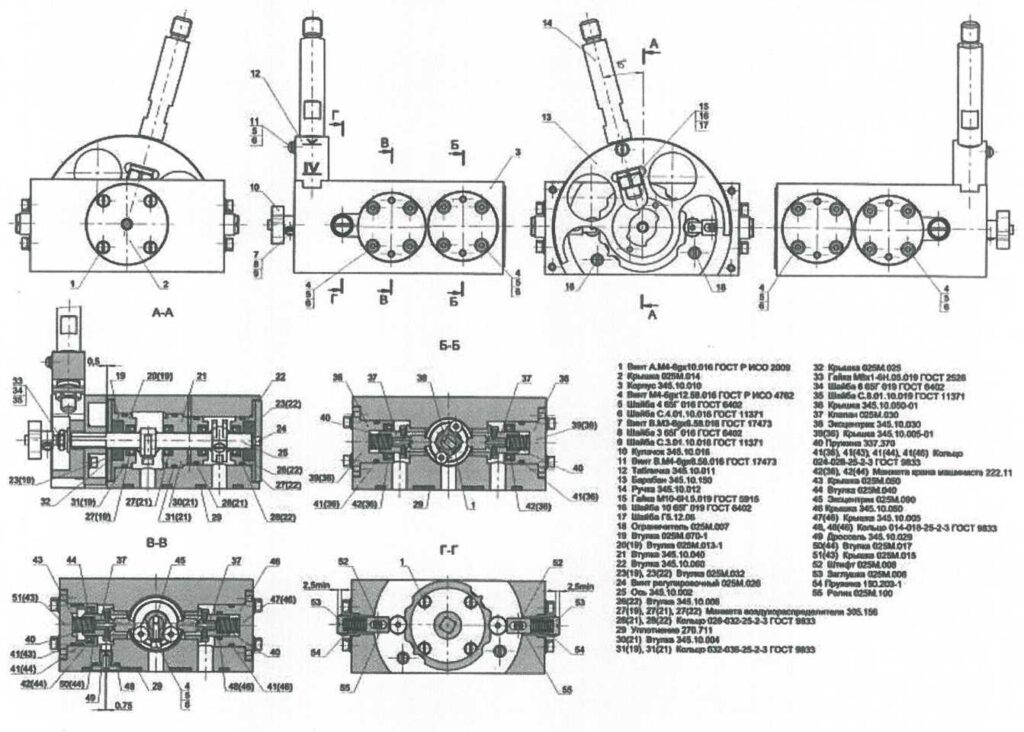
Рисунок 12.7.1.3 – Модуль пневматический 345.10.100
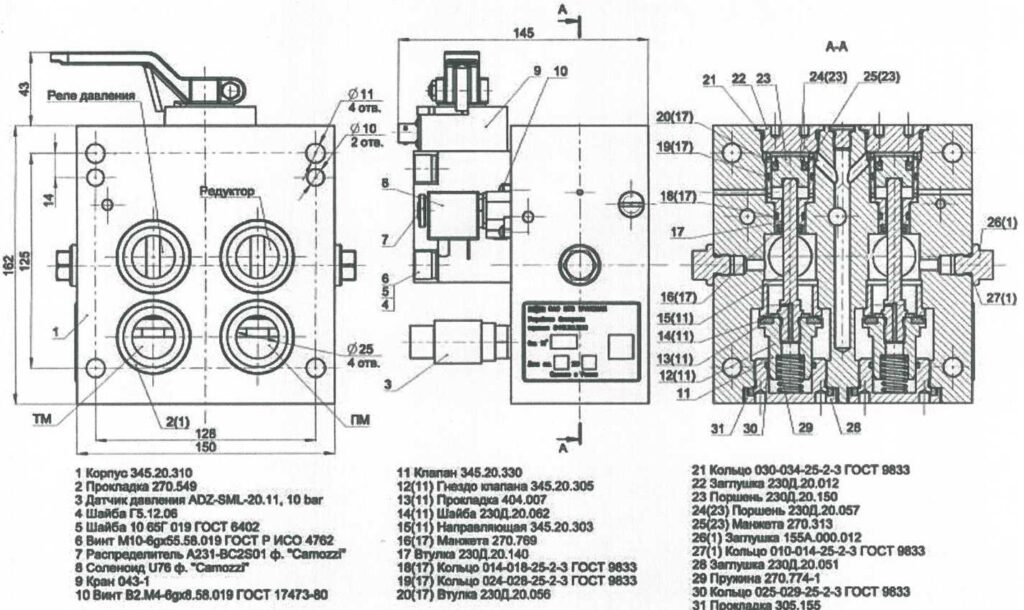
Рисунок 12.7.1.4 – Устройство блокировки тормозов 345.20.300
Разобрать редуктор 345.20.400 (рисунок 12.7.1.5):
- ослабить гайку (6), вывернуть регулировочный винт (7) и открутить гайку (6);
- вывернуть винты (5), снять шайбы (3 и 4) и демонтировать крышку (2);
- извлечь упорку (8), пружину (9) и диафрагму (10);
- отвернуть гайку (14(10)), демонтировать шайбы (13(10) и 11(10), диафрагму (12(10)) с толкателя (15(10));
- вывернуть винты (21), извлечь крышку (18), кольцо (20), пружину (19) и клапан (16) из корпуса (1);
- извлечь прокладки (17(1)) из корпуса (1).
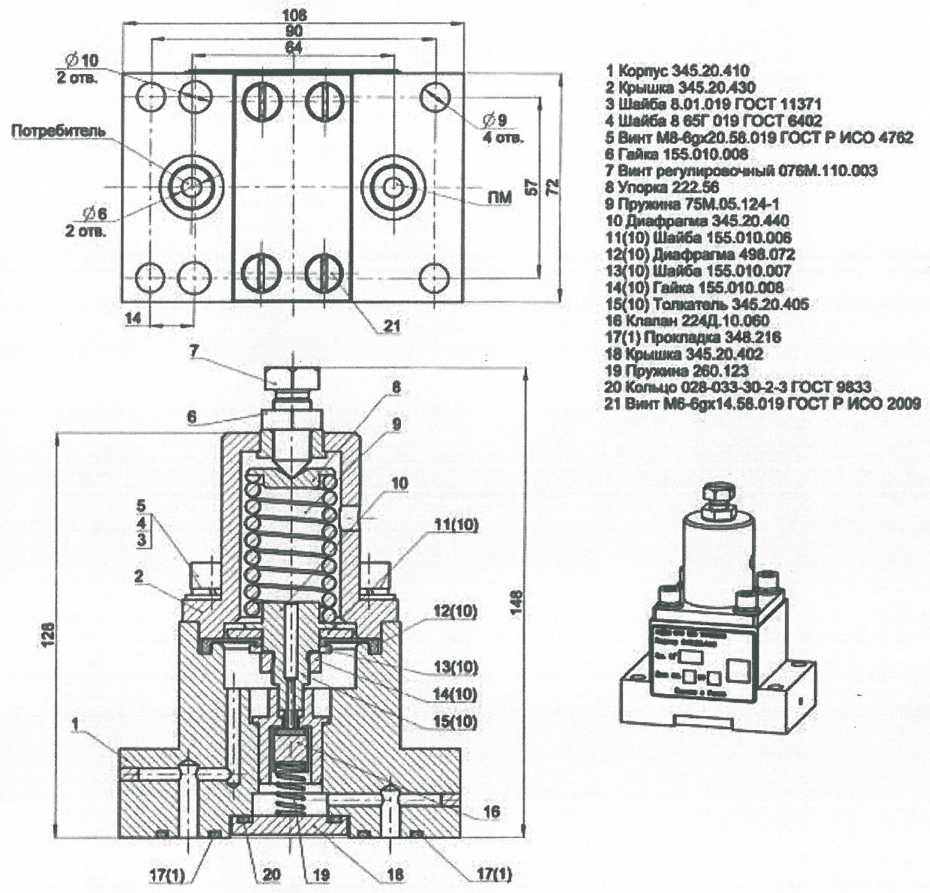
Рисунок 12.7.1.5 – Редуктор 345.20.400
Провести замену резиновых уплотнительных изделий в соответствии с таблицей 12.7.1.1, осмотреть, проверить и заменить, при необходимости, пружины в соответствии с таблицей 12.7.1.2.
Собрать редуктор 345.20.400 в порядке, обратном разборке. В процессе сборки трущиеся и уплотняемые поверхности деталей и узлов «металл-металл», «металл-резина», резьбовые разборные соединения смазать смазкой ЖТ-79Л ТУ 0254-002-01055954.
Разобрать клапан срывной 345.20.500 (рисунок 12.7.1.6):
- вывернуть винты (5), снять шайбы (3 и 4) и демонтировать крышку (2) из корпуса (1);
- демонтировать кольцо (12) из крышки (2);
- извлечь пружину (9) и поршень-гнездо (7);
- демонтировать манжету (10(7)) с поршня гнезда (8(7));
- извлечь прокладки (6 и 11) из корпуса (1).

Рисунок 12.7.1.6 – Клапан срывной 345.20.500
Проверить состояние резиновых уплотнительных изделий и вулканизированного поршня-гнезда (10) в соответствии с таблицей 12.7.1.1, проверить пружины в соответствии с таблицей 12.7.1.2.
Собрать клапан срывной 345.20.500 в порядке, обратном разборке.
В процессе сборки трущиеся и уплотняемые поверхности деталей и узлов «металл-металл», «металл-резина», резьбовые разборные соединения смазать смазкой ЖТ-79Л ТУ 0254-002-01055954.
Разобрать клапан срывной 345.20.500-01 (рисунок 12.7.1.7):
- вывернуть винты (5), снять шайбы (3 и 4) и демонтировать крышку (2) из корпуса (1);
- демонтировать кольцо (13) из крышки (2);
- извлечь пружину (11) и поршень-гнездо (9);
- демонтировать манжету (12(9)) с поршня-гнезда (10(9));
- извлечь прокладки (8) из корпуса (1);
- открутить винт (6) и демонтировать распределитель (7).
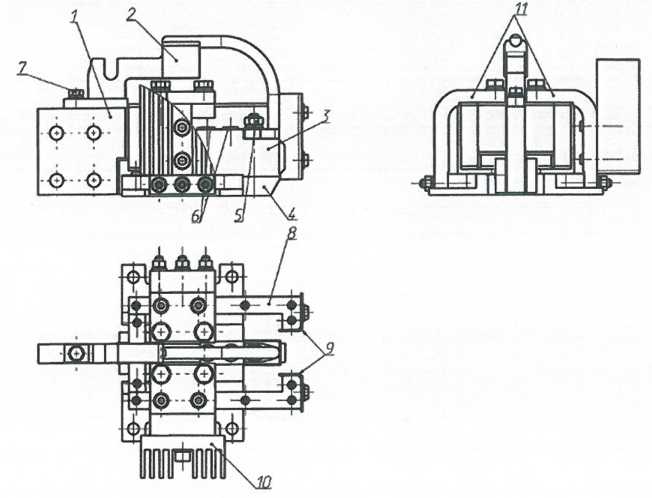
Рисунок 12.7.1.7 – Клапан срывной 345.20.500-01
Проверить состояние резиновых уплотнительных изделий и вулканизированного поршня-гнезда (8) в соответствии с таблицей 12.7.1.1, проверить пружины в соответствии с таблицей 12.7.1.2.
Собрать клапан срывной 345.20.500-01 в порядке, обратном разборке.
В процессе сборки трущиеся и уплотняемые поверхности деталей и узлов «металл-металл», «металл-резина», резьбовые разборные соединения смазать смазкой ЖТ-79Л ТУ 0254-002-01055954.
Разобрать резервуар 345.30 (рисунок 12.7.1.8):
- открутить розетку (42);
- вывернуть переходник с датчиком (2), извлечь кольцо (6(2));
- вывернуть датчик давления (5(2)).
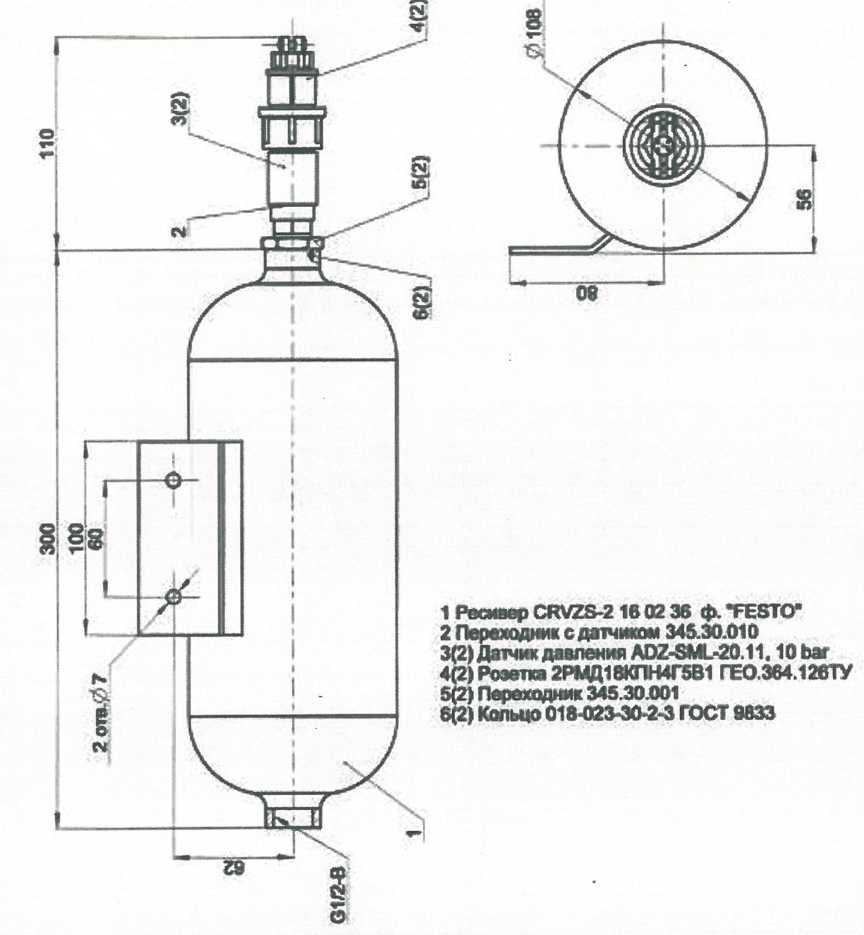
Рисунок 12.7.1.8 – Резервуар 345.30
Проверить состояние резиновых уплотнительных изделий в соответствии с таблицей 12.7.1.1.
Собрать резервуар 345.30 в порядке, обратном разборке.
В процессе сборки трущиеся и уплотняемые поверхности деталей и узлов «металл-металл», «металл-резина», резьбовые разборные соединения смазать смазкой ЖТ-79Л ТУ 0254-002-01055954.
Разобрать реле давления Е.311КМ.500 (рисунок 12.7.1.9):
- извлечь прокладку (8), кольцо (10);
- отвернуть четыре винта (3), извлечь шайбы (4 и 5);
- демонтировать крышку (12) и извлечь из нее манжету (14);
- извлечь из корпуса (1) кольцо (11), поршень (18), отвернуть гайку (15), извлечь шайбу (16), шток (21), кольцо (17), манжету (19);
- извлечь из корпуса (1) стопорное кольцо (9), фильтр (29), очистить фильтр, при наличии повреждений заменить фильтр (29);
- отвернуть заглушку (26) и извлечь из корпуса (1) клапан (22), пружину (24), кольцо (23), шайбу (25), манжету крана машиниста (14).
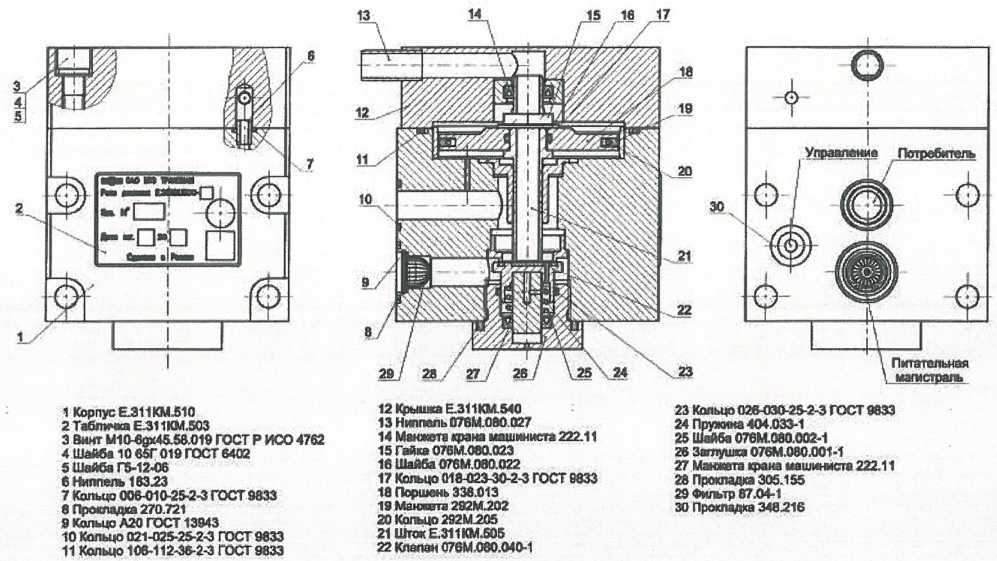
Рисунок 12.7.1.9 – Реле давления Е.311КМ.500
Очистить и продуть каналы корпуса (1).
Прочистить калиброванное отверстие диаметром 2 мм в корпусе (1). Запрещается производить какие-либо изменения данного отверстия.
Проверить состояние резиновых уплотнительных изделий и вулканизированных клапанов (22) в соответствии с таблицей 12.7.1.1. Клапан (22) не подлежит разборке и заменяется целиком при повреждении уплотнений.
Проверить пружины в соответствии с таблицей 12.7.1.2.
Собрать реле давления Е.311КМ.500 в порядке, обратном разборке. В процессе сборки трущиеся и уплотняемые поверхности деталей и узлов «металл-металл», «металл-резина», резьбовые разборные соединения смазать смазкой ЖТ-79Л ТУ 0254-002-01055954.
При монтаже крана машиниста 345 на электропоезд моменты затяжек резьбовых соединений должны соответствовать данным, приведенным в таблице Д.1 приложения Д.
После проведения ремонта произвести проверку крана машиниста 345 на соответствие характеристикам, указанным в таблице 12.7.1.3.
Таблица 12.7.1.3 – Характеристики крана машиниста 345 при стендовых испытаниях
№ п/п | Наименование характеристики | Значение |
1 | Давление сжатого воздуха в тормозной магистрали (ТМ) в положении «ПОЕЗДНОЕ» крана машиниста (зарядное давление), МПа | 0,50±0,01 |
2 | Автоматическое поддержание установившегося зарядного давления (0,50±0,01) МПа в ТМ при создании искусственной утечки, МПа, не более | ±0,015 |
3 | Изменение в течении 180 с установившегося давления в ТМ в положении «ПЕРЕКРЫША С ПИТАНИЕМ» после ступени торможения, МПа, не более | ±0,01 |
4 | Время снижения давления в ТМ при служебном торможении от 0,49 МПа до 0,39 МПа, с | 4-5 |
5 | Время снижения давления в ТМ при экстренном торможении от 0,49 МПа до 0,15 МПа, с, не более | 3 |
6 | Время снижения давления в ТМ при снятии напряжения с ЭПВН2 с 0,49 до 0,15 МПа, с, не более | 3 |
7 | Включение и отключение блокировки тормозов | Имеется |
8 | Герметичность мест соединения узлов и деталей | Пропуск воздуха не допускается |
9 | Работоспособность функции диагностики блокировки тормозов и крана трехходового КрРШ2 | Имеется |
10 | Замыкание микропереключателей контроллера в положении «ЭКСТРЕННОЕ ТОРМОЖЕНИЕ» | Имеется |
Блоки тормозного оборудования 420, 420-01, 420-02 (БТО 420)
При ремонте БТО420 провести замену всех резиновых уплотнительных изделий в соответствии с таблицей 12.7.2.1.
Таблица 12.7.2.1 – Перечень резиновых уплотнительных изделий
Месторасположение | Наименование | Обозначение | Кол-во на изделие | Примечание | |
Рисунок | Позиция | ||||
Часть пневматическая 420.20 | |||||
12.7.2.2, 12.7.2.3, 12.7.2.4 | 30 | Кольцо ГОСТ 9833 | 006-010-25-2-3 | 1 | |
31 | Кольцо ГОСТ 9833 | 044-048-25-2-3 | 1 | ||
67 | Прокладка крышки | 86.13 | 2 | ||
70 | Прокладка | 270.721 | 11 | ||
77 | Прокладка | 348.216 | 8 | ||
84 | Прокладка | 270.549 | 7 | ||
Делитель давления 420.40 | |||||
12.7.2.5 | 9 | Диафрагма | 498.072 | 1 | |
11 | Диафрагма | 013.031 | 1 | ||
13 | Уплотнение | 211.020.012 | 1 | ||
14 | Уплотнение клапана | 270.357 | 4 | ||
16 | Кольцо ГОСТ 9833 | 028-033-30-2-3 | 1 | ||
18 | Клапан (резина группы 3 (7-7130) ТУ 2539-054-05766882 | 211.020.030 вулканизированный клапан | 1 | Неразборное соединение | |
Блок управления тормозом 420.50-1 | |||||
12.7.2.6 | 12 | Прокладка | 305.155 | 1 | |
13 | Прокладка | 270.721 | 1 | ||
16 | Кольцо ГОСТ 9833 | 021-025-25-2-3 | 1 | ||
17 | Кольцо ГОСТ 9833 | 106-112-36-2-3 | 1 | ||
18 | Манжета крана машиниста | 222.11 | 2 | ||
22 | Кольцо ГОСТ 9833 | 018-023-30-2-3 | 1 | ||
25 | Манжета | 292М.202 | 1 | ||
27 | Клапан (резина группы 3 (7-7130) ТУ 2539-054-05766882 | 076М.080.040-1 вулканизированный клапан | 1 | Неразборное соединение | |
29 | Кольцо ГОСТ 9833 | 026-030-25-2-3 | 1 | ||
31 | Прокладка | 348.216 | 2 | ||
44 | Кольцо ГОСТ 9833 | 020-024-25-2-3 | 1 | ||
45 | Кольцо ГОСТ 9833 | 006-010-25-2-3 | 3 | ||
46 | Манжета воздухораспределителя | 120-7-2 | 2 | ||
48 | Кольцо ГОСТ 9833 | 040-045-30-2-3 | 1 | ||
Ограничитель давления автоматического тормоза 420.70 -1 | |||||
12.7.2.7,
12.7.2.8 |
11 | Прокладка | 348.216 | 1 | |
19 | Кольцо ГОСТ 9833 | 006-010-25-2-3 | 5 | ||
24 | Кольцо ГОСТ 9833 | 022-026-25-2-3 | 1 | ||
28 | Манжета | 278.434 | 1 | ||
38 | Кольцо ГОСТ 9833 | 055-060-30-2-3 | 1 | ||
42 | Диафрагма | 418.002 | 1 | ||
46 | Манжета | 278.539 | 2 | ||
52 | Кольцо ГОСТ 9833 | 020-024-25-2-3 | 1 | ||
56 | Кольцо ГОСТ 9833 | 030-034-25-2-3 | 1 | ||
61 | Манжета | 420.70.014 | 1 | ||
Клапан минимального давления 420.80.200 | |||||
12.7.2.10 | 7 | Кольцо ГОСТ 9833 | 027-032-30-2-3 | 1 | |
9 | Кольцо ГОСТ 9833 | 027-032-30-2-3 | 1 | ||
10 | Кольцо ГОСТ 9833 | 021-025-25-2-3 | 1 | ||
11 | Клапан вулканизированный | 420.80.220 | 1 | Неразборное соединение | |
Клапан пропорционального управления 420.100 | |||||
12.7.2.11 | 2 | Клапан вулканизированный | 420.100.050 | 1 | Неразборное соединение |
7 | Кольцо ГОСТ 9833 | 032-036-25-2-3 | 1 | ||
10 | Уплотнение | 278.465-4 | 3 | ||
13 | Манжета | 278.376 | 1 | ||
16 | Кольцо ГОСТ 9833 | 045-050-30-2-3 | 1 | ||
23 | Манжета | 278.375 | 1 | ||
26 | Манжета | 420.100.018 | 1 | ||
Орган дополнительной разрядки 420.200 | |||||
12.7.2.12 | 3 | Кольцо ГОСТ 9833 | 021-025-25-2-3 | 1 | |
5 | Кольцо ГОСТ 9833 | 080-085-30-2-3 | 2 | ||
9 | Диафрагма | 013.031 | 1 | ||
12 | Клапан (резина группы 3 (7-7130) ТУ 2539-054-05766882 | вулканизированный клапан 003М.030-1 | 1 | Неразборное соединение | |
14 | Прокладка | 348.216 | 3 | ||
20 | Клапан (резина группы 3 (7-7130) ТУ 2539-054-05766882 | вулканизированный клапан 420.200.040 | 1 | Неразборное соединение | |
21 | Манжета воздухораспределителя | 305.156 | 1 |
При ремонте БТО провести проверку всех пружин в соответствии с таблицей 12.7.2.2. Пружины необходимо заменить при наличии отклонений от контрольных значений параметров, наличии любых внешних повреждений (изломов, трещин и т.д.).
Таблица 12.7.2.2 – Перечень пружин
Месторасположение | Обозначение | Средства измерений | Контрольные значения параметров | |
Рисунок | Позиция | |||
Делитель давления 420.40 | ||||
12.7.2.5 | 17 | 222.25 | Машина для испытания пружин, штангенциркуль | Р1=1,56 ± 0,15 кгс; H1=14 мм P2=3,12 ± 0,31 кгс; Н2=10 мм |
Блок управления тормозом 420.50-1 | ||||
12.7.2.6 | 28 | 404.033-1 | Машина для испытания пружин, штангенциркуль | P1=8,08 ± 0,8 кгс; H1=14 мм Р2=12,12 ± 1,21 кгс; Н2=10 мм |
Ограничитель давления автоматического тормоза 420.70-1 | ||||
12.7.2.8,
12.7.2.9 |
21 | 278А.647 | Машина для испытания пружин, штангенциркуль | Р1=2,02 ± 0,2 кгс; H1=21 мм Р2=3,54 ± 0,35 кгс; Н2=15 мм |
30 | 278А.648 | Машина для испытания пружин, штангенциркуль | P1=0,56 ± 0,8 кгс; H1=22 мм Р2=1,13 ± 1,21 кгс; Н2=18 мм |
|
35 | 278А.645 | Машина для испытания пружин (МИП), штангенциркуль | Р1=0,43 ± 0,04 кгс; H1=17 мм P2=0,61 ± 0,06 кгс; Н2=14 мм |
|
50 | 278А.646 | Машина для испытания пружин (МИП), штангенциркуль | Р1=4,92 ±0,5 кгс; H1=29 мм Р2=7,02 ± 0,7 кгс; H2=26 мм |
|
63 | 420.70.005-1 | Машина для испытания пружин (МИП), штангенциркуль | Р1=13,89 ±1,4 кгс; H1=50 мм Р2=29,32 ± 2,9 кгс; H2=45 мм |
|
63 | 420.70.006-1 | Машина для испытания пружин (МИП), штангенциркуль | Р1=7.43 ± 0,7 кгс; H1=50 мм Р2=15,69 ±1,6 кгс; Н2=45мм |
|
Клапан минимального давления 420.80.200 | ||||
12.7.2.10 | 14 | 270.371 | Машина для испытания пружин (МИП), штангенциркуль | Р1=12 ± 1,2 кгс; H1=50 мм Р2=15,69 ±1,6 кгс; Н2=45мм |
Клапан пропорционального управления 420.100 | ||||
12.7.2.11 | 3 | 420.100.028 | Машина для испытания пружин (МИП), штангенциркуль | F1=1,41 ± 1,1 кгс; L1=17 мм F2=l,6 ± 0,1 кгс; L2=15,5mm |
11 | 420.100.027 | Машина для испытания пружин (МИП), штангенциркуль | F1=0,68 ± 0,06 кгс; L1=23,5 мм F2=0,725 ± 0,07 кгс; L2=22 мм | |
Орган дополнительной разрядки 420.200 | ||||
12.7.2.12 | 13 | 135.01.10 | Машина для испытания пружин (МИП), штангенциркуль | Р1 = 0,84 ± 0,08 кгс; H1=13 мм Р2=1,4 ±0,14 кгс; Н2=11 мм |
После демонтажа всего навесного оборудования необходимо продуть сжатым воздухом пневматические каналы кронштейн-плиты 420.20.020.
Порядок текущего ремонта блока тормозного оборудования 420 (420-01; 420-02) (рисунок 12.7.2.1):
- открыть крышку кожуха (1);
- отвернуть винты (34), снять шайбы (8, 9), отвернуть все гайки заземления (25), снять шайбы (23, 24), с задней крышки отвернуть винты разъемов жгутов (37), далее демонтировать жгуты (31, 32, 35, 37);
- демонтировать фиксаторы (30), извлечь блоки (27, 28,29);
- отвернуть винты (26), снять шайбы (3,4), извлечь рейку (31);
- отвернуть винты (10) крепления блока «Барс-6М», снять винт (5) и шайбы (4, 3);
- извлечь электронный блок «Барс-6М» (2);
- отвернуть винты (10) крепления коробки коммутационной, снять шайбы (8, 9), демонтировать коробку коммутационную (7);
- отвернуть винты (10) крепления регистратора, снять шайбы (8, 9), демонтировать регистратор (11);
- отвернуть винты (10) крепления шлюза, снять шайбы (8, 9), демонтировать шлюз (12);
- отвернуть винты (10) крепления адаптера, снять шайбы (8, 9), демонтировать адаптер (13);
- отвернуть гайки (16) крепления части пневматической, снять шайбы (15, 14), извлечь часть пневматическую (17);
- отвернуть винт (34) крепления адаптера, снять шайбы (8, 9), демонтировать адаптер (35).
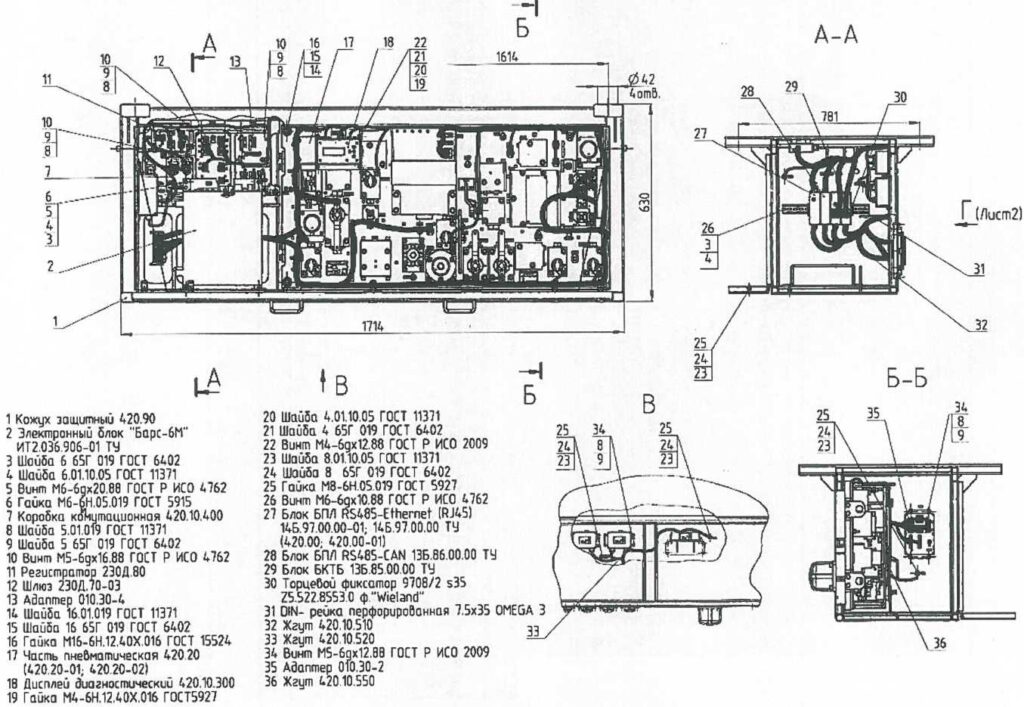
Рисунок 12.7.2.1 – Блок тормозного оборудования 420 (420-01, 420-02)
Часть пневматическая 420.20 (420.20-01, 420.20-02) (рисунки 12.7.2.2, 12.7.2.3, 12.7.2.4)
Разобрать часть пневматическую 420.20:
- кронштейн-плита (1) – неразборное соединение;
- вывернуть винты (7), снять шайбы (6, 5) и демонтировать кран (4), краны (21), кран (56);
- демонтировать тестовые точки (3);
- вывернуть винты (8), снять шайбы (6, 5) и демонтировать редукторы (10);
- вывернуть винты (12), снять шайбы (6, 5), демонтировать кран (11) и переходник (92), извлечь прокладку (70);
- вывернуть винты (14), снять шайбы (6, 5), демонтировать клапан минимального давления (13) и переходник (71), извлечь прокладку (70);
- вывернуть винты (15), снять шайбы (6, 5) и демонтировать фильтр (16);
- вывернуть винты (15), снять шайбы (6, 5) и демонтировать клапан обратный (18);
- демонтировать датчик давления (19);
- вывернуть винты (25), снять шайбы (26, 27) и демонтировать переходник с распределителем (22), вывернуть винты (24), рассоединить переходник (28) и распределитель (23), извлечь кольца (30, 31);
- вывернуть винты (33), снять шайбы (34, 35) и демонтировать блок управления тормозом (32);
- вывернуть винты (38), снять шайбы (6, 5) и демонтировать делитель давления (37);
- вывернуть заглушку (39), извлечь кольцо (30);
- вывернуть винты (43), снять шайбы (44, 45), и демонтировать ограничитель давления автоматического тормоза (42);
- вывернуть винты (8), снять шайбы (6, 5) и демонтировать блок управления стояночным тормозом (46);
- вывернуть винты (48), снять шайбы (6, 5) и демонтировать кран (47);
- вывернуть винты (52), снять шайбы (6, 5) и демонтировать клапаны переключательные (51);
- вывернуть винты (48), снять шайбы (6, 5) и демонтировать кран (53);
- вывернуть винты (54), снять шайбы (6, 5), демонтировать кран (53) и переходник (93), извлечь прокладку (70);
- вывернуть винты (58), снять шайбы (44, 45) и демонтировать клапан пропорционального управления (57);
- вывернуть винты (60), снять шайбы (44, 45) и демонтировать редуктор (59);
- вывернуть винты (38), снять шайбы (6, 5) и демонтировать орган дополнительной разрядки (61).
Собрать часть пневматическую. В процессе сборки трущиеся и уплотняемые поверхности деталей и узлов «металл-металл», «металл-резина», резьбовые разборные соединения смазать смазкой ЖТ-79Л ТУ 0254-002-01055954.
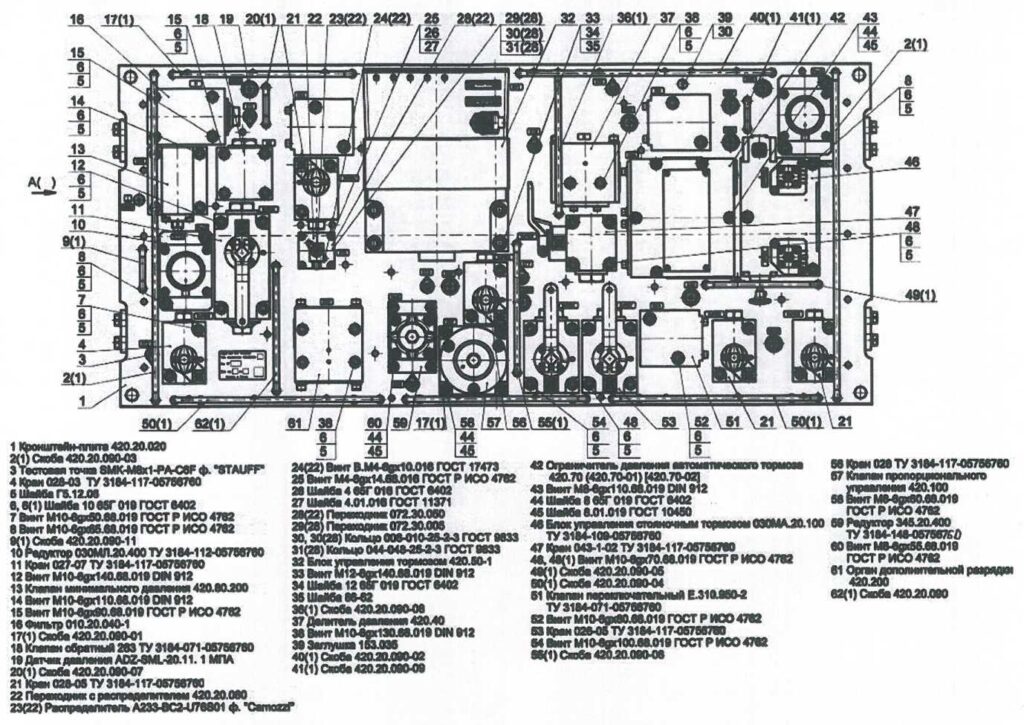
Рисунок 12.7.2.2 – Часть пневматическая 420.20 (420.20-01,420.20-02)
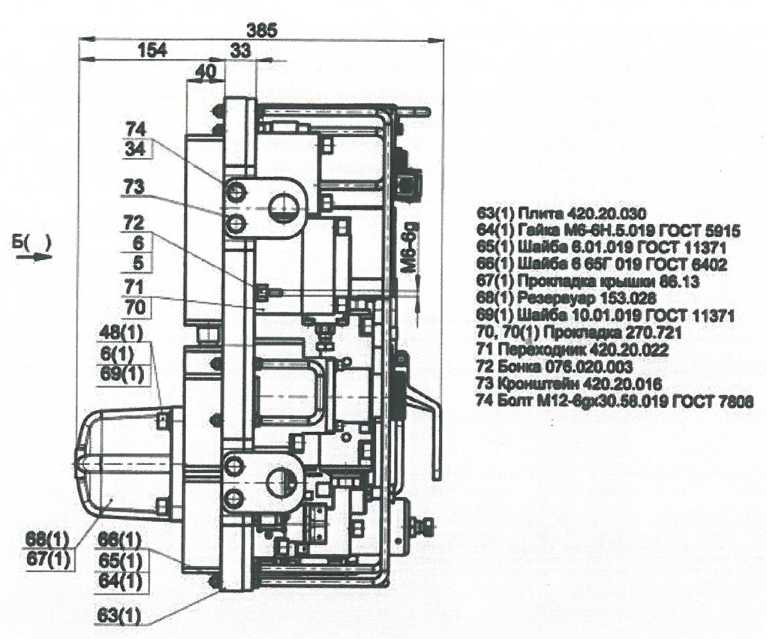
Рисунок 12.7.2.3 – Часть пневматическая 420.20 (420.20-01, 420.20-02)
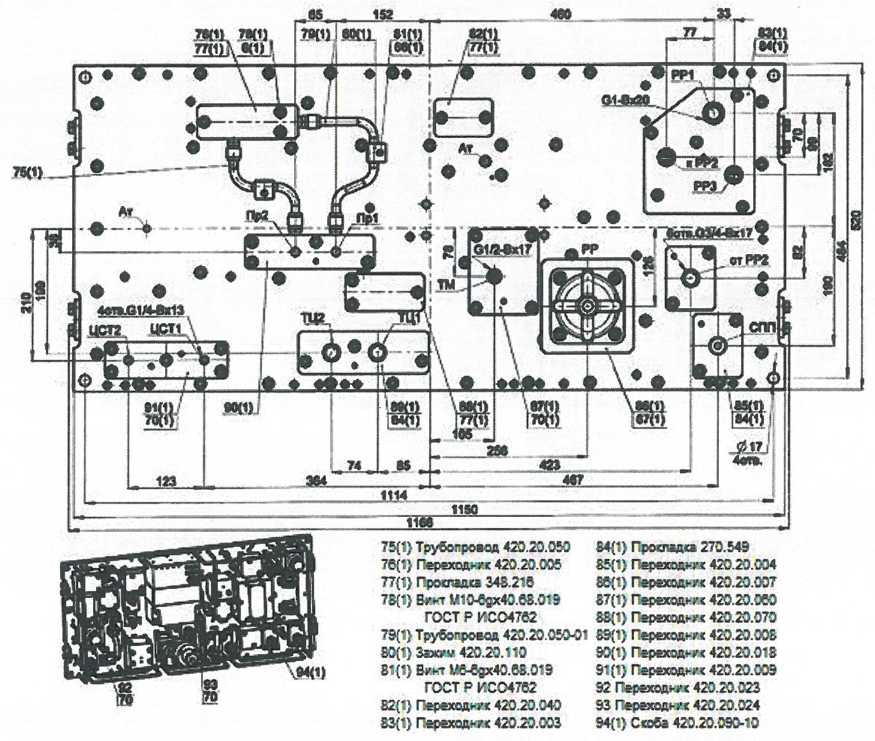
Рисунок 12.7.2.4 – Часть пневматическая 420.20 (420.20-01, 420.20-02)
Делитель давления 420.40
Разобрать делитель давления 420.40 (рисунок 12.7.2.5):
- вывернуть винты (21), снять шайбы (19, 20), снять крышку (4);
- извлечь диафрагму (5);
- отвернуть гайку (6(5)), снять шайбу (8(5)) и диафрагму (9(5));
- извлечь втулку (3);
- извлечь диафрагму (2);
- отвернуть гайку (6(2)), снять шайбу (10(2)) и диафрагму (11(2)), извлечь уплотнение (13(2)) из диска диафрагмы (12(2));
- вывернуть винты (22), снять крышку (15) и кольцо (16), извлечь пружину (17) и клапан (18).
Сборку делителя давления 420.40 провести в обратной последовательности.

Рисунок 12.7.2.5 – Делитель давления 420.40
Блок управления тормозом (БУТ) 420.50-1 (рисунок 12.7.2.6)
Разобрать БУТ:
- вывернуть винты (32), демонтировать крышку (6), разъемы распределителей (33(3), 41(3)), датчиков давления (43(42(3)), корпуса (5);
- вывернуть винты (34), снять шайбы (35, 36), демонтировать корпус (5);
- вывернуть винты (38(3)), снять шайбы (39(3) и 40(3)), демонтировать распределители (33(3), 41(3));
- вывернуть винты (8(3)), снять шайбы (9(3)) и демонтировать переходник с датчиком (42(3)), извлечь кольцо (44(42(3)), вывернуть датчик давления (43(42(3));
- вывернуть винты (37), снять шайбы (35 и 36), демонтировать корпус (4(3)), извлечь кольца (45(1), 17(1)), манжету крана машиниста (18(3));
- вывернуть винты (8(3)), снять шайбы (9(3) и 10(3)), демонтировать крышку (7(3)), поршень (47(3)), извлечь кольцо (48(1)), манжету воздухораспределителя (46(3));
- демонтировать поршень (19), вывернуть гайку (20(19)), снять шайбу (21(19)), демонтировать поршень (24(19)), извлечь кольцо (22(19)), манжету (25(19)), кольцо (26(19));
- вывернуть заглушку (11(1)), извлечь клапан (27(1)), пружину (28(1)), прокладку (12(1)), кольцо (29(1)), шайбу (30(1)), манжету крана машиниста (18(1));
- извлечь прокладку (13(1)), кольцо (14(1)), фильтр (15(1)), кольцо (16(1)), прокладки (31(1)).
Собрать БУТ. В процессе сборки трущиеся и уплотняемые поверхности деталей и узлов «металл-металл», «металл-резина», резьбовые разборные соединения смазать смазкой ЖТ-79Л ТУ 0254-002-01055954.
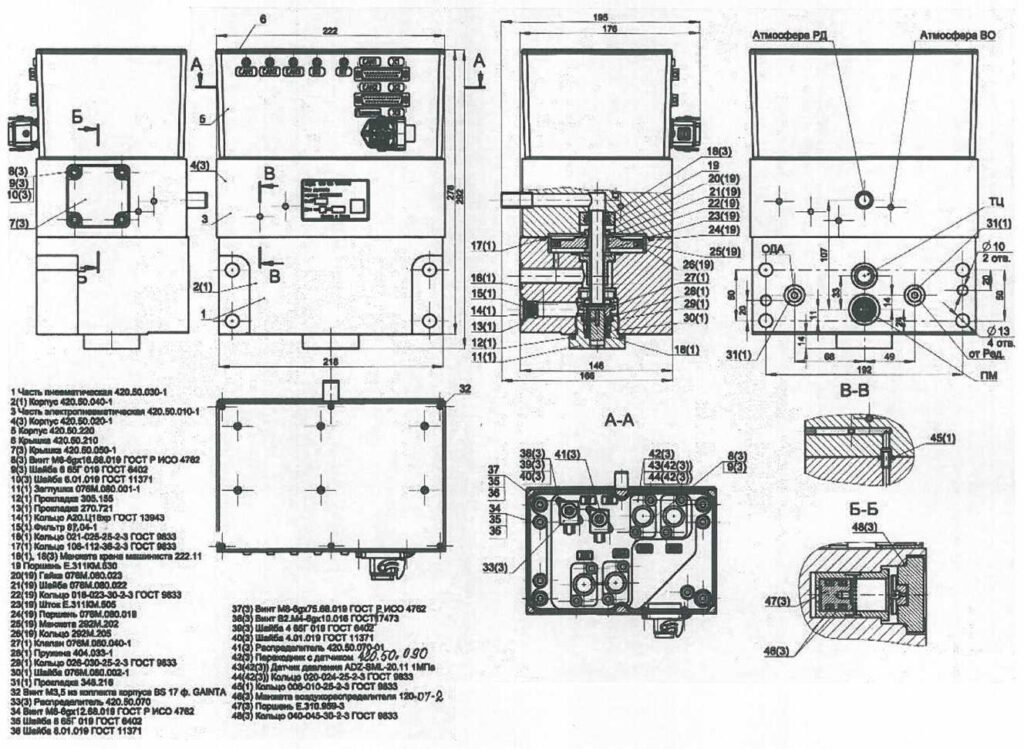
Рисунок 12.7.2.6 – Блок управления тормозом 420.50-1
Порядок текущего ремонта ограничителя давления автоматического тормоза (ОДА) 420.70-1
Для проведения ремонта ОДА его необходимо демонтировать с плиты-кронштейна блока тормозного оборудования 420.
Разобрать ОДА (рисунки 12.7.2.7, 12.7.2.8, 12.7.2.9):
- отвернуть 12 винтов (три по четыре) (5), снять крышки (4, 17 и 18);
- снять четыре прокладки (11);
- отвернуть дроссель (20) и снять уплотнительное кольцо (19);
- отвернуть четыре винта (2) и демонтировать крышку (1) затем снять с нее уплотнительное кольцо (56(1));
- извлечь манжету (8), втулку (57), пружину (21) и клапан (23);
- извлечь втулку (22), затем снять с нее уплотнительное кольцо (24(22));
- извлечь в сборе втулку (27), клапан (26), втулку (51), подшипник (29), пружину (30), тарелку (31) и кольцо (32);
- демонтировать кольцо (32) с хвостовика клапана (26), затем снять тарелку (31), пружину (30), втулку (51), подшипник (29) и втулку (27);
- снять с втулки (27) уплотнительное кольцо (52(27)), демонтировать кольцо (54(27)), извлечь шайбу (55(27)) и манжету (28(27)).
Осмотреть, проверить и при необходимости заменить пружины в соответствии с таблицей 12.7.2.2.
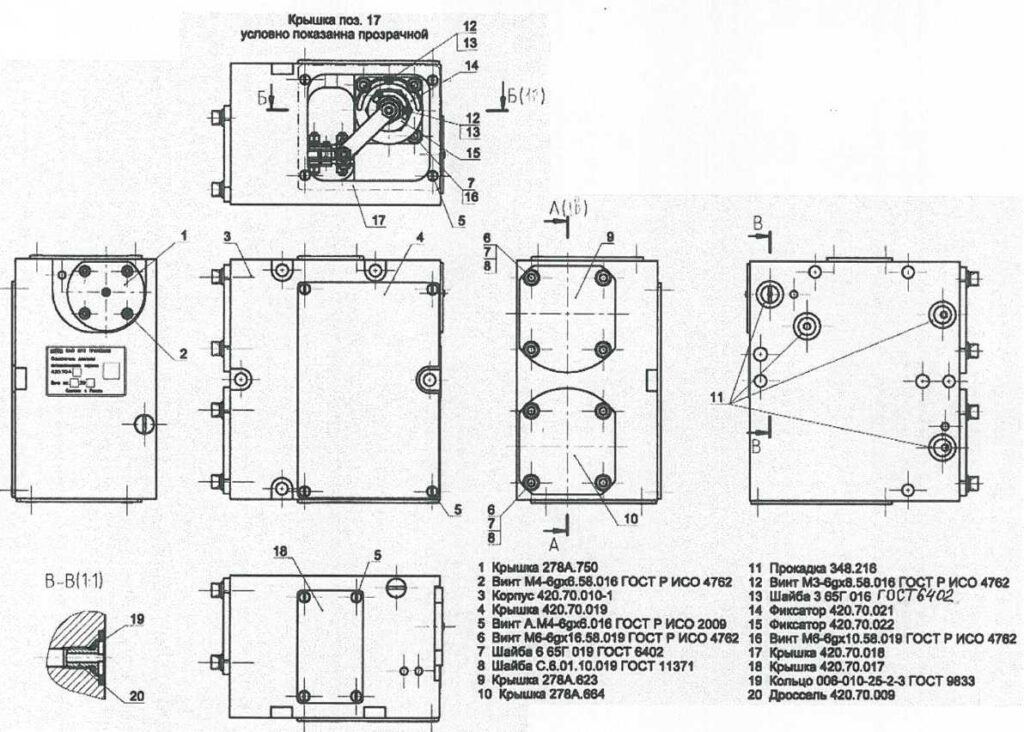
Рисунок 12.7.2.7 – Ограничитель давления автоматического тормоза 420.70-1
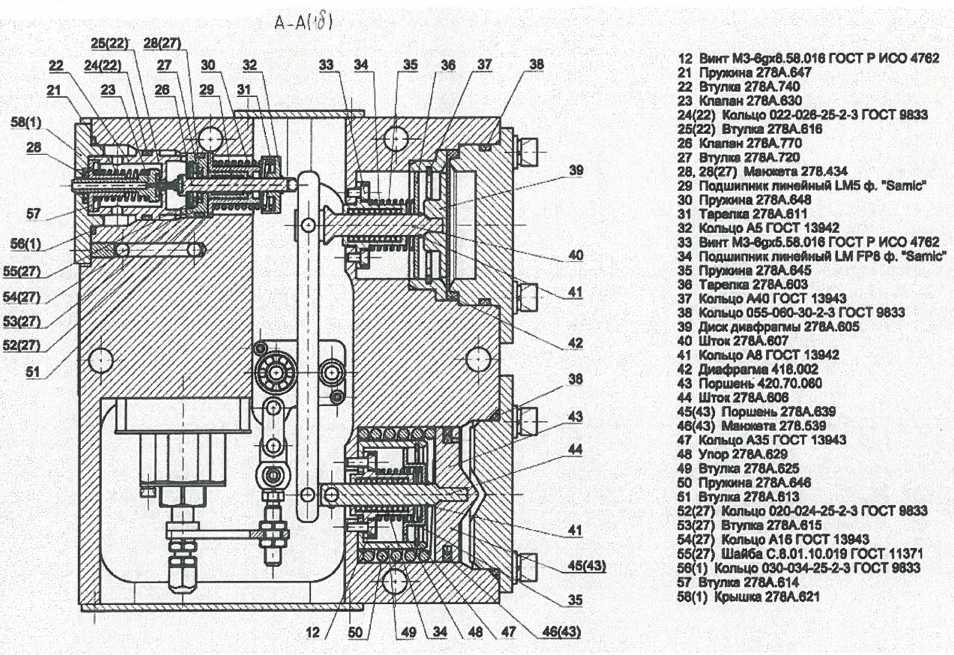
Рисунок 12.7.2.8 – Ограничитель давления автоматического тормоза 420.70-1
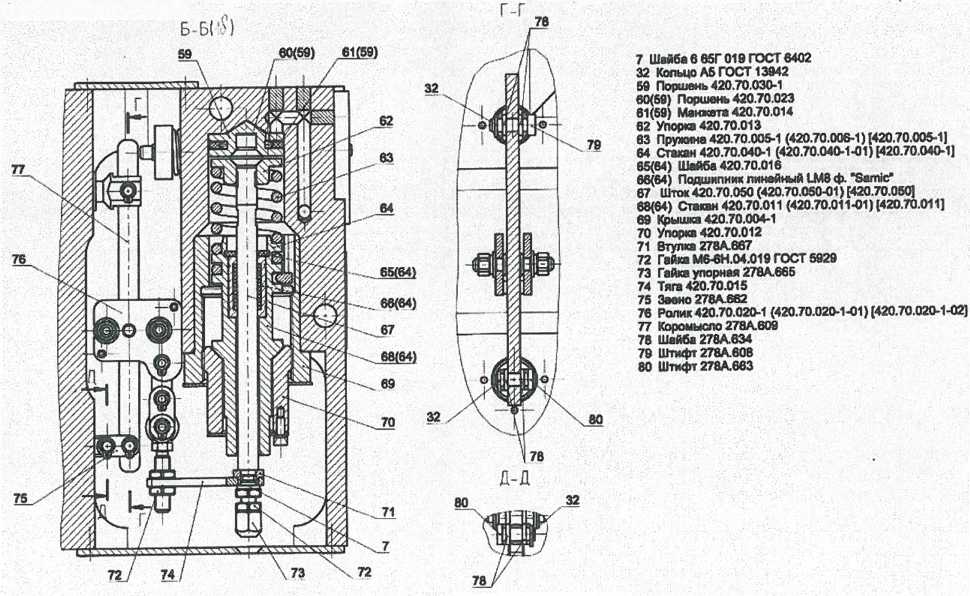
Рисунок 12.7.2.9 – Ограничитель давления автоматического тормоза 420.70-1 (420.70-1-01, 420-70-1-02)
Собрать ОДА в обратном порядке. В процессе сборки трущиеся и уплотняемые поверхности деталей и узлов «металл-металл», «металл-резина», резьбовые разборные соединения смазать смазкой ЖТ-79Л ТУ 0254-002-01055954. Прокладки (11) рекомендуется устанавливать на клей 88-СА ТУ 38.105.1760-89.
Клапан минимального давления 420.80.200 (рисунок 12.7.2.10)
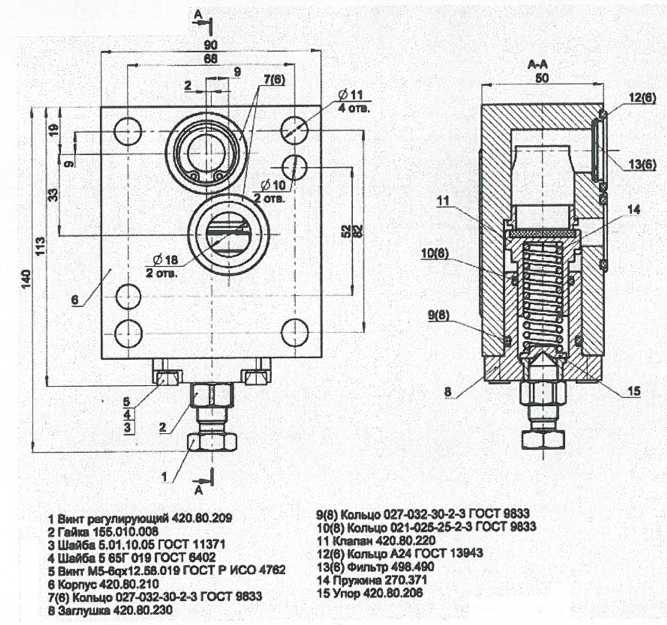
Рисунок 12.7.2.10 – Клапан минимального давления 420.80.200
Разобрать клапан минимального давления:
- отвернуть гайку (2), вывернуть винт (1);
- вывернуть винты (5), снять шайбы (3 и 4), демонтировать заглушку (8), извлечь кольца (9(8), 10(8)), упор (15), пружину (14), клапан (11);
- демонтировать кольцо (12(6)), извлечь фильтр (13(6)), кольца (7(6)).
Собрать клапан минимального давления. В процессе сборки трущиеся и уплотняемые поверхности деталей и узлов «металл-металл», «металл-резина», резьбовые разборные соединения смазать смазкой ЖТ-79Л ТУ 0254-002-01055954.
Клапан пропорционального управления 420.100 (рисунок 12.7.2.11)
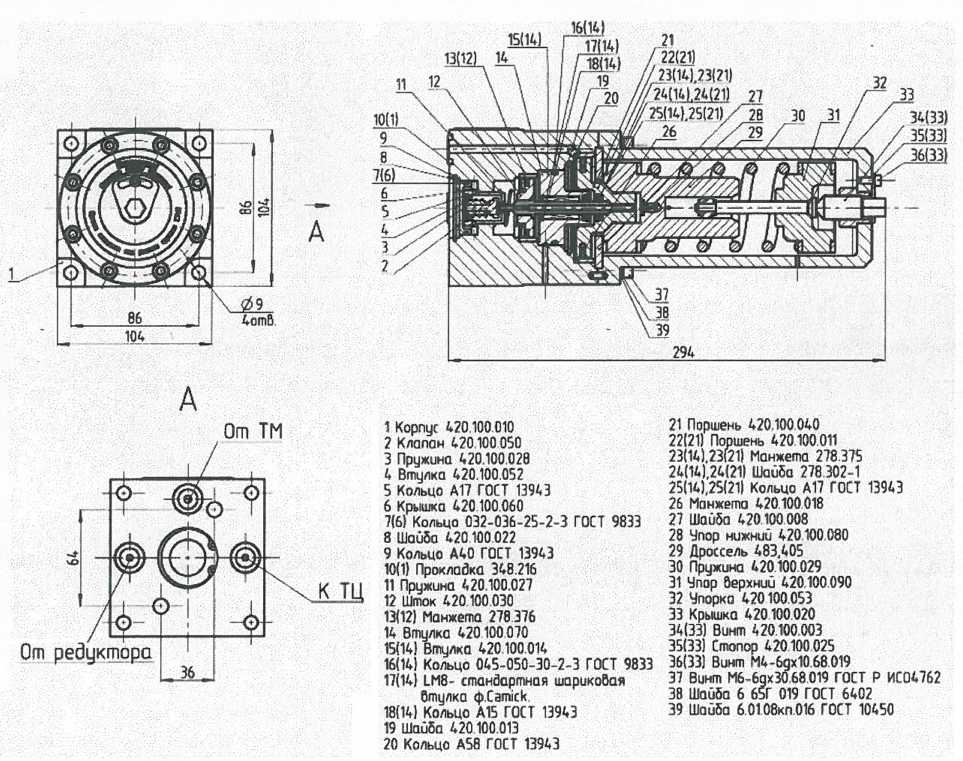
Рисунок 12.7.2.11 – Клапан пропорционального управления 420.100
Разобрать клапан пропорционального управления:
- вывернуть винты (36), снять шайбы (37 и 38);
- осторожно демонтировать крышку (32), извлечь из крышки винты (33(32), 35(32)), стопор (34(32));
- извлечь упорку (31), извлечь упор верхний (30), пружину (29), упор нижний (28);
- извлечь шайбу (27), поршень (21);
- извлечь из поршня (21) манжету (26), кольцо (25(21)), шайбу (25(21)), манжету (23(21));
- извлечь кольцо (20) и шайбу (19);
- демонтировать втулку (14), из которой извлечь кольцо (16(14)), кольцо (18), шариковую втулку (17(18)), извлечь кольцо (25(14)), шайбу (25(14)), манжету (23(14));
- вынуть шток (12), извлечь манжету (13(12));
- извлечь пружину (1);
- извлечь кольцо (9) и шайбу (8), крышку (6), из которой извлечь кольцо (7(6));
- извлечь кольцо (5), втулку (4); пружину (3);
- демонтировать клапан (2).
Собрать клапан пропорционального управления. В процессе сборки трущиеся и уплотняемые поверхности деталей и узлов «металл-металл», «металл-резина», резьбовые разборные соединения смазать смазкой ЖТ-79Л ТУ 0254-002-01055954.
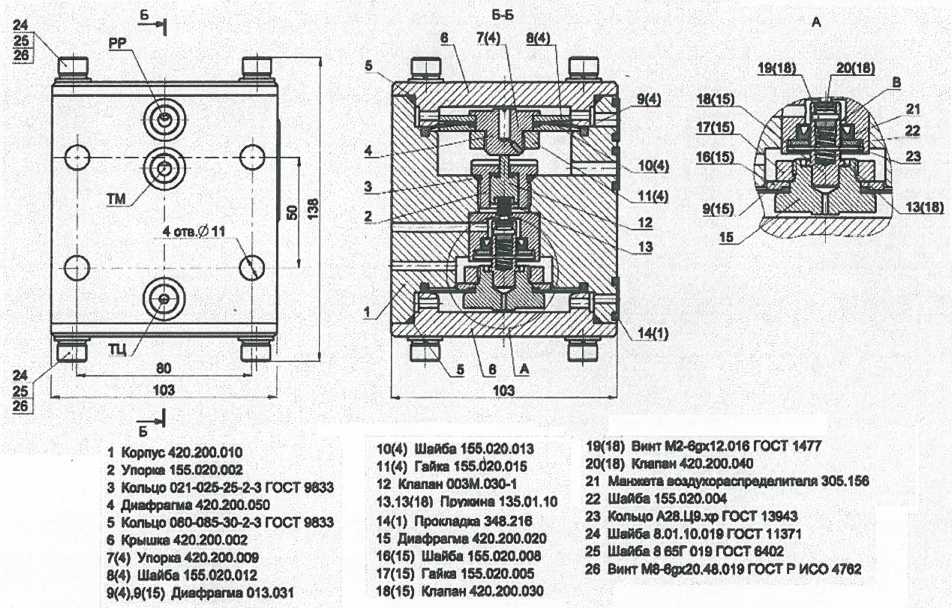
Рисунок 12.7.2.12 – Орган дополнительной разрядки 420.200
После сборки БТО его необходимо проверить на стенде (рисунок 12.7.2.13) на соответствие показателей таблицы 12.7.2.3.
Таблица 12.7.2.3 – Характеристики БТО 420, 420-01, 420-02 применительно к условиям стендовых испытаний
Наименование характеристики | Значение | ||
БТО 420 | БТО 420-01 | БТО 420-02 | |
Автоматическое пневматическое торможение | |||
1 При давлении сжатого воздуха в тормозной магистрали (ТМ), равном (0,50±0,01) МПа, должен быть полный отпуск | Имеется | ||
2 При снижении давления сжатого воздуха в ТМ крана машиниста (КМ) до (0,30±0,02) МПа *, давление в тормозном цилиндре (ТЦ) должно быть, МПа:
|
0,32±0,01
0,38±0,01 |
0,23±0,01
0,29±0,01 |
0,24±0,01
0,27±0,01 |
3 Время наполнения ТЦ с 0 до 0,25 МПа при экстренном торможении, с, не более | 3,5 | ||
4 Время снижения давления в ТЦ при повышении давления сжатого воздуха в ТМ КМ до (0,50±0,1) МПа, с 0,2 МПа до 0,04 МПа, с, не более | 5,0 | ||
Автоматическое электропневматическое торможение | |||
5 При снятии напряжения с вентиля тормоза безопасности (ВТБ) давление в ТЦ должно быть МПа:
|
0,32±0,01
0,38±0,01 |
0,23±0,01
0,29±0,01 |
0,24±0,01
0,27±0,01 |
6 Время наполнения ТЦ от 0 до давления, соответствующего п.5, при снятии напряжения с ВТБ, должно быть, с, не более:
|
3
4 |
||
7 При подаче напряжения на ВТБ, должен произойти полный отпуск.
Время снижения давления до 0,04 МПа, в ТЦ должно быть, с, не более:
|
5
7 |
||
Электропневматическое торможение | |||
8 Формирование вагонным блоком управления тормозом (БУТ) по команде от системы верхнего уровня давления в ТЦ с точностью ± 0,01 МПа | Имеется | ||
Стояночный тормоз | |||
9 При импульсной (не более 2 с) поочередной подаче напряжения на вентили блока управления стояночным тормозом (БУСТ), по командам от системы верхнего уровня, должно обеспечиваться соответственно наполнение или выпуск воздуха из цилиндра стояночного тормоза (ЦСТ):
|
Имеется выпуск Имеется наполнение |
10 Давление в ЦСТ должно быть, МПа | 0,45±0,01 |
11 Время наполнения резервуара ЦСТ с 0 до 0,4 МПа (с 0 до 4,0 кгс/см2) при дистанционном и ручном управлении должно быть, с, не более | 8 |
12 Время выпуска воздуха из резервуара ЦСТ с 0,39 МПа до 0,05 МПа
при дистанционном и ручном управлении должно быть, с, не более |
20 |
Режим пониженной тормозной эффективности «холодный резерв» |
|
13 При снижении давления сжатого воздуха в ТМ КМ до (0,30 ±0,02) МПа, давление в ТЦ должно быть, МПа | 0,15±0,02 |
Подача воздуха к системе пневматического подвешивания |
|
14 При повышении давления в ПМ, до достижения значения (0,66 ±0,02) МПа ((6,7 ±0,2) кгс/см2), не должно происходить повышения давления в системе пневмоподвешивания | Имеется |
15 Максимальное давление в системе пневмоподвешивания, МПа | 0,79±0,02 |
Чувствительность реле давления |
|
16 Автоматическое поддержание установившегося, в течение не менее 30 с, давления в ТЦ при создании утечки из него, МПа | ±0,015 |
Проверка диагностики |
|
17 Отображение на дисплеи информации о работоспособности датчиков давления, диагностики кранов и штока БУСТ, наличие напряжения в цепи безопасности, определение работоспособности каналов питания ИП-ЛЭ, наличие связи с устройствами внутренней сети CAN, отключение противоюза | Имеется |
Проверка герметичности |
|
18 Должна быть обеспечена герметичность плиты-кронштейна, мест соединений навесных приборов, атмосферных отверстий | Пропуск воздуха не допускается |
Примечания:
* Давление может уточняться по результатам испытаний.
** Давление в пневморессорах на порожнем режиме (0,29±0,01) МПа ((3,0±0,1) кгс/см2).
*** Давление в пневморессорах на груженом режиме (0,61±0,01) МПа ((6,2±0,1) кгс/см2).
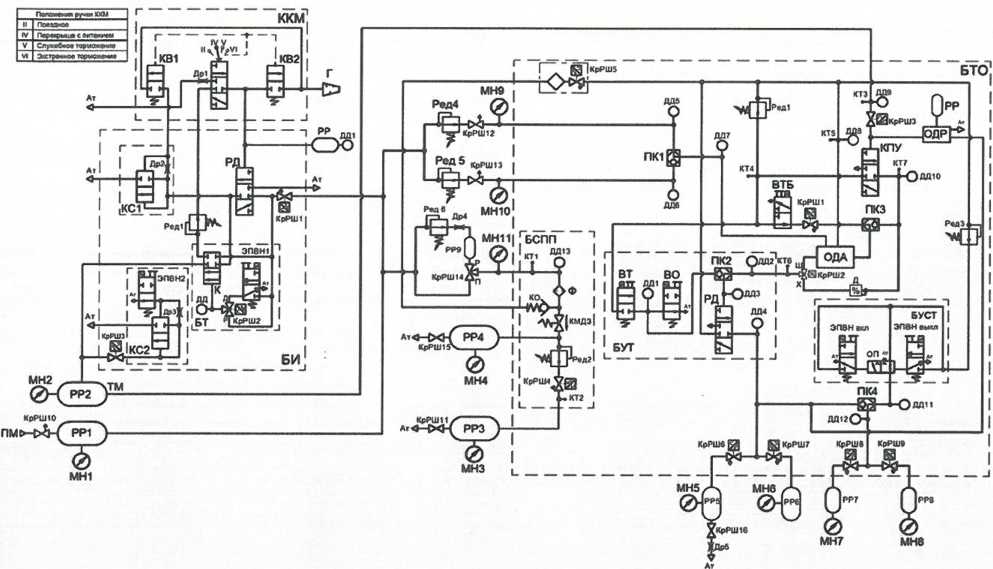
Рисунок 12.7.2.13 – Схема стенда БТО 420.00.000 П3.1
Спецификация
Обозначение | Наименование | Кол. | Примечания |
БТО | Блок тормозного оборудования 420 | ||
КПУ | Клапан пропорционального управления | 1 | |
ОДА | Ограничитель давления автоматического тормоза | 1 | |
ОДР | Орган дополнительной разрядки | 1 | |
РР | Резервуар | 1 | |
ВТБ | Вентиль тормоза безопасности | 1 | |
КрРШ2 | Кран шаровый трехходовой с диагностикой | 1 | |
КрРШ1, КрРШ3, КрРШ6, КрРШ7, КрРШ8, КрРШ9 | Кран шаровый разобщительный с диагностикой | 6 | |
КрРШ5 | Кран с фильтром с диагностикой | 1 | |
Ред1,Ред3 | Редуктор | 2 | |
ДД5-ДД12 | Датчик давления | 8 | |
КТ3-КТ7 | Контрольная точка | 5 | |
ПК1, ПК3, ПК4 | Клапан переключательный | 3 | |
Д | Делитель давления | 1 | |
БУСТ | Блок управления стояночным тормозом | 1 | |
ЭПВН вкл | Вентиль электропневматический (вкл) | 1 | |
ЭПВН выкл | Вентиль электропневматический (выкл) | 1 | |
ОП | Орган переключательный | 1 | |
БУТ | Блок управления тормозом | 1 | |
ВТ | Вентиль тормоза | 1 | |
ВО | Вентиль отпуска | 1 | |
ПК2 | Клапан переключательный | 1 | |
РД | Реле давления | 1 | |
ДД1, ДД2, ДД3, ДД4 | Датчик давления | 4 | |
БСПП | Блок системы пневмоподвеса | 1 | |
КО | Клапан обратный | 1 | |
Ф | Фильтр | 1 | |
КрРШ4 | Кран шаровый разобщительный | 1 | |
Ред2 | Редуктор | 1 | |
КТ1. КТ2 | Контрольная точка | 2 | |
КМД3 | Клапан минимального давления зарядки | 1 | |
ДД13 | Датчик давления | 1 | |
КМ | Кран машиниста 345 | ||
ККМ | Контроллер крана машиниста | 1 | |
KB1,KB2 | Клапан возбудительный | 2 | |
БИ | Блок исполнительный | 1 | |
KC1, КС2 | Клапан срывной | 2 | |
РД | Реле давления | 1 | |
Ред | Редуктор | 1 | |
Др1-Др3 | Дроссель | 3 | |
РР | резервуар | 1 | |
УБТ | Устройство блокировки тормозов | 1 | |
К | Клапан | 1 | |
ДД,ДД1 | Датчик давления | 2 | |
ЭПВН1, ЭПВН2 | Вентиль электропневматический | 2 | |
КрРШ1, КрРШ3 | Кран шаровый разобщительный | 2 | |
КрРШ2 | Кран шаровый трехходовой с диагностикой | 1 | |
ПМ | Питательная магистраль | ||
ТМ | Тормозная магистраль | ||
Ат | Атмосфера | ||
РР1 | Резервуар | 1 | 110 л |
РР2, РР3, РР4 | Резервуар | 3 | 55 л |
РР5, РР6 | Резервуар | 2 | 10 л |
РР7, РР8, РР9 | Резервуар | 3 | 5 л |
КрРШ10-КрРШ15 | Кран шаровый разобщительный | 6 | |
КрРШ16 | Кран шаровый трехходовой | 1 | Р – редуктор П – питательная |
Ред4 | Редуктор | 1 | 3,0±0,1 кгс/см2 |
Ред5 | Редуктор | 1 | 6,2±0,1 кгс/см2 |
Ред6 | Редуктор | 1 | 6,7±0,2 кгс/см2 |
Др4, Др5 | Дроссель | 2 | Диаметр 1 мм |
MH1 -МН11 | Манометр | 11 |
Блок пневматического оборудования 419 (БПО 419)
При ремонте БПО заменяются все резиновые уплотнительные изделия и вулканизированный клапан, указанные в таблице 12.7.3.1.
Таблица 12.7.3.1 – Перечень резиновых уплотнительных изделий
Месторасположение | Наименование | Обозначение | Кол-во на изделие | Примечание | |
Рисунок | Позиция | ||||
Блок пневматического оборудования 419 | |||||
12.7.3.1 | 16 | Прокладка | 270.549 | 2 | |
19 | Прокладка | 348.216 | 1 | ||
29 | Прокладка | 270.721 | 2 | ||
Пневмораспределитель 419.60 | |||||
12.7.3.2 | 6 | Прокладка | 348.216 | 1 | |
7 | Кольцо ГОСТ 9833 | 044-048-25-2-3 | 1 | ||
8 | Кольцо ГОСТ 9833 | 044-048-25-2-3 | 1 | ||
10 | Манжета | 278.376 | 1 | ||
15 | Прокладка | 305.155 | 1 | ||
. 16 | Манжета крана машиниста | 222.11 | 1 | ||
20 | Кольцо ГОСТ 9833 | 026-030-25-2-3 | 1 | ||
21 | Кольцо ГОСТ 9833 | 014-018-25-2-3 | 1 | ||
Пневмораспределитель 419.60-01 | |||||
12.7.3.3 | 6 | Кольцо ГОСТ 9833 | 044-048-25-2-3 | 1 | |
7 | Кольцо ГОСТ 9833 | 044-048-25-2-3 | 1 | ||
13 | Прокладка | 305.155 | 1 | ||
14 | Манжета крана машиниста | 222.11 | 1 | ||
15 | Клапан (резина группы 3(7-7130) ТУ 2539-054-05766882 | 076М.080.050-1 (вулканизированный клапан) | 1 | Неразборное соединение | |
18 | Кольцо ГОСТ 9833 | 026-030-25-2-3 | 1 | ||
19 | Кольцо ГОСТ 9833 | 014-018-25-2-3 | 2 |
При ремонте БПО 419 провести проверку всех пружин в соответствии с таблицей 12.7.3.2.
Пружины необходимо заменить при наличии отклонений от контрольных значений параметров, наличии любых внешних повреждений.
Таблица 12.7.3.2 – Перечень пружин
Месторасположение | Обозначение | Средства измерений | Контрольные значения параметров | |
Рисунок | Позиция | |||
12.7.3.2, | 19 | 419.60.008 | Машина для испытания пружин, штангенциркуль | P1=14,33±0,8 кгс; H1=11 мм |
12.7.3.3 | 17 | Р2=15,63±1,21 кгс; Н2=10 мм |
Разобрать БПО 419 (рисунок 12.7.3.1):
- вывернуть винты (5), снять шайбы (3 и 4) и демонтировать кран шаровой разобщительный (2);
- вывернуть винты (9), снять шайбы (7 и 8) и демонтировать пневмораспределители (6);
- вывернуть винты (12), снять шайбы (3 и 4), демонтировать кран шаровой разобщительный (2) и переходник (28), извлечь прокладку (29).
Собрать БПО 419, в процессе сборки трущиеся и уплотняемые поверхности деталей и узлов «металл-металл», «металл-резина», резьбовые разборные соединения смазать смазкой ЖТ-79Л ТУ 0254-002-01055954.
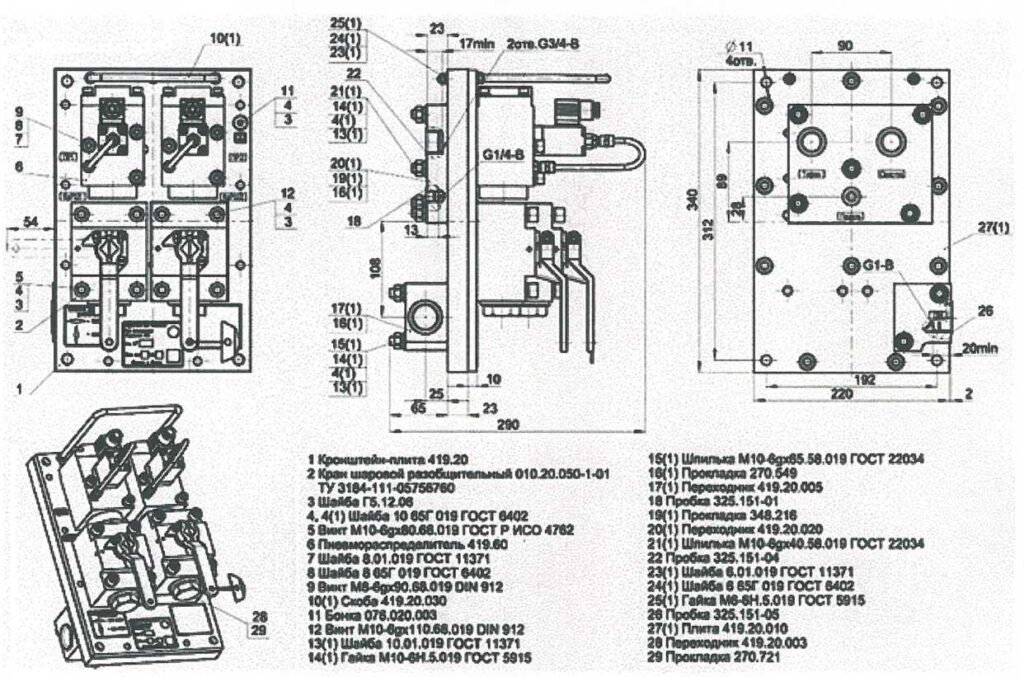
Рисунок 12.7.3.1 – Блок пневматического оборудования 419
Пневмораспределитель 419.60 (рисунок 12.7.3.2)
Разобрать пневмораспределитель:
- вывернуть винты (4), снять шайбы (2 и 3) и демонтировать крышку (5), извлечь кольцо (8(5));
- вывернуть заглушку (14), извлечь клапан (17), пружину (19), прокладку (15), кольцо (20), шайбу (18), манжету крана машиниста (16);
- извлечь поршень (9), манжету (10(9)), кольца (21(1), 7(1)), прокладку (6(1));
- демонтировать трубопровод (13), вывернуть винты (22(12)), демонтировать распределитель (12).
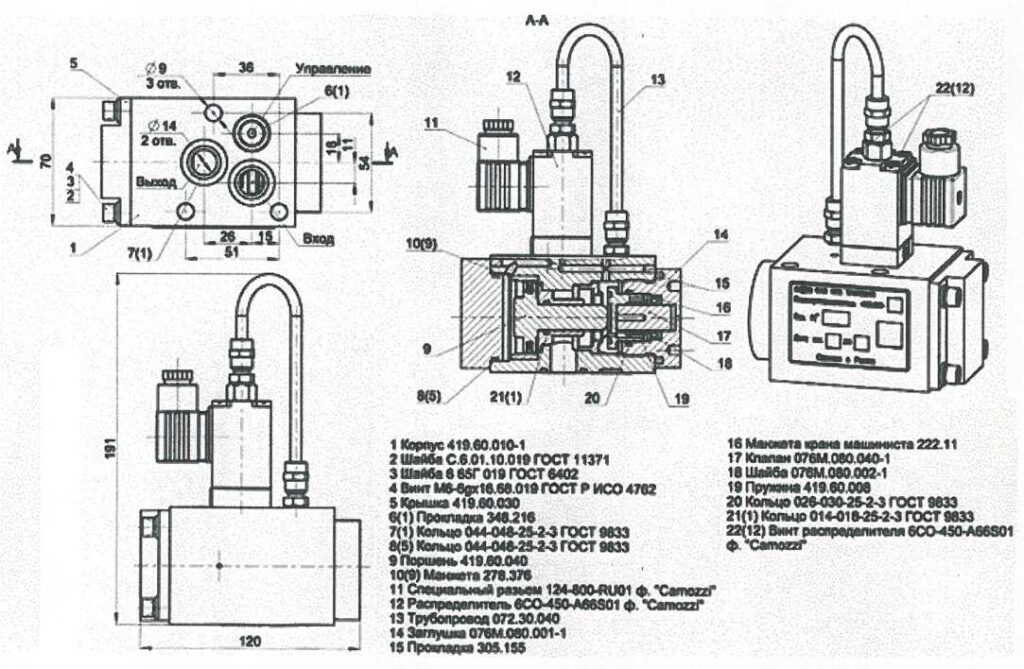
Рисунок 12.7.3.2 – Пневмораспределитель 419.60
Собрать пневмораспределитель, в процессе сборки трущиеся и уплотняемые поверхности деталей и узлов «металл-металл», «металл-резина», резьбовые разборные соединения смазать смазкой ЖТ-79Л ТУ 0254-002-01055954.
Пневмораспределитель 419.60-01 (рисунок 12.7.3.3)
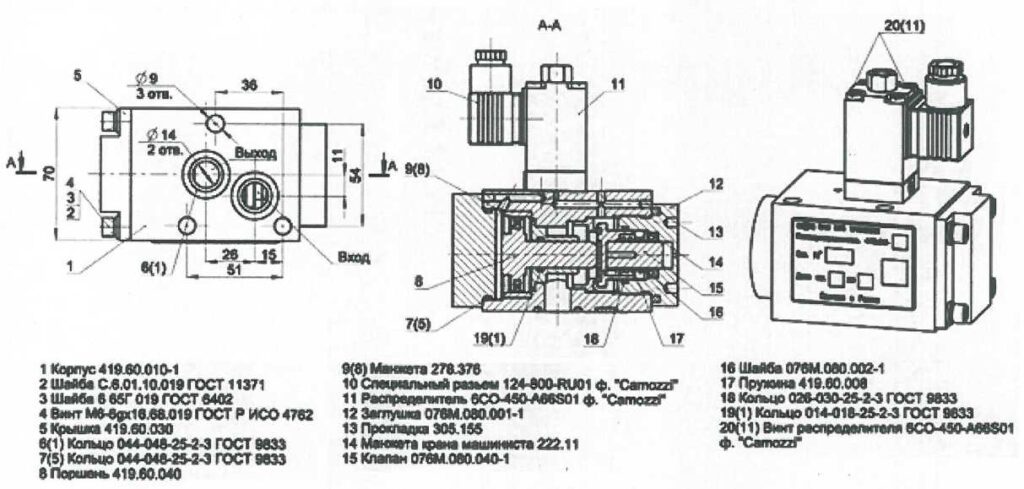
Рисунок 12.7.3.3 – Пневмораспределитель 419.60-01
Разобрать пневмораспределитель:
- вывернуть винты (4), снять шайбы (2 и 3) и демонтировать крышку (5), извлечь кольцо (7(5));
- вывернуть заглушку (12), извлечь клапан (15), пружину (17), прокладку (13), кольцо (18), шайбу (16), манжету крана машиниста (14);
- извлечь поршень (8), манжету (9(8)), кольца (19(1), 6(1));
- вывернуть винты (20(11)), демонтировать распределитель (11).
Собрать пневмораспределитель в порядке, обратном разборке.
В процессе сборки трущиеся и уплотняемые поверхности деталей и узлов «металл-металл», «металл-резина», резьбовые разборные соединения смазать смазкой ЖТ-79Л ТУ 0254-002-01055954.
После сборки БПО проверить на соответствие показателей таблицы 12.7.3.3, проверить целостность пневматических и электрических соединений.
Проверку показателей работы БПО 419 произвести на стенде в соответствии с рисунком 12.7.3.4.
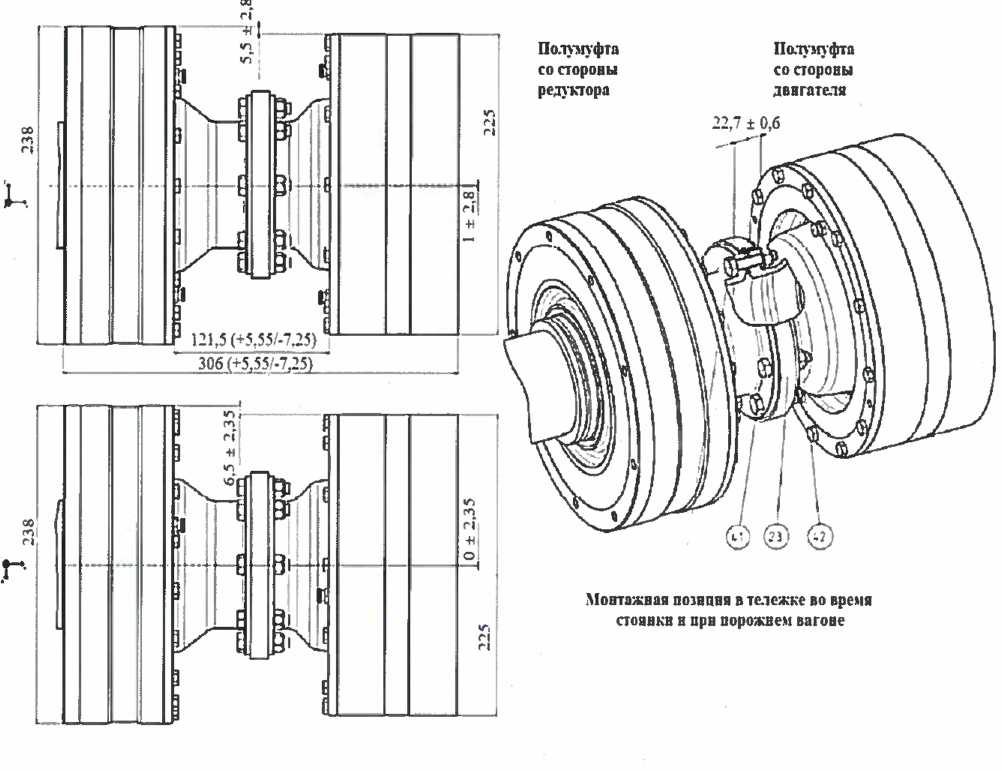
Рисунок 12.7.3.4 – Схема пневматическая принципиальная стенда БПО 419.00.000 П3
Таблица 12.7.3.3 – Характеристики БПО 419
Наименование характеристики | Значение |
1 Время наполнения сжатым воздухом резервуара от 0 до давления 0,49 МПа при подаче напряжения на вентиль В1, с, не более | 3 |
2 Время наполнения сжатым воздухом резервуара от 0 до давления 0,49 МПа при подаче напряжения на вентиль В2, с, не более | 3 |
3 Время наполнения сжатым воздухом резервуаров от 0 до давления 0,49 МПа при дублировании пневматического сигнала от педали, с, не более | 3 |
4 Должна быть обеспечена герметичность кронштейн-плиты, мест соединений навесных приборов, атмосферных отверстий | Пропуск воздуха не допускается |
Индикатор тормозной 421 (ИТ 421)
При проведении ремонта ИТ 421 заменить указанные в таблице 12.7.4.1 все резиновые уплотнительные изделия.
Таблица 12.7.4.1 – Перечень резиновых уплотнительных изделий ИТ
Месторасположение | Наименование | Обозначение | Кол-во на изделие | Примечание | |
Рисунок | Позиция | ||||
Блок пневматического оборудования 419 | |||||
12.7.4.1 | 16 | Кольцо ГОСТ 9833 | 025-030-30-2-3 | 1 | |
10 | Уплотнение | 421.008 | 1 |
Назначенный срок службы составляет четыре года, не считая 12 месяцев от даты изготовления, указанной на резиновом уплотнительном изделии или паспорте на партию изделий.
Установка в ИТ 421 резиновых уплотнительных изделий, имеющих надрывы и трещины, а также с истекшим назначенным сроком службы недопустима.
При ремонте ИТ 421 провести проверку всех пружин в соответствии с таблицей 12.7.4.2. Пружины необходимо заменить при наличии отклонений от контрольных значений параметров, наличии любых внешних повреждений (изломов, трещин и т.д.).
Таблица 12.7.4.2 – Перечень пружин ИТ 421
Месторасположение | Обозначение | Средства измерений | Контрольные значения параметров | |
Рисунок | Позиция | |||
12.7.4.1 | 6 | 421.016-04 | Машина для испытания пружин (МИП), штангенциркуль | F1=1,51±0,18; L1=66 мм F2=2,51±0,25; L2=30,5 мм |
17 | 421.014-01 | Машина для испытания пружин (МИП), штангенциркуль | F1=11,23±1,1; L1=66 мм F2=32,5±3,2; L2=30 мм |
Разобрать ИТ 421 (рисунок 12.7.4.1):
- вывернуть винты (2) и снять крышку (11);
- вывернуть винты (23), снять шайбы (21) и вынуть из корпуса (9) элемент индикаторный (1) и элемент индикаторный (3).
Разобрать элемент индикаторный 421.010 (1):
- открутить гайку (14(1)), снять шайбы (12(1) и 13(1)), снять флажок (15(1));
- из корпуса (4(1)) извлечь кольцо (8(1)), вынуть шайбу стопорную (7(1)), пружину (6(1)), поршень (5(1)).
Разобрать элемент индикаторный 421.010-1 (3):
- открутить гайку (14(3)), снять шайбы (12(3) и 13(3)), снять флажок (18(3));
- из корпуса (4(1)) извлечь кольцо (8(1)), вынуть шайбу стопорную (7(1)), пружину (6(1)), поршень (5(1)).
Сборку ИТ 421 провести в обратной последовательности. В процессе сборки трущиеся и уплотняемые поверхности деталей и узлов «металл-металл», «металл-резина», резьбовые разборные соединения смазать смазкой ЖТ-79Л ТУ 0254-002-01055954.
После сборки ИТ 421 его необходимо проверить на соответствие показателей таблицы 12.7.4.3, а также проверить целостность пневматических и электрических соединений.
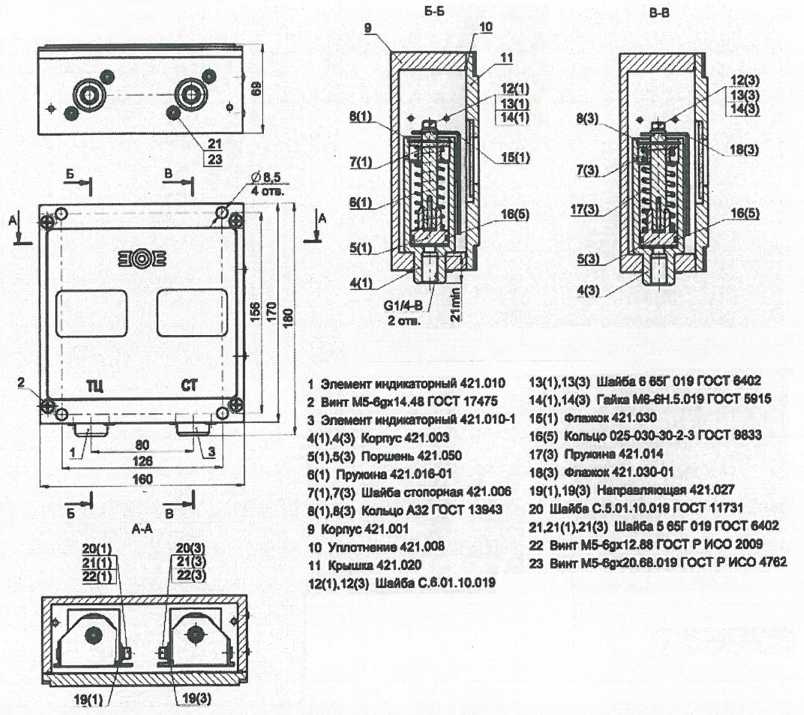
Рисунок 12.7.4.1 – Индикатор тормозной 421
Таблица 12.7.4.3 – Характеристики ИТ 421
Наименование характеристики | Значение | ||
1 При давлении сжатого воздуха в тормозном цилиндре (ТЦ) в диапазоне от 0,02 до 0,05 МПа, цвет индикатора в левом окне ИТ должен быть «Красный с черным кругом» | ![]() |
||
2 При давлении сжатого воздуха в ТЦ менее или равном 0,02 МПа, цвет индикатора в левом окне ИТ должен быть «Зеленый» | ![]() |
||
3 При давлении сжатого воздуха в стояночном тормозе (СТ) в диапазоне от 0,44 до 0,48 МПа, цвет индикатора в правом окне ИТ должен быть «Зеленый» | ![]() |
||
4 При давлении сжатого воздуха в СТ менее или равном 0,44 МПа, цвет индикатора в правом окне ИТ должен быть «Красный с черной полосой» | ![]() |
||
5 Должна быть обеспечена герметичность мест соединений и атмосферных отверстий | Пропуск воздуха не допускается |
Блок пневматического оборудования 422 (БПО 422)
При проведении ремонта БПО 422 для дистанционного управления давлениями сжатого воздуха, подходящими к:
- форсунке песочницы передней тележки моторного вагона электропоезда;
- форсунке песочницы задней тележки моторного вагона электропоезда;
- системе осушки песка, находящегося в бункере;
- подачи через разобщительные краны сжатого воздуха к сидениям машиниста и помощника машиниста, стеклоочистителям заменяются указанные в таблице 12.7.5.1, все резиновые уплотнительные изделия.
Таблица 12.7.5.1 – Перечень резиновых уплотнительных изделий
Месторасположение | Наименование | Обозначение | Кол-во на изделие | Примечание | |
Рисунок | Позиция | ||||
Блок пневматического оборудования 422 | |||||
12.7.5.1 | 21 | Прокладка | 270.549 | 1 | |
23 | Прокладка | 270.721 | 2 |
При ремонте БПО 422 проводится проверка всех пружин в соответствии с таблицей 12.7.5.2.
Пружины необходимо заменить при наличии отклонений от контрольных значений параметров, наличии любых внешних повреждений.
Таблица 12.7.5.2 – Перечень пружин БПО 422
Месторасположение | Обозначение | Средства измерений | Контрольные значения параметров | |
Рисунок | Позиция | |||
Редуктор 030МЛ.20.400 | ||||
12.7.5.1 | – | 483.031 | Машина для испытания пружин, штангенциркуль | P1=7,15±0,72 кгс; H1= 11,5 мм Р2=8,8±0,88 кгс; Н2= 10 мм |
Разобрать блок пневматического оборудования 422 (рисунок 12.7.5.1):
- вывернуть винты (5), снять шайбы (3 и 4) и демонтировать кран шаровой разобщительный (2);
- вывернуть винты (9), снять шайбы (7 и 8) и демонтировать пневмораспределители (6);
- вывернуть винты (11), снять шайбы (10 и 4), и демонтировать кран шаровой разобщительный (12);
- вывернуть винт (14), снять шайбы (4, 13), демонтировать редуктор (15).
Сборку БПО 422 провести в обратной последовательности.
В процессе сборки трущиеся и уплотняемые поверхности деталей и узлов «металл-металл», «металл-резина», резьбовые разборные соединения смазать смазкой ЖТ-79Л ТУ 0254-002-01055954.
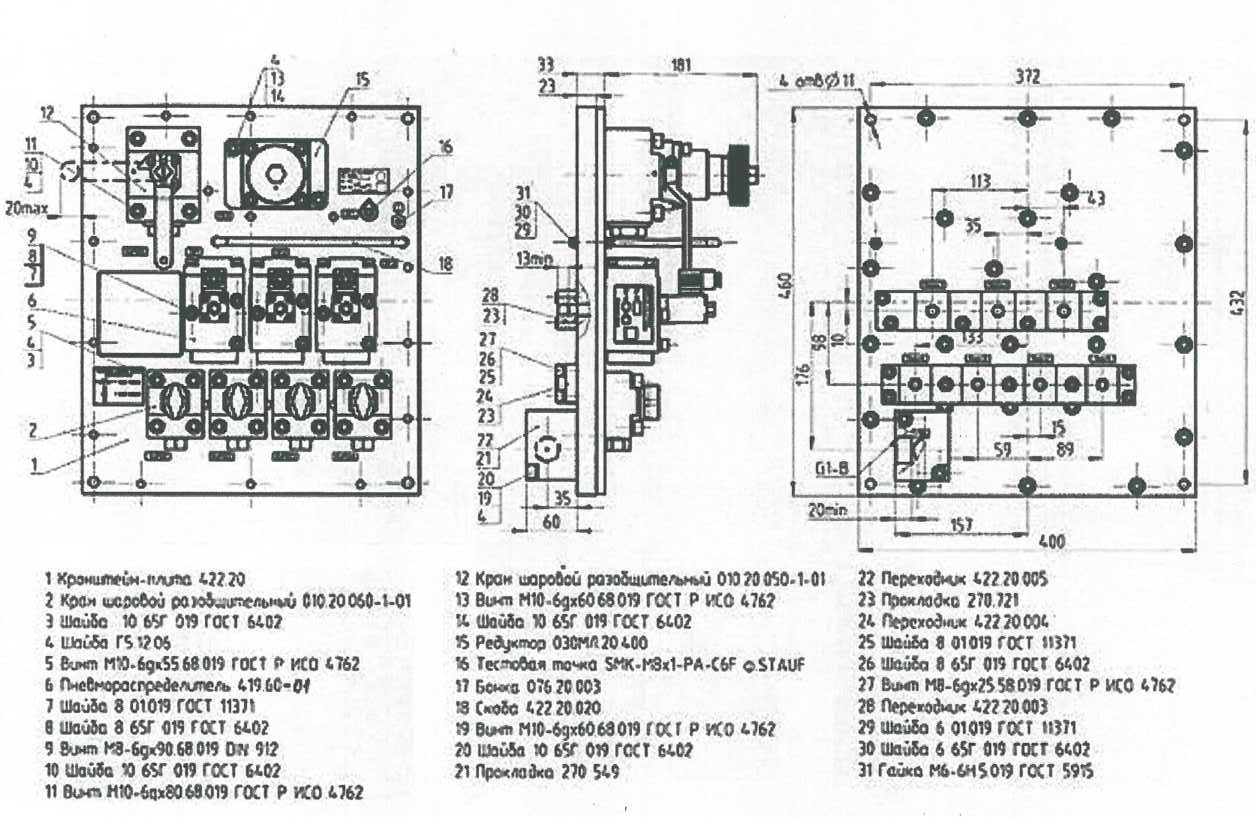
Рисунок 12.7.5.1 – Блок пневматического оборудования 422
После сборки БПО 422 его необходимо проверить на соответствие показателей таблицы 12.7.5.3, а также проверка целостности пневматических и электрических соединений.
Таблица 12.7.5.3 – Характеристики БПО 422
Наименование характеристики | Значение |
1 Редуцированное давление сжатого воздуха, подводимое к песочнице, МПа | 0,27±0,01 |
2 Время наполнения сжатым воздухом резервуара от 0 до давления 0,25 МПа при подаче напряжения на вентиль В1, с, не более | 3 |
3 Время наполнения сжатым воздухом резервуара от 0 до давления 0,25 МПа при подаче напряжения на вентиль В2, с, не более | 3 |
4 Время наполнения сжатым воздухом резервуара от 0 до давления 0,25 МПа при подаче напряжения на вентиль ВЗ, с, не более | 3 |
5 Время наполнения сжатым воздухом резервуара от 0 до давления 0,49 МПа при открытии крана КрРШ1, с, не более | 4 |
6 Время снижения давления сжатого воздуха в резервуаре от 0,49 до 0,05 МПа при закрытии крана КрРШ1, с, не более | 5 |
7 Время наполнения сжатым воздухом резервуара от 0 до давления 0,49 МПа при открытии крана КрРШ2, с, не более | 4 |
8 Время снижения давления сжатого воздуха в резервуаре от 0,49 до 0,05 МПа при закрытии крана КрРШ2, с, не более | 5 |
9 Время наполнения сжатым воздухом резервуара от 0 до давления 0,49 МПа при открытии крана КрРШ3, с, не более | 4 |
10 Время снижения давления сжатого воздуха в резервуаре от 0,49 до 0,05 МПа при закрытии крана КрРШ3, с, не более | 5 |
11 Время наполнения сжатым воздухом резервуара от 0 до давления 0,49 МПа при открытии крана КрРШ4, с, не более | 4 |
12 Время снижения давления сжатого воздуха в резервуаре от 0,49 до 0,05 МПа при закрытии крана КрРШ4, с, не более | 5 |
13 Должна быть обеспечена герметичность плиты-кронштейна, мест соединений навесных приборов, атмосферных отверстий | Пропуск воздуха не допускается |
Блок пневматического оборудования 425 (БПО 425) для отключения при помощи разобщительных кранов агрегатов компрессорных, питательной магистрали (ПМ) а также сообщения тормозной магистрали (ТМ) и ПМ через обратный клапан при следовании электропоезда «Холодным резервом». При ремонте БПО 425 заменяются все резиновые уплотнительные изделия, указанные в таблице 12.7.6.1.
Таблица 12.7.6.1 – Перечень резиновых уплотнительных изделий БПО 425
Месторасположение | Наименование | Обозначение | Кол-во на изделие | Примечание | |
Рисунок | Позиция | ||||
Блок пневматического оборудования 425 | |||||
12.7.6.1 | 17 | Прокладка | 305.155 | 1 | |
18 | Прокладка | 270.549 | 1 | ||
25 | Прокладка | 270.721 | 1 | ||
Кран 425.50-01 | |||||
12.7.6.2 | 2 | Кольцо ГОСТ 9833 | 014-018-25-2-3 | 1 | |
8 | Кольцо ГОСТ 9833 | 050-055-30-2-3 | 1 | ||
10 | Кольцо ГОСТ 9833 | 045-050-30-2-3 | 2 | ||
Кран 026-08 | |||||
12.7.6.3 | 2 | Кольцо ГОСТ 9833 | 014-018-25-2-3 | 1 | |
8 | Прокладка | 270.549 | 1 | ||
9 | Прокладка | 270.721 | 1 | ||
10 | Кольцо ГОСТ 9833 | 028-033-30-2-3 | 2 | ||
Кран 026-1-06 | |||||
12.7.6.4 | 2 | Кольцо ГОСТ 9833 | 014-018-25-2-3 | 1 | |
5 | Прокладка | 270.549 | 1 | ||
6 | Прокладка | 270.721 | 1 | ||
7 | Кольцо ГОСТ 9833 | 028-033-30-2-3 | 2 |
При ремонте БПО 425 провести проверку всех пружин в соответствии с таблицей 12.7.6.2. Пружины необходимо заменить при наличии отклонений от контрольных значений параметров, наличии любых внешних повреждений (изломов, трещин).
Таблица 12.7.6.2 – Перечень пружин БПО 425
Месторасположение | Обозначение | Средства измерений | Контрольные значения параметров | |
Рисунок Позиция | ||||
Клапан обратный 263 | ||||
12.7.6.1 | 11 | 150.218 | Машина для испытания пружин (МИП), штангенциркуль | P1=0,57±0,03 кгс; H1= 15 мм Р2=0,74±0,035 кгс; Н2= 13 мм |
Разобрать БПО 425 (рисунок 12.7.6.1):
- убедиться в отсутствии давления (воздуха), подводимого к БПО 425;
- отсоединить электрические подключения к кранам (3, 7);
- вывернуть винты (6), снять шайбы (4 и 5) и демонтировать кран (3);
- вывернуть винты (8), снять шайбы (4 и 5), демонтировать кран (7) и переходник (26) с прокладкой (25);
- вывернуть винты (9), снять шайбы (4 и 5) и демонтировать кран (7);
- вывернуть винты (8), снять шайбы (4 и 5) и демонтировать клапан (11);
- вывернуть винты (9), снять шайбы (4 и 5) и демонтировать кран (12);
- кронштейн-плита (1) несъемный узел. Каналы кронштейн-плиты продуть сжатым воздухом.
Сборку БПО 425 провести в обратной последовательности.
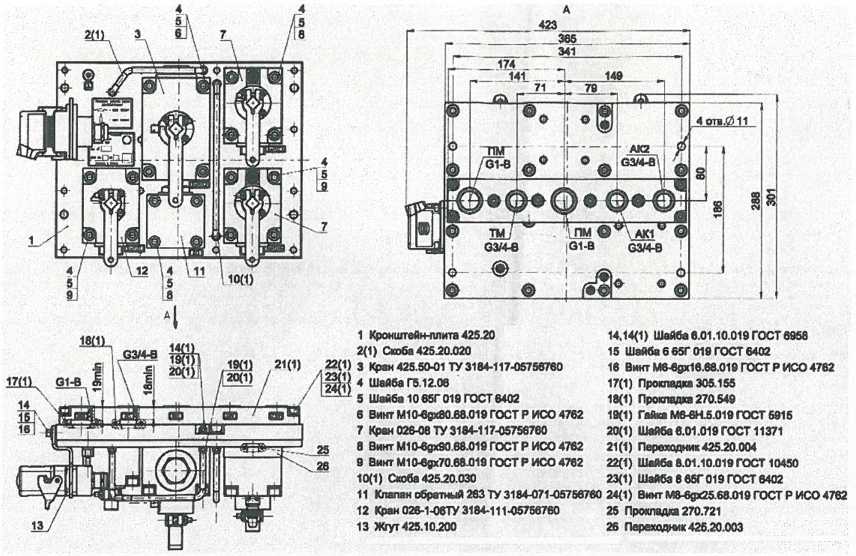
Рисунок 12.7.6.1 – Блок пневматического оборудования 425
Кран 425.50.000-01 (рисунок 12.7.6.2)
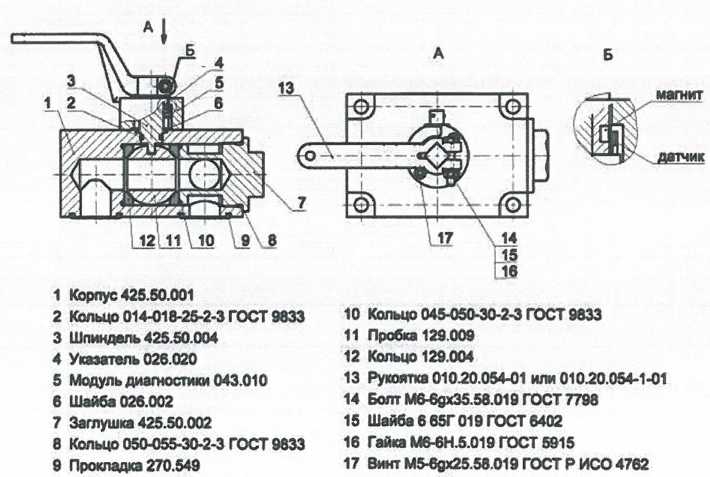
Рисунок 12.7.6.2 – Кран 425.50-01
Разобрать кран:
- кран подлежит ремонту только в случае появления утечек;
- отвернуть болт (14) крепления рукоятки (13), снять рукоятку (13);
- выкрутить винты (17), снять модуль диагностики (5), извлечь шпиндель (3), указатель (4) и шайбу (6);
- вывернуть заглушку (7) и последовательно извлечь резиновые кольца (10), фторопластовые кольца (12) и пробку (11);
- проверить состояние резиновых уплотнительных изделий в соответствии с таблицей 12.7.6.1;
- заменить фторопластовые уплотнения. После замены уплотнений из фторопласта необходимо прогреть кран в крайнем положении «закрыто» в печке при температуре + 60 °C в течение 1 ч и выдержать кран в течение 24 ч при комнатной температуре. Должна быть обеспечена герметичность затвора корпуса и мест соединений при рабочем давлении;
- собрать кран;
- проверить прочность резьбовых соединений после сборки.
ВНИМАНИЕ
ПОВЕРХНОСТЬ ПРОБКИ (11) ПРЕДОХРАНИТЬ ОТ ПОВРЕЖДЕНИЙ.
После замены уплотнений провести сборку крана в обратной последовательности.
При сборке крана, обращать внимание за расположением магнита, установленного в указателе (4), по отношению к датчикам, установленным в модуле диагностики (5). Магнит должен располагаться напротив датчика.
В процессе сборки трущиеся и уплотняемые поверхности деталей и узлов «металл-металл», «металл-резина», резьбовые разборные соединения смазать смазкой ЖТ-79Л ТУ 0254-002-01055954.
Кран 026.000-08 (рисунок 12.7.6.3)
Разобрать кран:
- кран подлежит ремонту только в случае появления утечек;
- отвернуть болт (14) крепления рукоятки (17), снять рукоятку (17);
- выкрутить винты (13), снять модуль диагностики (5), извлечь шпиндель (3), указатель (4) и шайбу (6);
- вывернуть заглушку (7) и последовательно извлечь резиновые кольца (10), фторопластовые кольца (12) и пробку (11).
- проверить состояние резиновых уплотнительных изделий в соответствии с таблицей 12.7.6.1;
- заменить фторопластовые уплотнения. После замены уплотнений из фторопласта необходимо прогреть кран в крайнем положении «закрыто» в печке при температуре + 60 °C в течение 1 ч и выдержать кран в течение 24 ч при комнатной температуре. Должна быть обеспечена герметичность затвора корпуса и мест соединений при рабочем давлении;
- собрать кран;
- проверить прочность резьбовых соединений после сборки.
ВНИМАНИЕ
ПОВЕРХНОСТЬ ПРОБКИ (11) ПРЕДОХРАНИТЬ ОТ ПОВРЕЖДЕНИЙ.
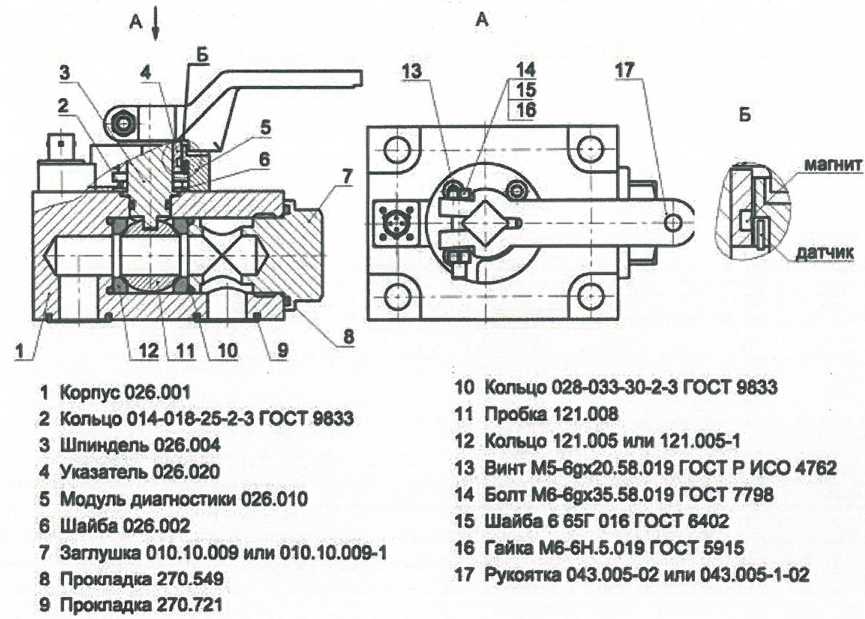
Рисунок 12.7.6.3 – Кран 026-08
После замены уплотнений провести сборку крана в обратной последовательности.
При сборке крана, обращать внимание за расположением магнита, установленного в указателе (4), по отношению к датчикам, установленным в модуле диагностики (5). Магнит должен располагаться напротив датчика.
В процессе сборки трущиеся и уплотняемые поверхности деталей и узлов «металл-металл», «металл-резина», резьбовые разборные соединения смазать смазкой ЖТ-79Л ТУ 0254-002-01055954.
Кран 026.000-1-06 (рисунок 12.7.6.4)
Разобрать кран:
- кран подлежит ремонту только в случае появления утечек;
- отвернуть болт (13) крепления рукоятки (12), снять рукоятку (12);
- отвернуть винты крепления крышки (10);
- снять крышку (10) и извлечь шпиндель (3);
- вывернуть заглушку (4) и последовательно извлечь резиновые кольца (7), фторопластовые кольца (9) и пробку (8).
- проверить состояние резиновых уплотнительных изделий в соответствии с таблицей 12.7.6.1;
- заменить фторопластовые уплотнения. После замены уплотнений из фторопласта необходимо прогреть кран в крайнем положении «закрыто» в печке при температуре + 60 °C в течение 1 ч и выдержать кран в течение 24 ч при комнатной температуре.
ВНИМАНИЕ
ПОВЕРХНОСТЬ ПРОБКИ (8) ПРЕДОХРАНИТЬ ОТ ПОВРЕЖДЕНИЙ
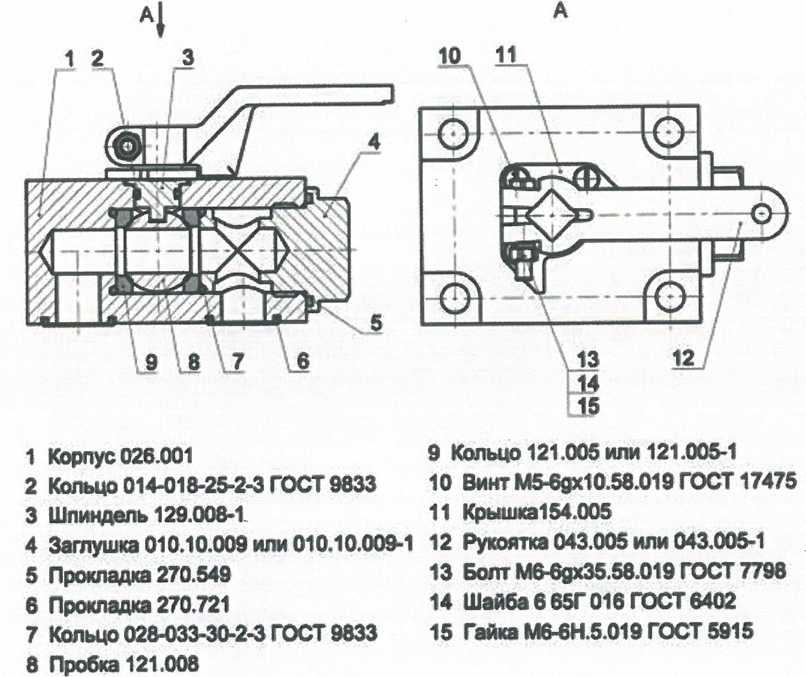
Рисунок 12.7.6.4 – Кран 26-1-06
Должна быть обеспечена герметичность затвора корпуса и мест соединений при рабочем давлении;
- собрать кран;
- проверить прочность резьбовых соединений после сборки.
После замены уплотнений провести сборку крана в обратной последовательности.
В процессе сборки трущиеся и уплотняемые поверхности деталей и узлов «металл-металл», «металл-резина», резьбовые разборные соединения смазать смазкой ЖТ-79Л ТУ 0254-002-01055954.
Собрать БПО 425, после сборки необходимо проверить на соответствие показателей таблицы 12.7.6.3.
Наименование характеристики | Значение |
1 Время наполнения сжатым воздухом резервуара от 0 до давления 0,49 МПа при открытии крана КрРШ1, с, не более | 3 |
2 Время наполнения сжатым воздухом резервуара от 0 до давления 0,49 МПа при открытии крана КрРШ2, с, не более | 3 |
3 Время наполнения сжатым воздухом резервуара от 0 до давления 0,49 МПа при открытии крана КрРШ3, с, не более | 3 |
4 Время наполнения сжатым воздухом резервуара от 0 до 0,49 МПа при открытии крана КрРШ4, с, не более | 3 |
5 Должна быть обеспечена герметичность плиты-кронштейна, мест соединений навесных приборов, атмосферных отверстий | Пропуск воздуха не допускается |
6 Работоспособность диагностики положения разобщительных кранов КрРШ2, КрРШ3, КрРШ4 | Пропуск воздуха не допускается |
Давление в ПМ, подводимое к БПО 425, должно быть в диапазоне (0,83 -0,98) МПа ((8,5 – 10,0) кгс/см2).
Регуляторы положения кузова 003ММ, 003ММ-01, 003ММ-02, 003ММ-03 (РПК) для автоматического поддержания заданного уровня высоты кузова от головки рельса независимо от величины нагрузки на пневморессору.
При ремонте РПК заменить все резиновые уплотнительные изделия, указанные в таблице 12.7.7.1.
Таблица 12.7.7.1 – Перечень резиновых уплотнительных изделий и вулканизированных клапанов
Месторасположение | Наименование | Обозначение | Количеств о на изделие | Примечание | |
Рисунок | Позиция | ||||
12.7.7.1 | 3 | Клапан (резина группы 3 (7-7130) ТУ 2539-054-05766882 | 003М.030-1 вулканизированный клапан | 2 | Неразборное соединение |
11 | Кольцо ГОСТ 9833 | 021-025-25-2-3 | 1 | ||
13 | Кольцо ГОСТ 9833 | 017-021-25-2-3 | 2 | ||
23 | Кольцо ГОСТ 9833 | 010-014-25-2-3 | 1 | ||
Регулятор положения кузова 003ММ-02 | |||||
12.7.7.3 | 3 | Кольцо ГОСТ 9833 | 010-014-25-2-3 | 1 |
При ремонте РПК провести проверку пружин в соответствии с таблицей 12.7.7.2.
Пружины необходимо заменить при наличии отклонений от контрольных значений параметров, наличии любых внешних повреждений (изломов, трещин и т. д.).
Таблица 12.7.7.2 – Перечень пружин РПК
Месторасположение | Обозначение | Средства измерений | Контрольные значения параметров | |
Рисунок | Позиция | |||
12.7.7.1 | 2 | 150.203-1 | Машина для испытания пружин (МИП), штангенциркуль | F1=34±3,4 Н (3,48±0,18 кгс) 11=14,5 мм
F2=51±5,1 Н (5,22±0,26 кгс) 12=13 ММ |
При ремонте РПК продуть сжатым воздухом все сетчатые фильтры (заменить при наличии повреждений).
Порядок текущего ремонта РПК 003ММ (рисунки 12.7.7.1 – 12.7.7.4)
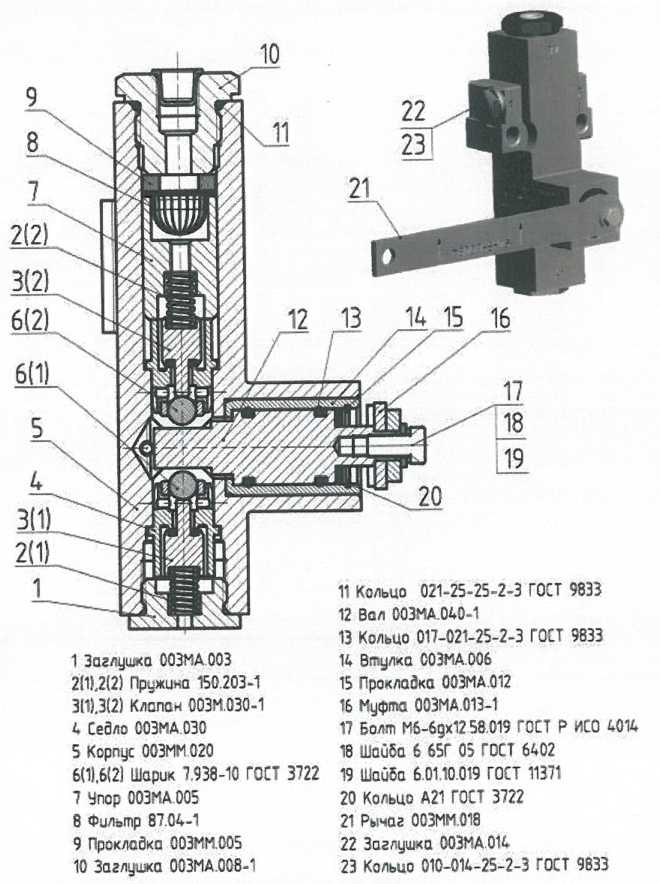
Рисунок 12.7.7.1 – Регулятор положения кузова 003ММ
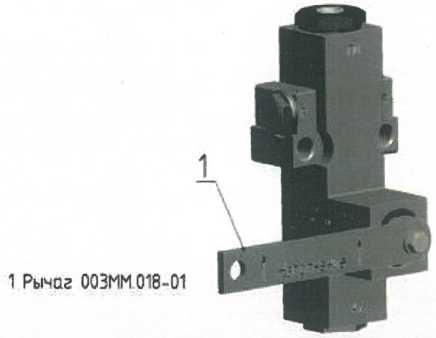
Рисунок 12.7.7.2 – Регулятор положения кузова 003ММ-01

Рисунок 12.7.7.3 – Регулятор положения кузова 003ММ-02
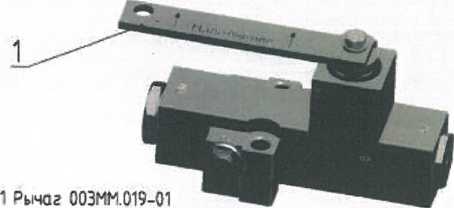
Рисунок 12.7.7.4 – Регулятор положения кузова 003ММ-03
Разобрать РПК:
- отвернуть болт (17) и снять с вала (12) последовательно шайбы (18 и 19), рычаг (21) и муфту (16);
- извлечь стопорное кольцо (20), затем прокладку (15) и вал (12) с уплотнительными кольцами (13). Кольца снять с вала;
- извлечь шарики (6);
- из корпуса (5) вывернуть заглушку (10) и снять с нее уплотнительное кольцо (11), последовательно извлечь из корпуса прокладку (9), фильтр (8), упор (7), пружину (2(2)) и клапан питательный (3(2));
- из корпуса (5) вывернуть заглушку (1). Извлечь пружину (2(1)) и клапан (3(1));
- из корпуса (5) вывернуть заглушку (22) и снять с нее уплотнительное кольцо (23).
После разборки РПК его детали, кроме резиновых уплотнительных изделий, промыть моющими средствами, каналы продуть сжатым воздухом. Очищенные детали протереть насухо.
Проверить визуально состояние деталей.
Произвести очистку сетчатых фильтров, при наличии повреждений фильтры заменить.
Собрать РПК, в процессе сборки трущиеся и уплотняемые поверхности деталей и узлов «металл-металл», «металл-резина», резьбовые разборные соединения смазать смазкой ЖТ-79Л ТУ 0254-002-01055954.
После сборки РПК, его необходимо проверить на соответствие показателей таблицы 12.7.7.3.
Таблица 12.7.7.3 – Характеристики РПК
Наименование характеристики | Значение* |
1 Холостой ход РПК (зона нечувствительности), соответствующий величине перемещения оси конца привода рычага РПК от положения начала наполнения пневморессоры до положения начала разрядки, мм | 10±2 |
2 Время наполнения резервуара при полном открытии клапана от 0 до 0,59 МПа, с, не более | 20 |
3 Время разрядки резервуара при полном открытии клапана от 0,59 до 0,03 МПа, с, не более | 45 |
4 Изменение давления в резервуаре при нейтральном положении рычага и исходном давлении 0,29 МПа за 1 мин, МПа, не более | 0,02 |
5 Герметичность мест соединений сборочных единиц и деталей | Пропуск воздуха не допускается |
Примечание – * Характеристики РПК, приведенные в таблице 12.7.7.3, установлены применительно к условиям стендовых испытаний.
Давление в ПМ, подводимое к РПК, должно быть в диапазоне (0,66 -0,98) МПа.
Клапан аварийного экстренного торможения 130.30 (КАЭТ)
Произвести ревизию клапана, при необходимости, замену отдельных узлов и деталей, испытания и регулировку.
Заменить резиновые уплотнительные изделия по достижению назначенного срока службы (уплотнения и манжеты – 4 года, прокладки -5 лет), который устанавливается, не считая 12 месяцев от даты изготовления, указанной на резиновом изделии (паспорте на партию изделий) или по дате изготовления клапана, указанной на корпусе, или по дате проведения последнего ремонта клапана. Резиновые уплотнительные изделия, имеющие надрывы и трещины, а также с истекшим сроком службы, заменить новыми. Перечень резиновых уплотнительных изделий приведен в таблице 12.7.8.1.
Таблица 12.7.8.1 – Перечень резиновых уплотнительных изделий КАЭТ
Месторасположение | Наименование | Обозначение | Количество на изделие | Примечание | |
Рисунок | Позиция | ||||
12.7.8.1 | 3 | Прокладка | 404.007 | 1 | |
5 | Манжета воздухораспределителя | 120.07.2 | 1 | ||
25 | Кольцо ГОСТ 9833 | 028-033-30-2-3 | 2 | ||
27 | Манжета крана машиниста | 265.133 | 1 | ||
29 | Прокладка | 305.155 | 1 |
Пружины при наличии изломов, трещин, а также в случае потери упругости или при просадке по высоте заменить. Проверку проводить в свободном состоянии. Растягивание и заделка пружин не допускаются.
Проверка работоспособности пружин приведена в таблице 12.7.8.2.
Таблица 12.7.8.2 – Параметры пружин КАЭТ
Месторасположение | Обозначение | Средства измерений | Контрольные значения параметров | |
Рисунок | Позиция | |||
12.7.8.1 | 14 | 150.203 | Машина для испытания пружин (МИП), штангенциркуль | F1=3,48±0,18 кгс; 11=14,5 мм F2=5,22±0,26 кгс; 12=13 мм Lсв=17±0,6 мм |
21 | 130.30.022 | F1=2,64±0,26 кгс; 11=21 мм F2=5,94±0,59 кгс; 12=11 мм Lсв=29 ±1,2 мм |
||
28 | 270.774 | F1=5,24±0,524 кгс; 11=18 мм F2=6,045 ±0,604 кгс; 12=16 мм Lсв=31±0,8 мм |
Произвести демонтаж клапана (рисунок 12.7.8.1), разборку ремонт и сборку.
Вывернуть винт (19) и снять кнопку (15), затем отвернуть гайку (18) и выбить штифт (16), вынуть и снять втулку (17). Снять кожух (37), отвернуть винты (12). Проверить пайку штепсельного разъема (4) к проводам и проводов к выключателю (10). Отвернуть винты (12) крепления кронштейна (8) выключателя (10) на корпусе клапана (1). Отвернуть упорку (11), вынуть толкатель (9) и пружину (14). Проверить состояние толкателя (9) и пружины (14), при износе заменить. Вывернуть упорку (22) и пружину (21), вывернуть заглушку (30). Вынуть клапан (2), очистить и продуть корпус (1). Проверить состояние резиновых уплотнительных изделий в соответствии с п.п. 12.7.8.1. Проверить пружины в соответствии с п.п. 12.7.8.2. Собрать клапан в порядке, обратном разборке, в процессе сборки смазать трущиеся поверхности «металл-металл» и «металл-резина» тонким слоем смазки ЖТ-79Л ТУ 0254-002-01055954.
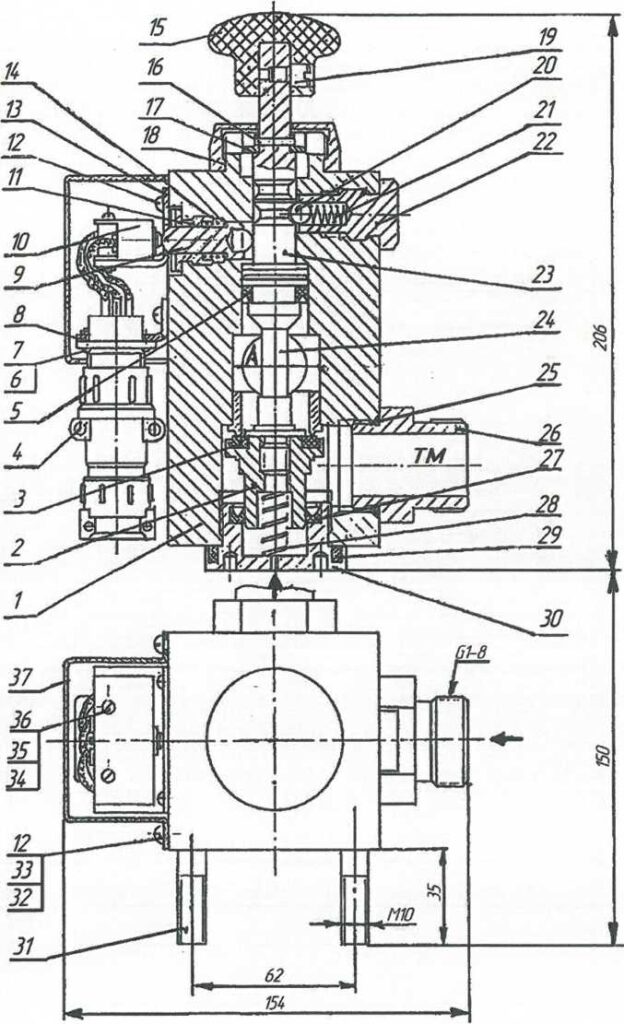
Рисунок 12.7.8.1 – Клапан аварийного экстренного торможения 130.30: 1 – корпус 130.30.010; 2 – клапан 130.30.020; 3 – прокладка 404.007; 4 – разъем 130.30.040; 5 – манжета воздухораспределителя 120.07.2; 6 – гайка М3-6Н.5.016; 7 – винт ВМ3-6gx10.36.016; 8 – кронштейн 130.30.011; 9 – толкатель 130.30.007; 10 – выключатель БВПЛ-401; 11 – упорка 130.30.005; 12 – винт BM5-6gx12.36.016; 13 – кронштейн 130.30.016; 14 – пружина 130.30.022; 15 – кнопка 130.30.014; 16 – штифт 130.30.017; 17 – втулка 130.30.008; 18 – гайка 130.30.004; 19 – винт 130.30.009; 20 – шарик 7938-10; 21 – пружина 150.203; 22 – упорка 130.30.006; 23 – шток 130.30.015; 24 – поршень 130.30.017; 25 – кольцо 028-033-30-2-3; 26 – штуцер 130.30.012; 27 – манжета крана машиниста 265.133; 28 – пружина 270.774; 29 – прокладка 305.155; 30 – заглушка 130.30.030; 31 – шпилька М10-6gx35.A05; 32 – шайба 5.01.10.019; 33 – шайба 5.65Г 05; 34 – шайба 4.01.10.019; 35 – гайка М4-6Н.5.016; 36 – винт BM4-6gx10.36.016; 37-кожух 130.30.013
После сборки произвести регулирование и испытание клапана на стенде (рисунок 12.7.8.2).
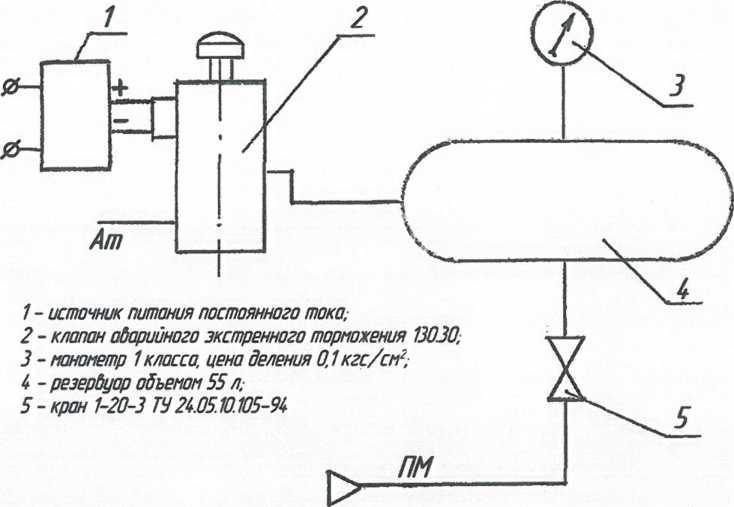
Рисунок 12.7.8.2 – Стенд для испытания КАЭТ
Подвести сжатый воздух и провести испытание клапана на соответствие требований таблицы 12.7.8.3.
Испытание проводить при давлении в ПМ (0,6 -0,7) МПа ((6,0 – 7,0) кгс/см2).
Таблица 12.7.8.3 – Проверка параметров клапана
№ п/п | Наименование параметра | Значение |
1 | При нажатии на кнопку
Время снижения давления в резервуаре объемом 55 л с 0,5 до 0,1 МПа, с. При этом должно произойти размыкание контактов выключателя |
2, не более |
2 | Должна быть обеспечена герметичность мест соединений при обмыливании | Образование мыльных пузырей не допускается |
3 | Должна быть обеспечена плотность клапана | Пропуск воздуха не допускается |
Для испытания по п. 1 таблицы 12.7.8.3 открыть разобщительный кран на ПМ и наполнить резервуар объемом 55 л до давления (0,53 – 0,55) МПа и закрыть кран. Далее нажать кнопку клапана – должна произойти разрядка резервуара. Замер времени производить секундомером. Одновременно должна погаснуть лампа на стенде.
Для испытания по п. 2 таблицы 12.7.8.3 наполнить резервуар до давления 0,7 МПа и обмылить корпус и места соединений.
Для испытания по п. 3 таблицы 12.7.8.3 после наполнения резервуара закрыть разобщительный кран, через 30 с замерить падение давления в резервуаре в течении 1 мин.
После установки на электропоезд клапан должен быть подвергнут повторным испытаниям, независимо от проведенных испытаний на стенде.
Клапан электропневматический экстренного торможения дистанционного управления 266-1 (КЭЭТ)
Произвести ревизию клапана, при необходимости, замену отдельных узлов и деталей, испытания и регулировку.
Заменить резиновые уплотнительные изделия по достижению назначенного срока службы (уплотнения и манжеты – 4 года, прокладки -5 лет), который устанавливается, не считая 12 месяцев от даты изготовления, указанной на резиновом изделии (паспорте на партию изделий) или по дате изготовления клапана, указанной на корпусе, или по дате проведения последнего ремонта клапана. Резиновые уплотнительные изделия, имеющие надрывы и трещины, а также с истекшим сроком службы, заменить новыми. Перечень резиновых уплотнительных изделий приведен в таблице 12.7.9.1.
Таблица 12.7.9.1 – Перечень резиновых уплотнительных изделий КЭЭТ
Месторасположение | Наименование | Обозначение | Количество на изделие | Примечание | |
Рисунок | Позиция | ||||
Клапан электропневматический экстренного торможения с дистанционным управлением 266 | |||||
12.7.9.1 | 11 | Уплотнение | 334.1729А-2 | 1 | |
13 | Уплотнение клапана | 270.357 | 2 | ||
16 | Прокладка | 216.1496 | 1 | ||
Клапан срывной 266.060 | |||||
12.7.9.2 | 2 | Кольцо ГОСТ 9833 | 021-025-25-2-3 | 1 | |
5 | Кольцо ГОСТ 9833 | 010-014-25-2-3 | 1 | ||
13 | Манжета крана машиниста | 222.11 | 1 | ||
15 | Манжета воздухораспределителя | 270.317 | 1 | ||
17 | Прокладка | 150.01.009 | 1 | ||
18 | Уплотнение клапана | 270.357 | 1 | ||
23 | Прокладка | 270.549 | 2 | ||
24 | Кольцо ГОСТ 9833 | 055-060-30-2-3 | 1 | ||
Кронштейн 266.010-2, 266А.010 | |||||
12.7.9.3 | 2 | Кольцо ГОСТ 9833 | 028-033-30-2-3 | 1 |
Пружины при наличии изломов, трещин, а также в случае потери упругости или при просадке по высоте заменить. Проверку проводить в свободном состоянии. Не допускаются растягивание и заделка пружин. Проверка работоспособности пружин приведена в таблице 12.7.9.2.
Таблица 12.7.9.2 – Параметры пружин КЭЭТ
Месторасположение | Обозначение | Средства измерений | Контрольные значения параметров | |
Рисунок | Позиция | |||
12.7.9.2 | 8 | 254.14 | Машина для испытания пружин (МИП), штангенциркуль | F1=1,1±0,01 кгс; 11=21 мм F2=2,5±0,25 кгс; 12=11 мм Lcb=29±1,2 мм |
14 | 130.10.092 | F1=2,13±0,21 кгс; 11=11 мм F2=2,3±0,23 кгс; 12=9 мм Lcb=37±0,7 мм |
Произвести демонтаж клапана (рисунок 12.7.9.1), разборку ремонт и сборку.
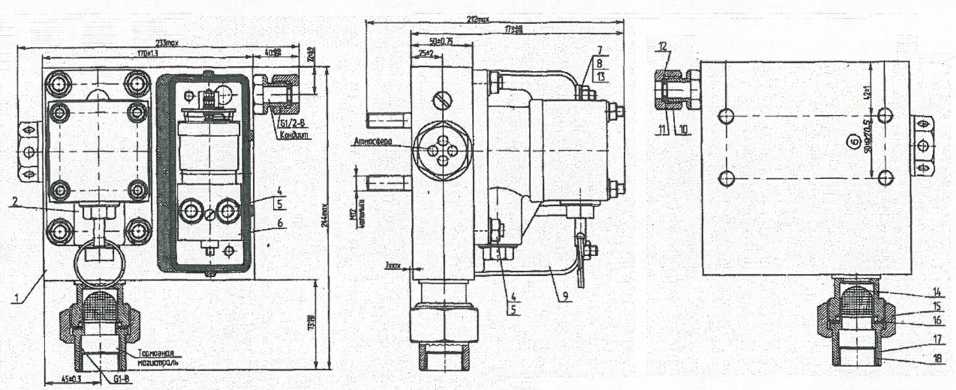
Рисунок 12.7.9.1 – Клапан электропневматический экстренного торможения с дистанционным управлением 266А-1: 1 – кронштейн 266А.010; 2 – клапан срывной 266.060; 4 – гайка М10; 5 – шайба 10.01.10.019; 6 – вентиль электропневматический 120; 7 – гайка М8; 8 – шайба 8.01.10.019; 9 – крышка 266.050; 10 – гайка накидная334.1730; 11 – уплотнение 334.1729А-2; 12 – прокладка тип 1 СТП 10-205-2001; 13 – уплотнение клапана 270.357; 14 – фильтр 216.1497С; 15 – гайка накидная 216.1494А; 16 – прокладка 216.1496; 17 – наконечник 216.1495Б; 18 – пробка 325.151-05
Демонтировать клапан:
- снять навесные изделия с кронштейна (1);
- отвернуть гайки (4 и 7);
- снять срывной клапан (2);
- снять крышку (9);
- снять ЭПВ (6), предварительно отсоединив кабель от контактной колодки.
Проверить состояние резиновых уплотнительных изделий в соответствии с таблицей 12.7.9.1. Прочистить и, при необходимости, заменить фильтр (14) и крышку (9). Кронштейн (1) – несъемная часть клапана. После снятия всех навесных приборов кронштейн (1) очистить и продуть сжатым воздухом.
Клапан срывной 266.060 (рисунок 12.7.9.2):
- отвернуть гайки (10);
- снять крышку (26), из крышки вывернуть упорку (7), затем снять кольцо (3) и извлечь фиксатор (4) с пружиной (8);
- извлечь манжету (13);
- в корпусе (25) снять прокладку (23) и уплотнение клапана (18);
- извлечь поршень (16), с поршня снять манжету (15) и отвернуть гайку (20).
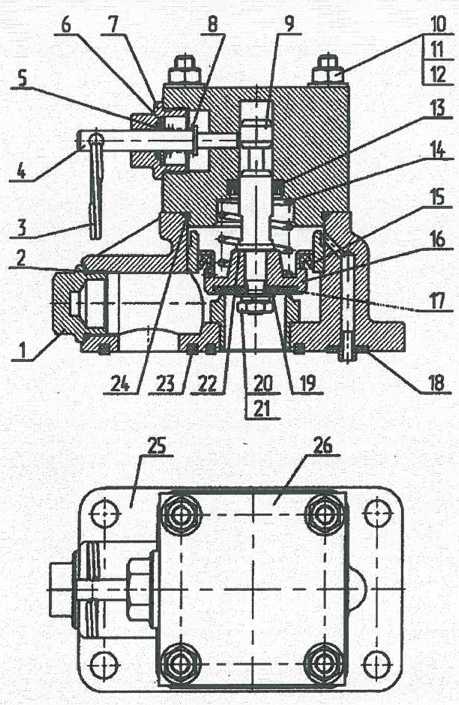
Рисунок 12.7.9.2 – Клапан срывной 266.060: 1 – заглушка 254.27; 2 – кольцо 021-025-25-2-3; 3 – кольцо 150.03.130; 4 – фиксатор 266.030-2; 5 – кольцо 010.014.25.2.3; 6 – шайба 150.129; 7 – упорка 266.005-1; 8 – пружина 254.14; 9 – поршень 266.020-1; 10 – гайка М8; 11 – шайба 8.01.10.019; 12 – шпилька 266.012; 13 – манжета крана машиниста 222.11; 14 – пружина 130.10.092; 15 – манжета воздухораспределителя 270.317; 16 – поршень 150.01.121; 17 – прокладка 150.01.009; 18 – уплотнение клапана 270.357; 19 – шайба 1.МЮ.37М; 20 – гайка 2М8; 21 – шайба 8.65Г.019; 22 – шайба 150.144; 23 – прокладка 270.549; 24 – кольцо 055-060-30-2-3; 25 – корпус 266.040; 26 – крышка 266.002-2
Проверить состояние резиновых уплотнительных изделий в соответствии с таблицей 12.7.9.1. Новое резиновое уплотнение (17) поставить на клей 88-СА ТУ 38.1051760.
Проверить пружины в соответствии с таблицей 12.7.9.2.
Собрать клапан в порядке, обратном разборке, в процессе сборки смазать трущиеся поверхности «металл-металл» и «металл-резина» тонким слоем смазки ЖТ-79Л ТУ 0254-002-01055954.
Разборку и сборку ЭПВ произвести в соответствии с требованиями «Руководства по эксплуатации 120.000 РЭ».
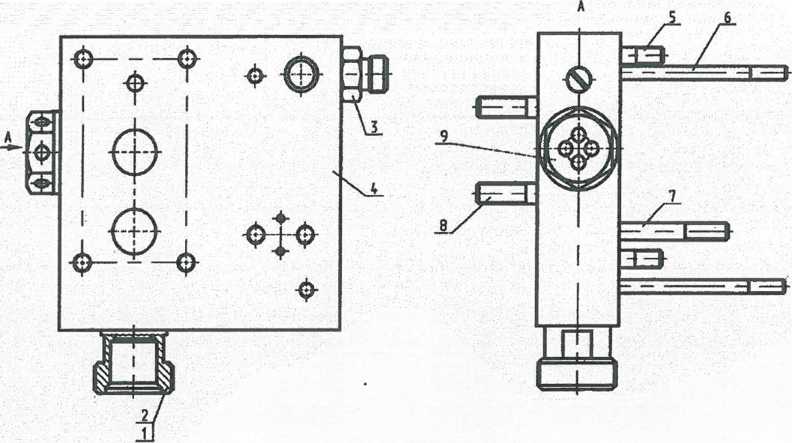
Рисунок 12.7.9.3 – Кронштейн 266.010-2: 1 – штуцер 153.024; 2 – кольцо 028-033-30-2-3; 3 – штуцер 266.007; 4 – плита 266.070-1; 5 – шпилька М10; 6 – шпилька 266.013; 7 – шпилька М10; 8 – шпилька M12; 9 – цоколь 266.006-1
Регулирование и испытание
Собранные узлы установить на кронштейн, подвести сжатый воздух и подсоединить электрический кабель с контактными колодками ЭПВН.
Провести испытания на соответствие требований таблицы 12.7.9.3.
Таблица 12.7.9.3 – Проверка параметров клапана
№ п/п | Наименование параметра | Значение |
1 | При подаче сигнала
Время снижения давления в резервуаре объемом 55 л с 0,5 до 0,25 МПа, с, не более |
2 |
2 | Должна быть обеспечена фиксация клапана в открытом состоянии после его срабатывания | |
3 | Должна быть обеспечена герметичность мест соединений при обмыливании | Образование мыльных пузырей не допускается |
4 | Должна быть обеспечена плотность клапана | Снижение давления в резервуаре не допускается |
5 | Должно обеспечиваться закрытое состояние клапана (без подрыва) при повышении давления в ТМ до 0,7 МПа включительно | Снижение давления в резервуаре не допускается |
Испытание проводить при давлении в питательной магистрали (0,6 -0,8) МПа.
Для испытания по п. 1 таблицы 12.7.9.3 открыть разобщительный кран на ПМ и наполнить резервуар объемом 55 л до давления 0,5 МПа и закрыть кран. Далее для клапанов электропневматических 266-1 подать (266А-1 снять) напряжение постоянного тока величиной соответствующего номинального напряжения ЭПВ. Замерить время снижения давления в резервуаре с 0,5 МПа до 0,25 МПа.
Испытание по п. 2 таблицы 12.7.9.3 выполнить после испытания по п. 1. Подать напряжение на вентиль. Продолжающееся дутье в атмосферный канал свидетельствует о фиксации клапана в открытом положении. Далее оттянуть за кольцо фиксатор – дутье должно прекратиться.
Испытания по п. 3 таблицы 12.7.9.3 провести при давлении в резервуаре 0,7 МПа.
Для испытания по п.4 таблицы 12.7.9.3 после наполнения резервуара до давления 0,7 МПа закрыть разобщительный кран. Через 30 с замерить падение давления в резервуаре в течении 1 мин.
Для испытания по п. 5 таблицы 12.7.9.3 открыть разобщительный кран, наполнить резервуар стенда объемом 55 л от 0,7 МПа. Наполнение резервуара должно происходить при закрытом клапане (без обрыва). Через 30 с замерить снижение давления в резервуаре в течении 1 мин.
Установленный на электропоезд клапан независимо от проведенных испытаний должен быть подвергнут повторным испытаниям.
Электропневматический клапан автостопа 153А-01 (ЭПК) с блоком КОН
Провести ревизию съемных частей ЭПК.
При необходимости провести ремонт и замену отдельных узлов и деталей, гарантирующих их работоспособность между соответствующими видами ремонта. Резиновые уплотнительные изделия заменить по достижению назначенного срока службы:
- уплотнений и манжет – 4 года;
- прокладок – 5 лет.
Назначенный срок службы устанавливается, не считая 12 месяцев от даты изготовления, указанной на резиновом уплотнительном изделии (паспорте на партию изделий) или по дате изготовления ЭПК, указанной на кронштейне (33) в соответствии с рисунком 12.7.10.2, устанавливается по ТУ 2539-170-00152106.
Резиновые уплотнительные изделия, имеющие надрывы, трещины, а также с истекшим сроком службы, заменить новыми. Перечень резиновых уплотнительных изделий приведен в таблице 12.7.10.1.
Полный установленный срок службы резиновых уплотнительных колец 5 лет (ГОСТ 18829).
Таблица 12.7.10.1 – Перечень резиновых уплотнительных изделий
местоположение | наименование | обозначение | кол-во на изделие | примечание | |
рисунок | позиция | ||||
Клапан электропневматический автостопа 153А | |||||
12.7.10.2 12.7.10.3 |
7 | Уплотнение | 334.1729А-2 | 1 | |
25 | Прокладка | 216.1496 | 1 | ||
29 | Кольцо ГОСТ 9833 | 028-033-30-2-3 | 2 | ||
30 | Прокладка | 270.549 | 2 | ||
32 | Прокладка крышки | 86.13 | 1 | ||
Кронштейн 153.010 | |||||
12.7.10.4 | 5 | Кольцо ГОСТ 9833 | 014-018-25-2-3 | 2 | |
9 | Кольцо ГОСТ 9833 | 006-010-25-2-3 | 1 | ||
Клапан срывной 153.020 | |||||
12.7.10.5 | 2 | Кольцо ГОСТ 9833 | 055-060-30-2-3 | 1 | |
7 | Манжета воздухораспределителя | 270.317 | 1 | ||
10 | Уплотнение клапана | 270.357 | 1 | ||
12 | Прокладка | 150.01.009 | 1 | ||
13 | Прокладка | 270.549 | 2 | ||
15 | Кольцо ГОСТ 9833 | 021-025-25-2-3 | 1 | ||
Замок 153.030-1 | |||||
12.7.10.6 | 2 | Уплотнение клапана | 270.357 | 2 | |
6 | Кольцо ГОСТ 9833 | 014-018-25-2-3 | 1 | ||
8 | Кольцо ГОСТ 9833 | 021-025-25-2-3 | 1 | ||
9 | Кольцо ГОСТ 9833 | 006-010-25-2-3 | 1 | ||
Выключатель управления автоматический 153А.040 | |||||
12.7.10.7 | 6 | Манжета воздухораспределителя | 120.07.2 | 2 | |
9 | Манжета | 270.769 | 2 | ||
10 | Уплотнение клапана | 270.753 | 1 | Неразъемное соединение – заменить клапан 153.070 целиком | |
26 | Уплотнение | 270.711 | 1 | ||
33 | Уплотнение клапана | 270.357 | 2 | ||
Вентиль электропневматический 175 | |||||
12.7.10.8 | 27 | Прокладка | 305.134 | 3 | Неразъемное соединение – заменить клапан 175.020-01 и клапан 120.003 целиком |
30 | Манжета воздухораспределителя | 337.321 | 1 | ||
32 | Манжета | 270.769 | 2 | ||
33 | Кольцо ГОСТ 9833 | 021-025-25-2-3 | 1 | ||
35 | Кольцо ГОСТ 9833 | 014-018-25-2-3 | 1 | ||
38 | Кольцо ГОСТ 9833 | 006-010-25-2-3 | 2 | ||
43 | Кольцо ГОСТ 9833 | 028-033-30-2-3 | 1 | ||
44 | Прокладка | 348.216 | 1 |
Пружины при наличии изломов, трещин, а также в случае потери упругости или при просадке по высоте заменить Проверку пружин выполнять в свободном состоянии при помощи машины для испытания пружин и штангенциркуля. Не допускаются растягивание и заделка пружин. Проверка работоспособности пружин приведена в таблице 12.7.10.2.
Таблица 12.7.10.2 – Проверка работоспособности пружин
местоположение | обозначение | контрольные значения параметров | |
рисунок | позиция | ||
Клапан срывной 153.020 | |||
12.7.10.5 | 4 | 150.01.014 | P1=23,7±2,37 кгс; H1=29 мм P2=34±3,4 кгс; Н2=21 мм Нсв=47±3 мм |
Выключатель управления автоматический 153А.040 | |||
12.7.10.7 | 3 | 153А.009 | P1=13,4±1,34 кгс; H1=26 мм P2=17±1,7 кгс; Н2=23 мм |
12 | 045.001 | P1=2,33±0,2 кгс; H1=10 мм Р2=0,85±0,28 кгс; Н2=8 мм Нсв = 19 ±0,8 мм |
|
15 | 170.02.17 | P1=0,6±0,06 кгс; H1=13 мм Рг2=1,05±0,1 кгс; Н2=10 мм Нсв =17 ±0,9 мм |
|
Вентиль электропневматический 175 | |||
12.7.10.8 | 29 | 150.218 | P1=0,57±0,057 кгс; H1=15 мм Р2=0,74±0,07 кгс; Н2=13 мм Нсв=22±0,8 мм |
ЭПК демонтировать с электропоезда и разобрать:
- повернуть ключ (1) в рабочее положение (носик ключа должен быть повернут влево), снять заглушку (2), отвернуть винт (3), извлечь шайбы (4, 5), снять ключ (рисунок 12.7.10.1).
- с кронштейна (33) снять кожух (22) и все узлы, находящиеся под кожухом: клапан срывной (37), АВУ (1), свисток (20), замок (16) и ЭПВ (19) (рисунки 12.7.10.2 и 12.7.10.3).
Рисунок 12.7.10.1 – Ключ: 1 – ключ 153.012; 2 – заглушка 133.002; 3 – винт B.M5-gxl0.36.019 ГОСТ 17473; 4 – шайба; 5 65Г.019 ГОСТ 6402; 5 – шайба Х3.10330М; 6 – шпиндель 153.011; 7 – штифт 153.043; 8 – крышка 153.011
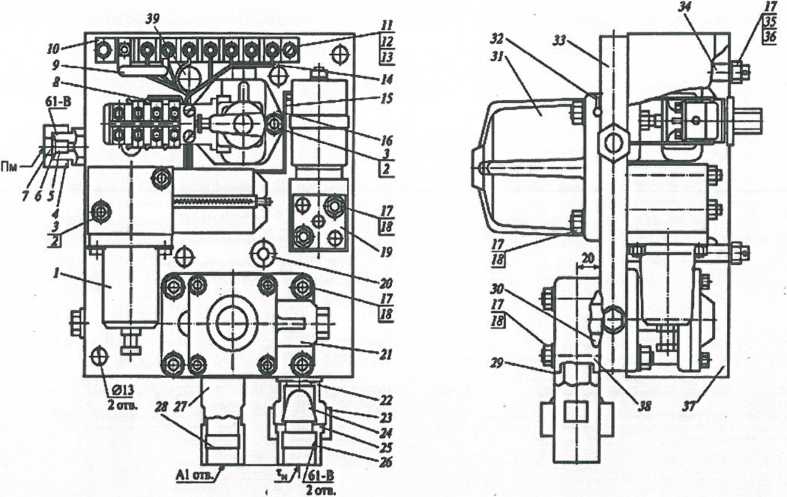
Рисунок 12.7.10.2 – Клапан электропневматический автостопа 153А: 1 – выключатель управления автоматический 153А.040; 2 – вывод 150.590; 3 – гайка М8-6Н.5.019 ГОСТ ISO 4032-2014; 4 – шайба 8.01.10.019 ГОСТ 11371; 5 – гайка накидная 334.1730; 6 – фильтр 305.088; 7 – уплотнение 334.1729А-2; 8 – прокладка 326.223-01; 9 – вывод 153.190; 10 – вывод 153.090; 11 – колодка 164.080; 12 – винт B.M6-6gx20.36.019 ГОСТ 17473; 13 – шайба 6.65Г.019 ГОСТ 6402; 14 – шайба 6.0110.019 ГОСТ 11371; 16 – замок 153.030-1; 17 – гайка М10-6Н.5.019 ГОСТ ISO 4032-2014; 18 – шайба 10.01.10.019 ГОСТ 11371; 19 – вентиль электропневматический175.000-28; 20 – свисток 150.510; 21 – кожух 153А.030; 22 – штуцер 153.024; 23 – гайка накидная 216.1494А; 24 – фильтр 216.1497С; 25 – прокладка 216.1496; 26 – наконечник 216.1495Б; 27 – штуцер 153.025; 28 – пробка 325.151-05; 29 – кольцо 028-033-30-2-3; 30 – прокладка 270.549; 31 – резервуар 153.028; 32 – прокладка крышки 86.13; 33 – кронштейн 153.010; 34 – шпилька 153.048; 35 – шайба 10.65Г.019 ГОСТ 6402; 36 – шайба Г5-12-06; 37 – клапан срывной 153.020; 38 – переходник 153.002; 39 – пробка 153.056
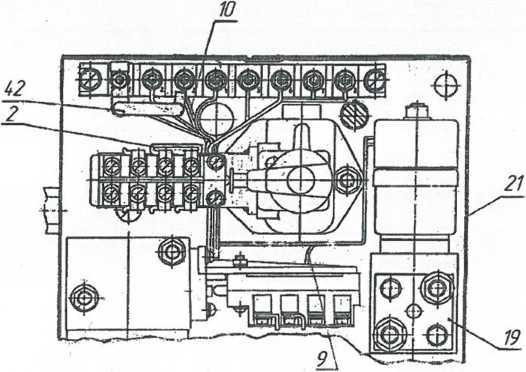
Рисунок 12.7.10.3 – Клапан электропневматический автостопа 153А-01: 2 – вывод 150.590; 10 – вывод 153.090; 19 – вентиль электропневматический 175.000-13 (175.000-14, 175.000-15); 21 – кожух 153А.030-01; 42-резистор с диодом 153.100
Выполнить ремонт составных частей.
Несъемные узлы (рисунок 12.7.10.4):
- каналы кронштейна очистить и продуть сжатым воздухом;
- воздушные фильтры, установленные на ПМ и ТМ, тщательно очистить;
- прочистить дроссельные отверстия дросселей 153.022-01 и 153.022;
- запрещается производить какие-либо изменения размеров калиброванных отверстий, расположенных под фильтром на ПМ, диаметром (0,7±0,03) мм и под резервуаром диаметром (0,8±0,03) мм.
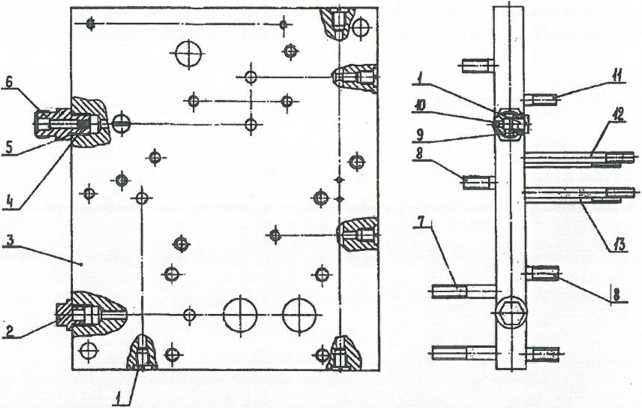
Рисунок 12.7.10.4 – Кронштейн 153.010: 1 – заглушка 153.035; 2 – заглушка 222.135; 3 – плита 153.001; 4 – дроссель 153.022-01; 5 -кольцо 014-018-25-2-3; 6 – штуцер 153.160; 7 – шпилька M10-6gx55.36.10.019 ГОСТ 22034; 8 – шпилька M10-6gx25.36.10.019 СТП 10-215-82; 9 – кольцо 006-010-25-2-3; 10 – дроссель 153.022; 11 – шпилька M8-6gx25.36A.019 ГОСТ 22034; 12 – шпилька M8-6gx85 ГОСТ 22034; 13 – шпилька M10-6gx75 ГОСТ 22034
Клапан срывной (рисунок 12.7.10.5):
- снять крышку (3), извлечь пружину (4) и поршень (11);
- очистить и продуть каналы корпуса (14);
- прочистить калиброванное отверстие поршня (11) диаметром (0,8 ±0,03) мм. Запрещается проводить какие-либо изменения данного отверстия;
- проверить состояние резиновых уплотнительных изделий в соответствии с таблицей 12.7.10.1. Новые резиновые изделия устанавливать на клей 88СА ТУ 38.1051760;
- осмотреть и при необходимости проверить пружину в соответствии с таблицей 12.7.10.2;
- собрать клапан, в процессе сборки смазать поверхности трущихся деталей смазкой ЖТ-79Л ТУ 0254-002-01055954.
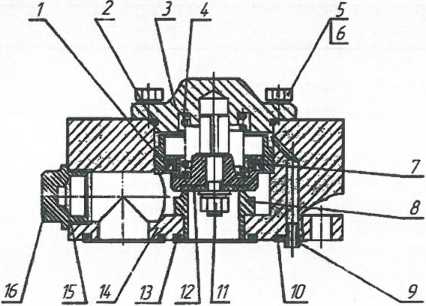
Рисунок 12.7.10.5 – Клапан срывной 153.020: 1 – втулка 153.006; 2 – кольцо 055-060-30-2-3; 3 – крышка 153.003; 4 – пружина 150.01.014; 5 – болт M8-6gx20.36.019 ГОСТ 7808; 6 – шайба 8.01.10.019 ГОСТ 11371; 7 – манжета воздухораспределителя 270.317; 8 – седло клапана 153.004; 9 – ниппель 222.03; 10 -уплотнение клапана 270.357; 11 – поршень 150.01.2; 12 – прокладка 150.01.009; 13 -прокладка 270.549; 14-корпус 153.005-1; 15 – кольцо 021-025-25-2-3; 16-заглушка 254.27
Замок (рисунок 12.7.10.6):
- замок подлежит разборке и ремонту только в случае появления утечек из-за нарушения резиновых уплотнений шпинделя и фторопластовых уплотнений;
- снять выключатель (20) с полкой (21), на которой он установлен, извлечь упорку (19), затем снять крышку (12) и извлечь шпиндель (10) с резиновым кольцом (9);
- отвернуть заглушку (7) и последовательно извлечь резиновые кольца (8 и 6), кольца фторопластовые (5) и шаровую пробку (4). Поверхность шаровой пробки (4) предохранить от повреждений;
- проверить состояние резиновых уплотнительных изделий в соответствии с таблицей 12.7.10.1;
- заменить фторопластовые уплотнения;
- собрать, смазать шпиндель смазкой ЖТ-79Л ТУ 0254-002-01055954 или смазкой ПЛАСМА-Т5 ТУ 0254-006-17432736;
- проверить прочность резьбовых соединений после сборки.
После замены уплотнений из фторопласта необходимо прогреть замок в крайнем положении «закрыто» в печи при температуре ± 60 °C в течении 1 ч и выдержать замок в течении 24 ч при комнатной температуре:
- контактный выключатель замка (20), с помощью которого осуществляется контроль за включением автостопа, отрегулировать так, чтобы размыкание контактов происходило только при ключе (14) повернутом в сторону контактного выключателя. Ключ устанавливать по риске на шпинделе (10) замка.
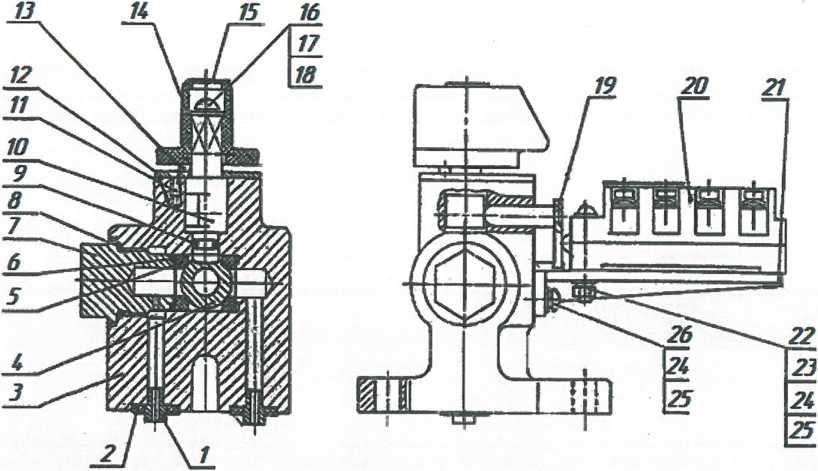
Рисунок 12.7.10.6 – Замок 153.030-1: 1 – ниппель 222.83; 2 – уплотнение клапана 270.357№ 3 – корпус 153.040-1; 4 – пробка 133.006; 5 – кольцо 133.004-1; 6 – кольцо 014-018-25-2-3; 7 – заглушка 153.008; 8 – кольцо 021-025-25-2-3; 9 – кольцо 006-010-25-2-3; 10 – шпиндель 153.009; 11 – винт В М4; 12 – крышка 153.011; 13 – штифт 153.043; 14 – ключ 153.012; 15 – заглушка 133.002; 16 – винт В М5; 17 – шайба 5.65Г.019 ГОСТ 6402; 18 – шайба Х3.10330М; 19 – упорка 153.200-1; 20 – выключатель ВП 19М21Б 411; 21 – полка 153.017-1; 22 – винт В М4; 23 – гайка М4; 24 – шайба 4.65.016 ГОСТ 6402; 25 – шайба 4.01.10.016 Гост 11371; 26 – винт ВМ4
Свисток (20) (рисунки 12.7.10.2 и 12.7.10.3) осмотреть, промыть от масла, попадающего в него сжатым воздухом.
Выключатель управления автоматический (рисунок 12.7.10.7):
- снять крышку (1), извлечь пружину (3), шайбу (4), толкатель (5) с манжетой (6), затем демонтировать стопорное кольцо (7), шайбу (8) с манжетами (9);
- снять шайбу (11), извлечь пружину (12) с клапаном (13);
- снять выключатель (20) с кронштейном (34) и полкой (19) и извлечь пружину (15) и поршень (14) с манжетой (6);
- осмотреть и продуть корпус (31);
- проверить состояние резиновых уплотнительных изделий в соответствии с таблицей 12.7.10.1;
- пружины осмотреть и при необходимости проверить в соответствии с таблицей 12.7.10.2;
- замыкающие контакты концевого выключателя (20) отрегулировать так, чтобы их размыкание производилось после обесточивания ЭПВ;
- собрать и смазать в процессе сборки трущиеся детали смазкой ЦИАТИМ-201 ГОСТ 6267-74.
ЭПВ (рисунок 12.7.10.8): - отвернуть гайку (15);
- снять крышку (10), затем отвернуть штуцер (19), снять колодку с контактами (22), затем катушку (45) в корпусе (8);
- отвернуть винты (28) и снять крышку (7), извлечь прокладку (44) и седло клапана (23);
- отвернуть заглушку (6) с резиновым кольцом (43), извлечь пружину (29) и клапан (41);
- снять крышку (1), извлечь толкатель (31) с манжетой (32), клапан (37);
- демонтировать из корпуса (5) манжету (32);
- очистить и продуть корпус (5);
- проверить состояние резиновых уплотнительных изделий в соответствии с таблицей 12.7.10.1;
- пружины осмотреть, при необходимости проверить в соответствии с таблицей 12.7.10.2;
- собрать, в процессе сборки смазать трущиеся детали смазкой ЖТ-79Л ТУ 0254-002-01055954.
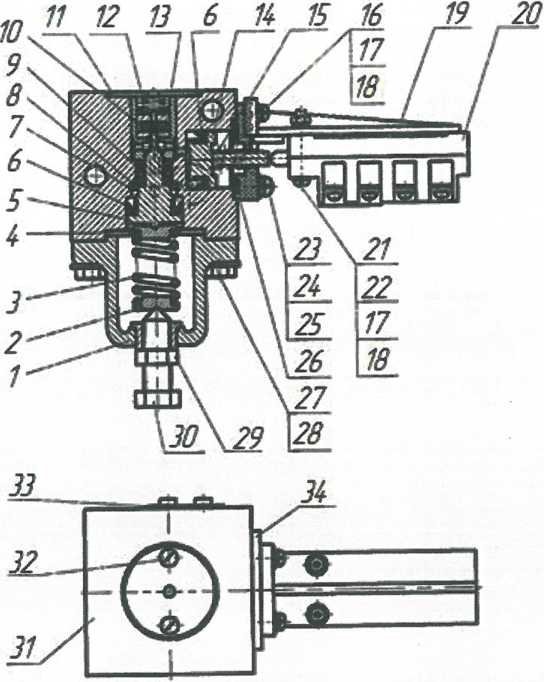
Рисунок 12.7.10.7 – Выключатель управления автоматический 153А.040: 1 – крышка 153А.060; 2 – упорка 153А.007; 3 – пружина 153А.009; 4 – шайба 153А.005; 5 -толкатель 153А.006; 6 – манжета воздухораспределителя 270.769; 7 – кольцо стопорное 153.034; 8 – шайба Х3. 11.35; 9 – пружина 045.001; 10 – уплотнение клапана 270.753; 11 -шайба 045.002; 12 – пружина 045.001; 13 – клапан 153.070; 14 – поршень 045.003; 15 -пружина 170.02.17; 16 – винт В М4; 17 – шайба АЛ65ГО16 ГОСТ 6402; 18 – шайба 4.01.10.016 ГОСТ 11371; 19-полка 153.017-1; 20 – выключатель ВП19М21Б411-00У3.17; 21 – винт В М4; 22 – гайка М4; 23 – винт В М5; 24 – шайба 5Л65Г016 ГОСТ 6402; 25 – шайба 5.01.10.016 ГОСТ 11371; 26 – уплотнение 270.711; 27 – болт 305.308; 28 – шайба 8.01.10.016 ГОСТ 11371; 29 – гайка M12; 30 – винт регулирующий 153А.008; 31 – корпус 153А.050; 32 -винт В М4; 33 – уплотнение клапана 270.357; 34 – кронштейн 045.004
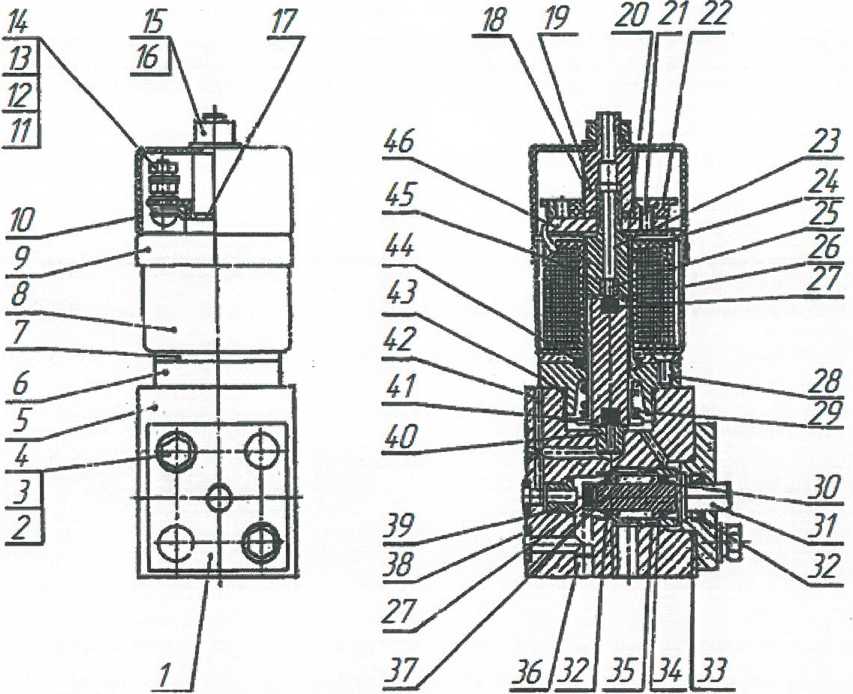
Рисунок 12.7.10.8 – Вентиль электропневматический 175: 1 – крышка 175.011; 2 – шайба 6.01.10.019; 3 – шайба 6.65Г.019; 4 – болт М6; 5 – корпус 175.010; 6 – заглушка 120.013; 7 – крышка 120.026-1; 8 – корпус электромагнита 120.016; 9 -крышка 120.015; 10 – крышка 120.026-1; 11 – шайба 4.01.10.016; 12 – шайба 4.65Г.016; 13 -гайка М4; 14 – винт В М4; 15 – гайка М8; 16 – шайба 8.0110.019; 17 – шайба 8.65Г.019; 18 -трубка 305 ТВ-40А 14 ГОСТ 19034; 19 – штуцер 120.037; 20 – прокладка 120.031; 21 – винт В М4; 22 – колодка 120.029; 23 – седло клапана 120.020-02; 24 – прокладка 120.011-01; 25 -седло 120.004; 26 – шайба 206.012; 27 – прокладка 305.134; 28 – винт В М4; 29 – пружина 150.218; 30 – манжета воздухораспределителя 337.321; 31 – толкатель 175.012; 32 – манжета 270.769; 33 – кольцо 021-025-25-2-3; 34 – втулка 175.009; 35 – кольцо 014-018-25-2-3; 36 -заглушка 175.004; 37 – клапан 175.020-01; 38 – кольцо 006-010-25-2-3; 39 седло 175.003; 40 -седло 175.002; 41 – клапан 120.030; 42 – заглушка 2.3×5 СТП 10-217-2004; 43 – кольцо 028-033-30-2-3; 44 – прокладка 348.216; 45 – катушка 175.110; 46 – шайба 120.017
Собрать ЭПК:
- на кронштейн (33) установить ЭПВ (19), замок (16), свисток (20), АВУ
(1) , клапан срывной (37), затем установить кожух (21) (рисунки 12.7.10.2 и 12.7.10.3); - установить ключ (1) в рабочем положении (носик ключа направлен влево) по риске на шпинделе (6) (риска должна быть в горизонтальной плоскости), установить шайбы (5 и 4), ввернуть винт (3), поставить заглушку (2) (рисунок 12.7.10.1). Для предотвращения поворота ключа на 360 ° штифт (7), ограничивающий поворот ключа, установленный на крышке (8), должен входить в паз, расположенный в нижней плоскости ключа.
Регулирование и испытание
После сборки ЭПВ и установки его на стенд, подать на катушку номинальное напряжение постоянного тока 50 В и замерить сопротивление. Расчетное сопротивление R20 при температуре 20 °C, вычисляется по формуле:
R20 = Rизм х 255 / (235+tв), Ом,
где: Rизм – измеренное значение сопротивления, Ом;
tв – температура воздуха в конце выдержки, °C.
Сопротивление изоляции должно быть для напряжения 50 В – 250 Ом. Отклонение сопротивления при 20 °C допускается в пределах + 6, – 8 %.
После осмотра, ремонта, регулировки и сборки ЭПК необходимо проверить на соответствие техническим требованиям:
- время выдержки ЭПК с момента обесточивания ЭПВ до срабатывания срывного клапана должно составлять (7 + 1) с. Время выдержки регулировать винтом (30) (рисунок 12.7.10.8). При этом звуковой сигнал должен начинаться немедленно от момента обесточивания вентиля и быть непрерывным в течении всего времени выдержки;
- величина остаточного давления в ТМ должна быть (0,13 – 0,20) МПа;
- время снижения давления в ТМ с 0,5 до 0,25 МПа должно быть не более 2 с;
- герметичность мест соединений – пропуск воздуха не допускается;
- при давлении в ПМ (0,6 – 1,0) МПа ((6,0 – 10,0) кгс/см2) понизить напряжение постоянного тока, подаваемое на ЭПВ. Звуковой сигнал должен появиться при напряжении не менее 10% от номинального. Повысить постепенно, начиная от ноля, напряжение постоянного тока, подаваемое на ЭПВ. Отключение звукового сигнала должно произойти при напряжении не более 70 % от номинального.
После установки выполнить работы по проверке ЭПК на электропоезде:
- электропневматический клапан должен быть надежно закреплен на кронштейне и не должен иметь утечек воздуха по месту соединения;
- поворот ключа замка должен происходить свободно без заеданий. Ключ замка должен быть закреплен надежно, выпадение его недопустимо;
- проверить целостность и крепление узлов: срывного клапана, выключателя управления автоматического (АВУ), вентиля электропневматического выключающего (ЭПВ), замка, резервуара, свистка, колодки и выключателя замка. Ослабшие болты и гайки подтянуть. Наконечники проводов должны быть надежно закреплены, касание соседних клемм и наконечников не допускается. Обрыв жил проводов более 10% не допускается. Ослабшие провода закрепить. Мелкие раковины или наплывы на контактах устранить опиловкой надфилем с последующей зачисткой замшей. Не допускается зачищать раковины и наплывы наждачной бумагой. После зачистки поверхность контактов должна быть ровной и обеспечивать соприкосновение по всей поверхности контакта. Проверить наличие диода с резистором шунтирующих катушку ЭПК, их исправность и правильность подключения;
- проверить исправность разобщительных кранов питательной и тормозной магистрали, надежность крепления рукояток на них;
- проверить ЭПК на герметичность при подключенном блоке КОН под давлением (0,7 – 0,8) МПа путем обмыливания мест соединения.
Блок КОН осмотреть:
- очистить от пыли и грязи блок КОН;
- места прилегания резиновых уплотнительных колец вентиля к фланцу трубопровода блока осмотреть, при необходимости кольца заменить;
- блок КОН, соединения воздухопроводов, подводящие провода проверить. На корпусе блоков вмятины, отколы, трещины не допускаются, при их наличии блоки заменить;
- проверить электрическое подключение блока КОН согласно схеме подключений;
- проверить крепление блока. Отключить разъем, осмотреть разъемы блока и кабеля, промыть контакты разъемов кистью, смоченной спиртом, просушить на воздухе в течение 20 мин. В разъемах грязные, погнутые и подгоревшие контакты не допускаются. Изоляторы разъемов должны быть чистыми, сколы и трещины не допускаются. Оплетка кабеля должна быть закреплена в разъеме хомутом, не допускается выход из разъема проводов без оплетки;
- проверку блока КОН на герметичность соединений произвести совместно с проверкой ЭПК. Пропуск воздуха в местах соединений не допускается.
После осмотра ЭПК его корпус опломбировать.
Клапан сбрасывающий трехпозиционный 182
Произвести ревизию клапана, при необходимости выполнить ремонт и замену отдельных узлов и агрегатов. Выполнить замену резиновых уплотнительных изделий. Срок службы диафрагм и уплотнений – 3 года, прокладок и уплотнительных колец – 4 года. Резиновые уплотнительные изделия, имеющие надрывы и трещины, а также с истекшим сроком службы заменить новыми.
Перечень резиновых уплотнительных изделий указан в таблице 12.7.11.1.
Таблица 12.7.11.1 – Перечень резиновых уплотнительных изделий
Место расположения | Наименование | Обозначение | Количество на изделие | Примечание | |
Рисунок | Позиция | ||||
12.7.11.1 | 3 | Прокладка | 182.009 | 1 | |
6 | Прокладка | 270.549 | 2 | ||
8 18 |
Уплотнение клапана | 270.357 | 2
1 |
||
10 | Диафрагма | 177.001 | 2 | ||
19 | Кольцо ГОСТ 9833 | 055-060-30-2-2 | 1 | ||
34 | Кольцо ГОСТ 9833 | 060-010-25-2-3 | 4 |
Пружину при наличии изломов, трещин, а также в случае потери упругости или при просадке по высоте более допуска – заменить.
Проверку проводить в свободном состоянии, растягивание и заделка пружины не допускается.
Проверка работоспособности пружины приведена в таблице 12.7.11.2.
Таблица 12.7.11.2 – Проверка работоспособности пружины
местоположение | обозначение | контрольные значения параметров | |
рисунок | позиция | ||
12.7.11.1 | 12 | 260.238 | P1=0,162±0,016 кгс; H1=13,5 мм Р2=0,0225±0,023 кгс; Н2=13 мм |
Разборка клапана (рисунок 12.7.11.1):
- отвернуть гайки (21) и снять электропневматическую часть с кронштейна (5), извлечь прокладки (6);
- отвернуть гайку (16), снять уплотнение клапана (18);
- снять крышку (1) и удалить прокладки (3);
- отвернуть гайку (24) и отделить корпус (30) от корпуса (14);
- извлечь пружины (12), диафрагмы (10), уплотнения клапанов (8) и кольцо (19);
- вывернуть из корпуса (30) электромагнит с крышкой (2);
- отвернуть гайку (31);
- вывернуть седло (33) из корпуса (30) и снять с него кольца (34).
После разборки детали клапана, кроме резиновых, промыть моющими средствами или растворителем, каналы продуть сжатым воздухом. Очищенные детали протереть насухо. Посадочные места в клапанах при наличии рисок прошлифовать. Электромагнит с крышкой (2) при наличии пробоя изоляции, обрыва витков или выводных концов, а также заниженного сопротивления -заменить новым.
Собрать клапан в последовательности, обратной разборке. При сборке смазать тонким слоем все внутренние поверхности деталей и узлов смазкой ЖТ-79Л ТУ 0254-002-01055954.
Установить клапан на испытательный стенд К 575.000СЗ для регулирования хода клапана вентилей (винт седла (33) на рисунке 12.7.11.1) и проверки на соответствие техническим требованиям ТУ 3184-007-05756760.
После установки клапана на электропоезд повторно провести испытания на герметичность мест соединений воздухопроводов и кронштейна.
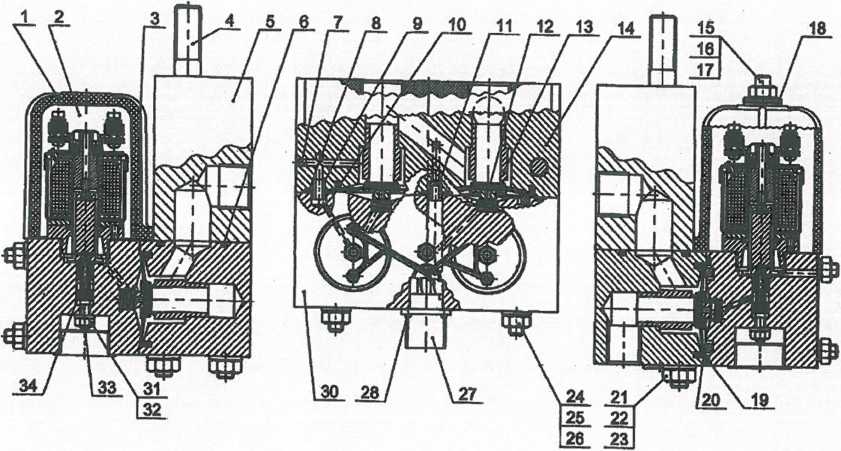
Рисунок 12.7.11.1 – Клапан сбрасывающий трехпозиционный 182: 1 – крышка 182.008; 2 – электромагнит с крышкой120.100-101; 3 – прокладка 182.009; 4 – шпилька М16; 5 – кронштейн 182.007; 6 – прокладка 270.549; 7 – заглушка; 8, 18 -уплотнение клапана 207.357; 9 – ниппель 183.23; 10 – диафрагма 177.001; 11 – дроссель 182.003; 12 – пружина 260.238; 13 – седло 182.002; 14 – корпус 182.001; 15 – шпилька М8; 16 – гайка М8; 17 – шайба; 19 – кольцо 055-060-30-2-3; 20 – вкладыш 418.003; 21 – гайка М10; 22 – шайба; 23 – шпилька М10; 24 – гайка М8; 25 – шайба; 26 – шпилька М8; 27 – электросоединитель; 28 – винт М4; 30 – корпус 182.005; 31 – гайка М6; 32 – шайба; 33 – седло 120.008; 34 – кольцо 006-010-25-2-3
Агрегат компрессорный винтовой АКБ 0,81/1
Выполнить все операции технического обслуживания 13 АКБ (порядок выполнения работ указан в п. 10.14) и следующие работы:
Произвести ревизию термостатического клапана и заменить детали, входящие в состав ремкомплекта (поставляется отдельно):
- на неработающем и отключенном агрегате разобрать термостатический клапан, не снимая его с АКБ;
- заменить элементы «А» (рисунок 12.7.12.1);
- собрать клапан.
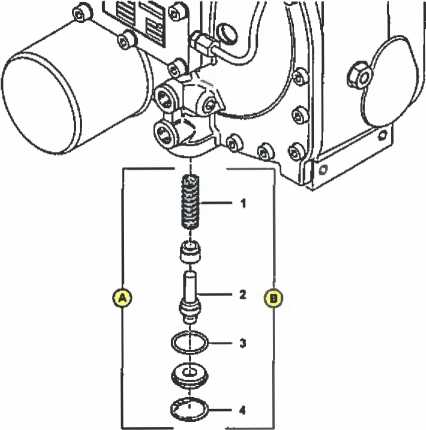
Рисунок 12.7.12.1 – Расположение деталей термостатического клапана NK31: А, В – элементы, входящие в ремкомплект
Произвести замену предохранительных клапанов:
- выкрутить клапаны из корпуса компактного модуля и из трубопровода на выходе из АКВ;
- настроить клапан на давление срабатывания 1,38 МПа (для компактного модуля) и 1,05 МПа (перед выходом из АКВ);
- Порядок настройки. Клапан вкручивается в трубопровод, оснащенный манометром, в трубопроводе создается давление срабатывания, далее выкручиванием либо закручиванием регулировочной гайки (6) (рисунок 12.7.12.2) настраивается клапан, чтобы при указанном давлении он открылся и начал стравливать воздух;
- собрать клапаны, поставить пломбы. На пломбе предохранительного клапана должна содержаться следующая информация: знак организации, проводившей испытание, год, месяц испытаний, давление срабатывания;
- установить клапаны на прежние места.
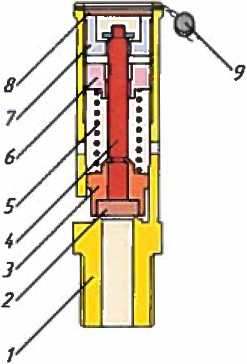
Рисунок 12.7.12.2 – Клапан предохранительный: 1 – корпус; 2 – кольцо уплотнительное; 3 – поршень; 4 – штанга; 5 – пружина; 6 – гайка регулировочная; 7 – крышка рифленая; 8 — номерная табличка; 9 – проволока, пломба и уплотнение
Проверка работоспособности предохранительного клапана осуществляется на работающем АКВ. Для этого необходимо выкрутить рифленую крышку (7) (рисунок 12.7.12.2). Клапан должен стравливать воздух. Залипание поршня (3) не допускается.
Произвести проверку крепления узлов и деталей АКВ.
Каждое второе техническое обслуживание 15 электропоезда проводить замену подшипников приводного электродвигателя.
Занести данные о проведенных работах в журнал технического состояния электропоезда и формуляр АКВ.
Агрегат компрессорный поршневой безмасляный АКПБ 0,07/0,7 (АКПБ)
Перед техническим обслуживанием необходимо отключить питание АКПБ, открыть откидную крышку и дать остыть компрессору в течении (5 — 10) минут.
Произвести очистку (протереть ветошью) от пыли, грязи, масла и других загрязнений наружные и внутренние поверхности АКПБ, включая наружные и легкодоступные внутренние части электродвигателя.
Проверить визуально затяжку резьбовых соединений на соответствие совпадения маркировочных рисок на соединениях. При обнаружении несовпадения рисок соответствующее резьбовое соединение затянуть и восстановить маркировочную риску. Моменты затяжки резьбовых соединений:
М6 – (10±1) Н м; М8 – (25±2) Н·м; М10 – (43±3) Н·м; М12 – (75±5) Н м.
При проверке затяжки резьбовых соединений обратить особое внимание на затяжку гаек крепления двигателя компрессора к раме, а также затяжку болтов и гаек амортизаторов.
Продуть фильтры входящего и выходящего воздуха, продувку осуществлять сухим сжатым воздухом давлением не более 0,2 МПа в направлении изнутри корпуса компрессорного агрегата наружу.
У двигателя агрегата:
- проверить надежность крепления траверсы и положение ее по заводской метке;
- проверить состояние рабочей поверхности коллектора, протереть коллектор мягкой неволокнистой, сухой ветошью, слегка смоченной в бензине или спирте. Очистку коллектора от пыли осуществлять сухим сжатым воздухом давлением не более 0,2 МПа;
- проверить состояние щеток. Щетки с трещинами и высотой менее 15 мм заменить. Вновь установленные щетки притереть к коллектору до приобретения зеркального блеска контактными поверхностями щеток. Предварительная притирка щеток производится мелкой стеклянной шкуркой, закладываемой между коллектором и щеткой. Щетки должны свободно перемещаться вдоль обоймы без заеданий. После замены щеток отрегулировать нажатие пружины щеткодержателей, которое должно быть в пределах от 0,25 до 0,35 кгс. Установить зазор между нижней кромкой щеткодержателя и коллектором в пределах от 1,5 до 2,0 мм;
- проверить надежность крепления контактных электрических соединений, проверить надежность заземления корпуса двигателя;
- заменить воздушный фильтр компрессорной головки.
Резервуары воздушные
Произвести полное техническое освидетельствование воздушных резервуаров с гидравлическим испытанием (не реже 1 раза в 4 года). Главные воздушные резервуары РС1 (для создания в питательной магистрали электропоезда запаса сжатого воздуха требуемого давления, необходимого для работы пневматического оборудования), питательный резервуар тормозной магистрали РС2 (для создания запаса сжатого воздуха требуемого давления, необходимого для работы автоматического пневматического тормоза электропоезда), воздушный резервуар РС3 (для создания запаса сжатого воздуха требуемого давления, необходимого для работы пневматического рессорного подвешивания) подлежат обязательной пропарке или выщелачиванию с последующей промывкой горячей водой. Техническое освидетельствование, сварку при ремонте и испытании воздушных резервуаров производить порядком, установленным «Правилами надзора за воздушными резервуарами подвижного состава железных дорог ЦТ-ЦВ-ЦП-581».
Запрещается заваривать трещины на цилиндрической части и днищах по целому месту, а также вмятины с повреждением или без повреждения металла; производить подчеканку швов для устранения в них неплотностей и выпускать резервуары с признаками деформации металла и выпучинами на цилиндрической части и днищах. Разрешается на резервуарах оставлять без исправления вмятины без повреждения поверхностного слоя металла с плавными переходами глубиной не более 5 мм и мелкие прожоги металла глубиной до 0,3 мм на цилиндрической части и до 0,5 мм на днищах, заваривать трещины и пористые места в сварных швах (с предварительной вырубкой), а также заменять негодные штуцера путем вырубки старых и установки новых.
Резервуары допускаются к дальнейшей эксплуатации:
- с вмятинами в количестве не более трех, с расположением их вне сварных швов и на расстоянии друг от друга, равном не менее 15 % его диаметра, и глубиной вмятины не более 5 мм,
- с коррозионными повреждениями не более 20 % от общей поверхности резервуара с глубиной до 10 % от толщины стенки резервуара.
Воздухопроводы, рукава соединительные, краны концевые
Осмотреть состояние и крепление трубопроводов пневматического оборудования, цепей управления, тифонов и пескоподачи. Проверить герметичность мест соединений всех воздухопроводов. Не допускается пропуск воздуха в местах соединений. Ослабление креплений трубопроводов не допускается.
Выявленные утечки воздуха устранить протягиванием накидных гаек трубопроводов или заменой оборудования. При затягивании накидных гаек вторым ключом удерживать штуцер. В случае обнаружения повреждения трубопровода или отдельных труб произвести ремонт со снятием с электропоезда или заменить.
Резиновые рукава с протертыми местами или трещинами, надрывами до оголения текстильного слоя, а также рукава со сроком службы более 6 лет или не имеющие клейма даты изготовления, заменить новыми. Потертости и образование сетки из мелких трещин на верхнем слое резины не является браковочным признаком.
Соединительные рукава питательного воздухопровода проверить на прочность гидравлическим давлением 1,3 МПа в течение 2 мин.
Соединительные рукава тормозной магистрали, воздухопроводов тормозных цилиндров и вспомогательного тормоза проверить на прочность гидравлическим давлением 1,0 МПа в течение 2 мин.
Соединительные рукава питательного воздухопровода, тормозной магистрали, воздухопроводов тормозных цилиндров и вспомогательного тормоза проверить на герметичность пневматическим давлением 0,8 МПа с выдержкой в водяной ванне в течение 3 мин.
Появление на поверхности резиновой трубки вновь скомплектованных и бывших в эксплуатации соединительных рукавов пузырьков в начале испытания с последующим их исчезновением браковочным признаком не является. Образование мыльных пузырей в местах соединений рукавов не допускается. Головки соединительных рукавов тщательно осмотреть и проверить шаблоном. Неисправную головку заменить. Зазор между ушками хомутика должен быть в пределах (7-16) мм при затянутых болтах.
Разобщительные шаровые краны с фиксацией рукоятки 426 (на тормозной магистрали) и 426-1 (на питательной магистрали) проверить на фиксацию в закрытом и открытом положении, работу фиксатора. При наличии неисправностей кран заменить.
Проверить работоспособность сепаратора-влагоотделителя циклонного типа SP01-14, разобщительного крана для слива конденсата на корпусе сепаратора-влагоотделителя.
Установка обеззараживания воздуха (УОВ)
Произвести замену амальгамной лампы обеззараживателя (УФ-модуля).
Перед началом работы необходимо убедиться в отсутствии питающего напряжения.
Открыть крышки отсека нагревателей, отсека испарителя. Снять перемычки заземления со шпилек заземления на крышках отсеков, открутив гайки М8 с внутренней стороны крышек. Открутить верхние и нижние болты крепления калориферов и верхние болты крепления УФ-модуля. Демонтировать кабели, подходящие к коробке коммутационной, расположенной на УФ-модуле. Для этого открыть крышку коробки, открутив 4 винта, открутить крышки у 3 кабельных вводов с подходящими к УФ-модулю кабелями, и с помощью малой отвертки демонтировать провода подходящих кабелей из клеммников. Отодвинуть калориферы от УФ-модуля на расстояние, позволяющее получить доступ к нижним болтам крепления УФ-модуля. Открутить нижние болты крепления УФ-модуля. Переместить УФ-модуль из отсека, поднимая вверх поступательно, избегая рывков и ударов. Произвести замену амальгамной лампы УФ-модуля. Произвести сборку в обратном порядке, используя фиксатор резьбы Loctite 243. Болты предварительно очистить от загрязнений. Резьбовые соединения закручивать с моментом затяжки для болтов М6 – 5,9 Н-м, для болтов М8 – 14,1 Н-м. Установить и закрепить УФ-модуль, калориферы, смонтировать кабели. Установить крышки отсеков нагревателей, испарителя, прикрутить перемычки заземления, закрепить крышки.
Отслужившие УФ лампы должны быть обезврежены и утилизированы в соответствии с Постановлением Правительства Российской Федерации от 3 сентября 2010 г. № 681 «Правила обращения с отходами производства и потребления в части осветительных устройств, электрических ламп, ненадлежащие сбор, накопление, использование, обезвреживание, транспортирование и размещение которых может повлечь причинение вреда жизни, здоровью граждан, вреда животным, растениям и окружающей среде».
Двери салона электропоезда наружные ДБПС 004.01.00.000
Выполнить работы в объеме технического обслуживани 14.
Произвести замену зубчатого ремня ременной передачи.