Произвести демонтаж гидравлических демпферов и их ремонт в специализированном отделении в соответствии с требованиями «Руководства по эксплуатации РЭ УГД 210.240.150.390». Демпферы снять с вагона (см. таблицу 1.1.6.1), разобрать, отремонтировать или заменить неисправные металлические детали, заменить резиновые уплотнения, рабочую жидкость, собрать демпфер и испытать на стенде.
Таблица 1.1.6.1 – Восстановление работоспособности демпферов
Наименование | Способы восстановления |
Демпфер в сборе | Обмыть демпфер в моечной машине в вертикальном положении (головкой вверх), очистить и обтереть. Осмотреть, проверить маркировку и подвергнуть технологической разборке. Использовать моечные машины струйного типа и очистные машины щеточного типа с электрическим приводом, применяемые в ОАО «РЖД» |
Детали корпуса | Разобрать демпфер. Слить рабочую жидкость в емкости для отработанных масел. Корпус, головку со штоком, кожух, гайку корпуса промыть, обдуть сжатым воздухом, осмотреть и обмерить. Проверить резьбы непроходными калибрами по ГОСТ 17763-72 и ГОСТ 17756-72. Износ, смятие более двух ниток резьбы не допускается. Трещины в корпусе и кожухе заварить, овальности выправить прессом с применением оправок. Резьбовые участки ремонтировать наплавкой электродами марки УОНИ-13-45 диаметром (2 – 3) мм с последующим отжигом и нарезной резьбы. Перед наплавкой обточить поврежденную резьбу, после наплавки отжечь и нарезать резьбу согласно чертежной документации на детали демпфера. Использовать штангенциркуль, нутромер, калибры резьбовые, сварочный агрегат, токарный станок, оправки, промывочную установку |
Детали головок и проушин | Заменить металлические цапфы с погнутостями или с трещинами. Износ цапф по диаметру отверстий не должен быть более 0,4 мм. Резиновые втулки заменить новыми. Установку резиновых втулок и запрессовку в них цапф производить с применением клея 88-СА ТУ 38.1051760-89. При этом соблюдать симметричность резиновых втулок и цапф относительно торцов головок и проушин. Для фиксации резиновых втулок в головки и проушины завинтить болты М6. Использовать штангенциркуль, слесарный инструмент, зажимы |
Детали цилиндропоршневой группы | Промыть в моечной машине и обдуть сжатым воздухом шток в сборе с поршнем и клапанами, цилиндр, днище в сборе с клапаном, направляющую. Разобрать сборочные единицы. Осмотреть и обмерять детали. Использовать штангенциркуль, лупу, микрометр, нутромер, калибры резьбовые непроходные, моечную машину, источник сжатого воздуха |
Резьбовые соединения | Не допускать срез или смятие двух и более ниток резьбы. Резьбовые поверхности штока и днища ремонтировать наплавкой электродами марки УОНИ-13-45 диаметром 2-3 мм с последующей нарезкой резьбы. Допускаются иные прогрессивные методы наплавки для восстановления резьбы. Перед наплавкой произвести обточку поврежденного участка резьбы. После наплавки нарезать резьбу согласно чертежу*. Использовать резьбовые калибры, токарный станок, сварочный агрегат |
Шток | На цилиндрической хромированной поверхности штоков не допускается отслоение хрома, вмятины, выбоины и коррозийные повреждения, местный износ более 0,03 мм. Поврежденные штока заменить. Использовать микрометры, лупу |
Поршень и детали клапанов | Износ поршня не должен быть более 0,3 мм по наружному диаметру. Не допускаются задиры или риски глубиной более 0,3 мм. Износ канавки поршня по высоте не должен быть более 0,3 мм. Пластины клапанные, диск днища и поршневое кольцо заменить. Использовать микрометры, штангенциркули, резьбовые калибры, лупу |
Днище с клапанами | Разобрать, промыть и осмотреть днище и детали клапанов. Диск, пластины и пружину заменить. Проверить состояние болта и гайки. Использовать резьбовые калибры, лупу |
Направляющая штока | Осмотреть и обмерить направляющую штока: не должно быть трещин, отколов, задиров сопрягаемых поверхностей. Внутренний диаметр направляющих не должен иметь износов более 0,03 мм по диаметру. Направляющая с цилиндром должна сопрягаться с натягом. Использовать нутромер, микрометр |
Цилиндр | На внутренней поверхности цилиндра не допускаются задиры, выбоины и вмятины. Износ внутренней поверхности не должен превышать 0,3 мм по диаметру. Цилиндры с неисправностями заменить новыми. Для осмотра и измерения использовать лупу, нутромер |
Резиновые уплотнительные детали | Резиновые уплотнительные детали заменить, при монтаже контролировать правильность установки манжет, колец и грязесъемников. Перед сборкой резиновые детали выдержать не менее 10 мин. в рабочей жидкости. Резиновые втулки не должны иметь трещин, вспучиваний, отслоений, эрозий. Использовать слесарный инструмент, переходники, конусы, оправки |
Резиновые втулки головок и проушин | Резиновые втулки вставить в головки и проушины с применением клея 88-СА при соблюдении стандартной технологии склеивания резины с металлом. Затем запрессовать во внутрь втулок цапфы с применением клея 88-СА. Установить ограничительные кольца на цапфу и завинтить фиксирующие болты М6 в головки и проушины с двух сторон. Использовать гидропресс для установки втулок в проушины, щипцы для сжатия (ГОСТ 24589-81Е) и развода (ГОСТ 24590-81Е) пружинных колец, ключ S10 |
Цапфы | Цапфы монтажные ремонтировать наплавкой с последующей механической обработкой по чертежным размерам. При R1, R2 допускается износ цапфы по диаметру не более 0,4 мм. При R3, R4 износ цапф не допускается. Использовать штангенциркули, сварочный агрегат, токарный станок, гальванические ванны |
Рабочая жидкость | В демпферы налить свежую рабочую жидкость ВМГЗ ТУ 38.101.479-00, или АМГ-10 ГОСТ 6794-75, или МВП ГОСТ 1805-76 в объеме, установленном в рабочей документации. Перед заправкой жидкость профильтровать через металлическую сетку нормальной точности 016 Н ГОСТ 6613-86. Использовать дозаторы, мерные емкости. |
Сборка гасителя | Собрать демпферы по установленной технологии с применением специализированного оборудования, приспособлений и инструмента в производственных участках ремонта демпферов. У подготовленных для испытания демпферов не закрепляют защитный кожух. Использовать оборудование, зажимы, слесарный инструмент |
Испытание демпфера, окончательная сборка, маркирование | Демпферы испытать на стенде в дроссельном и клапанном режимах с записью рабочей диаграммы при контрольных скоростях поршня. Результаты испытаний занести в электронную базу данных программы стенда и в паспорт. Данные хранятся до следующего поступления демпфера в плановый ремонт. Затем произвести окончательную сборку – установить защитный кожух и нанести маркировку, сохраняя заводскую маркировку. Нанести условный номер ремонтного предприятия, месяц, две последние цифры года. Маркировку нанести ударным способом на корпусной проушине. Допускается маркирование на металлической бирке с креплением ее имеющимся болтом к головке или проушине. Использовать испытательный стенд СИЛ 02-01, зажимы, слесарный инструмент |
Окрашивание | Демпферы окрасить по ГОСТ 12549-2003 RAL7043 |
Примечание:
*- Состояние резьбы контролируемых деталей проверить непроходными резьбовыми калибрами. При изготовлении деталей использовать непроходные и проходные резьбовые калибры; **- Объем рабочей жидкости, л:
|
Перед подачей на ремонтный участок демпферы обмыть в моечной машине струйного типа в вертикальном положении и очистить в машине сухой очистки щеточного типа.
Для обмывки может быть рекомендована моечная машина ММД-8, для очистки – машина ОМГ-5.
Разборка-сборка демпферов
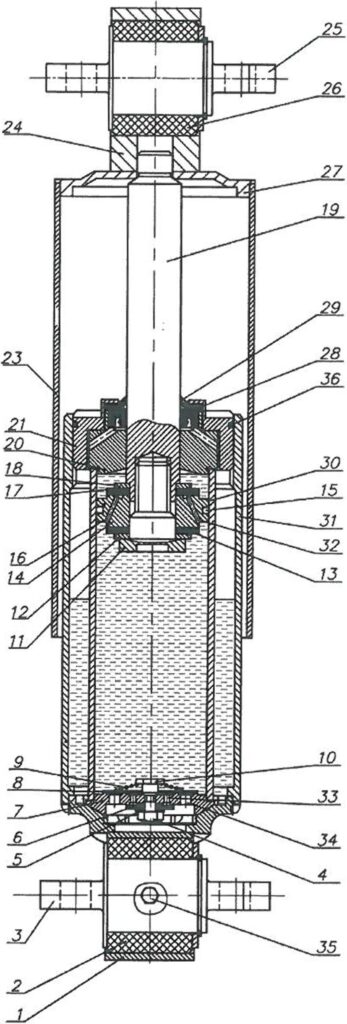
Рисунок 1.1.6.2 – Гидравлический демпфер УГД 390/4700/4700/002
Очистить демпфер (промывочное устройство, устройство сухой очистки, щетки, скребки, ветошь).
Разборка
- Разобрать головку и проушину (инструмент: ключ S10, пресс, отвертка, щипцы ГОСТ 24590-81Е для развода пружинных колец, ключ S10, молоток). Вывинтить болты (35). Снять с цапф стопорные упорные кольца и ограничительные кольца. Выпрессовать металлические цапфы (3, 25), вынуть резиновые втулки (2, 26). Снять кожух (ручная электрическая шлифовальная машина). Удалить сварной шов кожуха, снять кожух.
- Разобрать корпус (рожковый ключ, отвертка, бородок, молоток, противень, сливная ванна). Отвинтить гайку (21) корпуса. За проушину вынуть из корпуса цилиндропоршневую группу в сборе и уложить ее на противень. Выпрессовать днище (7) и слить рабочую жидкость из цилиндра. Выпрессовать направляющую (20) из цилиндра (30). Вынуть шток с поршнем из цилиндра. Из корпуса вылить рабочую жидкость.
- Разобрать шток с поршнем (инструмент: тиски, ключ S27, отвертка). Зажать шток (19) с поршнем (14) за проушину (24) поршнем вверх. Гаечным ключом отвинтить болт (11) (или гайку 11). Снять последовательно с поршня шайбу (12), пластины (13), поршень (14), пластины (17), шайбу (18), направляющую (20) с манжетой (28), гайку (21) с кольцом (36), кожух (23). Снять кольца (36) с гайки (2).
- Разобрать клапаны в днище (инструмент: зажим, ключ S13). Зажать днище (7) за гайку (10) в мягких прокладках. Вывинтить болт (4), снять шайбу (5), пластины (6), днище (7), диск (8) и коническую пружину (9).
- Осмотреть и обмерить детали. Заменить неисправные металлические и резиновые детали. Нормы допусков и износов деталей демпферов УГД приведены в таблице 1.1.6.2.
Таблица 1.1.6.2 – Нормы допусков и износов деталей демпферов УГД
а) Для демпфера УГД 390/4700/4700/002
Наименование деталей | Размер, мм | |||
Чертежный | Допустимый при выпуске из ремонта | Предельный в эксплуатации | ||
R1, R2 | R3, R4 | |||
Диаметр направляющей | 32 +0,01-0,01 | 32+0,006, не более | 32 +0,05, не более | 32,1 |
Диаметр штока | 32 –0,01-0,04 | 32 -0,08, не менее | 32 -0,04, не менее | 31,9 |
Диаметр цилиндра | 62 +0,03 | 62 +0,1, не более | 62 +0,06, не более | 62,3 |
Поршень | 62 +0,150-0,174 | 61,4 , не менее | 61,6 , не менее | 61,0 |
б) Для демпферов УГД 210/2950/2950/01, УГД 240/5200/4900/01, УГД 150/1000/1000/01
Наименование деталей | Размер, мм | |||
Чертежный | Допустимый при выпуске из ремонта | Предельный в эксплуатации | ||
R1,R2 | R3, R4 | |||
Диаметр направляющей | 25 +0,01-0,01 | 25, не более | 25 +0,05, не более | 25,1 |
Диаметр штока | 25 | 25, не менее | 25 -0,04 , не менее | 24,9 |
Диаметр цилиндра | 52 +0,03 | 52 +0,10, не более | 52 +0,06, не более | 52,3 |
Поршень | 62 +0,150-0,174 | 61,4, не менее | 61,6, не менее | 61,0 |
Сборка
- Собрать клапан в днище (инструмент: зажим, ключ S13, кернер, молоток). На болт (4) (М8) надеть шайбу (5) и пластины (6). Конусной стороной расположить шайбу к пластинам. Болт (4) с пластинами и шайбой завести в центральное отверстие днища (7). Сверху на днище уложить диск (8), на него широким основанием – коническую пружину (9). Прижать пружину, вставить в нее гайку (10) и навинтить ее на болт (4). Зажать гайку (10) в тисках и ключом S13 завинтить болт (4) до упора. Накернить резьбу легким ударом молотка по кернеру.
- Собрать поршень со штоком (инструмент: зажим, ключ S27, оправка). Зажать шток с головкой за проушину (24) штоком вверх. Надеть на шток гайку (21) с грязесъемником, манжету (28) и направляющую (20). На гайку (21) надеть резиновое кольцо (36). У демпфера УГД 390/470/4700/0 на гайку надеть два резиновых кольца. Для надевания манжеты (28) на шток (19) использовать оправку-конус. На кольцевую выточку штока положить конусную шайбу (18) и поршневые пластины (17). На пластины установить поршень (14). На поршень положить пластины (13) и конусную шайбу (12). Обе конусные шайбы должны прилегать к пластинам конусными сторонами. Завинтить болт (11) (или гайку 11). В канавку поршня вставить кольцо (15).
- Собрать цилиндр с днищем (инструмент: оправка, молоток). Легкими ударами молотка через оправку запрессовать в цилиндр (30) днище (7) в сборе.
- Собрать демпфер (тиски, рожковый ключ, гидропресс для установки втулок в проушины, щипцы ГОСТ 24590-81Е для развода пружинных колец, ключ S10, рабочая жидкость). Зажать корпус (31) гасителя за проушину (1). Поместить в него цилиндр с днищем в сборе. Залить приблизительно 0,4 л рабочей жидкости, вставить в цилиндр поршень (14) со штоком (19) в сборе. Прокачать поршнем рабочую жидкость в цилиндре. Добавить рабочую жидкость до нормы. Сцентрировать направляющую с цилиндром. Завинтить рожковым ключом гайку (21) в корпус. Установить в проушины (1 и 24) резиновые втулки (2, 26) и запрессовать в них металлические цапфы (3, 25), смазав их предварительно клеем 88-СА ТУ 38.105.1760-89. Надеть на цапфы ограничительные кольца и зафиксировать их стопорным упорным кольцом. Завинтить болты (35) в проушину и головку.
- Испытать демпфер на стенде с записью рабочей диаграммы, как указано в таблице 1.1.6.3. По форме диаграммы определить дефекты и усилия сопротивления на ходах растяжения- сжатия.
- Окончательная сборка демпфера после испытания. Закрепить кожух на крышке головки, приварить трубу кожуха к крышке головки. Уложить демпфер горизонтально на стеллаже для проверки герметичности в течение четырех часов. Маркировать демпфер на корпусной проушине и разместить его вертикально на стеллаже для последующей отправки на вагон.
Произвести монтаж демпферов
- Вертикальные демпферы системы рессорного подвешивания 1-ой ступени закрепить болтами и гайками M16 с моментом затяжки (174±8) Н·м. Предварительно на поверхность резьбы наносится монтажная смазка Staburags NBU 30 РТМ. После установки крепежные элементы и видимые грунтованные поверхности покрыть антикоррозийной жидкостью Tectyl 506 ЕН.
- Вертикальные демпферы системы рессорного подвешивания 2-ой ступени закрепить болтами M12 с моментом затяжки (68±3) Н·м. Предварительно на поверхность резьбы наносится монтажная смазка Staburags NBU 30 РТМ. После установки крепежные элементы и видимые грунтованные поверхности покрыть антикоррозийной жидкостью Tectyl 506 ЕН.
- Демпферы виляния закрепить болтами и гайками M16 с моментом затяжки (174±8) Н·м. Предварительно на поверхность резьбы наносится монтажная смазка Staburags NBU 30 РТМ. После установки крепежные элементы и видимые грунтованные поверхности покрыть антикоррозийной жидкостью Tectyl 506 ЕН.
- Предохранительный тросик демпфера виляния закрепить болтом М12 с моментом затяжки (68±3) Н·м. Предварительно на поверхность резьбы наносится контрящее средство Loctite 243. После установки крепежные элементы и видимые грунтованные поверхности покрыть антикоррозийной жидкостью Tectyl 506 ЕН.
- Поперечные демпферы системы рессорного подвешивания 2-ой ступени закрепить к шкворневому узлу болтами и гайками M12 с моментом затяжки (73±3) Н·м, к раме тележки болтами М12 с моментом затяжки (68±3) Н·м.
- Предварительно на поверхность резьбы нанести монтажную смазку Staburags NBU 30 РТМ.
- После установки крепежные элементы и видимые грунтованные поверхности покрыть антикоррозийной жидкостью Tectyl 506 ЕН.
Таблица 1.1.6.3 – Технология стендового контроля демпферов УГД
Наименование операции | Пояснение |
Установка демпфера на стенд | Демпфер в сборе закрепить болтами за цапфы на стенде типа «ЭНГА» СИЛ-02-01.
Зазоры в узлах крепления не допускаются |
Введение в рабочий режим | Включить стенд, прокачать демпфер не менее 5 колебаний и наблюдать за состоянием манжетного уплотнения.
Утечки жидкости через манжетное уплотнение штока и уплотнение гайки не допускаются, манжета не должна перемещаться относительно гайки корпуса. Не допускается выдавливание резиновых втулок и цапф из проушины и головки. Резиновые втулки не должны иметь повышенных деформаций или «отставать» от проушины (головки) или от цапфы |
Испытание демпфера с оценкой результатов | Включить режим испытания стенда на контрольной скорости поршня и на мониторе компьютера получить протокол испытаний с рабочей диаграммой, значения параметра сопротивления, усилий сопротивления на ходах растяжения-сжатия, их несимметричность и оценку соответствия нормативным требованиям.
По форме диаграммы оператор определяет возможные дефекты. Демпфер считают исправным, если форма диаграммы в дроссельном режиме близко соответствует эллипсу, значения параметра сопротивления и усилий сопротивления находятся в нормативных диапазонах, а несимметрия сил сопротивления на ходах сжатия и растяжения не более 25% (рисунок 1.1.6.3). Оценку работоспособности демпферов провести по усилиям сопротивления при контрольных скоростях. |
Прошедшие стендовые испытания демпферы укладывать горизонтально для проверки герметичности в течение не менее четырех часов. После «вылежки» у демпферов, не имевших утечек рабочей жидкости через уплотнения, приварить защитный кожух к головке.
Результаты испытаний занести в базу данных программы стенда |
|
Маркирование демпфера | Демпфер, признанный годным к эксплуатации, промаркировать. Отремонтированные демпферы разместить вертикально на стеллаже для последующей установки на вагон |
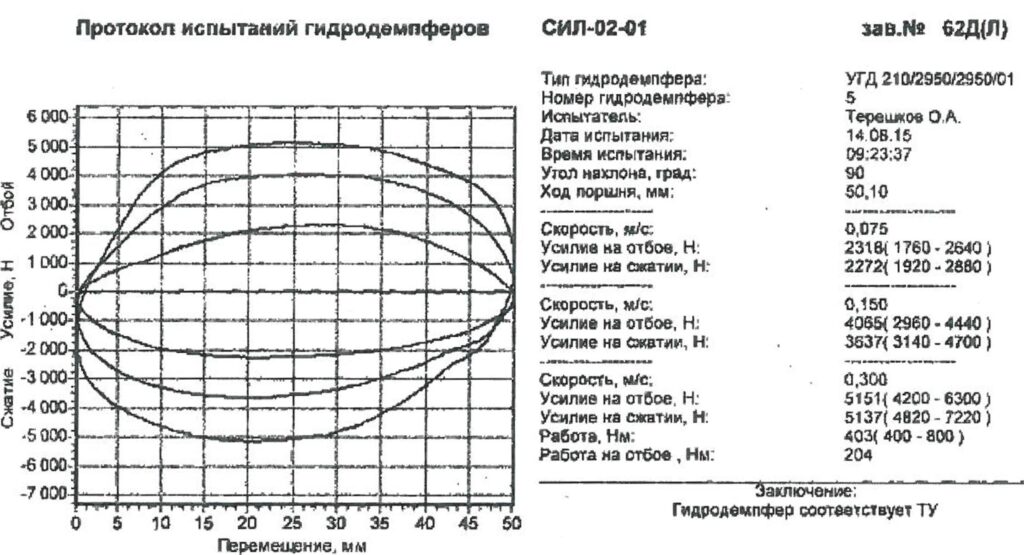
Рисунок 1.1.6.3 – Пример рабочей диаграммы демпфера УГД