Во время ревизии R1 производится проверка износов рабочих поверхностей БСУ-ТМ122 и соответствия чертежу геометрических параметров следующих деталей: пружинного замка, стопора клинового замка, центрирующего конуса, стопора клинового замка, приемного отверстия корпуса сцепки.
Произвести демонтаж сцепки с вагона. Произвести демонтаж, очистку, разборку, внешний осмотр, проверку годности деталей согласно маркировочных табличек и ремонт или замену деталей, при необходимости, восстановление лакокрасочного покрытия сцепки.
ВНИМАНИЕ! ОБРАТНАЯ СТОРОНА ПЛИТЫ СЦЕПКИ ОКЛЕЕНА ЭЛЕКТРОИЗОЛЯЦИОННОЙ ПРОКЛАДКОЙ ИЗ СТЕКЛОТЕКСТОЛИТА. ПРИ ДЕМОНТАЖЕ И МОНТАЖЕ УДЕЛИТЬ ОСОБОЕ ВНИМАНИЕ ЕЕ СОХРАННОСТИ. ПЕРЕД ДЕМОНТАЖЕМ С ВАГОНА ДЛИННОЙ МЕЖВАГОННОЙ СЦЕПКИ УСТАНОВИТЬ ТРАНСПОРТИРОВОЧНЫЕ БОЛТЫ В МЕХАНИЗМ ЦЕНТРИРОВАНИЯ, СЛЕГКА ПОДТЯНУВ ПРУЖИНЫ.
Произвести проверку износов рабочих поверхностей и соответствия чертежу геометрических параметров следующих деталей:
- проверку степени износа рабочих поверхностей стопора автоматического пружинного замка (рисунок 1.1.1.1) произвести при помощи контрольного шаблона ИИ-3274-00 (рисунок 1.1.1.2). Допустимая величина зазора по контуру рабочей поверхности стопора должна быть не более 0,3 мм;
- проверку рабочих поверхностей стопора клинового замка (рисунок 1.1.1.3) произвести при помощи контрольного шаблона ИИ-3275-00 (рисунок 1.1.1.4) . Допустимая величина зазора по контуру рабочей поверхности стопора должна быть не более 0,3 мм;
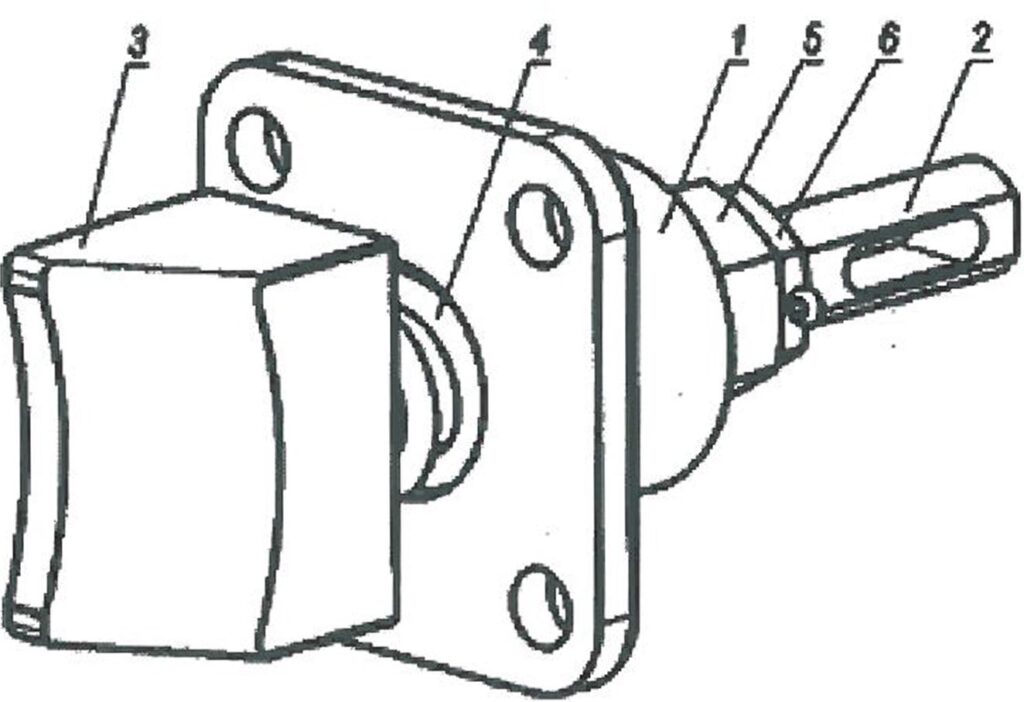
Рисунок 1.1.1.1 – Автоматический пружинный замок: 1 – корпус; 2 – шток; 3 – стопор; 4 – пружина; 5, 6 – гайки.
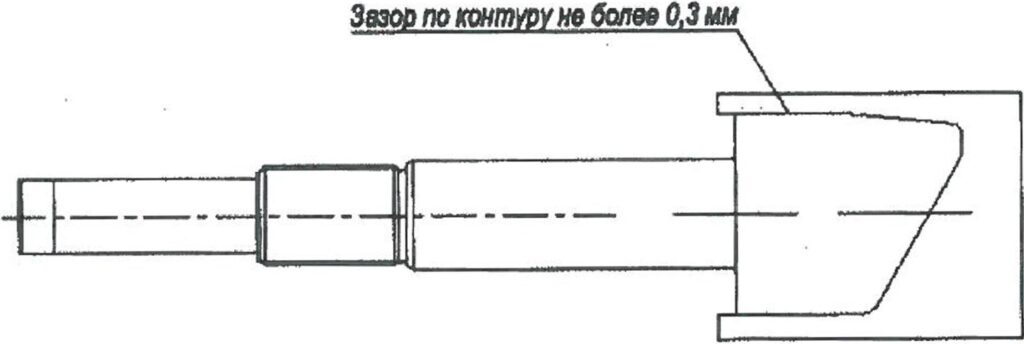
Рисунок 1.1.1.2 – Проверка степени износа рабочих поверхностей стопора автоматического пружинного замка шаблоном ИИ-3274-00
- произвести осмотр центрирующего конуса на предмет отсутствия трещин на его поверхности. Особое внимание следует обратить на участки, примыкающие к окнам. При обнаружении трещин конус заменить. Устранение трещин заваркой не допускается;
- проверить рабочие поверхности окон центрирующего конуса (рисунок 1.1.1.5). Проверку рабочих поверхностей окон центрирующего конуса произвести при помощи контрольных шаблонов ИИ-3277-00 и ИИ-3280-00 (рисунок 1.1.1.6);
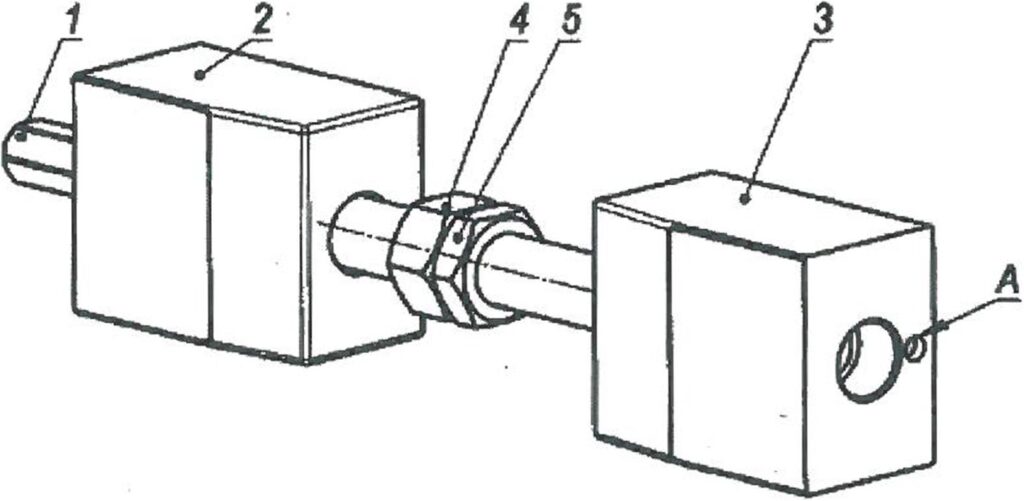
Рисунок 1.1.1.3 – Клиновой замок: 1 – шток; 2 – стопор с гладким отверстием; 3 – стопор с резьбовым отверстием; 4 – гайка регулировочная; 5 – гайка контровочная; А – отверстия на стопорах 2 и 3 для ориентации замка при установке в корпус головы сцепки
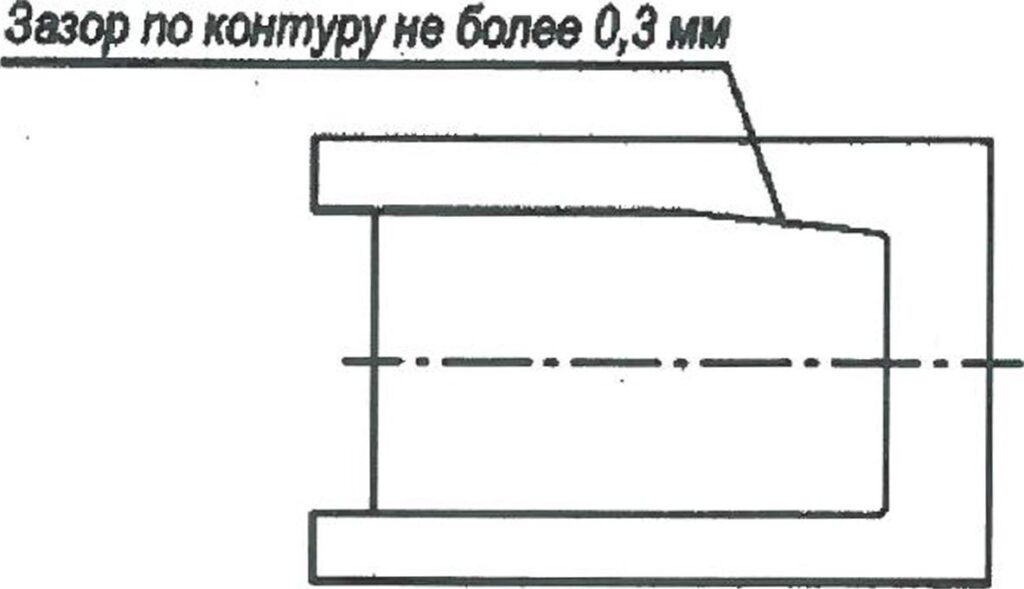
Рисунок 1.1.1.4 – Проверка степени износа рабочих поверхностей стопора клинового замка шаблоном ИИ-3275-00
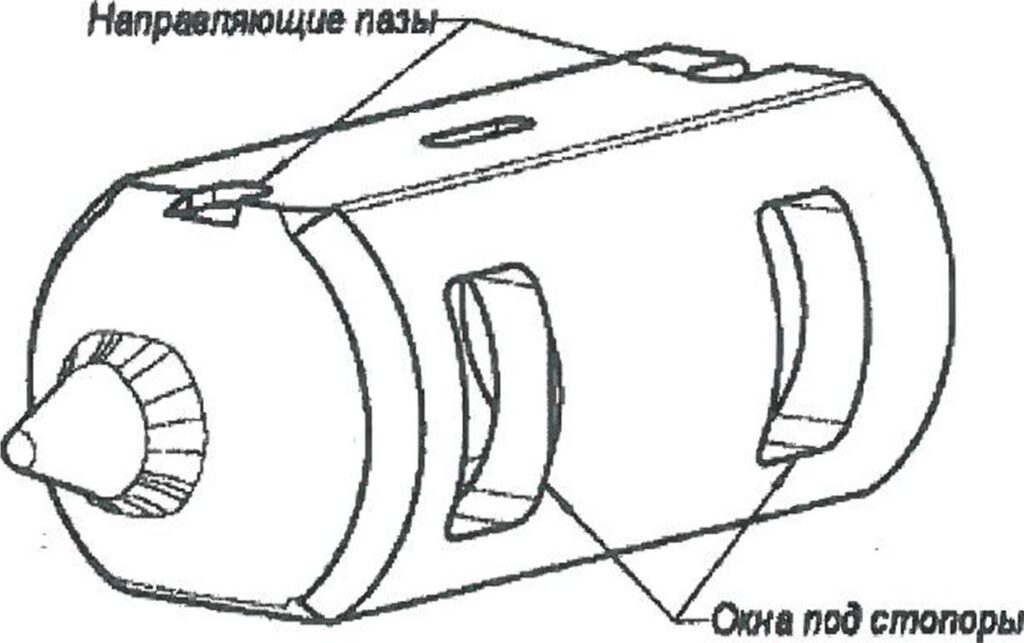
Рисунок 1.1.1.5 – Конус центрирующий
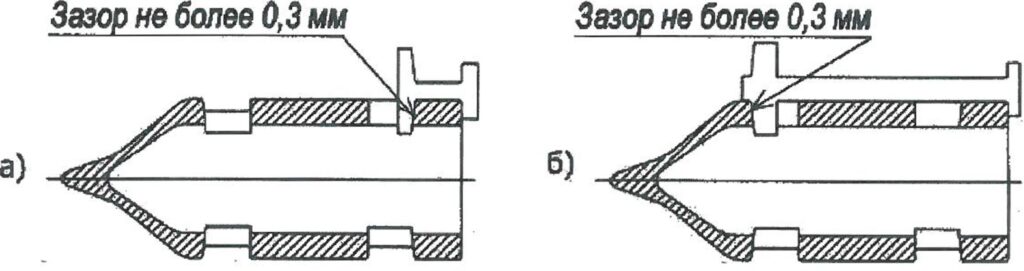
Рисунок 1.1.1.6 – Проверка степени износа рабочей поверхности окон центрирующего конуса шаблонами: а) ИИ-3277-00, б) ИИ-3280-00
- перед установкой конуса на место произвести его смазку графитной смазкой (приложение А);
- проверку степени износа приемного отверстия корпуса сцепки, рабочих поверхностей стопоров и направляющего конуса произвести путем измерения размеров деталей универсальными измерительными инструментами и сравнивая их с чертежными размерами (рисунки 1.1.1.7-1.1.1.9);
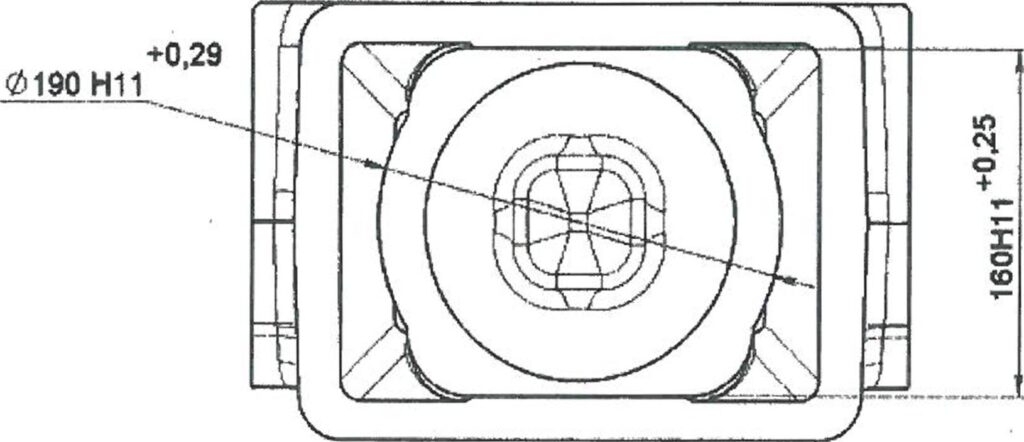
Рисунок 1.1.1.7 – Контролируемые размеры приемного отверстия корпуса головы сцепки
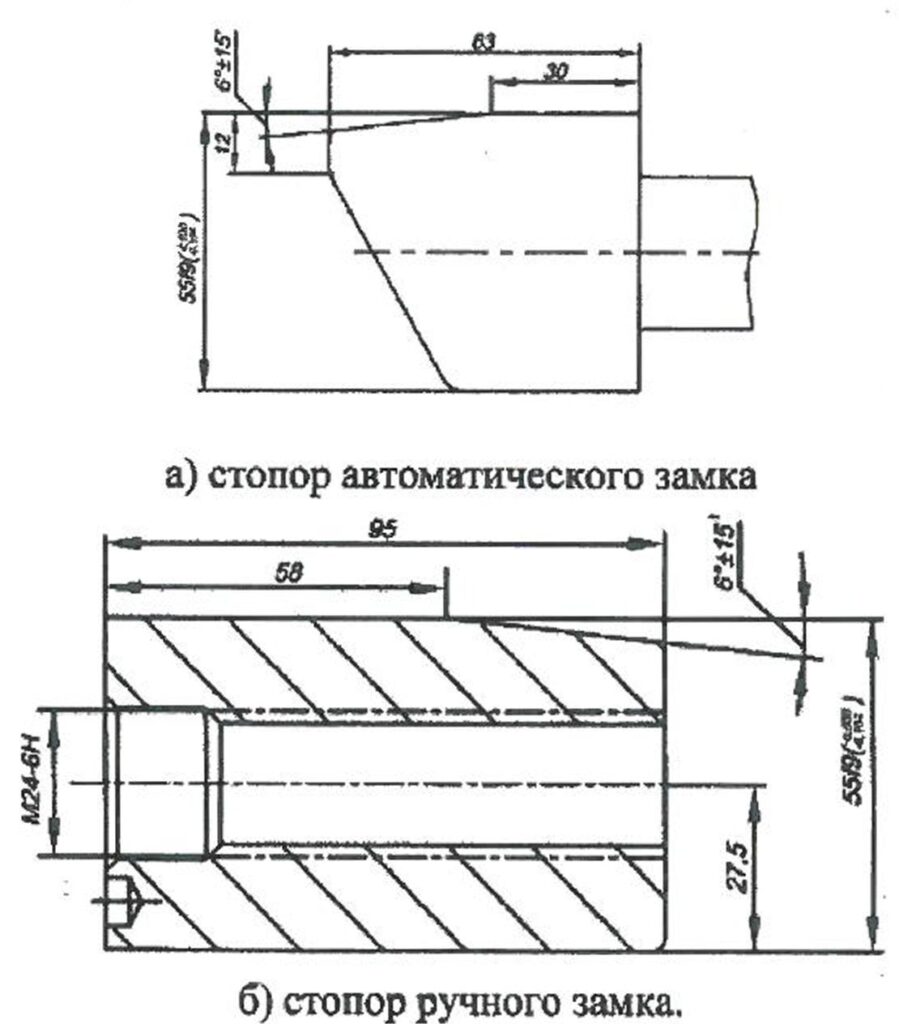
Рисунок 1.1.1.8 – Контролируемые размеры стопоров автоматических и ручных замков
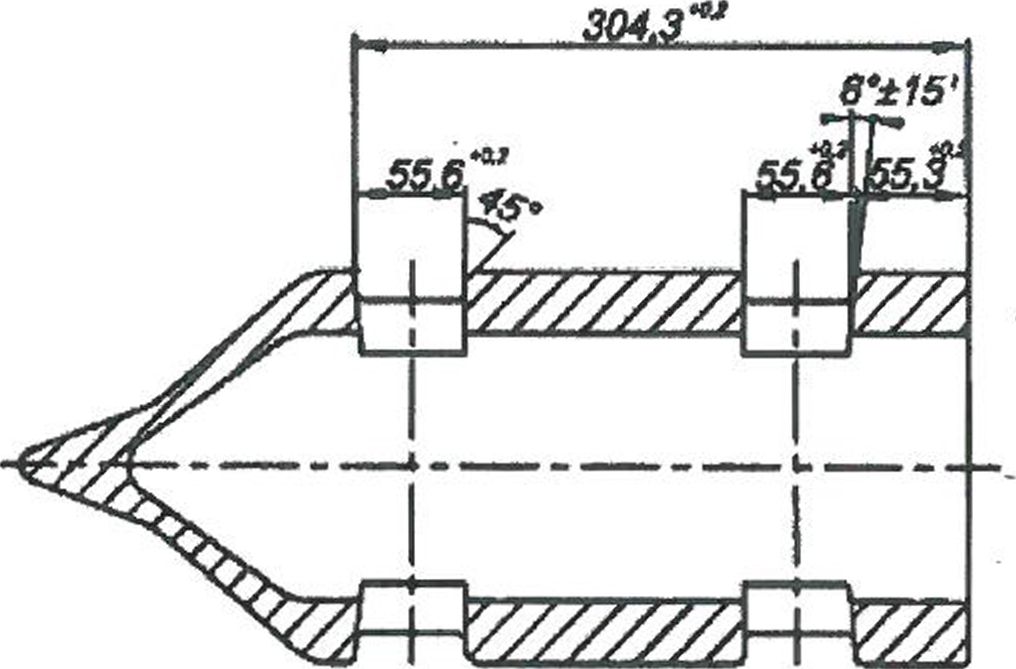
Рисунок 1.1.1.9 – Контролируемые размеры направляющего конуса
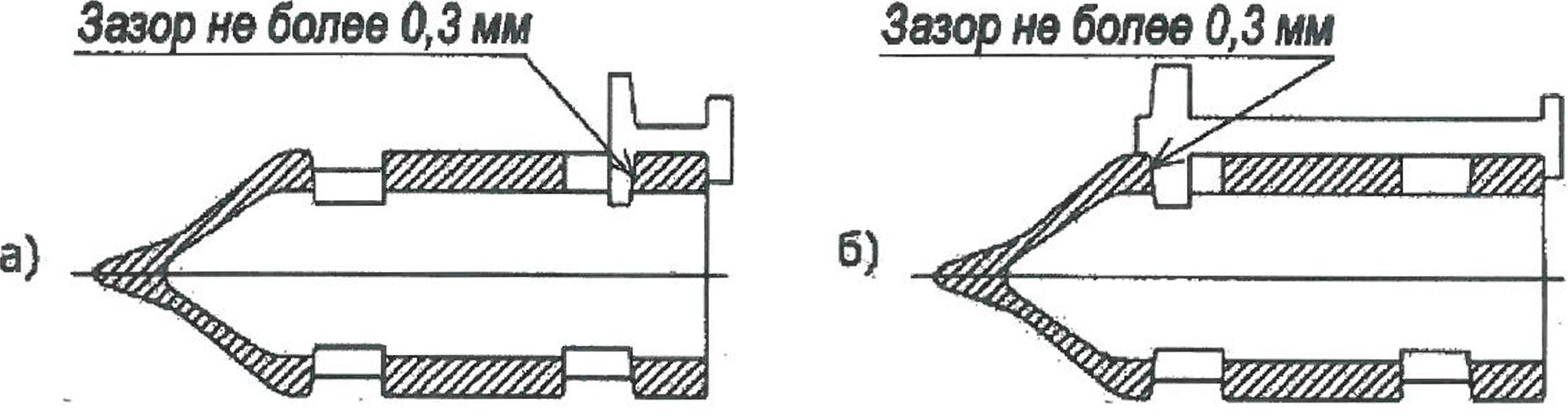
Произвести демонтаж, разборку и ремонт пневматических компонентов.
Произвести очистку, внешний осмотр, неразрушающий контроль сварных швов, при необходимости восстановить лакокрасочное покрытие вставки и крэш-элемента сцепки (рисунки 1.1.1.10, 1.1.1.11).
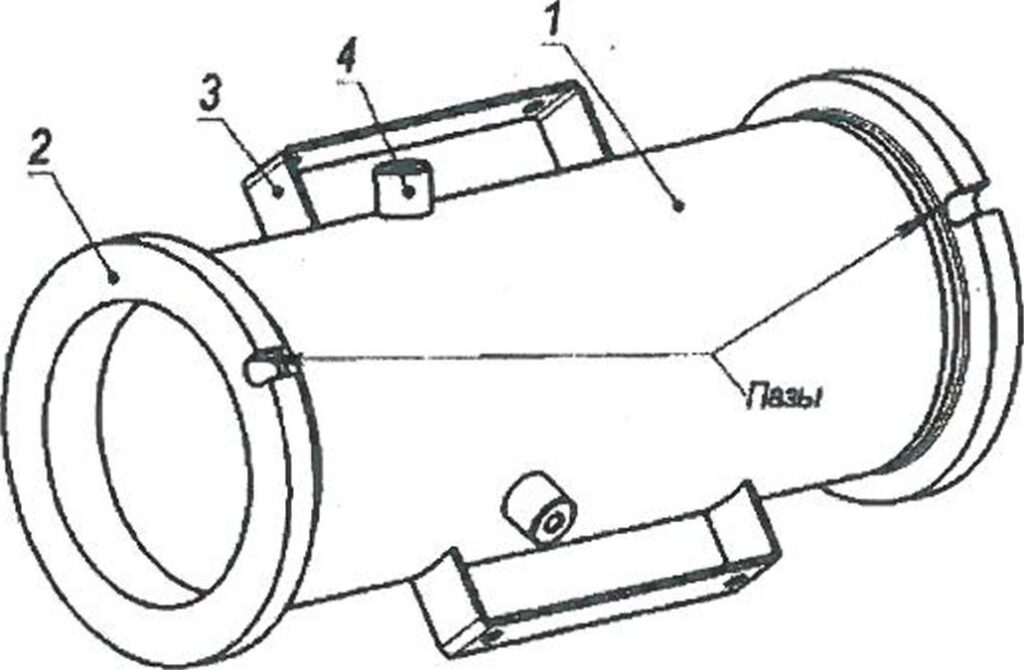
Рисунок 1.1.1.10 – Вставка: 1 – труба; 2 – фланец; 3 – скоба; 4 – бонка
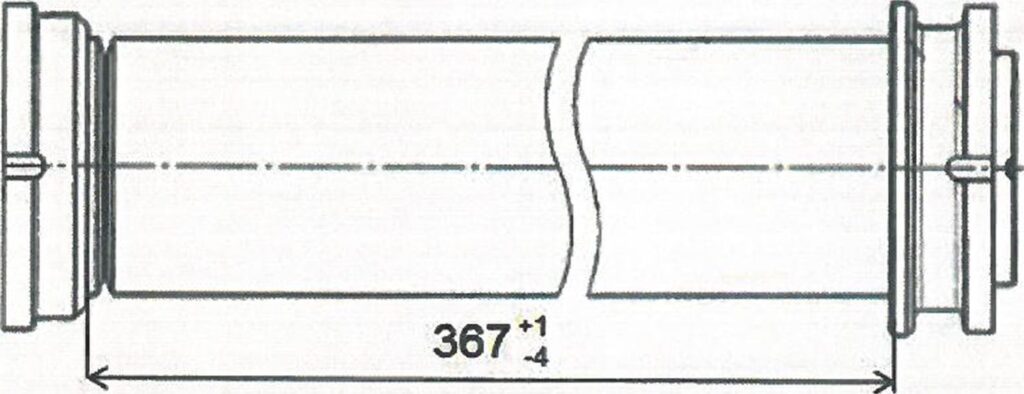
Рисунок 1.1.1.11 – Крэш-элемент
Произвести замер контрольного размера крэш-элемента, его значение и контрольную риску нанести несмываемым маркером. Произвести демонтаж, очистку, разборку, внешний осмотр, восстановление лакокрасочного покрытия опоры сцепки (рисунок 1.1.1.12).
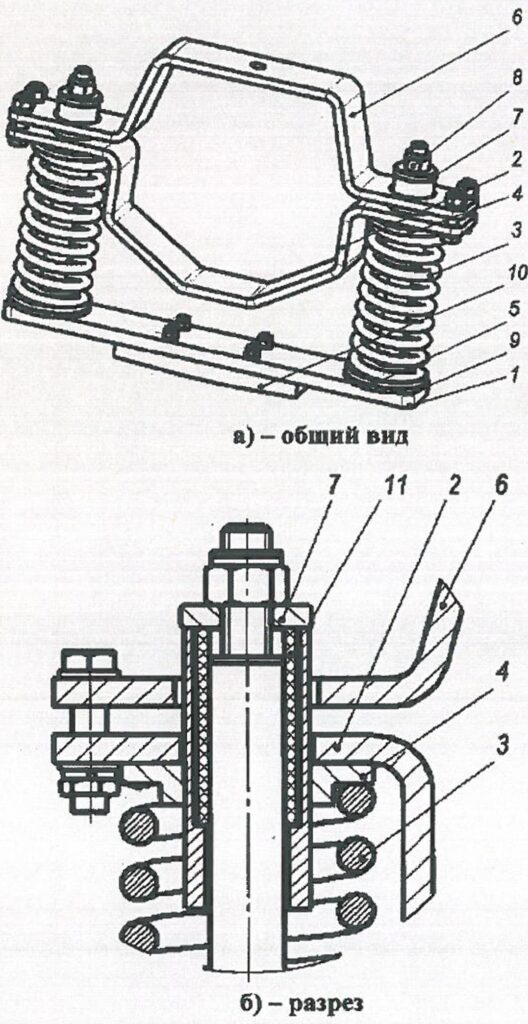
Рисунок 1.1.1.12 – Опора: 1 – основание; 2 – скоба; 3 – пружина; 4, 5, 11 – втулка; 6 – хомут; 7, 9 – шайба; 8 – гайка; 10 – планка
Произвести демонтаж, очистку, внешний осмотр, восстановление лакокрасочного покрытия поглощающего аппарата сцепки (рисунки 1.1.1.13, 1.1.1.14). Поглощающий аппарат не подлежит разборке. Проверить размер, определяющий конструкционный ход аппарата, который должен быть в пределах (73 – 78) мм. При несоблюдении данного размера или при наличии продольного люфта аппарат подлежит замене.

Рисунок 1.1.1.13 – Поглощающий аппарат Т-8П-04 (для ТМ122-00, -02): 1 – хвостовик; 2 – труба; 3 – фланец; 4 – шпилька; 5 – гайка; 6 – труба; 7 – сферический подшипник; 8 – планка; 9 – буфер отдачи; 10 – диск; 11 – фиксатор; 13 – пыльник; 14 – паспортная табличка
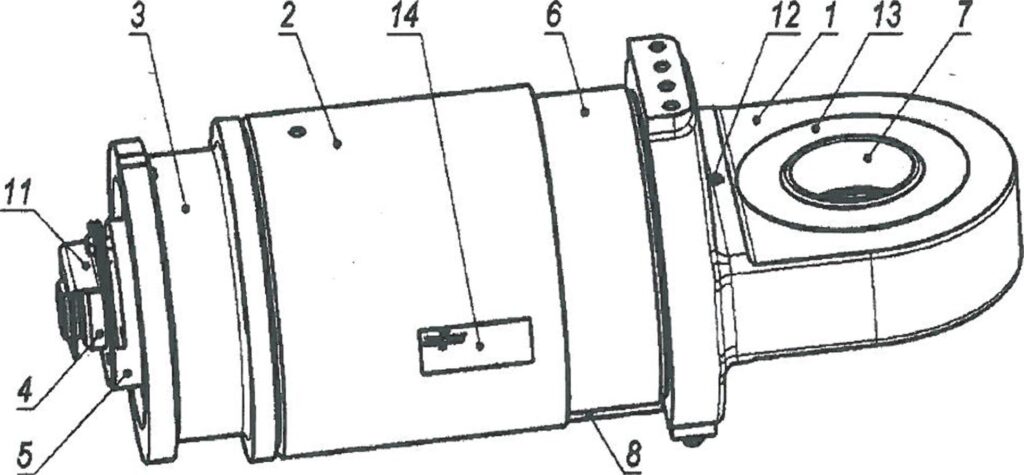
Рисунок 1.1.1.14 – Поглощающий аппарат Т-8П-01 (для ТМ122-01): 1 – хвостовик; 2 – труба; 3 – фланец; 4 – шпилька; 5 – гайка; 6 – корпус; 7 – сферический подшипник; 8 – планка; 11 – фиксатор; 12 – винт; 13 – пыльник; 14 – паспортная табличка
Произвести внешний осмотр, проверку годности плиты и соединительного пальца. Заменить сферический подшипник GE90FW-2RS на новый. Замену подшипника произвести по технологии предприятия-изготовителя сцепки. При замене подшипника заложить новую порцию смазки типа Солидол Ж ГОСТ 1033-79 (Литол-24 ГОСТ 21150-87 или аналогичной). Заменить резиновые кольца-пыльники (рисунок 1.1.1.15).
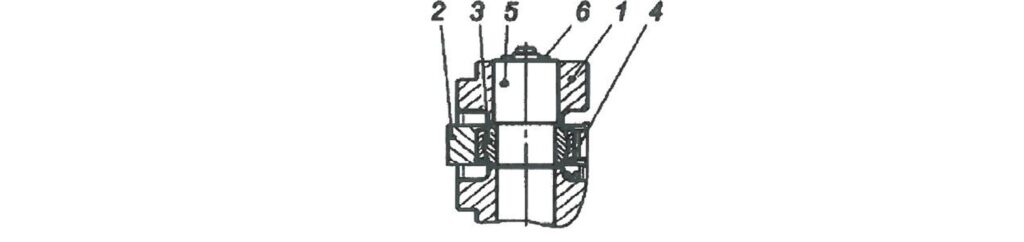
Рисунок 1.1.1.15 – Шарнирный узел: 1 – плита; 2 – хвостовик поглощающего аппарата; 3 – сферический подшипник; 4 – кольцо пружинное; 5 – палец; 6 – планка
Произвести разборку расцепного механизма (рисунок 1.1.1.16), проверку резьбовых соединений на износ, смазку и последующую сборку. При наличии коррозии наружных поверхностей деталей допускается окраска красками по металлу.
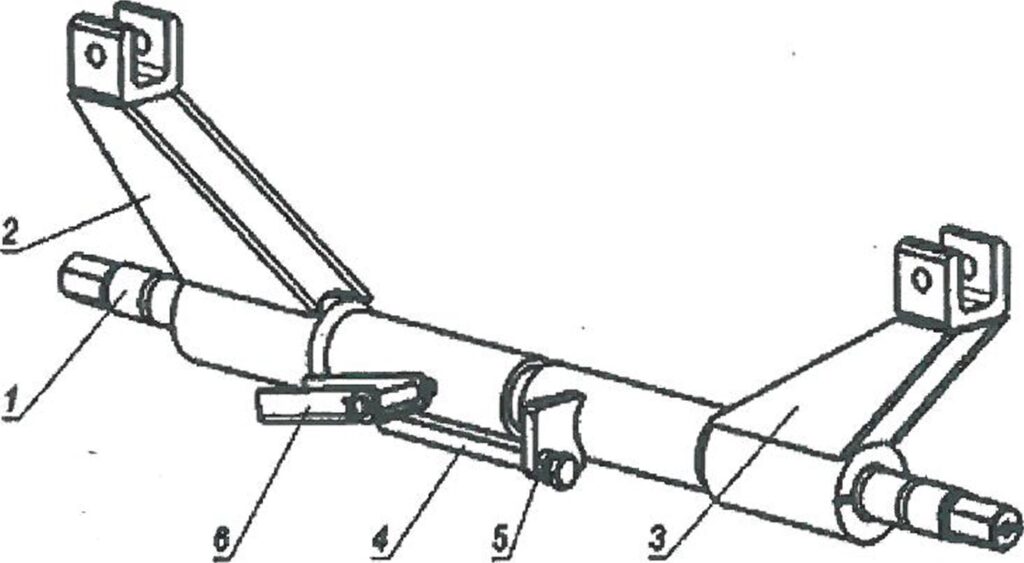
Рисунок 1.1.1.16 – Механизм расцепной: 1 – винт; 2, 3 – кронштейны; 4 – винт; 5 – гайка; 6 – флажок
Произвести сборку головы сцепки (рисунки 1.1.1.17 – 1.1.1.19) с соответствующими замками и другими устройствами.
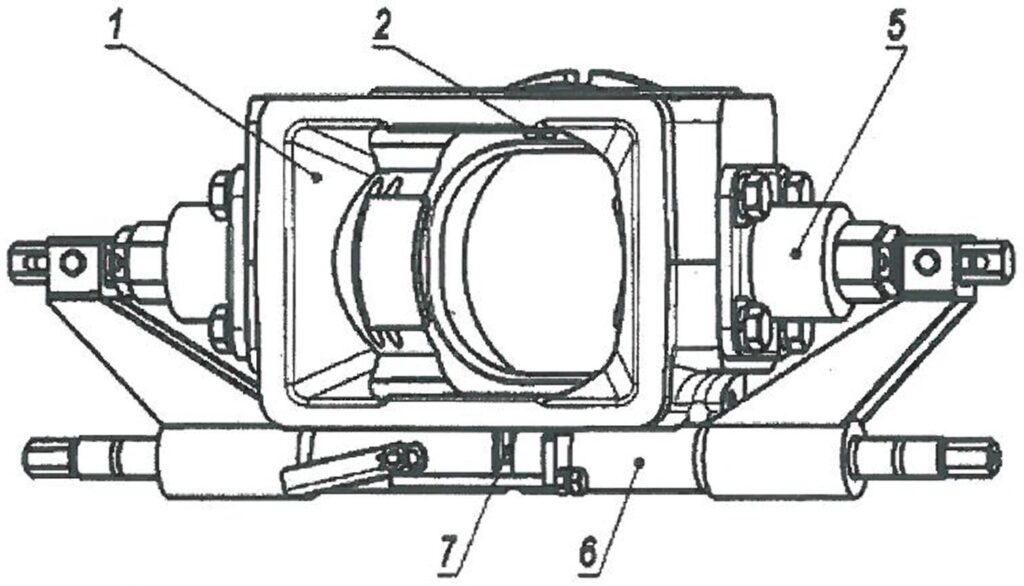
Рисунок 1.1.1.17 – Голова сцепки с автоматическими пружинными замками и расцепным механизмом: 1 – корпус; 2 – штифт; 5 – автоматический пружинный замок; 6 – механизм расцепной; 7 – штифт
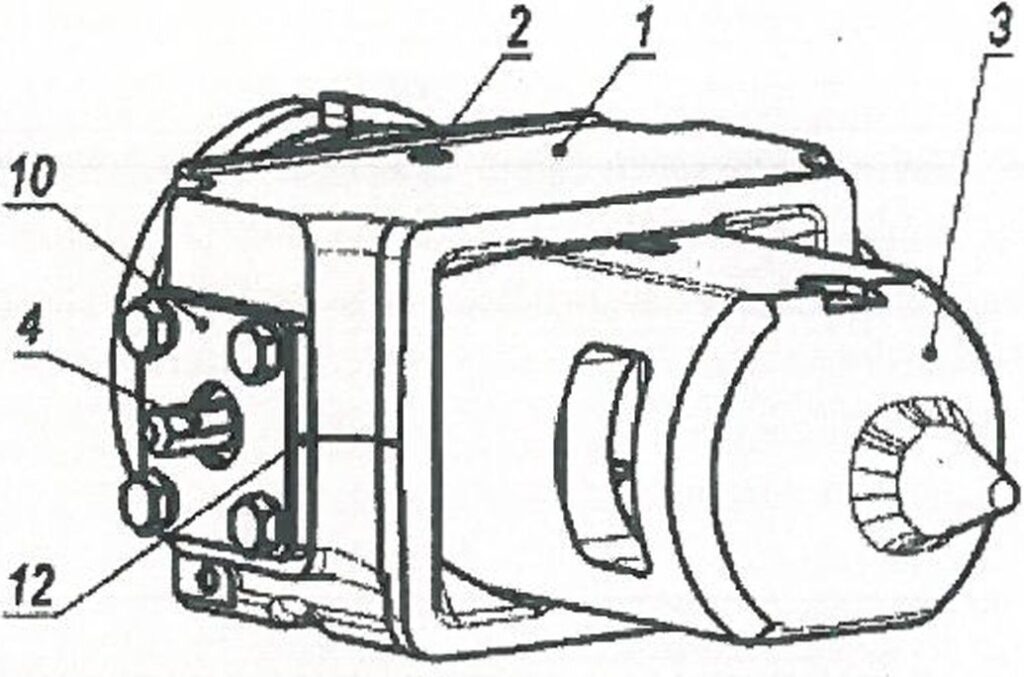
Рисунок 1.1.1.18 – Голова сцепки с центрирующим конусом: 1 – корпус; 2 – штифт; 3 – центрирующий конус; 4 – клиновой замок; 10, 11 (не видна) -крышка; 12 – прокладка
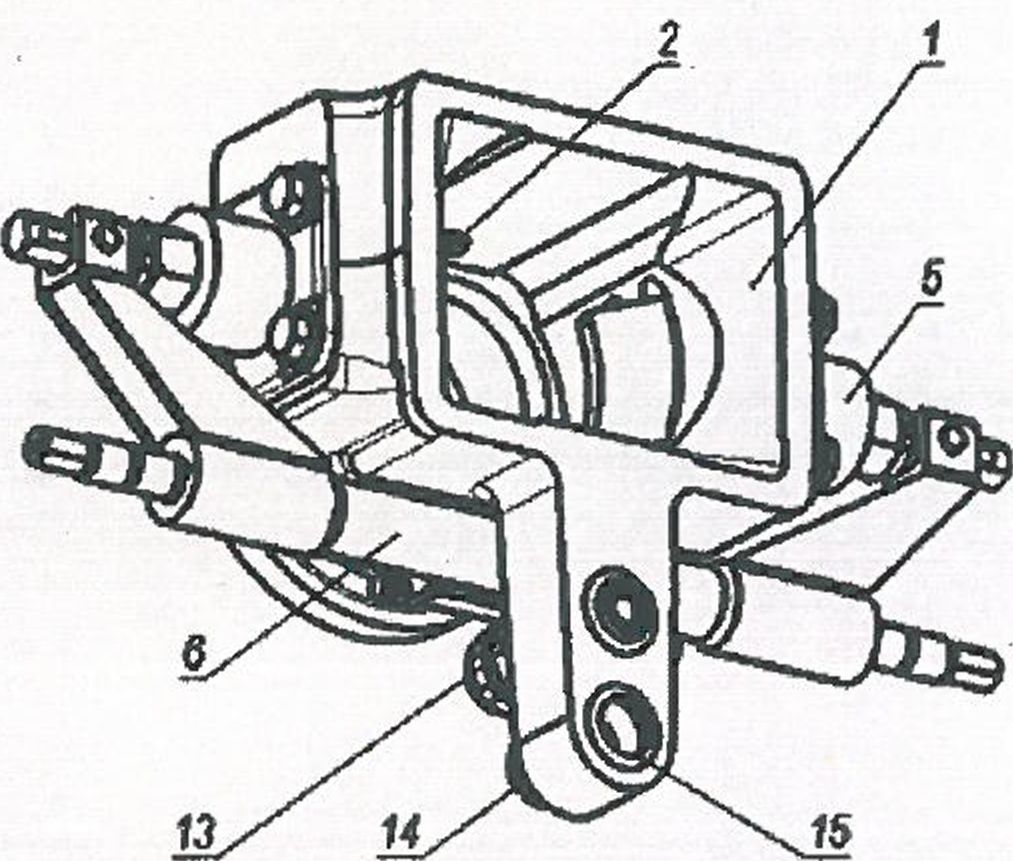
Рисунок 1.1.1.19 – Голова сцепки с автоматическими пружинными замками, расцепным механизмом и фитингами для автоматического соединения пневматических магистралей: 1 – корпус; 2 – штифт; 5 – автоматический пружинный-замок; 6 – механизм расцепной; 13 -клапан; 14 – штуцер; 15 – уплотнительное кольцо КУ ГОСТ 38-72
Произвести монтаж сцепки на вагон. Опору закрепить на сцепку до установки ее на вагон. Для установки сцепки на вагоне расположены места крепления с установочными отверстиями под V-образную опорную планку (черт. ТМ122.07.03.000). Для сцепок БСУ-ТМ122-00, -01 расположение отверстий на раме вагона показано на рисунке 1.1.1.20.
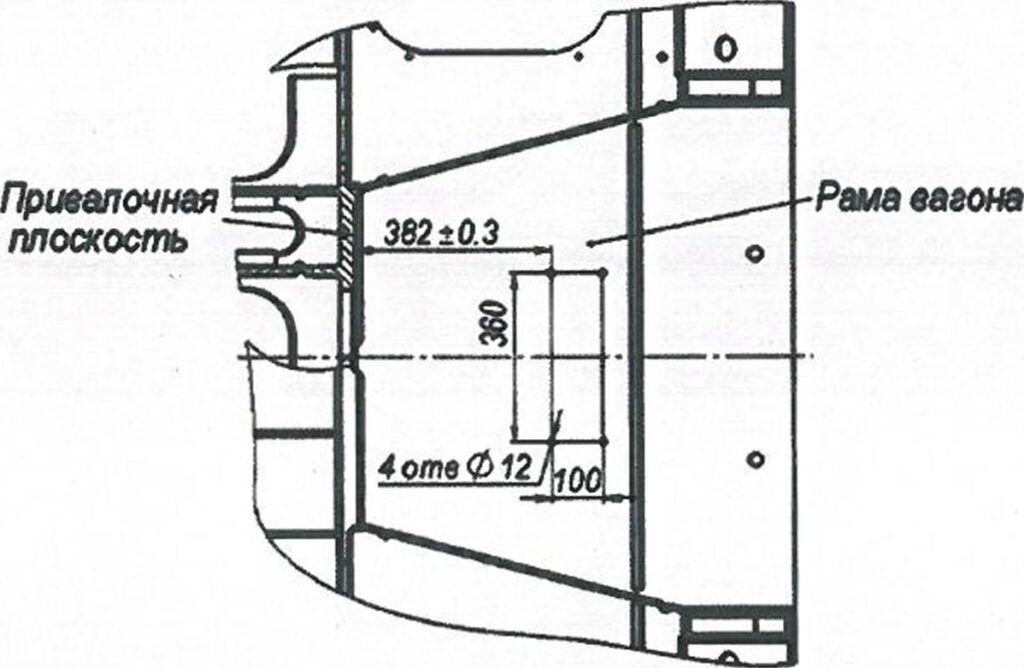
Рисунок 1.1.1.20 – Разметка под планку ТМ122.07.03.000 (для сцепок БСУ-ТМ122-00, -01)
Монтаж сцепки БСУ-ТМ122-00, -01 на раму вагона показан на рисунке 1.1.1.21. Крепеж сцепки БСУ-ТМ122 и планки ТМ122.07.03.000, а также шунтирующие кабели условно не показаны.
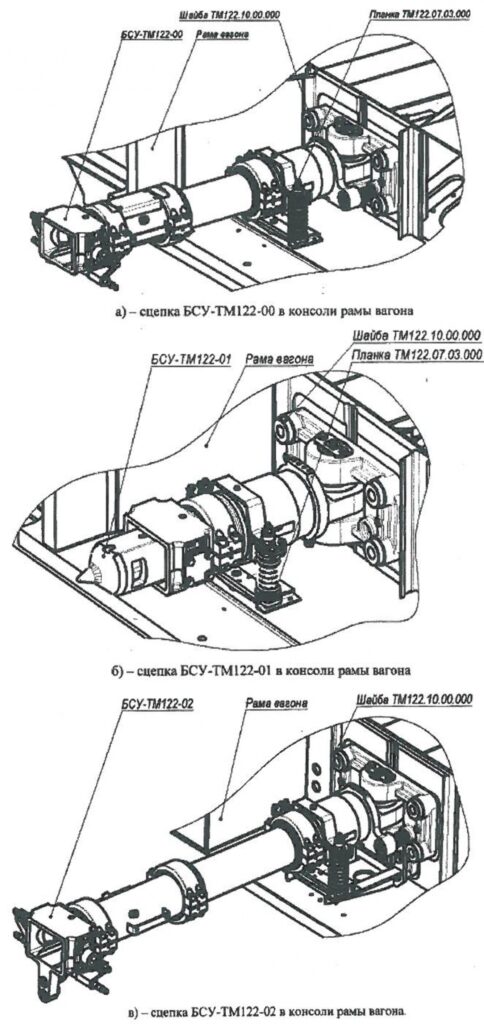
Рисунок 1.1.1.21 – Сцепки БСУ-ТМ122 на раме вагона
Сопрягаемая с плитой поверхность шайбы ТМ122.10.00.000 и сопрягаемые с вагоном поверхности плит снабжены электроизоляционной прокладкой из листового стеклотекстолита, которая приклеивается к плите сцепки.
Выступающая часть плиты должна быть изолирована путем обмотки лакотканью. Для защиты лакоткани от возможного повреждения при монтаже сцепки она должна быть защищена тонкостенным кольцом из оцинкованной жести. При монтаже не допускается повреждение электроизоляции сцепки.
Монтаж межвагонных сцепок на вагон:
- закрепить планку ТМ122.07.03.000 (если она входит в комплект) на нижнем листе консоли;
- на выступающие из стенки вагона болты М36 надеть термоусадочную трубку диаметром 40 мм, длиной 200 мм и прогреть феном для осадки;
- установить на болты соответствующие электроизоляционные пластины (из комплекта поставки) до контакта с торцевой плоскостью вагона;
- установить сцепку в консоль вагона с помощью грузоподъемного устройства, установить на концы болтов М36 силовые стальные шайбы текстолитовой шайбой к плите сцепки и закрепить сцепку болтовым соединением;
- вывернуть (при наличии) транспортировочные болты (2 шт с головками желтого цвета) из механизма центрирования и убрать в ЗИП.
После затяжки вагонных болтовых соединений, на резьбовую часть болтов и на гайки нанести желтой или красной краской контрольные линейные метки так, чтобы они продолжились на близлежащую поверхность закрепляемого элемента на (5 – 15) мм, шириной метки (3 – 6) мм. После установки сцепки на вагон, при необходимости, отрегулировать положение сцепки в вертикальной плоскости вращением гаек (8) опоры (рисунок 1.1.1.12). Ось сцепки должна быть параллельна нижнему листу консоли вагона.
Подсоединить шунтирующие кабели к вагону.
На межвагонные сцепки установить по два кабеля с каждой стороны, соединив следующие элементы:
- плита сцепки с корпусом поглощающего аппарата;
- корпус поглощающего аппарата с головой сцепки;
- головы межвагонных сцепок в сцепленном состоянии.
Установку головной сцепки произвести аналогичным образом. После установки подсоединить к штуцеру (13) клапана напорную магистраль пневмосистемы поезда, а к штуцеру (14) (рисунок 1.1.1.19) -тормозную магистраль. На накидные гайки нанести желтой или красной краской контрольные линейные метки так, чтобы они продолжились на близлежащую поверхность закрепляемого элемента на (5 – 15) мм, шириной метки (3 – 6) мм. Заземление головной сцепки выполнить кабелем с одной стороны. Каждая из сцепок соединяется кабелем от опорной плиты с кузовом вагона.
На голову головной сцепки одеть защитный кожух-крышку, который закрепить эластичным жгутом, перекинутым вокруг корпуса автоматических пружинных замков.