Для контроля и сбора диагностической информации о температурных параметрах опорно-подшипниковых элементов буксовых узлов и устройств компонентов механической передачи вращающего момента с ТЭД на колесные пары в процессе эксплуатации электропоезда применяются устройства контроля параметров температуры типа «Compact PT-100».
Функционирование температурного датчика РТ-100 основано на принципе работы так называемых термометров сопротивления. Термометр сопротивления (иначе называемый термосопротивлением) — это устройство для измерения температуры. Суть действия прибора заключается в изменении электрического сопротивления сплавов, полупроводников и чистых (т.е. без примесей) металлов при изменении температуры. Термометр сопротивления также называют резистивным датчиком сопротивления. Чувствительный элемент термометра сопротивления представляет собой резистор, сделанный из пленки или металлической проволоки, электрическое сопротивление которого зависит от температуры. Проволока намотана на жесткий каркас, изготовленный из кварца, слюды или фарфора, и заключена в защитную металлическую (стеклянную, кварцевую) оболочку. В температурном датчике РТ-100 в качестве чувствительного элемента применяется медь. Оболочка или защитная гильза элемента выполнена из никеля. Общий вид и конструкция измерительного элемента датчика РТ-100 приведены на рис. 8.78.
С помощью штыкового (байонетного) разъема датчик температуры может легко и быстро подключаться к оборудованию (монтаж и демонтаж осуществляются без инструмента). Упругая спираль из высококачественной нержавеющей стали обеспечивает защиту от перегиба, гарантирует равномерный нажим измерительного наконечника в отверстии и допускает регулировку установочной длины датчика вращением колпачка байонетного разъема. Благодаря регулируемому нажиму пружины достигается надежная теплопередача и высокая точность измерений. Датчик измерения параметров температуры РТ-100 осуществляет свою контрольно-измерительную функцию в диапазоне от —40 до +250 °С. При этом погрешность измерения составляет 0,01 °С.
В схеме подключения каждого термометра сопротивления РТ-100 используются четыре провода. Два из них служат для подачи питания +24 В постоянного тока на измерительный контур терсорезисторов датчика, и два — для снятия параметрических сигналов (один из этих проводов является резервным). Принципиальная схема подключения температурных датчиков двух буксовых узлов тележки представлена на рис. 8.79.
![]() |
![]() |
![]() |
![]() |
![]() |
Условные обозначения:
|
![]() Рис. 8.77. Расположение контрольных датчиков на ЭВС «Сапсан» (вторая тяговая секция) |

Рис. 8.77. Расположение контрольных датчиков на ЭВС «Сапсан» (вторая тяговая секция)
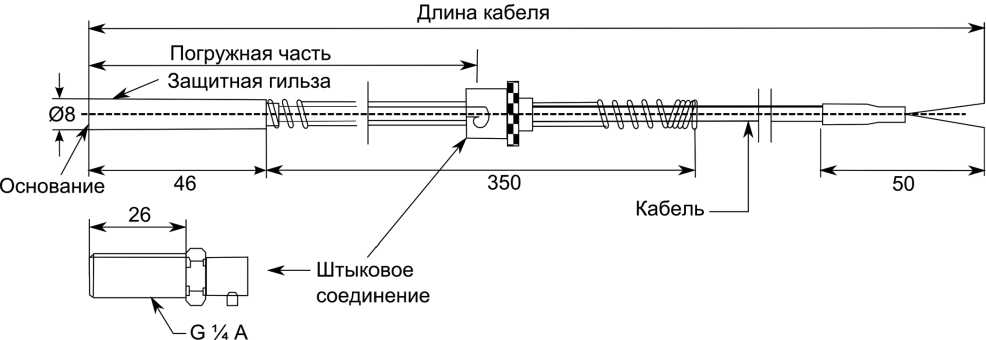
Рис. 8.78. Конструкция температурного датчика РТ-100
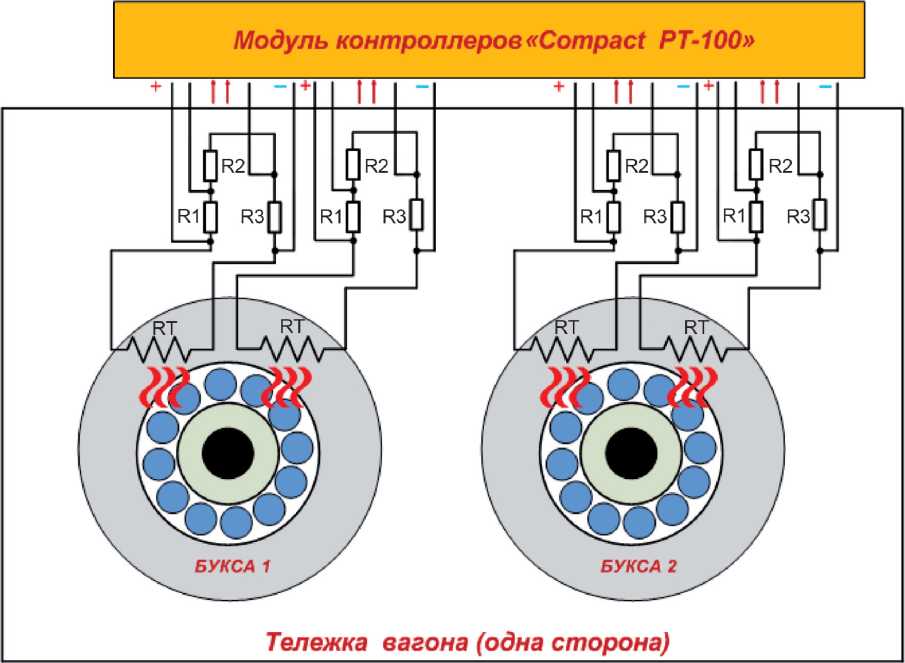
Рис. 8.79. Схема подключения температурного датчика РТ-100
Функция контроля нагрева опорно-подшипниковых элементов буксовых узлов и редукторов реализована в программном обеспечении электропоезда «Сапсан». Принцип формирования и передачи параметров сигнала о температурном состоянии вышеуказанных элементов представлен на рис. 8.80.
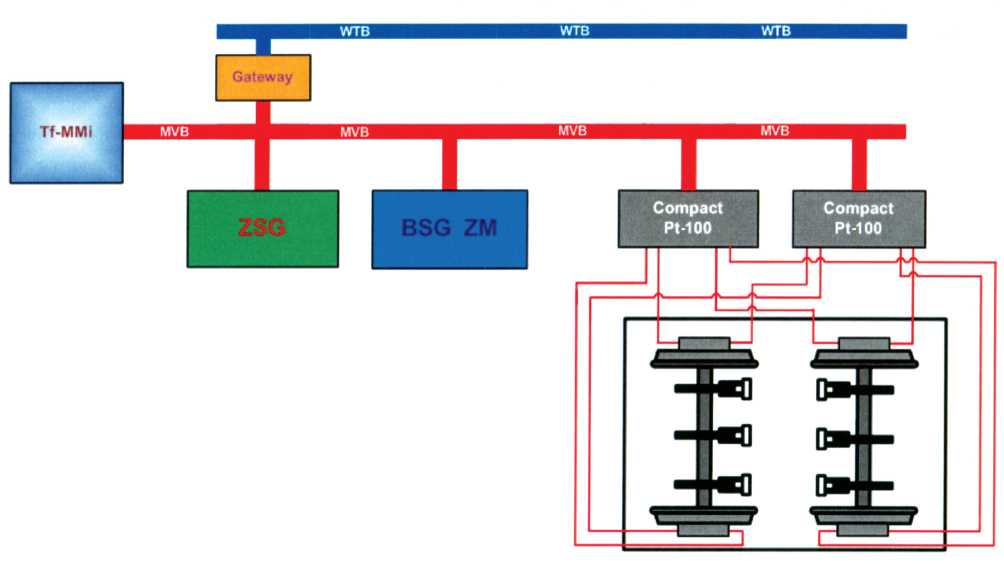
Рис. 8.80. Принцип формирования контрольного сигнала от датчика РТ-100
Сигналы температурных датчиков предварительно обрабатываются в устройствах типа «Compact PT-100», оцифровываются и далее посредством станции SIBAS-KLIP по шине MVB передаются в ЦБУ-мастер, который сравнивает температуры с согласованными предельными величинами и, при необходимости, выдает машинисту электропоезда сообщение на дисплей ИЧМ пульта управления, которое впоследствии квитируется, и принимаются соответствующие меры. Для системы контроля нагрева букс предусмотрена регистрация и запись данных каждого из вагонов. Объем флеш-памяти ЦБУ рассчитан таким образом, что запись новых данных поверх прежних производится только через сутки.
В каждый буксовый узел встроено по два температурных резистора РТ-100. Два измеренных параметра нагрева формируются в двух различных ячейках контроллера и далее, будучи преобразованными в цифровые сигналы, поступают в анализатор ЦБУ. Архитектурная схема формирования сигналов контроля параметров температуры буксовых подшипников приведена на рис. 8.81.
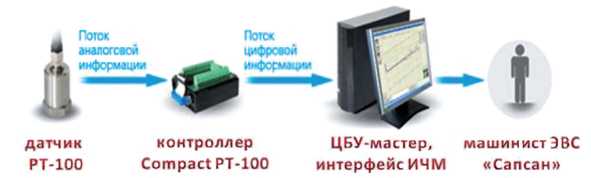
Рис. 8.81. Архитектурная схема формирования сигналов температуры буксовых узлов ЭВС «Сапсан»: Tf-MMi — интерфейс «Человек—машина»; ZSG — центральный блок управления; BSG ZM — блок управления тормозной системой (менеджер); Compact Pt-100 — контроллер температурных датчиков; Gateway — шлюз для связи многофункциональной и проводной шин
Тепло, являющееся результатом трения при качении элементов буксового подшипника, возникает преимущественно в верхней части подшипника, поэтому датчики встроены в верхнюю часть корпуса буксы. Помимо обработки и преобразования сигналов, контроллер «Compact PT-100» осуществляет распознавание разрыва кабеля и короткого замыкания, связь с шиной MVB, а также распознавание ложных сигналов от датчиков. Достоверность сигналов или их градиентов между собой определяется:
- по двум сигнальным показаниям отдельного буксового узла;
- отклонению сигналов от среднего значения отдельного вагона или стороны данного вагона;
- достоверности или предельным значениям сигналов средних температур буксовых узлов, поступающих от обоих контроллеров «Compact PT-100», т.е. по сигналам, непосредственно обрабатываемым в контроллерах.
Проверка достоверности температурных показаний осуществляется в рамках двух состояний: до эксплуатации и в процессе эксплуатации. В процессе эксплуатации недопустимо, чтобы значения сигналов высоких температур в фактически нагретой буксе рассматривались системой как недостоверные. Если два сигнала датчика одной буксы различаются, но сами по себе являются идентифицированными, то производятся следующие действия: в случае превышения порога срабатывания лишь одним из сигналов соответствующее сообщение выдается только тогда, когда и второе значение превышает предельный допустимый порог или отдельный сигнал превышает вышеуказанный порог в течение определенного системой промежутка времени. Данный метод позволяет считать, что вероятность ложного сигнала намного выше, чем вероятность фактического наличия нагретой буксы, так как часто датчики выдают спорадические или ошибочные сигналы. Если сигнал датчика однозначно распознан как ложный, то соответствующее диагностическое сообщение регистрируется ЦБУ и сохраняется в подменю «ТО» в режиме автоматического квитирования. Данный сигнал при дальнейшей работе системы контроля нагрева букс и обработке данных не учитывается. С целью соблюдения требований безопасности движения недостоверный сигнал, несущий некорректную информацию о фактической температуре нагрева буксового узла, обозначается и отсортировывается системой только в том случае, если второе значение сигнала этого буксового узла достоверно и значительно отклоняется по величине параметров измерения от первого параметрического значения.
Определение состояний буксового узла основывается на методе различения «теплой» и «горячей» буксы, в основе которого лежат два критерия со связью «ИЛИ». Первый критерий — абсолютное температурное значение буксового узла колесной пары. Второй критерий — отклонение температуры буксового узла от среднего значения. При этом система контроля нагрева автоматически формирует среднее значение высокой эффективности, например среднее значение одного вагона или каждой из сторон этого вагона. Ступени состояния буксовых узлов имеют соответствующие пределы по фактической измеренной температуре.
Наиболее значимой величиной является абсолютная температура буксового узла, так как при определенном нагреве наступает состояние, при котором происходит сгорание смазки подшипников и ее улетучивание, т.е. происходит нарушение нормального температурного рабочего диапазона и процесса теплопередачи при трении элементов качения. В режиме эксплуатации в буксовом узле колесной пары, в том числе в корпусе буксы и ее крышке, в зависимости от уровня нагрева и передачи тепла происходит распределение температуры. Предельный уровень нагрева имеет прямую зависимость от трения в самом подшипнике, точнее от поверхностей, которые испытывают трение, а также от качества и состояния смазки, механической нагрузки и скорости вращения оси колесной пары. Предельные значения по передаче тепла зависят от уровня теплопередачи тел качения, от площади рабочих поверхностей, внешней температуры циркуляции воздуха, в особенности от сопротивления встречных воздушных потоков.
В порядке увеличения нагрева буксового подшипника по пороговым значениям различают три ступени: предупреждение, первая ступень нагрева, вторая ступень нагрева. В случае полного технического отказа функции определения температуры, например при выходе температурного датчика из строя по причине обрыва кабеля, различают так называемую ступень «Отказ функции».
В соответствии с требованиями концепции обеспечения контроля нагрева букс и технического задания на изготовление высокоскоростного электропоезда «Сапсан», согласно алгоритмам работы системы управления данного поезда ступенчатый алгоритм определения уровня нагрева функционирует следующим образом:
- ступень «Предупреждение» формируется на основании интегрированного системой диагностики сообщения об уровне нагрева подшипников буксового узла в соответствии с пределом по абсолютной температуре буксы более 100 °С или об отклонении от среднего значения более 20 °С. Данное информационно-диагностическое сообщение регистрируется и сохраняется в подсистеме контроля нагрева букс ЦБУ. Квитирование происходит в автоматическом режиме, после чего также автоматически сообщение сохраняется в электронном реестре ремонтной службы. Машинист в данной ситуации слышит лишь акустический сигнал и может отследить, как в течение 2 с диагностическое сообщение переходит в подменю «ТО»;
- первая ступень автоматически определяется и формируется системой управления при нагреве до температуры по абсолютному ее значению более 120 °С и отклонении от среднего значения более 45 °С. При этом система диагностики формирует акустический сигнал и информационное сообщение, которое выводится машинисту на интерфейс «Человек—машина». Отличительной особенностью данного сообщения является невозможность его автоматического квитирования системой управления, т.е. подразумевается обязательное ознакомление с данным сообщением обслуживающего персонала, так как необходим повышенный контроль с его стороны. Рекомендуется обязательно произвести внешний осмотр с ручным замером температуры подшипникового узла на ближайшем остановочном пункте или по прибытию на конечный пункт назначения с привлечением компетентных экспертов ремонтной службы;
- вторая ступень реализует крайние меры по предотвращению более тяжелых последствий посредством автоматического принудительного торможения поезда путем активации режима экстренного торможения от петель безопасности системы управления поездом. В качестве критериев для формирования данного воздействия выступают параметрические показания датчиков контроля температуры буксовых узлов, сообщающие о достижении критической абсолютной температуры буксы более 140 °С или отклонении от среднего значения более 65 °С. При этом исполнителем принудительного торможения выступает петля контроля тележки, которая в свою очередь через посредническое воздействие БУТ-мастера осуществляет воздействие на контур петли экстренного торможения. При данном алгоритме диагностическое информационное сообщение также не имеет свойства автоматического квитирования системой управления и требует ознакомления с ним эксплуатационного обслуживающего персонала. При достижении фактической скорости поезда менее 40 км/ч для комфортности и плавности отпуска тормозов к моменту остановки имеется возможность отмены автоматического экстренного торможения путем кратковременного импульсного толчка задатчика тормозных усилий FS-41 в положение «ШСТ». В случае данной манипуляции электропоезд в зависимости от профиля участка пути даже при условии полного отпуска тормозов будет следовать со скоростью не более 3—5 км/ч. В такой ситуации после остановки требуется обязательный внешний осмотр и ручной замер фактической температуры элементов буксового узла с целью принятия решения о возможности дальнейшего следования электропоезда. Если движение будет возобновлено, система поезда позволит следовать с фактической скоростью не более 40 км/ч.
- в случае технического отказа датчика буксового узла из-за его повреждения система формирует диагностическое сообщение «Отказ функции». В процессе дальнейшего движения поезда система управления предоставляет возможность следовать со скоростью более 220 км/ч только в течение 5 мин, т.е. если в момент получения данного сообщения фактическая скорость составляет более 220 км/ч, то у машиниста есть 5 мин для ее снижения, в противном случае реализуется принудительное автоматическое торможение по той же схеме, что и на второй ступени. В любом случае для продолжения движения необходимо осуществить осмотр неисправного узла и исключить данный компонент из схемы петли контроля тележки путем его шунтирования при помощи переключателя «Контроль тележки» на данном вагоне. В случае отключения вагона из контура ПКТ устанавливается максимальная скорость следования поезда 200 км/ч.
Ниже приведены рекомендуемые действия локомотивной бригады при поступлении сообщений о нагреве буксового узла ЭВС «Сапсан» (версия ПО 5.4.0).
1. При срабатывании первой ступени контроля нагрева буксовых узлов на информационную строку ИЧМ-1 кабины управления поступает короткое диагностическое сообщение «Нагрев буксы. Тележка Х ось Х» с кодами 6АА0, 6АА4, 6АА8, 6ААС, 6АВО, 6АВ4, 6АВ8, 6АВС:
1.1. При получении данного сообщения необходимо путем плавного служебного торможения произвести остановку электропоезда на ближайшей станции.
1.2. Затем следует произвести осмотр данного буксового узла и ручной замер его температуры с применением приборов дистанционного контроля температуры «Кельвин».
1.3. В случае выявления нагрева элементов буксового узла более 120 °С можно продолжить движение до станции назначения со скоростью не более 200 км/ч и незамедлительно доложить о необходимости снятия электропоезда с линии.
При нагреве менее 120 °С можно продолжить следование с установленной скоростью без ограничений.
2. При срабатывании второй ступени контроля нагрева буксовых узлов на информационную строку ИЧМ-1 кабины управления поступает короткое диагностическое сообщение «Перегрев буксы. Тележка Х ось Х» с кодами 6АС0, 6АС8, 6АСС, 6АD0, 6AD4, 6AD8, 6ADC:
2.1. При фактической скорости движения электропоезда более 40 км/ч автоматически активируется принудительное торможение в режиме экстренного торможения с появлением короткого сообщения «Принудительное торможение. Контроль перегрева буксы», код 68С7.
2.2. Для поддержания экстренного торможения рукоятку тормозного котроллера FS-41 необходимо установить в положение «ПСТ» до полной остановки электропоезда.
2.3. После остановки следует произвести осмотр данного буксового узла и ручной замер его температуры аналогично описанному в п. 1.2.
2.4. В случае выявления температуры нагрева более 140 °С или разрушения элементов буксового узла нужно действовать согласно требованиям п. 3.1 распоряжения № 2528Р от 11.12.2009 г.
2.5. В случае отсутствия видимых разрушений элементов буксового узла, или их температуре не выше 140 °С, или разнице температур всех четырех буксовых узлов не более 65 °С следует действовать согласно следующим рекомендациям диагностического сообщения:
2.5.1. При v = 0 км/ч произвести переключение шунтирующего переключателя вагонного пульта № 2 43-S12 «Контроль тележки» неисправного вагона в пути в положение «Выкл.».
2.5.2. Продолжить следование со скоростью 200 км/ч до конечной станции с обеспечением контроля неисправного вагона в пути инженером 1-й категории.
Кроме того, необходимо незамедлительно произвести доклад о необходимости снятия электропоезда с линии.
3. При отказе функции контроля нагрева буксовых узлов на информационную строку ИЧМ-1 кабины управления поступает короткое диагностическое сообщение «Контроль перегрева буксы вышел из строя», код 68С4.
3.1. В течение 5 мин необходимо принять меры к остановке поезда плавным служебным торможением, в противном случае при фактической скорости электропоезда более 220 км/ч автоматически активируется принудительное торможение в режиме экстренного торможения.
3.2. После остановки произвести осмотр данного буксового узла и ручной замер его температуры аналогично описанному в п. 1.2.
3.3. В случае выявления температуры нагрева более 140 °С или разрушения элементов буксового узла нужно действовать согласно требованиям п. 3.1 распоряжения № 2528Р от 11.12.2009 г.
3.4. В случае отсутствия видимых разрушений элементов буксового узла, или их температуре не выше 140 °С, или разнице температур всех четырех буксовых узлов вагона не более 65 °С, следует действовать согласно рекомендациям диагностического сообщения, описанным в п. 2.5.1. и 2.5.2.