Тележка воспринимает тяговые и тормозные усилия, боковые, горизонтальные и вертикальные силы при прохождении неровностей пути и передает их на раму кузова. Каждый вагон электропоезда опирается на две двухосных тележки, которые подразделяются на моторные и немоторные (рисунки 2.1 – 2.2).
Конструктивно тележка (моторная и немоторная) состоит из:
- рамы;
- шкворневого узла с демпфером гашения поперечных колебаний;
- рессорного подвешивания первой ступени;
- рессорного подвешивания второй ступени с пневматическими рессорами;
- торсионной системы стабилизации и демпфера виляния.
Все детали и узлы тележек, смазка подшипников и масло для гидродемпферов соответствуют климатическому исполнению «У» категории 1 по ГОСТ 15150 и сохраняют работоспособность при температурах в диапазоне от минус 40 до плюс 55 °C.
По воздействию механических факторов внешней среды и ударных нагрузок детали тележки соответствуют по ГОСТ 30631 группам механического исполнения М26 и М27.
2.2 Рама тележки
Рама тележки служит для передачи нагрузки от кузова на колесные пары, передачи тяговых и тормозных усилий, а также установки на ней колесномоторного блока и тормозных блоков (рисунок 2.3).
Рама тележки состоит из двух сварных продольных балок коробчатого профиля, соединенных между собой поперечной балкой.
Рамы моторных и немоторных тележек различаются наличием на поперечной балке кронштейнов подвески колесно-моторного блока и различной формой кронштейнов подвешивания тормозных блоков. Продольные балки моторных тележек имеют кронштейны для монтажа оборудования системы подачи песка.
Продольные балки рамы первой по ходу движения электропоезда моторной тележки имеют кронштейны под установку приемных катушек локомотивной сигнализации.
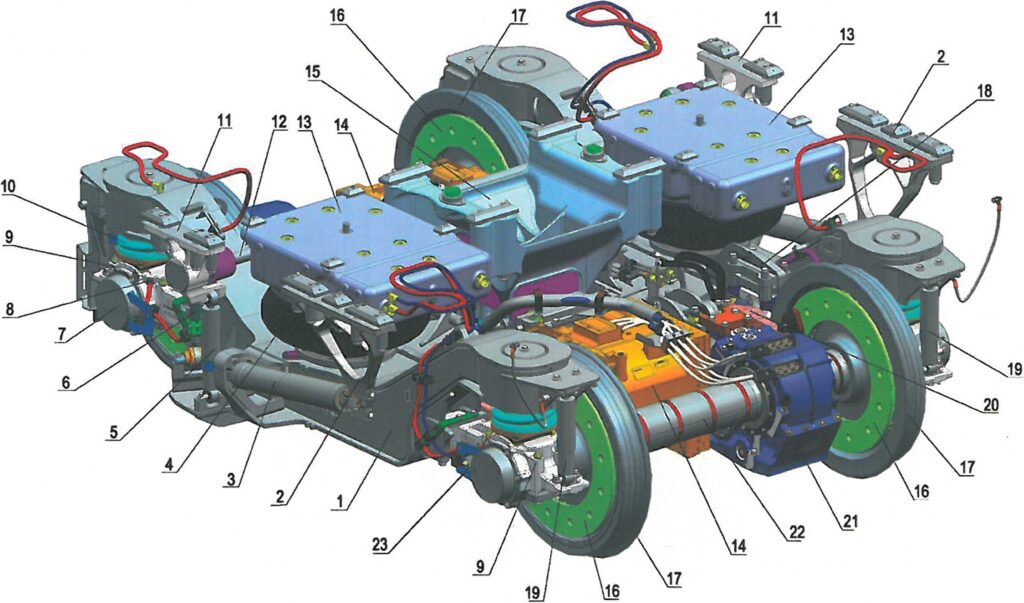
Рисунок 2.1 – Моторная тележка: 1 – продольная балка рамы тележки; 2 – кронштейн демпфера виляния; 3 – демпфер виляния; 4 – пневморессора второй ступени рессорного подвешивания; 5 – вертикальный демпфер второй ступени рессорного подвешивания; 6 – поводок торсионной системы стабилизации; 7 — крышка корпуса буксового узла; 8 — датчик температуры буксового узла; 9 – корпус буксового узла; 10 — пружины первой ступени рессорного подвешивания; 11 – кронштейн торсионной системы стабилизации; 12 – торсион системы стабилизации; 13 – адаптер кузова вагона; 14 – тяговый двигатель; 15 – шкворневой узел; 16 – тормозной диск; 17 – цельнокатаное колесо; 18 – поперечная балка рамы тележки; 19 – демпфер вертикальных колебаний первой ступени рессорного подвешивания; 20 – тормозной блок дискового тормоза; 21 – редуктор тягового привода; 22 – защита оси колесной пары; 23 – осевой двухканальный датчик ОДМ-2 системы противоюзной защиты.
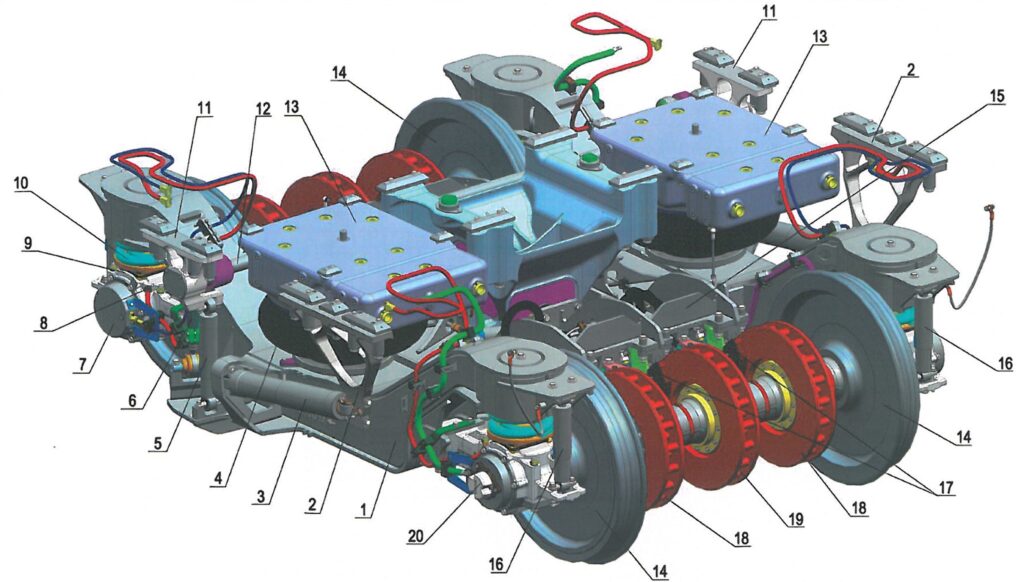
Рисунок 2.2 – Немоторная тележка: 1 – продольная балка рамы тележки; 2 – кронштейн демпфера виляния; 3 – демпфер виляния; 4 – пневморессора второй ступени рессорного подвешивания; 5 – вертикальный демпфер второй ступени рессорного подвешивания; 6 – поводок торсионной системы стабилизации; 7 – осевой двухканальный датчик ОДМ-2 системы противогазной защиты; 8 – датчик температуры буксового узла; 9 – корпус буксового узла; 10 – пружины первой ступени рессорного подвешивания; 11 – кронштейн торсионной системы стабилизации; 12 – торсион системы стабилизации; 13 – адаптер кузова вагона; 14 – цельнокатаное колесо; 15 – поперечная балка рамы тележки; 16 – демпфер вертикальных колебаний первой ступени рессорного подвешивания; 17 – тормозной блок дискового тормоза; 18 – тормозные диски крайние; 19 – тормозной диск средний; 20 – заземляющее устройство.
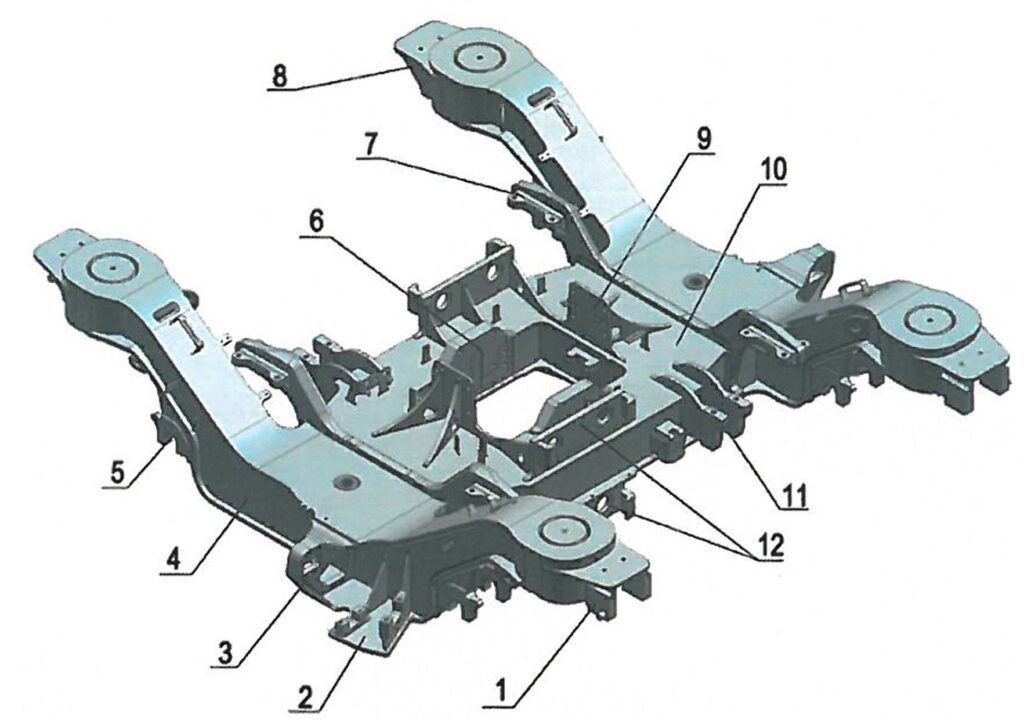
Рисунок 2.3 – Рама моторной тележки: 1 — кронштейн установки демпфера вертикальных колебаний первой ступени рессорного подвешивания и системы пескоподачи; 2 – кронштейн установки вертикального демпфера второй ступени рессорного подвешивания и поводка торсионной системы стабилизации; 3 – кронштейн установки демпфера виляния; 4 – продольная балка рамы тележки; 5 – кронштейн установки поводка буксового узла; 6 – кронштейн крепления буферного устройств передачи продольных усилий; 7 – кронштейн установки тормозного блока дискового тормоза моторной тележки; 8 – кронштейн установки демпфера вертикальных колебаний первой ступени рессорного подвешивания немоторной тележки; 9 – кронштейн крепления буферного устройства ограничения поперечных перемещений; 10 – поперечная балка рамы тележки; 11 – кронштейн установки поводка подвески тягового редуктора моторной тележки; 12 – кронштейн крепления тягового двигателя моторной тележки.
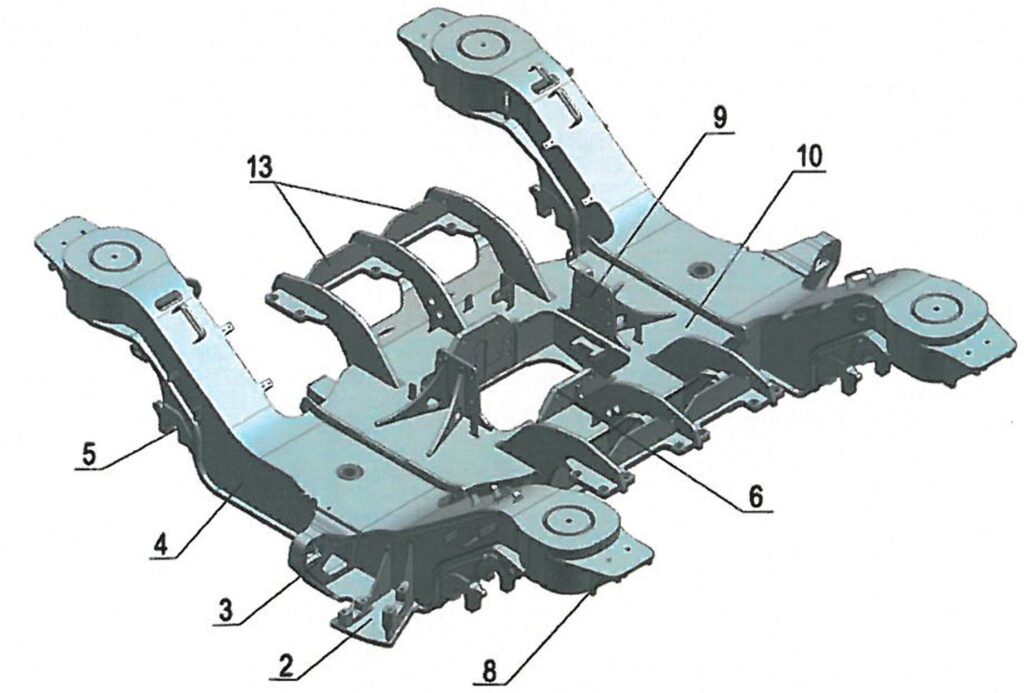
Рисунок 2.3 – Рама немоторной тележки: 1 — кронштейн установки демпфера вертикальных колебаний первой ступени рессорного подвешивания и системы пескоподачи; 2 – кронштейн установки вертикального демпфера второй ступени рессорного подвешивания и поводка торсионной системы стабилизации; 3 – кронштейн установки демпфера виляния; 4 – продольная балка рамы тележки; 5 – кронштейн установки поводка буксового узла; 6 – кронштейн крепления буферного устройств передачи продольных усилий; 7 – кронштейн установки тормозного блока дискового тормоза моторной тележки; 8 – кронштейн установки демпфера вертикальных колебаний первой ступени рессорного подвешивания немоторной тележки; 9 – кронштейн крепления буферного устройства ограничения поперечных перемещений; 10 – поперечная балка рамы тележки; 13 – кронштейн тормозного блока дискового тормоза немоторной тележки.
2.3 Шкворневой узел с демпфером гашения поперечных колебаний
Шкворневой узел обеспечивает передачу продольных усилий тяги и торможения с рамы тележки на раму остова кузова (рисунок 2.4). Шкворень также ограничивает поперечные перемещения кузова и является опорой для установки демпфера гашения поперечных перемещений.
Шкворень является литой алюминиевой конструкцией и крепится к раме остова кузова. На верхней монтажной поверхности шкворня, со стороны рамы остова кузова имеются центровочные болты, исключающие возможность неправильной установки шкворня. На боковых поверхностях, в области контакта с упорами буферных устройств передачи продольного усилия и ограничения поперечных перемещений установлены скользуны из нержавеющей стали.
Нижняя часть шкворня входит в «окно» поперечной балки рамы тележки. В нижней части шкворня закреплена пластина с износостойкими накладками, являющаяся ограничителем вертикального перемещения. Ограничитель вертикального перемещения предотвращает выход шкворня из «окна» поперечной балки тележки при подъеме кузова.
Передача продольного усилия с рамы тележки на шкворень осуществляется через два резинометаллических буферных устройства, расположенных на кронштейнах поперечной балки рамы тележки. Деформирующее воздействие шкворня на буфер ограничено предохранительным упором.
Поперечные перемещения шкворня в «окне» балки рамы тележки ограничено резиновыми буферами, которые также имеют металлические предохранительные упоры.
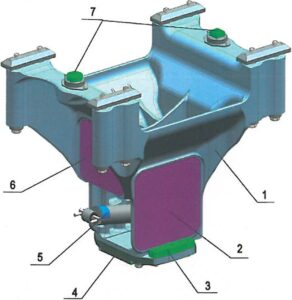
Рисунок 2.4 – Шкворневой узел: 1 – шкворень; 2, 6 – скользуны; 3 – вставки ограничителя вертикального перемещения; 4 – пластина ограничителя вертикального перемещения; 5 – демпфер гашения поперечных перемещений; 7 – установочные болты; 8 – поперечная балка рамы тележки; 9, 12 – регулировочные вкладыши; 10 – резинометаллический элемент упора; 11 – буфер; 13 – ограничитель поперечных перемещений.
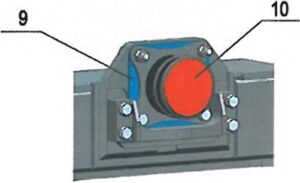
Буферное устройство передачи продольных усилий
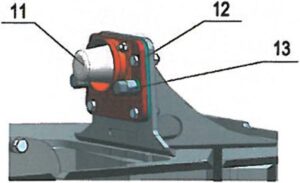
Буферное устройство ограничения поперечных перемещений
Между шкворнем и поперечной балкой рамы тележки установлен демпфер, гасящий поперечные горизонтальные движения между кузовом и тележкой. С одной стороны, поперечный демпфер соединен с кузовом вагона через шкворень, с другой стороны – с рамой тележки при помощи консоли.
2.4 Рессорное подвешивание
Рессорное подвешивание предназначено для передачи веса вагона электропоезда на шейки осей колесных пар, распределения этого веса равномерно между осями, смягчения ударов, получаемых колесными парами при неровности пути и уменьшения воздействия электропоезда на путь.
Для обеспечения комфорта пассажиров, на электропоезде применено двухступенчатое рессорное подвешивание. Рессорное подвешивание первой ступени включает в себя цилиндрические рессоры (пружины) и гидравлические демпферы. Рессорное подвешивание второй ступени представляет собой пневматическую подвеску с гидравлическими демпферами гашения колебаний.
2.4.1 Первая ступень рессорного подвешивания.
Первая ступень рессорного подвешивания расположена между корпусом буксового узла каждой колесной пары и рамой тележки и состоит из комплекта двух цилиндрических винтовых пружин сжатия, образующих единый блок, и гидравлического демпфера (рисунок 2.5).
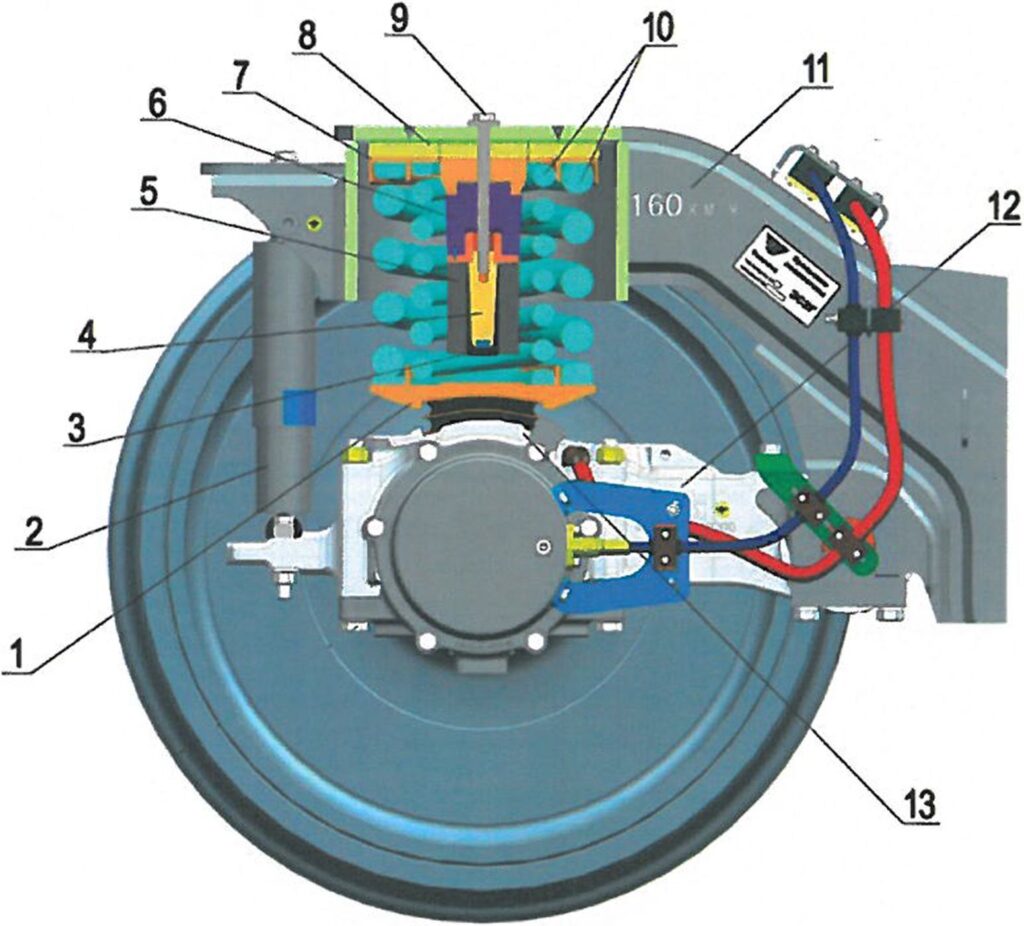
Рисунок 2.5 – Первая ступень рессорного подвешивания: 1 – нижняя опора пружин; 2 – демпфер вертикальных колебаний первой ступени рессорного подвешивания; 3 – упругий упор; 4 – упор; 5 – резиновый амортизатор; 6 – направляющая; 7 – верхняя опора пружин; 8 – комплект регулировочных прокладок; 9 – болт стяжной; 10 – комплект из двух цилиндрических винтовых пружин; 11 – боковина рамы тележки; 12 – корпус буксы; 13 – многослойная резинометаллическая пластина.
Комплект из двух цилиндрических винтовых пружин, установленный в вертикальном положении, удерживается и центрируются двумя опорами -верхней и нижней. Между верхней опорой и рамой тележки установлен комплект регулировочных пружин, используемый при развеске электропоезда. Между нижней опорой и корпусом буксы установлена многослойная упругая резинометаллическая пластина.
За счет применения упругого упора рессорное подвешивание первой ступени имеет прогрессивную характеристику – то есть, ее жесткость увеличивается по мере возрастания нагрузки (прогиба), за счет воздействия упора на нижнюю опору пружины. Дальнейший прогиб цилиндрических пружин ограничен жестким упором.
Применяемый совместно с цилиндрическими пружинами гидравлический гаситель колебаний первой ступени служит для гашения колебаний, возникающих при прохождении колесной парой неровностей пути, и предотвращает их передачу на раму тележки.
2.4.2 Вторая ступень рессорного подвешивания
Вторая ступень рессорного подвешивания расположена между рамой тележки и кузовом вагона и обеспечивает амортизацию и гашение возникающих между ними вертикальных колебаний, а также обеспечивает постоянную высоту кузова вагона независимо от изменяющейся нагрузки (увеличения или уменьшения количества пассажиров в вагоне).
Вторая ступень рессорного подвешивания каждой тележки состоит из двух пневматических рессор (рисунок 2.6) и двух вертикальных гидравлических демпферов (рисунок 2.1, 2.2).
Резиновая пневматическая рессора крепится к кузову вагона через адаптер – литую металлическую пустотелую конструкцию, закрепленную на раме остова кузова. Внутренние полости адаптера служат дополнительным объемом сжатого воздуха (100 л), и соединены с внутренним объемом пневматической рессоры через втулку. Один из адаптеров данной системы оборудован предохранительным клапаном, другой – разобщительным краном для выпуска воздуха при техобслуживании.
Бурт пневматической рессоры при помощи кольца закреплен на крепежной плите, которая в свою очередь закреплена на адаптере. Между крепежной плитой и адаптером устанавливаются регулировочные прокладки, при помощи которых во время сборки выставляется точный горизонтальный уровень кузова вагона. Обратная сторона пневматической рессоры крепится к установочному ободу. Установочный обод имеет опору с опорной плитой, на которую опускается кузов вагона при отсутствии сжатого воздуха в пневматической рессоре.
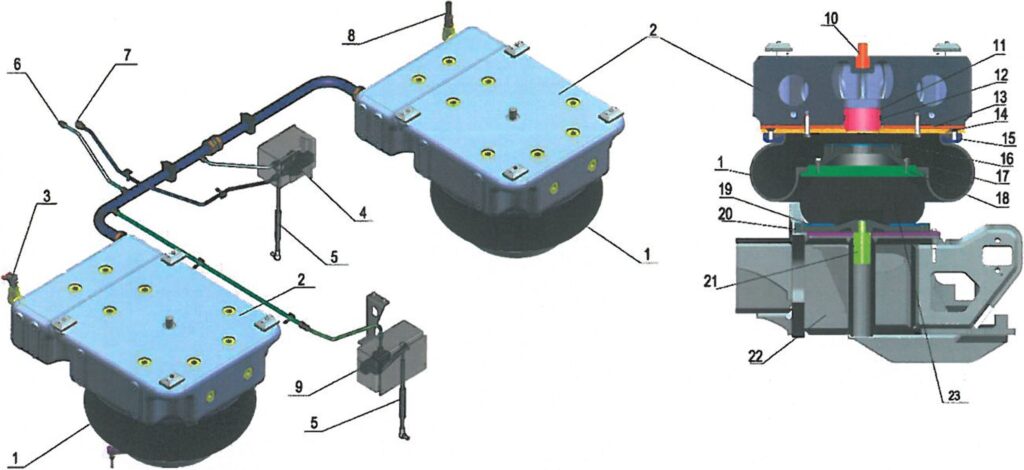
Рисунок 2.6 – Система пневматических рессор: 1 – пневморессора; 2 – адаптер; 3 – разобщительный кран; 4 – регулятор положения кузова; 5 – управляющая тяга; 6 – трубопровод к клапану среднего давления блока БТО 420; 7 – трубопровод питательной магистрали; 8 – предохранительный клапан пневморессоры; 9 – регулятор ограничения хода пневморессоры; 10 – центрирующая втулка; 11 – втулка уплотнительная; 12 – уплотнительные кольца; 13 – прокладки; 14 – крепежная плита; 15 – кольцо; 16 – плита опоры; 17 – опора; 18 – установочный обод; 19 – регулировочные прокладки; 20 – опорная плита; 21 – втулка отвода воздуха; 22 – поперечная балка рамы тележки; 23 – подушка резиновая.
На левую и правую боковины рамы тележки устанавливаются опорные плиты, на которые сверху ставиться бочкообразные цельнорезиновые страховочные рессоры, выполняющие функции амортизаторов при повреждении пневматических рессор. Воздух из полости под страховочной рессорой выводится через дренажную втулку. Между опорной плитой и рамой тележки установлены регулировочные прокладки.
Правая и левая пневматические рессоры одной тележки образуют единую систему. В систему пневматических рессор одной тележки входят также трубопроводы сжатого воздуха и установленные на них впускной клапан и клапан ограничения хода. Клапаны установлены в контейнере, закрепленном на раме остова кузова вагона в подвагонном пространстве.
Гашение вертикальных колебаний, возникающих во второй ступени рессорного подвешивания осуществляется гидравлическими демпферами, установленными между кронштейнами кузова вагона и рамы тележки, по одному с каждой стороны.
Регулировка высоты кузова вагона происходит за счет изменения давления в системе пневматических рессор второй ступени подвешивания, с целью удерживания пневматических рессор, на которые опирается кузов вагона, на одной и той же высоте независимо от создаваемой на них нагрузки. В качестве регулятора используется впускной клапан, который в соответствии с изменением нагрузки на рессору (разницей между заданной длиной тяги управления и фактической высотой рессоры) подает сжатый воздух в рессору, выпускает его из рессоры или блокирует подачу.
2.5 Торсионная система стабилизации и демпфер виляния
Торсионная система стабилизации (рисунок 2.9) ограничивает поперечные качания вагона, а при движении по кривым участкам пути предотвращает наклон кузова вагона в наружную сторону.
Основным элементом системы стабилизации является торсионный вал, на оба конца которого в горячем состоянии насажены рычаги системы стабилизации (рисунок 2.7) и опорные втулки. Торсионный вал посредством опорных втулок устанавливается в сайлентблоки кронштейнов кузова вагона. Рычаги и опорные втулки после посадки на торсионный вал представляют собой единую конструкцию, не подлежащую разборке (выпрессовке).

Рисунок 2.7 – Торсионный вал с опорными втулками и рычагами системы стабилизации
Связь торсионного вала системы стабилизации с рамой тележки осуществляется через поводки. Каждый поводок состоит из верхней и нижней опоры, соединенных между собой тягой. Палец верхней опоры поводка вставляется в проушину рычага торсиона и крепится с обратной стороны корончатой гайкой. Поводок нижней опоры, представляющей собой сайлентблок, установлен в кронштейн рамы тележки (рисунок 2.8). Параллельно поводку системы стабилизации, между кронштейном кузова и кронштейном рамы тележки устанавливается гидравлический демпфер второй ступени рессорного подвешивания (рисунок 2.10).
При следовании электропоезда по участку, качание кузова вагона приводит к круговому движению рычага и скручиванию торсиона, что при движении в кривых участках пути предотвращает наклон кузова вагона во внешнюю сторону.
Установленный между кузовом вагона и рамой тележки, демпфер виляния совместно с системой стабилизации гасит колебания тележек при входе в кривые участки пути и выходе из них (рисунок 2.10).
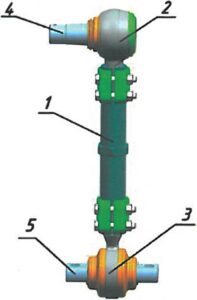
Рисунок 2.8 – Поводок системы стабилизации: 1 – тяга поводка; 2 – верхняя опора; 3 – нижняя опора; 4 – палец верхней опоры; 5 – поводок нижней опоры.
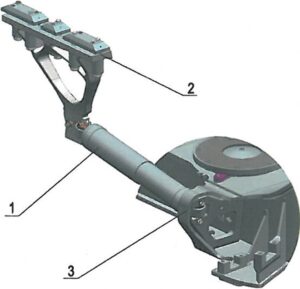
Рисунок 2.10 – Установка демпфера виляния: 1 – демпфер виляния; 2 – кронштейн кузова вагона; 3 – кронштейн рамы тележки.

Рисунок 2.9 – Система стабилизации в сборе: 1 – поперечная балка рамы тележки; 2 – продольная балка рамы тележки; 3 – вертикальный демпфер второй ступени рессорного подвешивания; 4 – поводок системы стабилизации; 5 – кронштейн кузова вагона; 6 – торсион системы стабилизации; 7 – рычаг системы стабилизации.
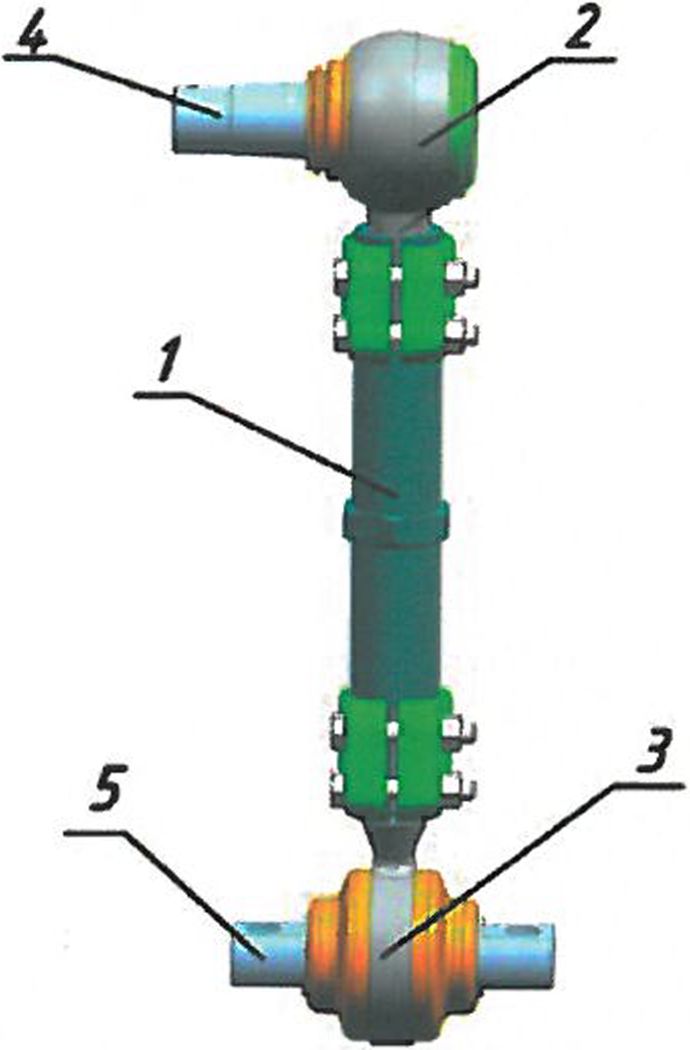
Рисунок 2.8 – Поводок системы стабилизации: 1 – тяга поводка; 2 – верхняя опора; 3 – нижняя опора; 4 – палец верхней опоры; 5 – поводок нижней опоры.
2.6.1 Назначение гидравлических демпферов
Для рассеивания энергии механических колебаний кузова и тележек, возбуждаемых неровностью пути установлены в рессорном подвешивании вагонов электропоезда гидравлические демпферы УГД.
Преимуществом демпферов УГД является повышенная эксплуатационная надежность, отсутствие утечек рабочей жидкости, оптимальная силовая характеристика, эффективное ограничение максимальных усилий сопротивления на расчетном уровне, способность функционировать во второй и первой ступенях рессорного подвешивания, простота конструкции и малая масса. Демпферы УГД работоспособны в наклонном, вертикальном и горизонтальном положениях.
2.6.2 Конструкция гидродемпферов
Демпферы УГД имеют телескопическую конструкцию с пластинчатыми клапанами в поршне и днище, манжетное уплотнение штока и корпуса. Общий вид представлен на рисунке 2.11.
Корпус демпферов УГД (рисунки 2.12) содержит стакан и приварную проушину. В корпусе смонтирована цилиндропоршневая группа, включающая цилиндр и поршень со штоком. Поршень имеет наклонные отверстия, перекрытые набором клапанных пластин, прижатых к верхнему седлу поршня через конусную шайбу. Встречные наклонные отверстия в поршне перекрыты набором клапанных пластин, прижатых к нижнему седлу поршня конусной шайбой. Поршень, пластины и шайбы с натягом закреплены на штоке гайкой.
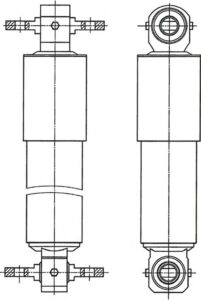
Рисунок 2.11 – Общий вид гидродемпферов
В седлах поршня выполнены дроссельные щели. В канавке поршня размещено чугунное уплотнительное кольцо.
Снизу цилиндр закрыт днищем, в котором смонтированы впускной и разгрузочный клапаны.
Впускной клапан содержит диск, прижатый к седлу днища конической пружиной с помощью фигурной гайки болта. В седле днища выполнена дроссельная щель. Разгрузочный клапан содержит набор пластин, прижатых болтом через конусную шайбу к седлу с другой стороны днища. В днище выполнены сквозные отверстия: впускные и разгрузочные. Сверху цилиндра монтируется направляющая штока, к верхней части штока приварена проушина. Шток гасителя уплотнен манжетой, размещенной в направляющей и прижатой гайке. В направляющей и в гайке имеются протоки для рабочей жидкости, ограниченной манжетой.

Рисунок 2.12 – Конструкция демпфера: 1, 24 – проушина; 2, 26 – резиновая втулка; 3, 25 – металлическая цапфа; 4, 35 – болт; 5, 12, 18 – шайба; 6 – набор пластин; 7 – днище; 8 – диск; 9 – пружина; 10, 11,21 – гайка; 13, 17 – набор клапанных пластин; 14 – поршень; 15 – уплотнительное кольцо; 16, 32 – наклонные отверстия; 19 – шток; 20 – направляющая штока; 23 – кожух; 27 – крышка; 28 – манжета; 30 – цилиндр; 31 – стакан; 33 – разгрузочное отверстие; 34 – впускное отверстие; 36 – резиновое кольцо.
К головке демпферов прикреплен кожух, который приваривается к крышке. Во втором варианте исполнения кожух имеет фланец, который болтами М6 с пружинными шайбами крепится к крышке.
В проушины корпуса и штока вмонтированы втулки резиновые, в которые впрессованы металлические цапфы. Резиновые втулки зафиксированы болтами М6. Полости цилиндра (подпоршневая «А» и надпоршневая «Б») полностью, а рекуперативная «В» частично заполнены рабочей (демпферной) жидкостью.
2.6.3 Работа демпферов
При колебаниях подрессоренных масс вагона на упругих элементах рессорного подвешивания поршень со штоком совершают соответствующие колебательные движения относительно цилиндра и корпуса демпфера, и перемещают рабочую жидкость между полостями «А», «Б» и «В». При этом демпферы развивают силы неупругого сопротивления, ограничивающие амплитуды колебаний кузова и тележки вагона. На ходе сжатия, когда поршень перемещается к днищу, рабочая жидкость дросселирует из подпоршневой полости «А» в надпоршневую «Б» и в рекуперативную «В» проходя через дроссельные щели в седлах поршня и днища.
В процессе дросселирования жидкости пропорционально скорости поршня реализуются силы вязкого трения, сопротивляющиеся перемещению поршня со штоком и, тем самым, оптимально ограничивающие амплитуды колебаний кузова и тележки вагона. При больших скоростях поршня (свыше 0,075 м/с) и давлениях рабочей жидкости свыше 3 МПа отгибаются от седла верхние клапанные пластины поршня, а затем пластины днища и жидкость пропускается уже через кольцевые сечения клапанов из подпоршневой полости «А» в надпоршневую «Б» и в рекуперативную «В». Вследствие этого ограничиваются в клапанном режиме на расчетном уровне максимальные давления рабочей жидкости и, соответственно, усилия сопротивления на ходе сжатия.
На ходе растяжения жидкость из надпоршневой полости «Б» вытесняется поршнем через дроссельные щели в поршне в подпоршневую полость «А». Поскольку сечение надпоршневой полости меньше подпоршневой на величину площади штока, то в подпоршневой полости образуется зона пониженного давления. Перепадом давления между подпоршневой «А» и рекуперативной «В» полостями открывается впускной клапан днища, и жидкость из рекуперативной полости «В» через впускные отверстия пополняет подпоршневую полость «А».
При больших скоростях поршня на ходе растяжения по достижению расчетного давления масла, а, следовательно, и расчетного усилия сопротивления, в надпоршневой полости «Б» отгибаются нижние пластины поршня и жидкость перепускается в подпоршневую полость «А» через встречные наклонные отверстия и кольцевое сечение открытого клапана.
Вследствие этого ограничиваются в клапанном режиме на расчетном уровне максимальные давления рабочей жидкости и усилия сопротивления на ходе растяжения. В итоге возвратно-поступательного движения поршня, дросселирования рабочей жидкости через дроссели и перетекания ее через клапанные отверстия на ходах сжатия-растяжения реализуются нужные силы неупругого сопротивления в дроссельном и клапанном режимах работы.
Характеристика сопротивления в дроссельном режиме зависит от размера дроссельных щелей и различных неплотностей, а в клапанном от набора (суммарной жёсткости) клапанных пластин.